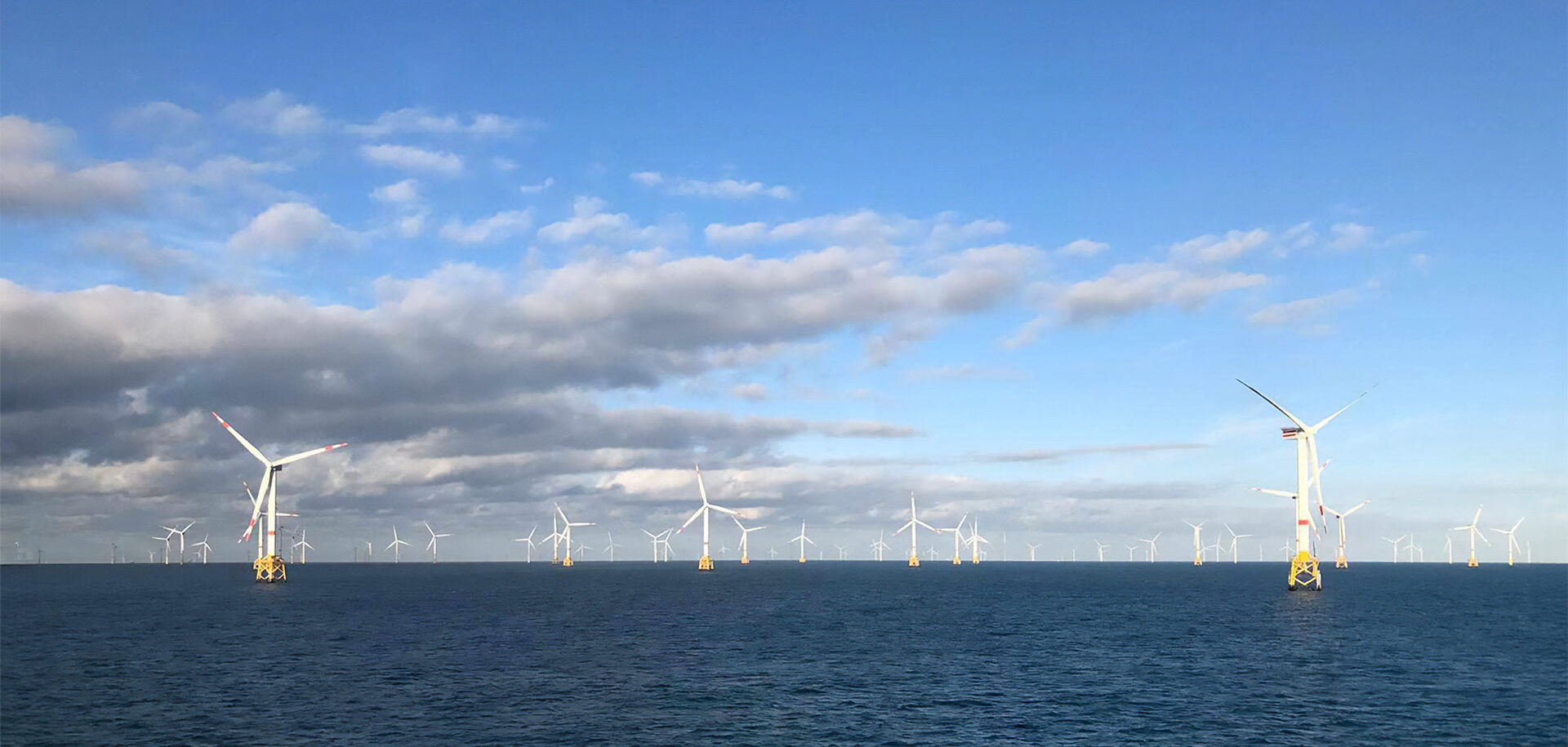
Collaboration keeps ageing wind farm in peak form
As one of Europe’s first offshore wind farms reaches middle age, innovative service and support solutions from SKF are helping to keep the turbines running.
On the Thornton sandbank, 30 kilometres off the Belgian coast, 54 wind turbines spin in the North Sea breeze. Today, the 325 MW C-Power wind farm is one of nine offshore renewable energy installations in the area, with a total capacity of 2.2 GW. An additional 3 GW is in development.
