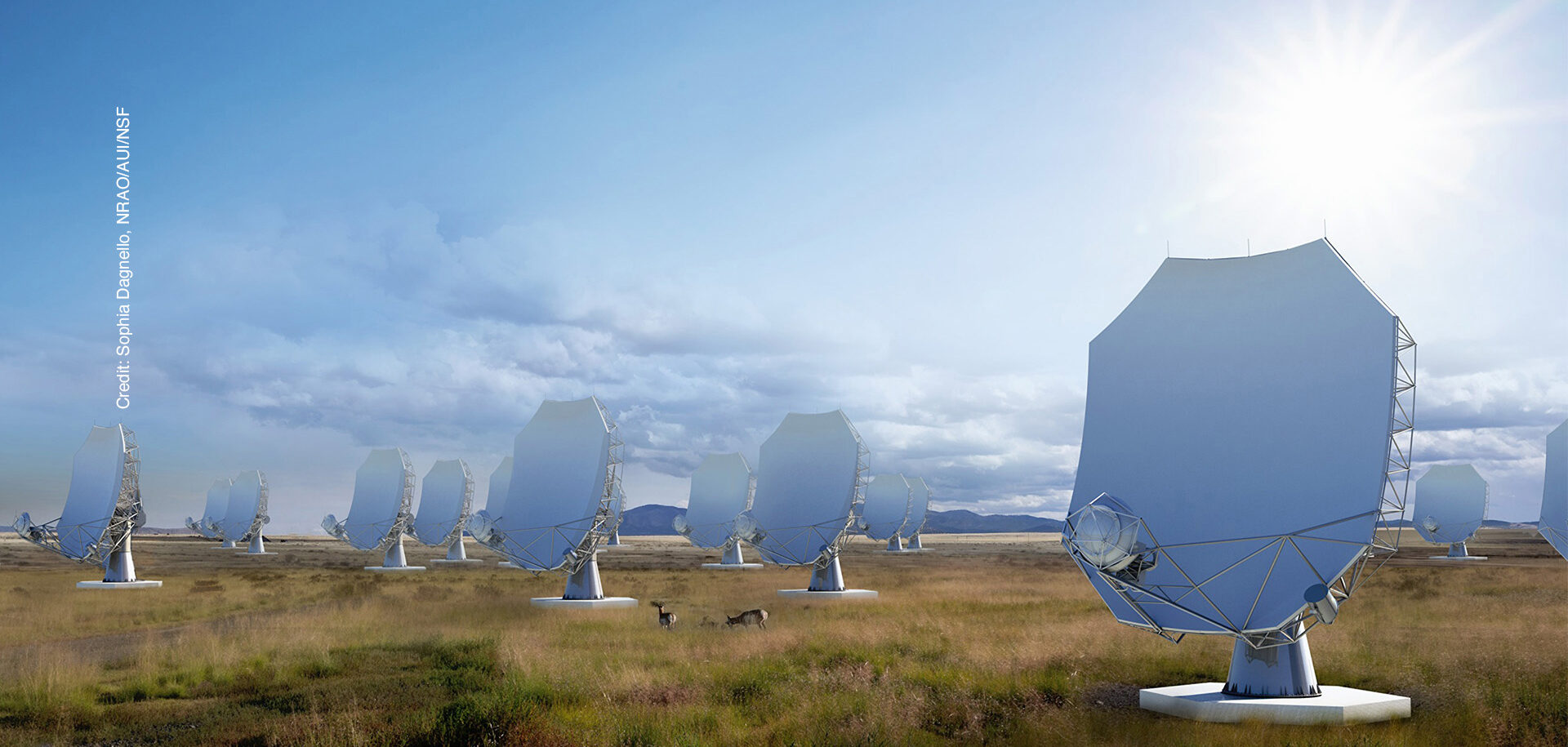
Across the heavens
SKF technology prepares to help astronomers see farther than ever before.
mtex antenna technology, a small company based in Germany, has been chosen to produce key components for a project that will combine hundreds of radio telescopes into the largest and most ambitious astronomical instrument ever built. The success of its design hinges on precision bearing technology from SKF.
mtex grew out of a specialized consulting firm founded by Dr Karl-Heinz Stenvers, who spent more than 40 years working on the antenna design of many of the world’s largest radio telescopes. Today, under the leadership of Dr Stenvers’ son, Lutz Stenvers, mtex offers a full range of design, manufacturing, installation and upgrade services for advanced radio antennas. That combination of capabilities and expertise helped mtex secure the contract to build the antennas for the next-generation Very Large Array (ngVLA), a telescope system that aims to peer deeper into the universe than ever before.
