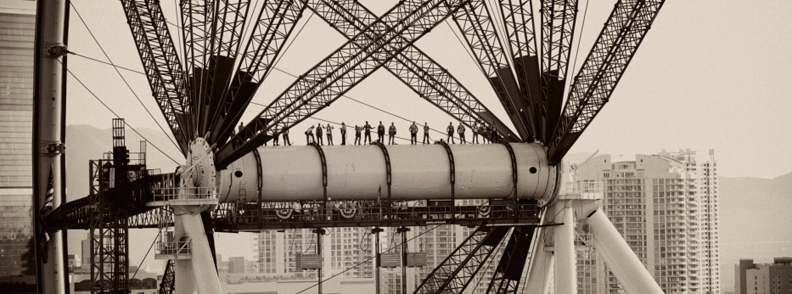
Использование моделирования при проектировании самого большого в мире колеса обозрения
При проектировании самого большого в мире колеса обозрения High Roller в Лас-Вегасе требовались исключительно качественные компоненты и передовые инженерные решения. SKF совместно с компанией Arup, выполнявшей проектные работы, а также строительной подрядной организацией American Bridge разработала подшипниковый узел для главного вала колеса. При этом были использованы новейшие инструменты моделирования для обеспечения надёжной круглосуточной работы аттракциона.
Колесо обозрения High Roller в Лас-Вегасе высотой 168 м является самым большим в мире. Каждая из 28 кабин оснащена кондиционером и вмещает до 40 человек. Поездка занимает 30 минут, в течение которых можно полюбоваться потрясающими видами оживлённого города. Колесо расположено на территории комплекса LINQ, инвестиции в который составили 550 млн долларов США. Строительство аттракциона было анонсировано в августе 2011 г., а его открытие состоялось в марте 2014 г.
За блеском и красотой нового аттракциона стоит настоящий инженерный подвиг – строительство гигантской конструкции, отвечающей самым строгим требованиям безопасности и эксплуатации. Подрядная организация American Bridge обратилась в SKF с просьбой разработать и поставить подшипниковую систему, которая должна была соответствовать спецификациям, составленным специалистами компании Arup, ранее принимавшей участие в строительстве гигантского колеса обозрения Singapore Flyer.
На колесе High Roller установлены два сферических роликоподшипника SKF, разработанных по индивидуальным требованиям. Каждый подшипник весит около 8,8 т, имеет наружный диаметр 2300 мм, внутренний диаметр 1600 мм и ширину 630 мм. Двухрядные сферические роликоподшипники оснащены 30 роликами в каждом ряду и являются крупнейшими из когда-либо произведённых на заводе SKF в Гётеборге. С целью определения оптимального радиального зазора подшипников была использована имитационная модель. Среди особенностей конструкции – отверстия для смазывания во внутреннем кольце W26, ролики с покрытием SKF NoWear и антифрикционное покрытие отверстия из PTFE. Кроме того, подшипниковая система оснащена автоматической системой смазывания и уплотнениями.
Помимо двух подшипниковых узлов SKF конструкция включает натяжной шкив диаметром 143 м, четыре стальные опоры, одну усиленную опору, фиксированный шпиндель, поворотную ступицу, трубчатый обод с диаметром трубы 2 м и 112 витых тросов в качестве спиц. Пассажирские кабины смонтированы с наружной части обода колеса, оснащены электродвигателями и могут вращаться независимо друг от друга для поддержания горизонтального положения пола кабины.
Критерии для проектирования
Перед разработчиками подшипниковой системы (рис. 1) стоял целый ряд сложностей ввиду повышенных требований к обеспечению безопасности и надёжности технического решения. Шпиндель и подшипник необходимо было проектировать с учётом тяжёлых нагрузок и значительных деформаций корпуса, а также различных процедур выверки соосности шпинделя. Согласно спецификациям на колесо обозрения, величина нагрузки на свободный конец составляет 1350 т. Натяжение каждого из 56 нижних радиальных тросов составляет 132 тонны, каждого из 56 верхних тросов – 47 тонн, а общее натяжение радиальных тросов – 4600 тонн.
Частота вращения вокруг оси Z была принята равной 0,033 об/мин. Имитационная модель учитывала воздействие постоянной ветровой нагрузки на каждый подшипник. Данная нагрузка воздействует на внешнюю часть наружного кольца каждого подшипника в направлении Z. Различные ветровые нагрузки использовались при моделировании различных рабочих условий. При расчёте величины перекоса подшипников учитывалось воздействие постоянных ветровых нагрузок, связанных с различными условиями эксплуатации, в то время как воздействие переменных ветровых нагрузок при моделировании не рассматривалось.