When the C-Power wind farm’s initial phase of six turbines was switched on in 2009, it was Belgium’s first commercial offshore renewable project. It was arranged in two grids, separated by a channel for power and gas pipeline. Although the 5 and 6 MW turbines on the farm are only half the size of today’s largest machines, they are still formidable pieces of engineering. Three 61.5-metre blades rotate on a hub 95 to 96 metres above the sea’s surface. The turbines owe their height to a 68-metre steel tower mounted on a 45-metre foundation. While the first turbines at the site used massive concrete foundations weighing up to 3,000 tonnes, most sit on a lighter steel lattice structure supported by four pin piles, each two metres in diameter, driven into the seabed.
At the top of each tower, a 320-tonne nacelle houses the turbine’s rotor bearings, gearbox, yaw system and power conversion equipment. C-Power describes its turbines, along with the farm’s separate offshore transformer station, as “like 55 factories that need maintenance and servicing.”
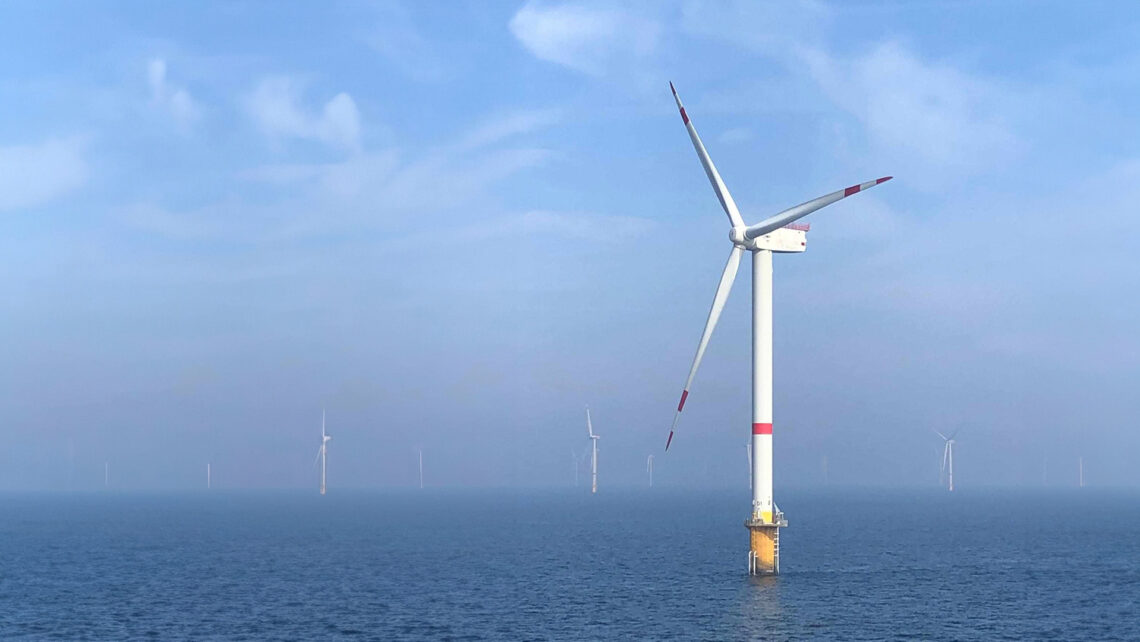
A full-time job
C-power’s oldest turbines have now been operating for 14 years in the harsh conditions of the North Sea. That’s more than halfway through the 25-year design life of the machines. Its youngest have already celebrated their 10th birthdays.
Like anyone facing the challenges of middle age, the turbines need extra care and support to keep them in tiptop condition. And unusually for an offshore wind installation, C-Power runs all its operations and maintenance activities in-house.
Almost every morning throughout the year, maintenance teams make the journey by boat from Ostend to work on the turbines. The basis of their maintenance regimen is a comprehensive programme of annual and semi-annual preventive maintenance tasks. On average, each turbine requires 11 days of preventive maintenance every year. Crews may also be called upon to trouble-shoot problems and perform repairs as necessary.
The service vessels head home again each evening, but C-Power keeps a close eye on assets via a 24/7 remote monitoring station in Ostend harbour. If the weather is too rough to access the turbines by sea, each is equipped with a helicopter winch platform to enable access for urgent repairs.
