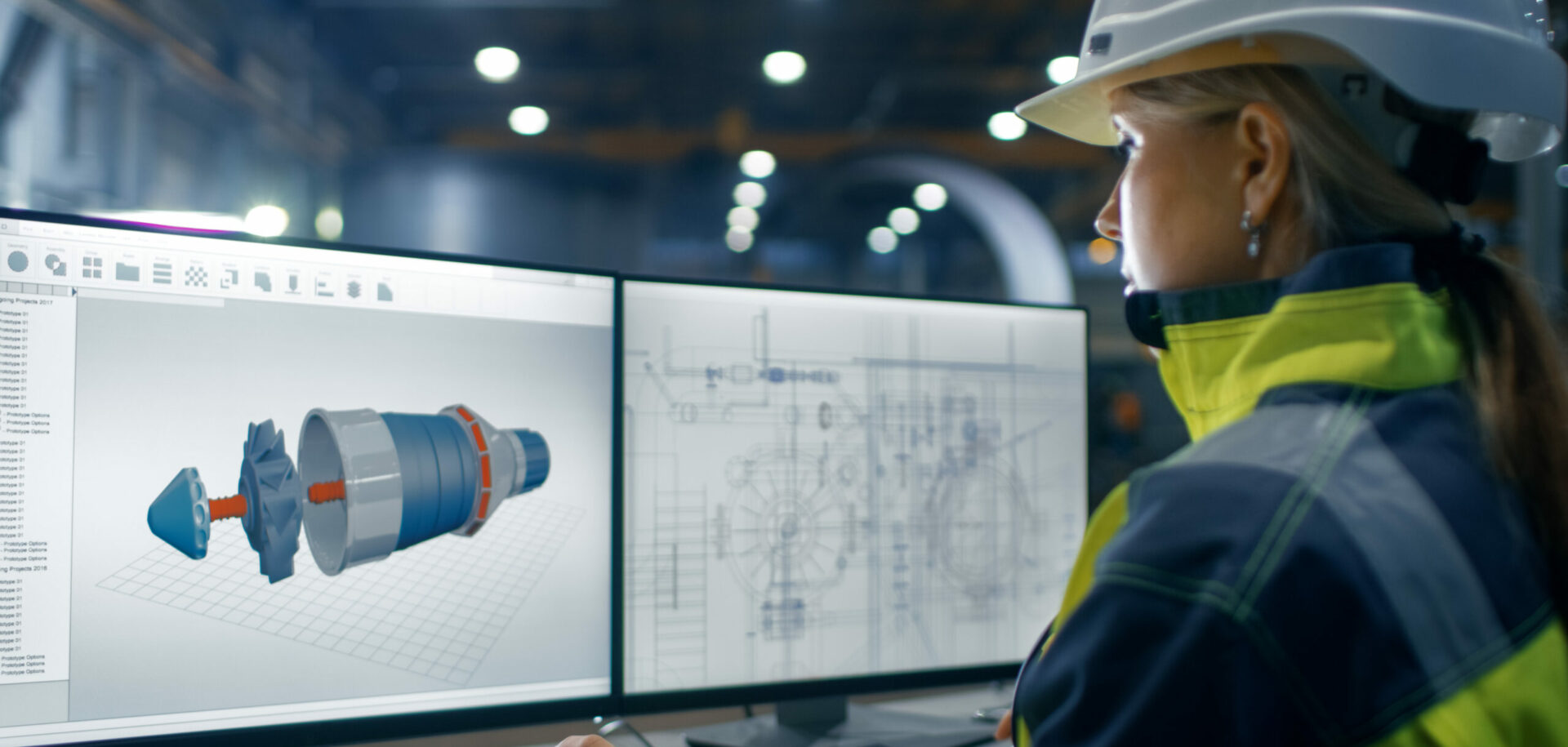
Modelado y simulación, elementos clave en el diseño del mayor observatorio giratorio del mundo
Cuando se construye el mayor observatorio giratorio del mundo, el High Roller de Las Vegas, es importante contar con los mejores componentes y procesos de ingeniería existentes. SKF intervino en el proyecto de construcción de los sistemas de husillo principal y cubo en colaboración con Arup, la empresa encargada del diseño, y el contratista American Bridge, aplicando las más modernas herramientas de análisis y diseño para asegurar un funcionamiento ininterrumpido.