Go big or go home
Astronomers have been using instruments to study the night sky since Galileo Galilei, the grandfather of modern stargazing technology, began building and selling handheld telescopes in 1609. Those instruments have been getting bigger ever since. Today’s largest optical telescopes have mirrors about 10 metres in diameter. The aptly named Extremely Large Telescope, currently under construction in Chile, will have a vast mirror 39.3 metres in diameter.
Radio telescopes, which detect electromagnetic radiation at wavelengths longer than visible light, have become even larger. These telescopes can use metal plates instead of mirrors in their reflectors, simplifying construction and allowing for truly gigantic designs. Several countries operate instruments 70 to 100 metres in diameter. The world’s largest is China’s Five-hundred-meter Aperture Spherical Telescope (FAST).
Is bigger always better?
Over the past few decades, giant telescopes have enabled extraordinary discoveries, from proving the existence of black holes to detecting planets orbiting distant stars. But building ever-larger telescopes is fraught with difficulties. For example, huge telescopes are enormously expensive to build and difficult to maintain. The Arecibo radio telescope, a 300-metre dish in Puerto Rico, collapsed in 2020 when the cables supporting its receiver assembly failed, sending the component crashing into the dish below.
Large telescopes are also tricky to control. The very largest radio telescopes, such as FAST and Arecibo, use fixed dishes. Astronomers point the telescope by moving the receiver assembly, an approach that allows them to look at only a small region of the sky. Smaller giants are fully steerable, but that requires heavy machinery and advanced control systems capable of precisely manoeuvring their huge dishes to locate and track target objects.
Arrays are the way
These technical and financial challenges have encouraged the scientific community to explore alternatives to ever-larger individual instruments. One way is to use software to combine images from several smaller telescopes. This approach, known as astronomical interferometry, allows scientists to create a virtual mirror with an aperture equal to the separation between the telescopes, which can be hundreds or thousands of metres. Since computers first became powerful enough to handle the complex mathematics required to assemble these intricate images, arrays of radio telescopes have sprung up around the world.
Among the most famous is the Very Large Array (VLA), a group of 28 radio telescopes, each 25 metres in diameter, arranged in a “Y” configuration on a desert plain in New Mexico in the United States. The VLA telescopes are mounted on railroad tracks so that they can be repositioned to suit the needs of astronomers. In its largest configuration, the farthest instruments are 21 kilometres from the centre of the array. Built in the 1970s and upgraded in the 2010s, the VLA has been a star performer for decades, providing rich data for the scientific community and regularly appearing on screen as a backdrop in science fiction movies.
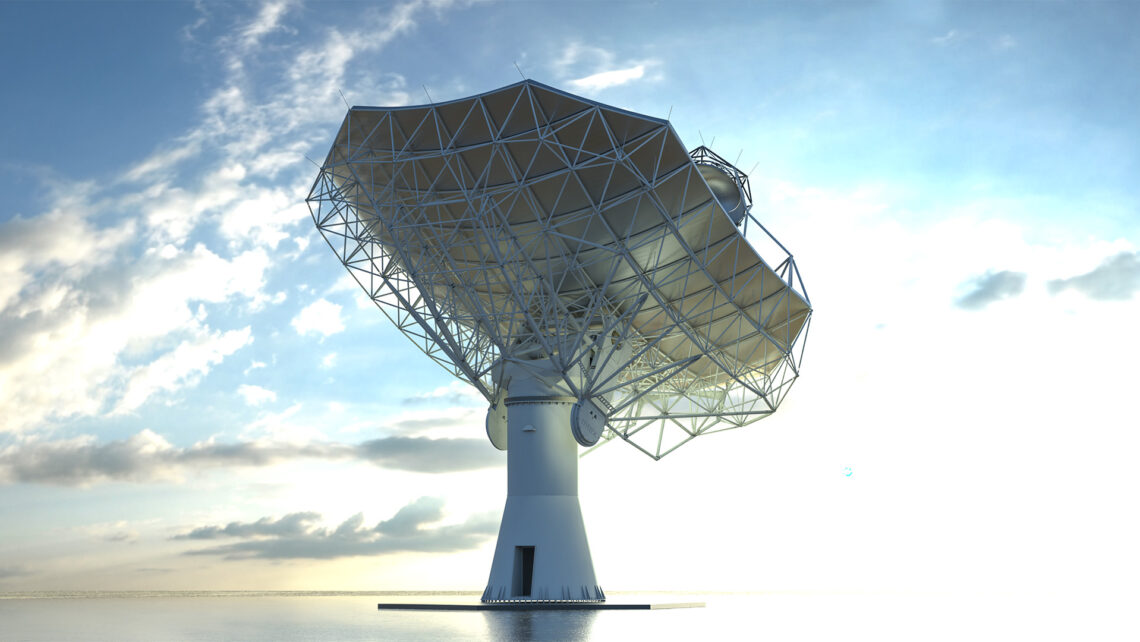
The Next Generation
With the VLA now well past its 40th birthday, its owner, the National Radio Astronomy Observatory (NRAO), is now embarking on an ambitious $2 billion programme to replace the instrument with an updated design. Following the astronomy community’s convention of naming telescopes in the most direct way possible, the new facility will be known as the next-generation Very Large Array (ngVLA).