Ещё одним важным расчётным параметром было нагружение подшипников при монтаже. Выход подшипников из строя может привести к большим затратам и вызвать множество проблем, поэтому на всех этапах реализации данного проекта – от разработки до производства и сборки – специалисты SKF применяли методологию «6 Sigma». Поскольку подшипники являются ключевыми компонентами этого аттракциона, одним из требований было обеспечение их длительного срока службы. Для этого специалисты SKF использовали передовые инструменты моделирования, которые позволили разработать конструкцию подшипников и шпинделей в полном соответствии со строгими техническими требованиями.
Этапы реализации проекта
Конструкторская и аналитическая часть проекта состояла из четырёх этапов, в ходе которых применялось программное обеспечение для моделирования и анализа, чтобы обеспечить соответствие рабочих характеристик конструкции реальным эксплуатационным условиям. Первоначальной целью была оценка сложного взаимодействия всех компонентов в системе и определение ключевых эксплуатационных показателей. Также требовалось изучить деформацию корпуса, распределение контактной нагрузки и контактного давления на дорожки качения. Особое внимание уделялось оценке влияния нагрузок и деформаций на эксплуатационные характеристики подшипников.
Инструменты моделирования SKF предназначены для анализа подшипников качения и оценки многочисленных факторов, воздействующих на функционирование систем, например: зазоры, перекос, гибкость опорных конструкций, граничные условия и т.д.
Реализация проекта включала следующие этапы:
Этап 1 – Определение объёма работ по проекту и анализ конструкции по методологии «6 Sigma»
- Определение объёма работ по проекту
- Подготовка основной документации для анализа конструкции по методологии «6 Sigma»
- Сбор проектных данных
Этап 2 – Моделирование подшипников
- Создание модели подшипников с учётом расчётных нагрузок
- Учёт отклонений и деформаций в качестве исходных данных
- Создание динамической модели, включая все компоненты узла
- Нагружение, имитирующее натяжение тросов (4 расчётных варианта)
Этап 3 – Анализ прочности подшипников
- Воздействие переменных граничных условий
- Анализ внутренней конструкции подшипника
- Параметрическое исследование внутренней геометрии подшипника
- Анализ сепаратора подшипника методом конечных элементов (МКЭ)
Этап 4 – Анализ МКЭ осевого смещения втулки во время монтажа
- Создание модели МКЭ
- Анализ МКЭ осевого смещения без учёта нагружения тросов
- Анализ МКЭ осевого смещения с учётом нагружения тросов
Этап 1 включал в себя точную оценку объёма работ в рамках проекта и определение всех данных и документов, требуемых для анализа конструкции по методологии «6 Sigma». В частности, при моделировании по методологии «6 Sigma» применяется анализ видов и последствий отказов (FMEA) для планирования инженерных работ и разработки технических решений. Анализ FMEA позволил команде инженеров-конструкторов выявить потенциальные причины отказов на основе предыдущих проектов, а также провести подбор конструктивных параметров для моделирования. Данный вид анализа выполняла команда, состоящая из специалистов Arup, American Bridge и SKF.
На начальном этапе подготовки основной документации, связанной с анализом по методологии «6 Sigma», определялись параметры, влияющие на усталостную долговечность подшипника (рис. 2). Далее с использованием исходных данных была построена диаграмма граничных условий, по которой определялось взаимодействие подшипниковой системы с сопряжёнными компонентами, а также требуемые значения выходных величин. Параметрическая диаграмма использовалась для выявления всех проектных параметров, а также шумового воздействия, которые влияют на требуемые значения выходных величин и, следовательно, производительность.
Затем, на этапе 2 специалисты SKF перешли к созданию моделей. С учётом конфигурации подшипника был проведён анализ его рабочих характеристик с использованием разработанных имитационных моделей. Для этого использовалось программное обеспечение SKF Simulator (прежнее название Orpheus), которое предназначено для анализа возможностей применения подшипников качения в качестве полностью интегрированных систем. Данное ПО способно анализировать статическое и динамическое поведение системы. Сначала создаётся модель системы, состоящая из всех компонентов оборудования, включая подшипники, валы, зубчатые колёса и корпуса. Различное комбинирование сил, заданных перемещений и частот вращения может использоваться для определения нагрузок, воздействующих на компоненты. В ПО SKF Simulator могут быть заданы как нелинейные элементы, например, подшипники качения, так и различные линейные элементы, например, валы и корпуса. Последние должны функционировать линейно, а их жёсткостные и демпфирующие свойства получают методом конечных элементов. Для уменьшения количества степеней свободы используются специальные методы редукции, что позволяет сократить время, затрачиваемое на выполнение расчётов при анализе. В рамках данного проекта для анализа использовались четыре различных режима нагружения.