Resumen
Para la construcción e instalación de mayor sistema de rodamientos jamás fabricado, destinado al observatorio giratorio más grande del mundo, SKF utilizó un equipo completo de expertos en diseño y análisis para asegurar que el rodamiento pudiera cumplir con los altísimos requisitos operativos. Un análisis cuidadoso utilizando sofisticadas herramientas de modelado y simulación de todos los aspectos del diseño identificó el sistema de rodamientos idóneo para el proyecto.
Enlaces relacionados
Contacto de venta
Randy A. Greaser, Randy.A.Greaser@skf.com
Con sus 168 metros de altura, el High Roller de Las Vegas se ha convertido en el mayor observatorio giratorio del mundo. Cada una de sus 28 cabinas tiene aire acondicionado y puede transportar hasta 40 pasajeros durante un viaje de 30 minutos, ofreciéndoles un bello panorama de esta trepidante ciudad. Es una de las atracciones del Linq, un barrio de comercios, restaurantes y actividades de ocio de Las Vegas que ha transformado el paisaje urbano y ha ofrecido a los visitantes una nueva perspectiva del gran bulevar Strip de la ciudad. La construcción del High Roller se anunció en agosto de 2011 y entró en servicio en marzo de 2014.
Tras la ostentación y glamour de esta nueva atracción de Las Vegas se esconde un hito en el campo de la ingeniería: construir una estructura gigantesca que debe cumplir rigurosas normas de seguridad y soportar duras condiciones operativas. El principal contratista, American Bridge, encargó a SKF el suministro y montaje del sistema de rodamientos del husillo. SKF, además de instalar este sistema, trabajó estrechamente con los ingenieros estructurales de Arup Engineers. Arup había participado también en el proyecto de la que, hasta ahora, era la mayor estructura equivalente del mundo, la Singapore Flyer.
El High Roller pivota sobre un par de rodamientos de rodillos a rótula, con un peso de aproximadamente 8,8 toneladas cada uno. Tienen un diámetro exterior de 2.300 mm, un agujero de 1.600 mm, y una anchura de 630 mm. Estos rodamientos de dos hileras de rodillos a rótula tienen 30 elementos rodantes por hilera y son los de mayor tamaño jamás fabricados por SKF en su planta de Gotemburgo. Para determinar la holgura radial óptima para este proyecto se utilizó un modelo de simulación. Entre sus características especiales pueden citarse orificios de lubricación W26 en el aro interior, rodillos revestidos SKF NoWear y revestimiento de PTFE en el agujero. Además, el sistema incorpora lubricación automática avanzada y dispositivos de obturación.
La estructura giratoria mide 143 metros de diámetro. Además de los dos sistemas de rodamiento de SKF, el armazón está compuesto por 4 patas de soporte de acero, una pata de un solo refuerzo, un husillo fijo, un cubo rotativo, un borde tubular de 2 m de diámetro, y 112 tramos de cable metálico en forma de varillas. Las cabinas de los viajeros están montadas en el borde exterior del observatorio y giran individualmente mediante motores eléctricos, a fin de mantener horizontal la base de la cabina en cada rotación completa.
Criterios de diseño
Al diseñar el sistema de rodamientos del husillo (fig. 1), se tuvo que hacer frente a diversos retos (en particular a la necesidad de suministrar una solución segura y fiable). En el husillo y rodamiento debían considerarse cargas pesadas y grandes deformaciones del soporte, con variaciones en la alineación del husillo. Según la especificación del observatorio, las cargas eran de 1.350 toneladas por extremo. En cada uno de los 56 cables radiales del fondo, la tensión era de 132 toneladas, y de 47 toneladas en los 56 cables de los extremos, siendo la tensión total radial de los cables de 4.600 toneladas.