The ngVLA, however, will take the application of astronomical interferometry to a new level. It will use smaller individual dishes: 18 metres in diameter instead of the 25 metres of its predecessors. But it will use many more of them. The core array will include 244 antennas arranged in a series of spiral arms on the current VLA site. An additional 30 dishes will extend those arms over more than 1,000 kilometres in the American Southwest, with additional dishes positioned across the continental United States, Hawaii and Puerto Rico to create a truly continental-scale virtual telescope.
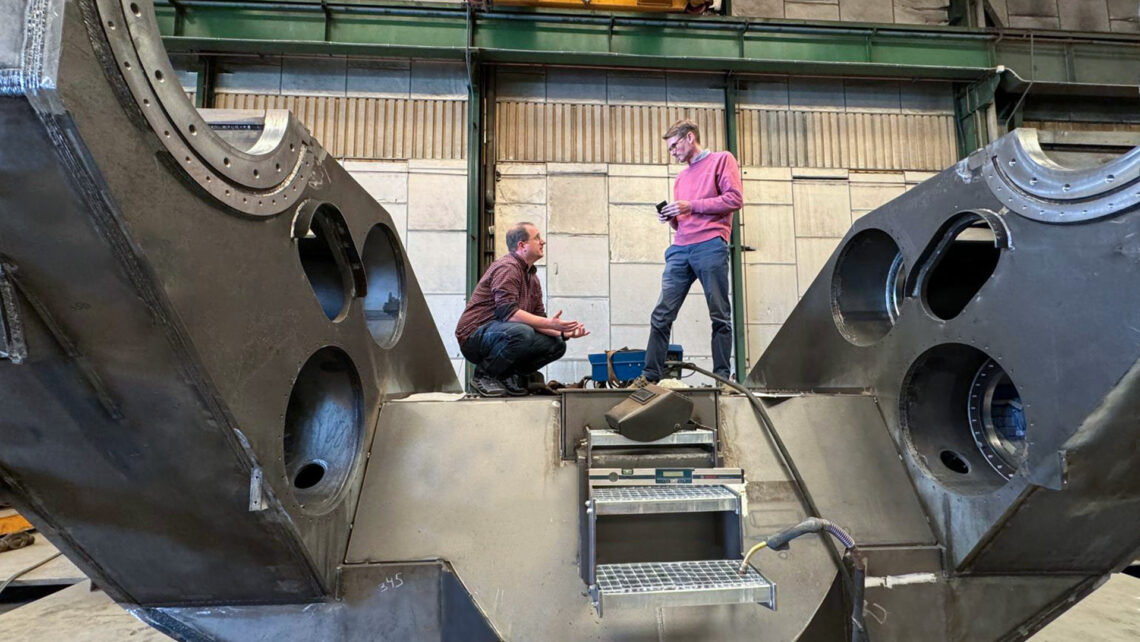
Dish of the Day
When Lutz Stenvers spoke to Evolution in May 2024, his team was en route to New Mexico with the first prototype ngVLA antenna. The new dishes aren’t really dishes at all. While most radio telescopes use a symmetrical circular reflector, with the receiving elements suspended above its centre, the ngVLA antennas will be a more rectangular shape, with the receiver suspended above its bottom edge. Called an “offset Gregorian antenna”, the design has been shown to provide higher performance than a symmetrical dish of the same overall size.