В статичных имитационных моделях подшипники моделируются в виде единичных сферических роликоподшипников, при этом для наружного кольца применяются четыре различных режима радиального и осевого нагружения. Внутреннее кольцо является неподвижным, тогда как наружное кольцо способно перемещаться во всех степенях свободы. Угол перекоса задавался в качестве относительного перекоса между внутренним и наружным кольцами в положительном и отрицательном направлениях (рис. 3).
После проведения данного анализа было исследовано влияние гибкости конструкции на рабочие характеристики подшипника, что потребовало упростить модели ступицы и шпинделя и описать их как абсолютно гибкие компоненты. После были выполнены дальнейшие имитационные исследования для четырёх режимов нагружения.
Один из ключевых аспектов при проектировании заключался в обеспечении соответствия рабочих характеристик подшипникового узла реальным условиям эксплуатации. На этапе 3 оценивалась величина прочности подшипника при изменении граничных условий и его внутренней геометрии. Этот анализ служит для оценки конструкции подшипника в конкретных условиях эксплуатации. Кроме того, был выполнен анализ сепаратора методом конечных элементов. После анализа внутренней геометрии подшипника первоначальный профиль роликов был изменён.
В ходе первоначальных расчётов была выявлена возможность совершенствования конструкции за счёт изменения профиля роликов и величины жёсткости вала/ступицы. Таким образом, были определены оптимальные характеристики модели, а также выполнен последующий имитационный анализ при различных режимах нагружения.
Анализ ресурса подшипника
Для достижения продолжительного и надёжного эксплуатационного ресурса подшипников колеса High Roller специалисты SKF использовали два метода расчёта срока службы подшипников: метод по DIN ISO 281 и комплексный метод расчётов усталостной долговечности подшипника SKF Advanced Fatigue Calculation (AFC).
При расчёте были использованы величины усталостной долговечности дорожек качения L2.53 и L10. Эксплуатационный ресурс подшипникаL10 предусматривает 90 %-е превышение расчётных величин при 10 %-й вероятности отказов. Усталостную долговечность с более низкой вероятностью отказа можно рассчитать с помощью распределения Вейбулла. Значение L2.53 было выбрано для повышения надёжности системы.
Все расчёты эксплуатационного ресурса для данного проекта выполнялись с использованием передовой программы моделирования SKF Simulator. Расчётный номинальный срок службы современных высококачественных подшипников может значительно отличаться от фактического срока службы в конкретной области применения. Эксплуатационный ресурс зависит от разнообразных факторов, включая условия смазывания, уровень загрязнения, перекос, правильный монтаж, климатические условия, возможное перемещение конструкции, уровни вибрации для стационарных подшипников, а также воздействие электрического тока.
При использовании метода расчётов SKF AFC учитывается совокупность контактных напряжений тела качения по всей длине ролика и оценивается общее количество циклов нагружения до окончания эксплуатационного ресурса. Данный метод также позволяет учитывать состояние смазочного материала, в том числе толщину смазочной плёнки и условия загрязнения в каждой отдельно взятой точке контакта.
Специалистам SKF удалось значительно увеличить величину L2.53 за счёт моделирования с использованием методологии «6 Sigma» и соответствующего имитационного анализа. Благодаря изменению стандартного профиля роликов подшипника, повышению жёсткости ступицы, использованию покрытия SKF NoWear с низким коэффициентом трения, а также применению автоматической системы смазывания, расчётный срок службы удалось увеличить более чем на 10 %.
По результатам моделирования были составлены рекомендации по оптимальной величине жёсткости ступицы и вала с учётом технических и экономических факторов. Величина контактного давления тел качения напрямую связана с жёсткостью ступицы и вала. Объём затрат на повышение жёсткости ступицы и вала был сопоставлен с ожидаемым увеличением эксплуатационного ресурса L2.53, в результате чего было принято решение повысить жёсткость компонентов. Специалистам SKF удалось обеспечить превышение расчётного срока службы подшипников по сравнению с указанным в проектных требованиях.
Также, по результатам моделирования были определены процедуры и оборудование, необходимые для монтажа подшипников. При монтаже потребовались инструменты для применения метода гидрораспора. Погрешность величины осевого смещения, необходимого для достижения требуемого внутреннего зазора в смонтированном узле, составила 2 % от расчётной величины. Данный результат впечатляет, учитывая сложность конструкции подшипникового узла.
Заключение
Применение методологии «6 Sigma» при моделировании позволило компании SKF спроектировать подшипниковый узел в соответствии с техническими требованиями проекта и провести имитационные испытания. Специалисты SKF учли все технические и экономические факторы, связанные с производством, транспортировкой и строительством конструкции. Подшипниковый узел SKF был успешно поставлен и смонтирован в срок.
NoWear – зарегистрированная торговая марка SKF Group.