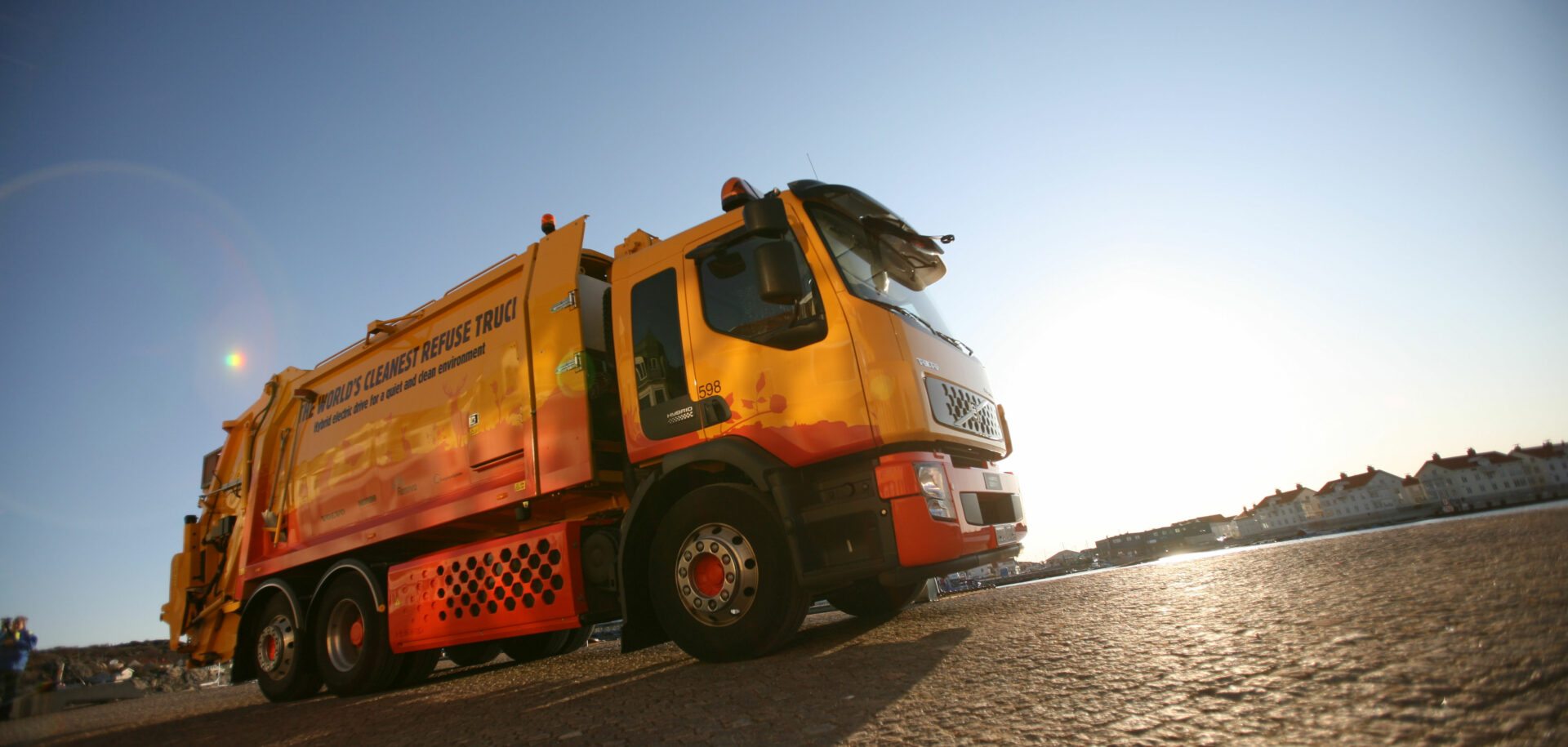
Sfruttare al meglio i rifiuti
È incredibile ciò che si può ottenere dalla spazzatura. Grazie all’innovazione tecnologica, Renova trasforma i rifiuti in preziosa energia.
Ogni anno l’impianto di termovalorizzazione della Renova, nella Svezia occidentale, produce circa un terzo dell’energia termica per riscaldamento della regione di Göteborg. Non solo, l’impianto fornisce anche il 5 percento dell’energia elettrica impiegata dalla città di Göteborg, che è la seconda città svedese. Un bel risultato se si pensa che l’energia prodotta proviene dall’incenerimento di rifiuti non riciclabili.
Gruppo Renova
L’impianto di termovalorizzazione dei rifiuti della Renova, a Sävenäs, Svezia, fa parte del Gruppo Renova, di proprietà di 10 municipalità della Svezia occidentale. La società, specializzata nella gestione e nel trasporto di rifiuti e materiali riciclabili, offre anche servizi di consulenza e formazione correlati a privati e industrie del settore delle costruzioni.