The specification calls for an angular accuracy of three arc seconds.
Lutz Stenvers, mtex antenna technology
“The design has many advantages over a circular antenna, but it is much more difficult to build,” says Stenvers. “The supporting framework for a circular antenna consists of a few rings; for ngVLA we needed a much more complex framework.”
And the supporting framework for the reflector surface is critical to its performance. To keep images in focus, the framework must hold the aluminium reflector panels in place to within fractions of a millimetre on a structure that moves constantly during operation and must operate for decades outdoors, exposed to strong winds and harsh weather.
To add to the complexity, the ngVLA project requires a design that can be packed into a small space for easy logistics and transportation, while still being able to be assembled quickly and accurately on site. And with hundreds of identical units required, cost is also a key consideration.
mtex’s solution is to support the reflector on a triangulated lattice of more than 700 steel tubes, connected by high-precision ball joints that lock together to maintain the desired final shape. The receiver package, which captures the reflected radio waves, is supported by 8-metre-long tubes of carbon fibre, a material chosen for its extreme stiffness.
The entire assembly is mounted on a steel tower that houses the motors and control systems used to steer the antenna. Disassembled, all the components are designed to fit into a few standard shipping containers. Each is marked with a unique QR code to ensure that the construction team can quickly assemble the right parts in the right order.
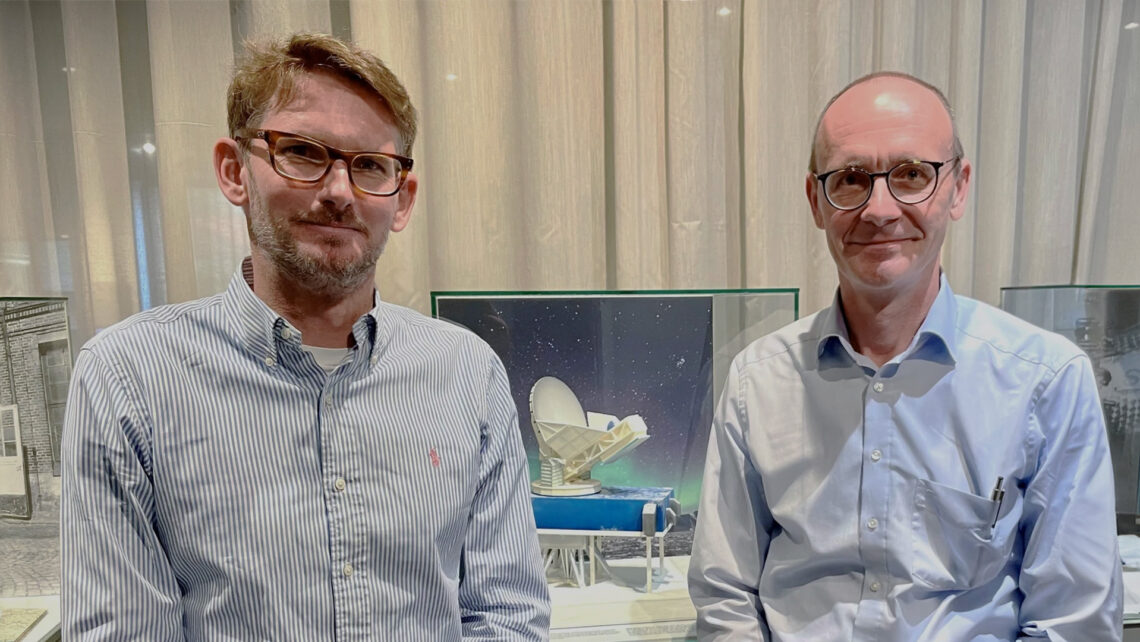
Life in slow motion
A radio telescope is both a mechanism and a structure. The dish and receiver rotate together around two axes to keep the instrument pointed at its target in the sky. This motion takes two forms: slow, as the telescope is slewed between targets, and very slow, as the control system makes tiny adjustments during operation to track the target while compensating for wind and the steady rotation of the Earth.
“The specification calls for an angular accuracy of three arc seconds,” Stenvers explains. That is less than a thousandth of a degree. On Earth, it would be accurate enough to shine a laser beam at a 1-metre-wide target from 69 kilometres away.
Achieving this level of accuracy requires sophisticated sensors and control software, as well as extremely precise mechanical components. For the two elevation bearings that rotate the telescope between 12 degrees and 90 degrees above the horizon, mtex selected SKF as its preferred supplier.
