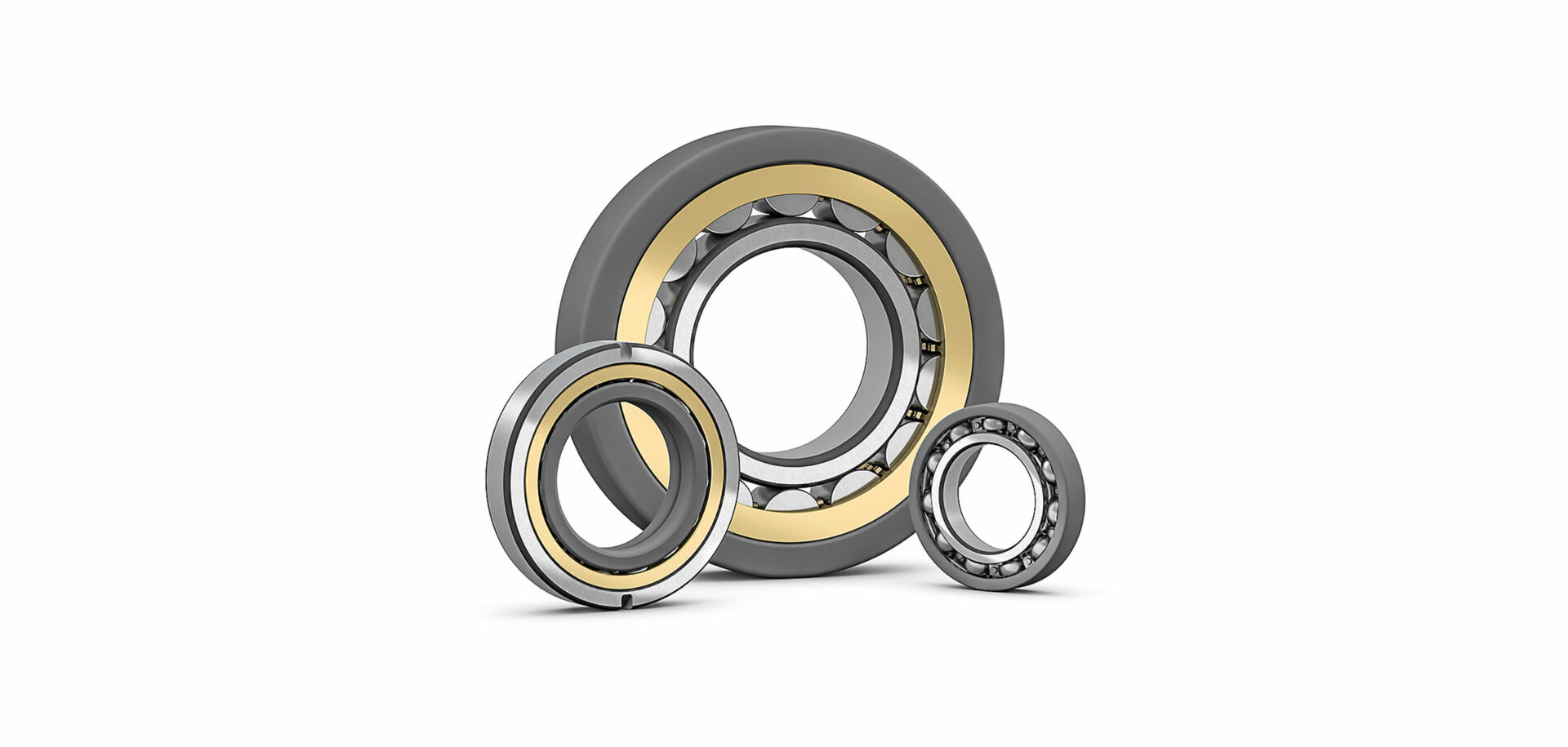
Cómo evitar daños de corrientes eléctricas
Los rodamientos aislados evitan las fallas prematuras que pueden causarles las corrientes eléctricas parásitas. Las propiedades del aislamiento deben mantenerse estables independientemente de las condiciones del entorno, especialmente cuando los rodamientos se almacenan, manipulan y utilizan en climas húmedos.
¿Por qué aislar los rodamientos?
Se pueden producir daños en los rodamientos cuando corrientes eléctricas utilizan el contacto rodante como vía de transmisión.
Actualmente hay diversas publicaciones que abordan esta cuestión [1, 2, 3, 4].