C-Power might manage maintenance itself, but it doesn’t do it alone. The company has a multi-year partnership with SKF, and the two organizations work closely together to improve turbine reliability and develop innovative solutions for the offshore energy sector. Teams from both companies take part in a weekly “pulse” meeting to discuss the progress of ongoing projects and identify new opportunities for collaboration.
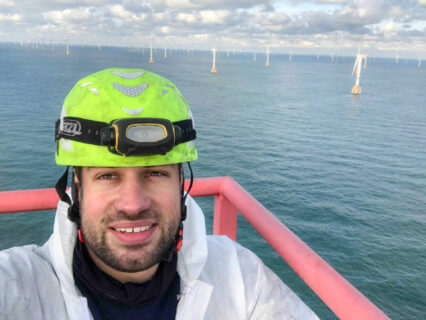
We use condition monitoring technology to understand what is going on with our turbines.
Bryan Uyttersprot, maintenance and control room engineer, C-Power
Remote control
Once every five weeks, Bryan Uyttersprot, maintenance and control room engineer for C-Power, oversees C-Power wind farm’s control room. The rest of the time he is responsible for a wide range of repair and reliability improvement projects. “Sometimes I go out on the boats and work on-site with our maintenance teams, especially when we are running a trial on something new,” he says. “But most of my work is office-based, working on longer-term projects.”
Those control shifts are a perfect example of the deep relationship between SKF and the C-Power. “We use condition monitoring technology to understand what is going on with our turbines,” Uyttersprot continues. “Their generator bearings and gearboxes have around 14 vibration sensors installed in them, and there are additional sensors in the rotor shaft main bearings.”
Data is collected from those sensors using SKF Multilog IMX machine monitoring devices, and transmitted over a secure data link to SKF’s Remote Diagnostics Services Centre (RDC) in Hamburg, Germany. At the RDC, SKF wind energy condition monitoring specialists analyse the vibration spectra, looking for early indications of problems in critical components.
“I work closely with the engineers in the RDC,” says Uyttersprot. “Their analysis can tell us if we have an issue, such as a broken bearing ring or damage to the rolling elements.” Based on SKF’s reports, Uyttersprot will decide on the best course of action to get the turbine back up and running.
“If we have a problem with a bearing in the generator or gearbox, replacing it is quite straightforward,” he says, “although we need to send a specialist team to complete the job.” The nacelles of the wind turbines each house a hydraulic crane, which the teams can use to move the heavy components safely.
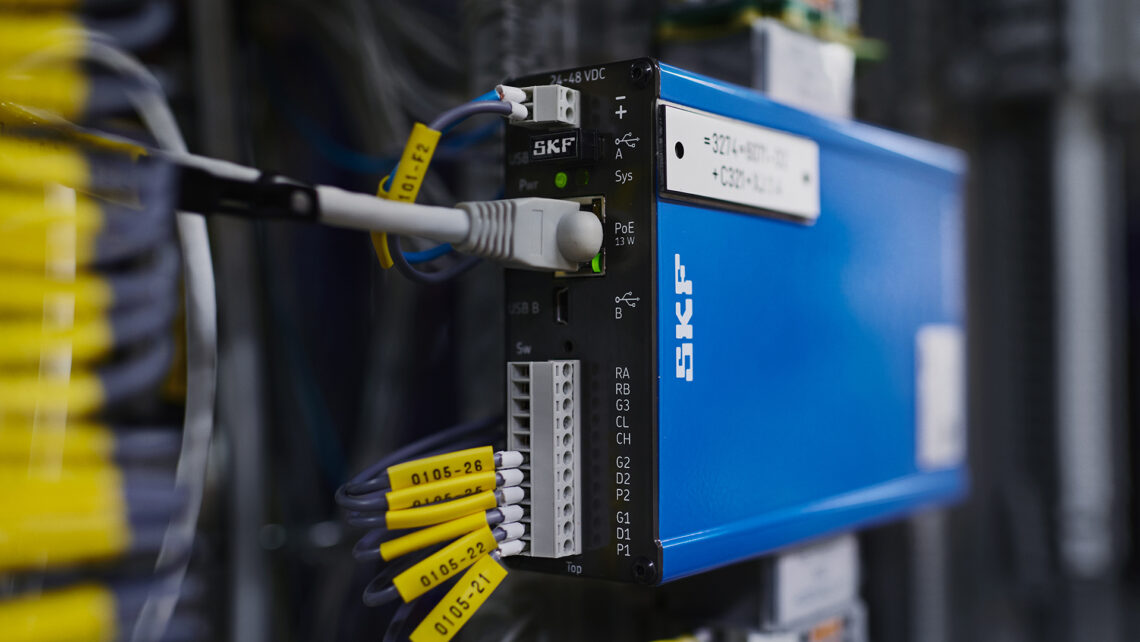
Heavy duty
If a problem occurs with the main rotor bearings, repairs are much more complex. “To do that job, we need to remove the complete mainshaft component, which weighs around 70 tonnes,” says Uyttersprot. “And to access that assembly, we need to remove the rotors and hub, which weigh 130 tonnes.” Those tasks require highly specialized heavy-lifting equipment. The work is done using a jack-up vessel equipped with a heavy crane and legs that can be lowered onto the seabed to provide support. Worn or damaged rotor shaft assemblies are transferred to an SKF facility for repair and overhaul.