El diseño se calculó con una velocidad rotativa en torno al eje Z de 0,033 rpm. Además, se tuvo en cuenta una carga constante del viento aplicada a cada rodamiento. Esta carga se aplica fuera del aro exterior de cada rodamiento, en la dirección Z. Se utilizaron diferentes cargas del viento en las diversas simulaciones de las condiciones de servicio. La desalineación de los rodamientos comprendía los efectos de las cargas de viento constantes asociadas a diferentes condiciones de servicio, aun cuando en las simulaciones no se incluyó el efecto de cargas de viento fluctuantes.
La carga sobre los rodamientos durante la instalación era otro factor clave a tener en cuenta. Las averías en éstos pueden ser extremadamente costosas y perjudiciales. Por ello, SKF aplicó al proyecto un enfoque Six Sigma desde el diseño hasta la fabricación y el montaje. Puesto que los rodamientos son un componente clave en esta prestigiosa atracción, era importante asegurar que se cumplieran los criterios de diseño de larga vida útil. Con este fin, SKF utilizó amplias y sofisticadas herramientas de análisis, basadas en los mejores principios de ingeniería de su clase para asegurar que el diseño del rodamiento y del husillo cumplieran los rigurosos requisitos de las especificaciones y de rendimiento.
Enfoque del proyecto
La parte de diseño y análisis del proyecto se dividió en cuatro fases, usándose mucho software de modelado y análisis para asegurar que el diseño final cumpliera con las condiciones operativas reales. El objetivo era evaluar la compleja interacción de todos los componentes del sistema e identificar los indicadores clave del rendimiento. Fundamentalmente, el propósito era estudiar la interacción en el sistema, incluyendo el efecto de las deformaciones de los soportes, la distribución de la carga de contacto y las presiones de contacto en los caminos de rodadura de los rodamientos. Se dedicó especial atención a evaluar los defectos de las cargas y deformaciones sobre la funcionalidad del rodamiento en términos de fuerzas y movimiento.
SKF posee herramientas de simulación avanzadas que se han desarrollado especialmente para el estudio de aplicaciones de rodamiento y para evaluar los múltiples factores que influyen en el comportamiento del sistema, como la holgura del conjunto de piezas, las desalineaciones, la flexibilidad de la estructura de soporte y las distintas condiciones límite.
Las fases del proyecto se realizaron como sigue
1ª fase – Definición del proyecto usando Diseño para Six Sigma (DfSS)
• Definición del proyecto
• Documentos básicos de DfSS
• Recopilación de datos de diseño
2ª fase – Análisis de simulación del rodamiento
• Modelo de rodamiento rígido con cargas concentradas
• Flexiones y deformaciones como parámetros
• Modelo flexible incluyendo los componentes del cubo y husillo
• Carga presentada en forma de tensión de cable (4 casos de simulación)
3ª fase – Análisis de sensibilidad del rodamiento
• Efectos de cambios en las condiciones límite
• Revisión del diseño interno del rodamiento
• Estudio de los parámetros de la geometría interna del rodamiento
• Análisis de la jaula con EF
4ª fase – Análisis con EF de las fuerzas de calado “Drive up” del manguito durante la instalación
• Creación de modelo de EF
• Análisis con EF de las fuerzas de calado sin cargas de cables
• Análisis con EF de las fuerzas de calado con cargas de cables
La 1ª fase implicaba claramente la definición del proyecto y la identificación de toda la información y documentos precisos para adoptar un enfoque de Diseño para Six Sigma (DfSS). Parte de la metodología DfSS es el uso del Failure Mode and Effect Análisis (FMEA) para impulsar el desarrollo de las actividades y soluciones de ingeniería. El FMEA se utilizó para facilitar que el grupo de diseño identificara las causas potenciales de averías en base a experiencias anteriores, y sirvió como referencia en la selección de características de diseño, actividades de simulación y recomendaciones. El FMEA lo desarrolló un grupo compuesto por Arup, American Bridge y SKF.
