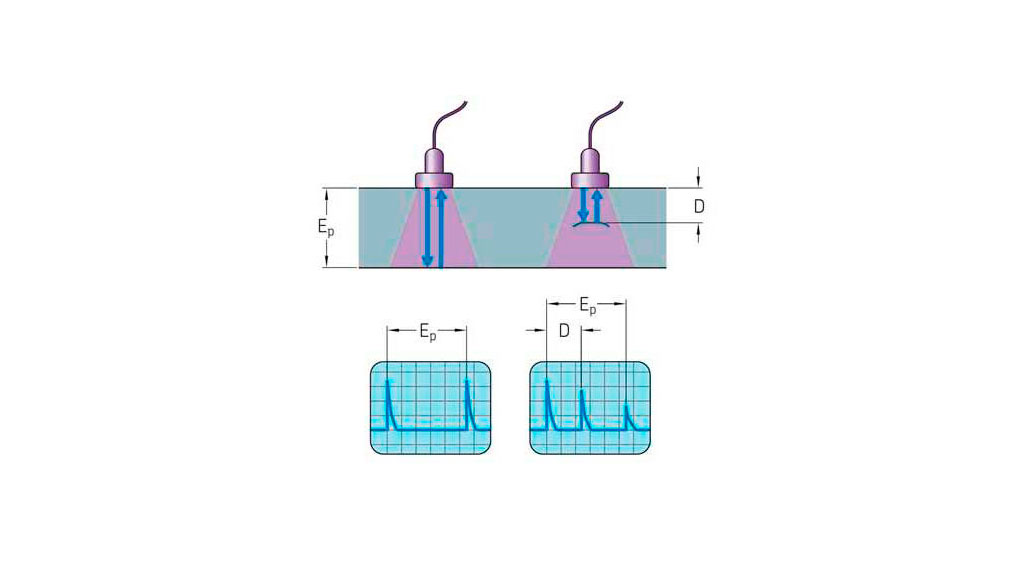
Эффективная форма контроля в SKF
Для поддержания постоянного уровня качества продукции SKF использует несколько методов неразрушающего контроля.
РЕЗЮМЕ
SKF стремится гарантировать качество производимых и восстанавливаемых изделий путём обеспечения высокой надёжности контроля в ходе всех производственных процессов. Неразрушающий контроль – один из ключевых методов контроля, который SKF постоянно стремится усовершенствовать с помощью стандартизации и разработки новых технологий. Повышение надёжности НК в SKF обеспечивается привлечением квалифицированного персонала и использованием соответствующего оборудования, точно описанных процедур и высокого уровня автоматизации. SKF также готова к использованию новых возможностей, доступных благодаря цифровым данным НК, а также данным, получаемым в течение всего процесса изготовления подшипников SKF.
Современные методы неразрушающего контроля (НК) применяются в SKF при изготовлении продукции, проведении работ по восстановлению и текущих проверках во время эксплуатации. Они необходимы для подтверждения целостности и надёжности изделий, для контроля производственных процессов и снижения производственных затрат, а также для поддержания постоянного уровня качества в соответствии с техническими требованиями компании.
Центр технологии качества (QT) – централизованная группа в составе подразделения SKF Group Technology Development, которая работает над стандартизацией и разрабатывает методы контроля качества на всех предприятиях SKF. Важной областью, в которой эта группа стремится к стандартизации производственных процессов в SKF, является неразрушающий контроль.
Технологии НК
Неразрушающий контроль можно определить как процесс проверки, испытания или оценки материалов, компонентов и узлов на нарушение целостности или отклонения характеристик материалов без влияния на эксплуатационные свойства компонента. Другими словами, когда проверка или испытание закончены, компонент по-прежнему можно использовать.
Методы НК могут быть связаны с использованием таких физических явлений, как электромагнитное излучение, распространение звука и внутренние свойства материалов, что позволяет испытывать сплошные образцы, например, компоненты подшипников. Существуют различные методы НК. Наиболее распространёнными из них являются:
- ультразвуковая дефектоскопия;
- электромагнитная дефектоскопия;
- магнитопорошковая дефектоскопия (вихретоковый контроль);
- рентгенографический контроль;
- капиллярная дефектоскопия;
- визуальный контроль;
- испытание методом акустической эмиссии;
- тепловая/инфракрасная дефектоскопия.
Ультразвуковая дефектоскопия и вихретоковый контроль – наиболее часто используемые из этих методов при изготовлении подшипников. Более подробное описание этих методов приводится ниже.
Ультразвуковая дефектоскопия
Ультразвуковая дефектоскопия – это группа технологий неразрушающего контроля, основанная на распространении ультразвуковых волн в испытываемом объекте или материале. В наиболее часто используемых методиках ультразвуковой дефектоскопии очень короткие ультразвуковые импульсы со средней частотой в диапазоне от 0,1 до 20 МГц передаются в материал для обнаружения внутренних дефектов или определения характеристик материала.