The high cost and complexity of such main shaft bearing repairs make reliability of these components a key concern for all wind farm operators. That topic has been a long-term area of focus for both SKF and C-Power. “We have made a lot of changes over the years,” says Uyttersprot. “We’ve changed the grease we use in these bearings to improve lubrication performance, and over time we’ve changed over to new bearing features to improve service life.”
On a handful of turbines, SKF and C-power are midway through a multi-year trial of an innovative condition monitoring technology. “We’ve equipped some of our turbines with main bearings that contain sensors within the rolling elements,” explains Uyttersprot. “That allows us to measure the loads within the bearings and to see how those loads vary in different operating conditions and at different positions around its circumference.” Data collection from the sensor-equipped bearings is still ongoing, but Uyttersprot says he hopes that insights from the trial will eventually unlock further improvements in the reliability of these critical components.
In the meantime, other SKF innovations are already making life simpler for C-Power’s maintenance teams. One example is a novel split seal design for main rotor bearings. Originally developed for the Belgian renewable energy pioneer, the new design is not only a more robust solution but also it results in decreased assembly time.
Powerful production
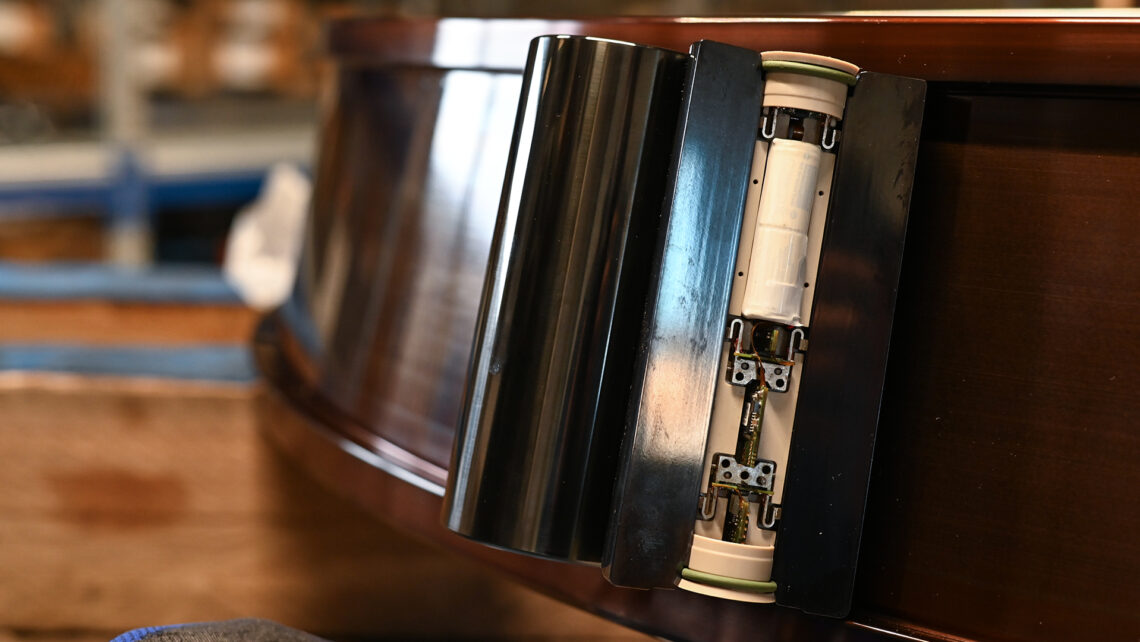