Nell’impianto di Sävenäs i rifiuti vengono inceneriti e trasformati in energia. L’energia che si ricava da un chilogrammo di rifiuti equivale al quantitativo di acqua calda per una doccia di sette minuti o a tre ore di alimentazione di un computer.
Vendite: 124 milioni di euro
Numero dipendenti: 780
Quantità di rifiuti trattati: 1.140.000 tonnellate
Energia per riscaldamento prodotta: 1.500.000 MWh
Energia elettrica prodotta: 250.000 MWh
(Dati 2016)
Situato nel parco industriale di Sävenäs, l’impianto Renova opera tutti i giorni dell’anno, 24 ore su 24. Dalla combustione di una tonnellata di rifiuti si ricavano 3,3 MWh di energia elettrica e termica.
Oggi siamo riusciti ad aumentare l’affidabilità operativa.
Göran Klamas, plant manager di Renova
L’impianto è costituito da tre enormi forni, i quali dispongono di ventilatori primari, che forniscono l’ossigeno necessario alla combustione a temperature anche di 1.000 °C, ventilatori secondari, che provvedono alla circolazione dell’aria all’interno della camera di combustione, e ventilatori di ricircolo per l’essiccazione dei rifiuti.
L’importanza di questi ventilatori è estrema, poiché il cedimento di anche solo uno di essi provoca costosi fermi dell’ordine di 100.000 euro. Per garantirne l’affidabilità ed evitare fermi non programmati, negli ultimi dieci anni la Renova ha collaborato con la SKF.
Proactive Reliability Maintenance (PRM)
Il programma SKF Proactive Reliability Maintenance (PRM) individua le cause all’origine dei guasti e fornisce gli strumenti per impedire che si ripetano. SKF effettua la diagnosi sistematica delle cause dei cedimenti attraverso le migliori prassi di manutenzione predittiva e altri processi. Con il contratto PRM, la SKF ha aiutato l’impianto di termovalorizzazione dei rifiuti di Renova, nella Svezia occidentale, a migliorare l’efficienza operativa attraverso attività di riparazione, misurazione e analisi di lubrificanti e cuscinetti.
“In passato le perdite di produzione per interventi urgenti di manutenzione si aggiravano intorno a 1.000 ore all’anno”, osserva Göran Klamas, plant manager della business area recycling di Renova. “Oggi siamo riusciti ad aumentare l’affidabilità operativa e a programmare i fermi, a tutto vantaggio della produttività”.
Questo risultato può essere in larga misura attribuito alla collaborazione tra Renova e SKF, che è stata incentrata sul programma SKF Proactive Reliability Maintenance (PRM), il quale ha permesso di migliorare notevolmente la stabilità operativa del macchinario rotante. (Vedere riquadro).
Attraverso il PRM, la SKF ha potuto creare un registro di circa 40 macchine critiche Renova e ottenere in modo rapido una visione della situazione sotto forma di relazioni e indicazioni visive, atte a evidenziare la necessità di interventi di manutenzione aggiuntivi. Le misurazioni segnalano chiaramente agli operatori il profilarsi di problemi imminenti al macchinario, così da consentire loro di intraprendere le opportune azioni correttive prima di incorrere in situazioni di emergenza.
“Può essere il caso del disallineamento ricorrente di una macchina”, dice Jennie Lindahl, service coordinator di SKF, che da molti anni esegue le misurazioni nell’impianto. “Misurando la forma delle inflessioni in condizioni di esercizio (ODS, Operating Deflection Shape), possiamo identificare la causa, imputabile, per esempio, a una deformazione della base su cui poggia, che necessita di essere corretta”.
Considerate le severe condizioni dell’ambiente in cui si opera, anche l’analisi dei lubrificanti può servire a identificare eventuali problemi. “L’analisi dei lubrificanti consente di individuare cause di fermi anche molto diverse da quelle supposte prima”, commenta Lindahl. “Lubrificazione inadeguata, presenza di acqua o temperature troppo elevate dei cuscinetti possono essere tra le cause che aumentano il rischio di formazione di sostanze chimiche nocive. Mentre l’ossidazione del grasso o la variazione di viscosità e la formazione di acido possono danneggiare la superficie dei cuscinetti”.
In sostanza, queste analisi contribuiscono a evitare cedimenti catastrofici.
E grazie al programma PRM, è possibile evitare gli interventi d’urgenza. Nel 2016 l’impianto Renova ha registrato zero fermi non programmati, mentre nei dieci anni precedenti se ne erano verificati cinque. Nello stesso anno, con il contratto PRM sono stati eseguiti solo due interventi di manutenzione programmati, due in meno di quelli che venivano eseguiti nei dieci anni precedenti.
Grazie alla maggiore affidabilità operativa, Renova ha ridotto i costi di manutenzione e ha impiegato le risorse per altri investimenti. Dice Klamas: “Le perdite di energia imputabili a fermi imprevisti costano circa 100.000 euro al giorno. Grazie al fatto che ora i ventilatori sono stabili, possiamo concentrarci a rendere più efficiente ed ecosostenibile il processo di combustione”.