На практике ультразвуковая энергия передаётся в испытываемый компонент при непосредственном контакте с излучателем, подключённым к диагностическому прибору. Основным элементом излучателя является пьезокристалл, преобразующий электрическую энергию в механическую в форме звуковых импульсов, которые передаются в материал [1].
Эти импульсы отражаются нарушениями целостности материала, например, посторонними включениями или порами, образовавшимися при выплавке стали (рис. 1).
На рис. 2 показаны основные компоненты излучателя, а также результирующее звуковое поле в виде волн звукового давления, распространяющихся в воде.
Вихретоковый контроль
Вихретоковый контроль — один из многих методов электромагнитной дефектоскопии, применяемых для НК. В нём используется электромагнитная индукция для обнаружения и определения характеристик поверхностных и подповерхностных дефектов в проводящих материалах, например, стали или алюминии.
Принцип действия вихретокового контроля [2] показан на рис. 3. Вихревые токи формируются в процессе, который называется электромагнитной индукцией. Когда по проводнику, например, медному проводу, проходит переменный ток, вокруг проводника возникает магнитное поле (a). Это магнитное поле расширяется при возрастании переменного тока до максимума и исчезает при снижении тока до нуля. Если в непосредственной близости от переменного магнитного поля появляется другой электрический проводник, в нём наводится электрический ток. Вихревые токи представляют собой электрические токи, протекающие по кольцевому пути (b).
Колебания проводимости, магнитной проницаемости испытуемого объекта и наличие дефектов в нём вызывают изменения вихревых токов и соответствующие изменения амплитуды и фазы, которые можно обнаружить прибором, подключённым к датчику (c).
На различных стадиях производственных процессов SKF технология вихретокового контроля применяется к заготовкам и готовым деталям подшипников для определения свойств материалов и для обнаружения подповерхностных дефектов, например, трещин и термических повреждений, возникших во время механической обработки твёрдых материалов.
НК в производственных процессах SKF
Меры, принимаемые SKF для обеспечения качества, начинаются с сырья. SKF работает совместно со своими поставщиками, чтобы гарантировать, что все приобретаемые материалы соответствуют требованиям SKF. Автоматизированный поточный неразрушающий контроль в процессе производства является важной частью этих требований.
Основная часть процедур неразрушающего контроля в SKF выполняется в ходе процесса производства. SKF соблюдает все промышленные нормативы тех отраслей, где используются подшипники SKF, например, железнодорожной и аэрокосмической промышленности. На рис. 4 показан прибор, осуществляющий 100 % поточный контроль вагонных колёс и буксовых подшипников.
Поскольку потребителям требуется высокая надёжность, неразрушающий контроль всё чаще используется и в других отраслях промышленности, например, в автомобилестроении и в сфере возобновляемых источников энергии.
SKF также имеет собственные критерии для подшипников ветряных турбин.
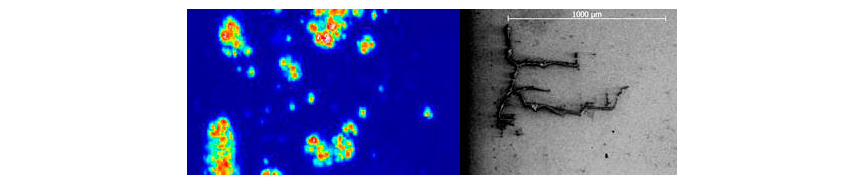
Восстановление и подробное исследование причин возвратов продукции
Для инспекции подшипников, находящихся в эксплуатации или проходящих ресурсные испытания, могут применяться различные методы неразрушающего контроля. Это позволяет лучше понять основные причины отказов подшипников и механизм ухудшения их рабочих характеристик, либо, в случае инспекции перед восстановлением подшипников, проверить подповерхностные дефекты и пригодность компонентов подшипника для дальнейшего использования.
В SKF ультразвуковая дефектоскопия используется для обнаружения подповерхностных усталостных трещин в рамках исследования такого типа дефектов. На рис. 5 (слева) приведён результат ультразвукового кругового сканирования, показывающий ультразвуковую энергию, отражённую от подповерхностных трещин вблизи дорожки качения подшипника. После выделения и проверки под микроскопом ультразвуковые сигналы могут быть соотнесены с фактически обнаруженными подповерхностными дефектами, как показано на рис. 5 (справа).
Автоматический или ручной НК?
SKF стремится к высокому уровню автоматизации НК в производственных процессах. Основной целью является повышение надёжности выполнения задач проверки. В нескольких исследованиях было показано, что даже при наличии точно предписанных процедур и опытных операторов все ручные проверки имеют меньшую надёжность из-за влияния человеческого фактора [3, 4, 5].
Все методы НК являются статистическими по своей природе, и их способность обнаруживать дефекты должна описываться вероятностно. Следовательно, НК показывает не достоверность, а только вероятность. Кроме того, помимо вероятности обнаружения существующих дефектов следует учитывать вероятность ошибочного срабатывания при отсутствии дефектов (т. е. ложный брак) и вероятность того, что существующие дефекты не будут обнаружены (т. е. необнаруженный брак) [6].