The two companies have been working together for about two years and defined a bearing solution that could meet the telescope’s requirements for high load capacity, low friction and extreme precision. “The basis of the solution are SKF Explorer class Spherical Roller Bearings,” says Juergen Blum, manager sales quality and process at SKF. “Each bearing has an outer diameter of 720 millimetres and weighs 290 kg. This is a type of bearing you would usually find in large paper mills or mining equipment.”
In these more typical applications, bearings of this type must withstand high speeds, shock and vibration. In a telescope, says Stenvers, “it is virtually stationary.” The telescope application, however, places different demands on the bearing system. It must be able to support the load with minimal clearance. And its motion, although slow, must be smooth and highly predictable.
SKF’s design and application engineering teams carried out extensive simulations to find the right system configuration for the job. They selected a reliable lubrication system supplying the right amount of grease at the right time to minimize stick-slip at the start and reduce friction and wear during the operation. They manufactured the bearing rings to unusually high accuracy, minimizing thickness variations around the ring that could cause the axle to wobble during motion. The bearings for the prototype are assembled on specially tapered sleeves that allow the final clearance to be precisely adjusted during assembly and, thanks to their design, further reduce radial runout during operation.
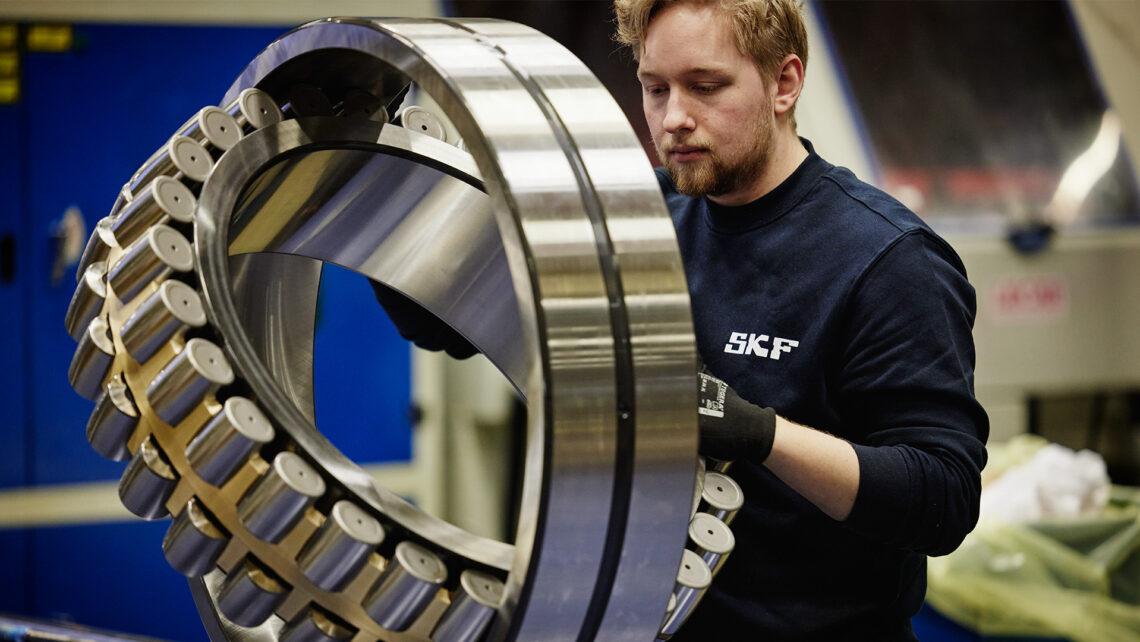
Toward first light
In early summer 2024, an SKF team will travel to Spain to help mtex install and adjust the bearings on the prototype telescope. It will then be disassembled and shipped to its final destination in New Mexico where mtex will spend two months testing the motion and control systems before handing the instrument over to its customer.
The NRAO team will then install a prototype sensor package on the instrument, with the goal of taking the first images – a step known in the telescope world as “first light” – in early 2025. This will kick off an 18-month period of intense testing and refinement. If all goes according to plan, the NRAO will begin large-scale production of antennas for the ngVLA project in 2027, supporting a construction process that is expected to take a decade.
For Lutz Stenvers, this is an exciting time, but also a poignant one. His father died a few weeks before assembly of the first ngVLA antenna began. The prototype will be named the Dr Karl-Heinz Stenvers Telescope in his memory.