En estado de conductor eléctrico, el rodamiento permanece en reposo y muestra una resistencia óhmica baja. Debido al contacto eléctrico relativamente bueno de metal a metal, solo las corrientes de un amperaje muy alto, como las corrientes de soldadura, pueden destruir la superficie del camino de rodadura.
El estado resistivo está presente en el rodamiento en un régimen de lubricación mixta, con una mayor resistencia óhmica. En este régimen, corrientes eléctricas leves, del rango de unos pocos amperios, son potencialmente peligrosas.
En estado capacitivo, el rodamiento se halla en un régimen de película lubricante completa, y actúa como un condensador eléctrico con un voltaje de ruptura específico. Si la potencia del campo eléctrico aplicado presente en la película lubricante de la zona de contacto es lo suficientemente alta (superior al valor umbral), se producirán descargas eléctricas, denominadas EDM (mecanizado por descarga eléctrica o electric discharge machining).
Todos los casos de daños tienen un factor en común: se produce la fusión local del área de contacto del camino de rodadura, y cambian las propiedades del acero en esa área. Además, las propiedades del lubricante pueden sufrir alteraciones. Esto tiene un efecto negativo en el rendimiento del rodamiento, en forma de daños en el camino de rodadura y la lubricación y, en consecuencia, aumentan el desgaste y la vibración en el rodamiento. El efecto de las corrientes EDM, visible como microcráteres, se muestra en las figs. 1 y 2. Los microcráteres son una consecuencia de corrientes de alta frecuencia en el rodamiento. Hoy, los daños de este tipo se observan comúnmente en aplicaciones que utilizan convertidores de frecuencia. Una solución para contrarrestar los posibles efectos destructivos de las corrientes eléctricas dañinas es emplear aislamiento eléctrico integrado en el rodamiento.
INSOCOAT: un rodamiento recubierto por pulverización térmica
Los rodamientos INSOCOAT suministrados por SKF van provistos de un recubrimiento que aísla de la electricidad y que se aplica en las superficies externas del aro exterior o interior para integrar la función aislante en el rodamiento. El material del recubrimiento son óxidos cerámicos (fig. 3) y se aplican en el rodamiento mediante pulverización térmica. Comúnmente se usa Al2O3 puro. A veces se aplican mezclas de óxidos debido a propiedades eléctricas y mecánicas deseadas diferentes de los recubrimientos resultantes [5, 6]. Durante la pulverización, las partículas de óxido se transportan mediante una corriente de plasma caliente, en la cual se funden. Este gas o corriente de plasma caliente transporta la mayoría de las partículas fundidas hasta un sustrato tratado previamente, donde se enfrían y forman el recubrimiento deseado.
La fig. 4 muestra la microestructura del recubrimiento resultante en un aro exterior de rodamiento.
Después de la pulverización, el recubrimiento muestra una cierta cantidad de poros abiertos e interconectados, una propiedad común en los recubrimientos por pulverización térmica. La cantidad y el aspecto de la porosidad depende en gran parte de los parámetros del proceso de recubrimiento. Es fácil comprender que el cierre, el “sellado”, de esta porosidad es fundamental en el proceso de pulverización térmica. Esto reduce el riesgo de corrosión, mejora las propiedades mecánicas y mantiene constantes las propiedades aislantes, lo que es muy importante en climas húmedos.
La fig. 5 muestra un ejemplo de porosidad cerrada, un poro típico interconectado con poros más pequeños en un recubrimiento por pulverización térmica. En la bibliografía existente [5, 6, 7], ya se han debatido muchas estrategias diferentes de sellado. En recubrimientos por pulverización térmica con aislación eléctrica, lo más viable es una etapa de sellado con sellantes orgánicos. Los sellantes posibles tienen diferentes propiedades en términos de viscosidad, temperatura de curado, características de evaporación, encogimiento, etc. Es preciso evaluar minuciosamente todo el proceso, pulverización térmica y sellado, para obtener las propiedades del recubrimiento deseado.
Generación anterior de INSOCOAT: defectos y su solución
En diversas aplicaciones en climas muy calurosos y húmedos, se detectaron valores de resistencia al aislamiento bajos en la generación anterior de rodamientos INSOCOAT. La resistencia de los aislantes eléctricos es siempre una combinación de su superficie y resistencia en volumen [8]. Además de las propiedades fundamentales del material, ambas partes son una función de la humedad y temperatura. Mientras que la parte de resistencia de la superficie reacciona inmediatamente a un cambio de clima, la parte de resistencia en volumen cambia durante un período prolongado. Si las propiedades aislantes quedan fuera del rango deseado, hay que mejorar todo el sistema de recubrimiento aislante [5, 6, 7].