Надёжность метода НК может быть выражена в виде количественного статистического показателя возможности в заданных условиях обнаружить дефекты определённого размера в данной детали. Надёжность метода НК зависит от нескольких факторов, в том числе от того, проводится ли испытание автоматически или вручную, от возможностей оборудования и от опыта оператора. Надёжность процесса НК при производстве может быть показана в виде так называемой кривой вероятности обнаружения. На рис. 6 показан принцип построения такой кривой. На графике (рис. 7) схематически изображено повышение вероятности обнаружения и надёжности технологий НК путём внедрения автоматических проверок, привлечения квалифицированного персонала, а также использования точно описанных процедур и соответствующего оборудования.
Цифровое кодирование
Цифровое кодирование – это процесс работы в цифровом виде со всей информацией, допускающей оцифровку, а также процесс преобразования информации в цифровой формат. В производственных процессах SKF цифровое кодирование является одной из составляющих перехода к новому стандарту, который называют Industry 4.0. Этот переход осуществляется также с помощью цифрового кодирования данных проверок в ходе НК, выполняемого в течение всего производственного процесса.
Обычно данные НК не сохраняются после завершения испытаний, и в результате теряется возможность отследить изменения состояния детали по прошествии времени. Даже если данные сохраняются, часто они не систематизированы, что ограничивает возможность их интеграции в целостную картину состояния детали [7] и определения целесообразных мер, которые могут быть приняты в отношении производственного процесса на основании этих данных. Цифровые взаимосвязанные данные контроля откроют новые возможности для производства подшипников, например, обеспечение быстрой обратной связи и управление производственными процессами.
Моделирование
Для ускорения разработки и сокращения объёмов физических испытаний, требующих большого количества ресурсов и времени, SKF использует аналитические средства и моделирование в процессе НК. На рис. 8 показан пример моделирования поля звукового давления в кольце подшипника.
Взаимодействие SKF с внешними партнёрами мирового класса
Для обеспечения доступа к новейшим разработкам в области НК компания SKF постоянно оценивает возможности взаимодействия с лучшими университетами, институтами и поставщиками.
Одной из инициатив SKF является спонсорская поддержка RCNDE [8] – Исследовательского центра по неразрушающему контролю. Этот консорциум является примером успешного взаимодействия промышленности и академической науки. Одним из его спонсоров также является Исследовательский совет инженерных и физических наук Великобритании (EPSRC). Члены этого консорциума – международные промышленные компании, представляющие нефтегазовую, аэрокосмическую, ядерную и обрабатывающую отрасли, а также высшие учебные заведения Великобритании, включая Имперский колледж Лондона, Манчестерский, Ноттингемский, Уорикский, Стратклайдский и Бристольский университеты. Эти университеты проводят фундаментальные исследования, направленные на решение задач общего промышленного характера, а также прикладные исследования, связанные с конкретными задачами SKF.
Недавно SKF подписала соглашение с ARTC, Центром передовых технологий восстановления в Сингапуре [9]. Этот центр поддерживает разработки SKF в области технологий изготовления и восстановления продукции между 4-м и 6-м уровнями готовности технологий, что подразумевает демонстрацию новых технологий в соответствующей им рабочей среде. Основной задачей этого центра является разработка технологий НК для проверки восстановленных компонентов и проверки в ходе их изготовления.
Кроме того, SKF является членом Jernkontoret, Шведской ассоциации производителей стали [10]. Один из исследовательских комитетов Jernkontoret занимается НК. Роль этого комитета заключается в запуске и управлении исследовательскими проектами по НК, которые финансируются шведским правительством и реализуются шведскими университетами и институтами.
Список литературы
[1] ASNT Handbook Non-destructive testing Volume 7 – Ultrasonic testing, 2007
[2] ASNT Non-destructive testing Handbook Volume 5 – Electromagnetic testing, 2004
[3] Marija Bertovic Human Factors Approach to the Acquisition and Evaluation of NDT Data, 18th World Conference on Non-destructive Testing, 16-20 April 2012, Durban, South Africa.
[4] Harris, D. H. and Chaney, F. B. Human Factors in Quality Assurance. (1969). New York, John Wiley and Sons.
[5] Drury, C. G. and Fox, J. G. Human Reliability in Quality Control. (1975). London, Taylor & Francis, Ltd.
[6] Guidelines to Minimize Manufacturing Induced Anomalies in Critical Rotating Parts, DOT/FAA/AR-06/3 — AIA Rotor Manufacturing Project (RoMan) Report October 24th, 2006.
[7] S. Holland, E. Gregory, T. Lesthaeghe Toward Automated Interpretation of Integrated Information: Managing “Big Data” for NDE, ASNT Research Symposium 24 March 2014.
[8] Research Centre in Non-Destructive Evaluation. https://www.rcnde.ac.uk/
[9] Advanced Remanufacturing & Technology Centre, Singapore. https://www.a-star.edu.sg/artc.
[10] Jernkontoret http://www.jernkontoret.se/en/research—education/.