En la práctica, el punto inicial para crear los documentos base del DfSS fue la identificación de los parámetros que influyen en la vida de fatiga del rodamiento (fig. 2) a fin de producir un diagrama límite que definiera las interacciones del sistema de rodamiento con sus alrededores, incluyendo los parámetros de entrada y valores deseados en el resultado. Otro diagrama, el P, se usó para identificar todos los parámetros de diseño que controlan el resultado, es decir el rendimiento, y los factores de ruido que tienen un efecto adverso sobre él.
SKF pasó entonces a la 2ª fase, generación y selección del concepto. Con una disposición de rodamientos en mente, se realizó un análisis de su rendimiento usando los modelos de simulación antes indicados. Esto implicó la aplicación del pack de software SKF Simulator (Orpheus), que ha sido desarrollado para investigar aplicaciones de rodamientos en forma de sistema totalmente integrado. El Orpheus es capaz de analizar el comportamiento estático y modal de la aplicación de rodamiento. Primero se construye un modelo conectando todos los tipos de componentes de máquinas, como rodamientos, ejes, engranajes y soportes. Puede usarse una combinación arbitraria de fuerzas, desplazamientos prescritos, y velocidades de rotación para definir las cargas de los componentes, que pueden ser elementos especiales (no lineales), definidos dentro del SKF Simulator (es decir, los rodamientos), así como elementos arbitrarios como ejes y soportes. Estos últimos deben tener un comportamiento lineal, y su rigidez y propiedades de atenuación se obtienen mediante el método de elementos finitos. Se aplican métodos de reducción especiales (en los modelos originales de elementos finitos) para reducir el número de grados de libertad, y disminuir así el tiempo de cálculo de los análisis. En este proyecto se seleccionaron para análisis cuatro condiciones de carga diferentes.
En las simulaciones de modelos rígidos (estáticos), el rodamiento se modela como un rodamiento de rodillos a rótula con cuatro juegos diferentes de cargas radiales y axiales aplicadas al aro exterior. El aro interior se rectificó en todos los grados de libertad, mientras que el aro exterior podía moverse con total libertad. Se aplicó un ángulo de desalineación como desalineación relativa entre los aros interior y exterior en las direcciones positiva y negativa (fig. 3).
Tras este análisis, el modelado se centró en la observación del efecto de la flexibilidad estructural en el rendimiento del rodamiento, lo que supuso añadir al modelo el cubo y husillo, como componentes plenamente flexibles, antes de realizar simulaciones posteriores basadas en las cuatro opciones disponibles.
Uno de los aspectos clave del proyecto de diseño era asegurar que el conjunto del rodamiento pudiera cumplir con las condiciones esperadas en el mundo real. Durante la 3ª fase se comprobó la sensibilidad del rodamiento a cambios en las condiciones límite y geometría interna. Estos análisis sirvieron para evaluar el diseño del rodamiento en condiciones reales. SKF realizó exámenes posteriores para estudiar este fenómeno. Uno de ellos estaba relacionado con la sensibilidad del rodamiento a cambios en las condiciones límite y la geometría interna. Además, se efectuó un análisis de la jaula con EF. El análisis de la geometría interna del rodamiento condujo a la revisión del perfil de rodillos inicialmente propuesto.
Procesos de optimización iniciales identificaron la posibilidad de mejoras de vida útil variando el perfil de los rodillos y la rigidez del eje/cubo. Se seleccionó el diseño óptimo y se realizaron simulaciones posteriores con las diversas condiciones de carga.