Experimentos en rodamientos de la generación anterior de INSOCOAT verificaron los problemas señalados por la experiencia de campo, analizando la resistencia eléctrica de INSOCOAT en contacto directo con el agua.1 Se observó que, durante un período largo, el recubrimiento absorbía agua y que el efecto era completamente reversible después del secado. Debido al largo tiempo del proceso de descenso de la resistencia, se han excluido las corrientes superficiales, la porosidad abierta o las grietas como causa raíz. Por lo tanto, el material del recubrimiento, el óxido y/o el sellante propiamente dicho tienen que ser la causa raíz. Como consecuencia de ello, se inició una extensa actividad de investigación y ensayos. Fue necesario evaluar diferentes estrategias de recubrimiento y sellado para encontrar una solución. Por ejemplo, se evaluaron diferentes materiales de polvo en aerosol, sellantes, procesos de curado y estrategias de pulverización térmica. Tal como se ha mencionado arriba, se realizó una primera evaluación en contacto directo con agua. Aun cuando este ensayo representa condiciones poco realistas (en aplicaciones reales, el rodamiento o el motor no está sumergido en agua), proporciona información muy rápida y sensible sobre el posible éxito o fracaso. En la fig. 6, se muestran algunos resultados de ejemplos positivos (V1 y V2) y negativos (V3), siempre en comparación con la generación anterior de la versión de rodamiento INSOCOAT. El V2 fue el mejor candidato para la nueva generación de INSOCOAT.
Nueva generación de rodamientos INSOCOAT
La fig. 7 muestra, en condiciones reales, el rendimiento eléctrico de la nueva generación de rodamientos INSOCOAT en comparación con la versión anterior. Esto significa que los rodamientos se montan de igual modo que en condiciones reales en campo y están expuestos a diferentes condiciones atmosféricas en una cámara climática. La disposición de los puntos de medición se muestra en la fig. 8. Muestra que la nueva versión INSOCOAT es mucho menos sensible a la humedad que la generación anterior de rodamientos.
Conclusión: nueva generación de rodamientos INSOCOAT
La nueva generación de rodamientos INSOCOAT se ha optimizado para que posea una resistencia de aislamiento eléctrico alta y estable, incluso en entornos húmedos. Las condiciones de validación se seleccionaron para simular también climas extremos.Además de los datos aquí presentados, se controlaron y validaron otros parámetros, como el rendimiento a bajas y altas temperaturas (de –40 °C a +150 °C), el rendimiento mecánico (adherencia del recubrimiento, tensiones de montaje/desmontaje, resistencia a los impactos), el rendimiento ante voltajes elevados, de hasta 6 kV CC, y la compatibilidad con distintos medios.
Incluso a niveles de humedad relativa superiores al 90%, a una temperatura de 30 °C, la resistencia óhmica del rodamiento sometido a ensayo 6316/C3VL0241 se mantiene superior a 2 000 MΩ, mientras que la versión anterior desciende hasta algo más de 50 MΩ.
1 Agua con una cierta conductividad.
INSOCOAT es una marca registrada del Grupo SKF.
Referencias
[1] Preisinger G.: Prevention of electric erosion in bearings, SKF Evolution, #2-2001 (http://evolution.skf.com/prevention-of-electric-erosion-in-bearings/)
[2]Mütze A.: Bearing currents in inverter-fed AC-motors, TU Darmstadt, 2004
[3] SKF, Bearing damage and failure analysis, PUB BU/13 14219 EN, 2014
[4] ISO 15243, Daños y fallas en rodamientos: términos, características y causas, segunda edición, 2017
[5] Fauchais P.L.: Thermal Spray Fundamentals, Springer, 2014
[6] Pawlowski L.: The science and engineering of thermal spray coatings, Wiley, 2008
[7] Knuuttila J.: Sealing of thermal spray coatings by impregnation, ASM, 1999
[8] IEC 62631-3-3: Dielectric and resistive properties of solid insulating materials – Parte 3-3: Determination of resistive properties (DC methods) – Insulation resistance, 2015