Análisis de la vida del rodamiento
Tal como se ha indicado antes, es necesario que los rodamientos del High Roller tengan una vida útil larga y fiable. Para este fin, SKF usó dos importantes métodos para el cálculo de la vida útil de los rodamientos. El primero fue el DIN ISO 281. El segundo, el método SKF Cálculo de Fatiga Avanzado (AFC) de la vida útil.
Los valores referenciados de la vida de fatiga calculada del rodamiento son los de los caminos de rodadura L2.53 y L10. La vida útil L10 se define como la del 90 % de los rodamientos que exceden el valor calculado con el 10 % de probabilidad de avería. La vida de fatiga con una probabilidad de avería inferior puede calcularse utilizando una distribución de Weibull, con un factor de configuración igual a 1,5 y un factor de forma elegido apropiadamente. Se eligió L2.53 para incrementar la fiabilidad del sistema.
Todos los cálculos de vida útil para este proyecto se realizaron utilizando el avanzado programa de simulación SKF Simulator. En rodamientos modernos de alta calidad, la vida nominal o básica puede desviarse significativamente de la vida de servicio que corresponda a una aplicación dada. La vida de servicio en una aplicación concreta depende de la influencia ejercida por diversos factores, incluyendo la lubricación, el grado de contaminación, la desalineación, una instalación correcta, condiciones del entorno, movimientos estructurales, vibraciones mientras el rodamiento es estacionario, y descargas de corriente eléctrica.
El método SKF Cálculo de Fatiga Avanzado (AFC) de la vida útil toma en consideración la integración completa de las tensiones de contacto de la longitud de los rodillos, y evalúa el número total de ciclos de tensión hasta que se consume la vida útil de todo el sistema sometido a cargas. El SKF AFC también incorpora las condiciones del lubricante, teniendo en cuenta el espesor de la película operativa y la contaminación de cada contacto.
SKF logró aumentos significativos de L2.53 graciasal proceso DfSS y al análisis de simulación resultante. Modificando el perfil del rodillo de rodamiento estándar, mejorando la rigidez del cubo, añadiendo la baja fricción del NoWear de SKF –un revestimiento de los rodillos con carbono resistente al desgaste–, y especificando un sistema de lubricación automático, la vida útil calculada se incrementó en más del 10%. Al contrario de lo que suele ocurrir -lo habitual es que un solo diseño sirva para distintos equipos-, se fabricaron rodamientos exclusivos para esta aplicación. SKF modificó el perfil de los rodillos para cumplir con las condiciones de baja velocidad y elevadas cargas de la aplicación.
Diversas simulaciones proporcionaron a SKF los datos para recomendar la mejor rigidez en el cubo y eje, teniendo en cuenta consideraciones técnicas y económicas. Las presiones de contacto de los elementos rodantes están relacionadas directamente con la rigidez del cubo y eje. El precio de mejorar la rigidez del cubo y eje se comparó con la mejora esperada en la vida útil L2.53. En base a esos estudios, se adoptó la decisión de mejorar la rigidez de los componentes del cubo y eje. Bajo todas las condiciones se superaron los requisitos de vida útil.
Finalmente se usaron los resultados de la simulaciones para determinar los procedimientos y equipos precisos para la instalación. Las simulaciones del procedimiento de instalación fueron casi idénticas al montaje real en el lugar de la obra. Durante la instalación, tal como se había pronosticado, fue necesario recurrir a la inyección hidráulica. El calado axial preciso para conseguir la holgura interna montada final estaba dentro del 2% del valor calculado. Un dato impresionante, considerando la complejidad del diseño del cubo.
Conclusión
El enfoque Six Sigma y las herramientas de simulación proporcionaron a SKF los instrumentos necesarios para diseñar una solución de montaje de cubo que cumplía con los requisitos técnicos del proyecto y, al mismo tiempo, tenía en consideración las limitaciones de fabricación, transporte, construcción y financiación. La solución de husillo ofrecida por SKF se entregó a tiempo y cumpliendo con el presupuesto.
NoWear es una marca registrada del Grupo SKF.