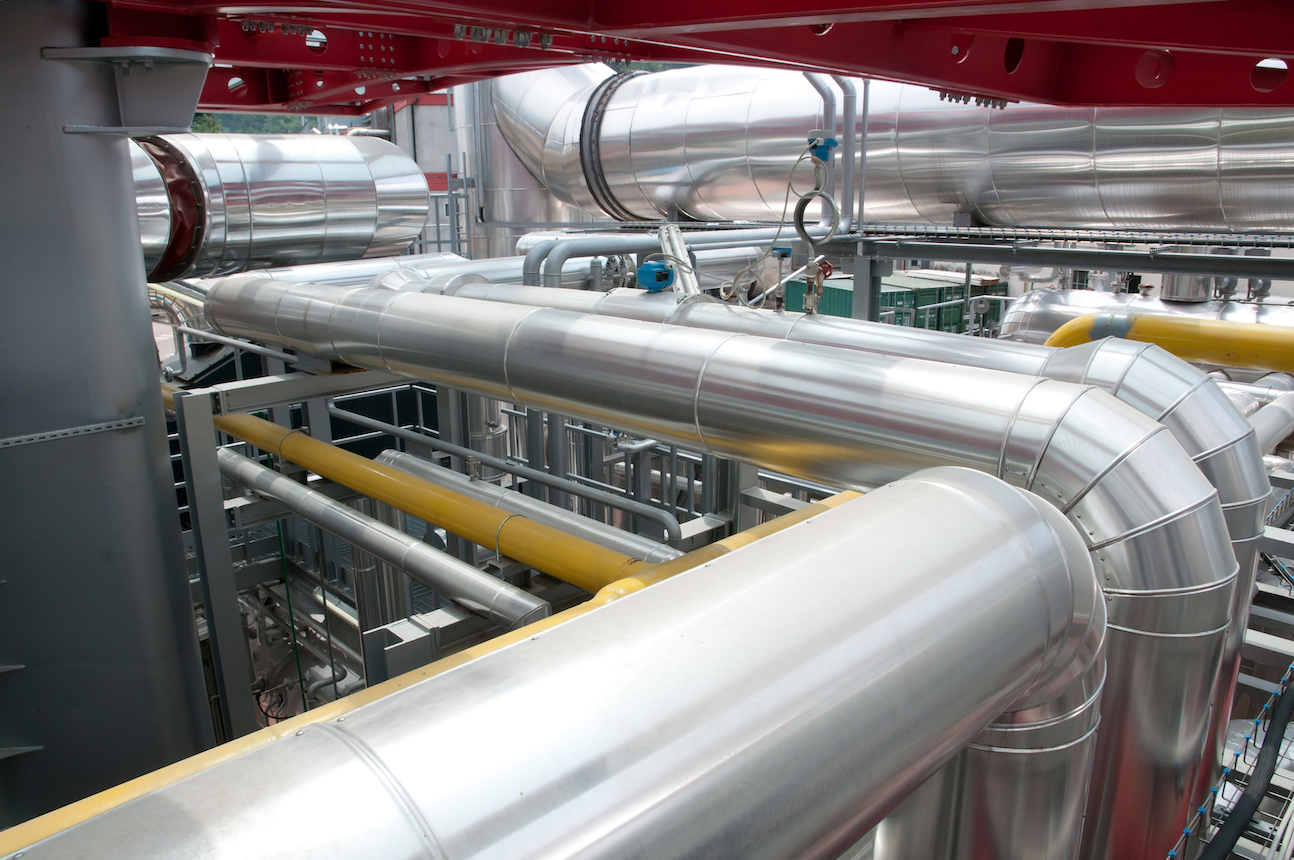
Cool running
Transporting iron ore by rail is a critical aspect of mining in the Arctic Circle. And predictive maintenance is a critical aspect of keeping the Iron Ore Line running smoothly and reliably in the region’s extreme climatic conditions.
During the winter months, temperatures can drop as low as –40 degrees Celsius in Kiruna, situated north of the Arctic Circle in Swedish Lapland. The town is home to the world’s largest underground iron ore mine, operated by LKAB, a world-leading producer of processed iron ore products. Despite these extreme weather conditions, millions of tonnes of iron ore are transported every year along the 500-kilometre-long Iron Ore Line. The world’s strongest locomotives haul ore from Kiruna to harbour storage depots in Luleå to the south and to Narvik, Norway, in the north-west. This railroad is the backbone of the northern mining industry and has been since its beginning more than a century ago. Iron ore was discovered in the region in the 1600s, but because of the remote location and harsh climate, no mining was initiated until the 1800s. At that time, small amounts of ore were extracted during the summer months and then transported in the winter using horse- and reindeer-drawn sleds. “The idea at first was to use balloons to transport the iron ore, but that didn’t work,” says Thomas Nordmark, manager R&D Railroad, LKAB. “Later, the Sami people got involved with their reindeers and the sleds, but it wasn’t until the railway came along that the iron ore operation really took off here.” That was in 1888, a decade after a process was developed to separate phosphorus from the ore. An English company built the first section of the ore railway between Malmberget in Gällivare municipality and the newly built ore harbour in Luleå. The railway was eventually sold to the Swedish state. In 1890 the government founded LKAB (Luossavaara-Kiirunavaara Aktiebolag), and plans to expand the railway were set in motion. At the turn of the century the Iron Ore Line was linked to Narvik, making it the world’s northernmost railroad. LKAB’s entire mining operation was linked via railways to its global markets. Efficient transport from the mines to its steel industry customers across Europe was, and still is, crucial to LKAB’s success. The mining company is responsible for 90 percent of the iron ore production within the European Union. Today, IORE locomotives builT by Bombardier Transportation and hauling 68 ore wagons, each with a load capacity of 100 tonnes, leave the Kiruna mine every other hour headed for the storage depots at Narvik or Luleå. “Without the railway logistics system we could never deliver the volumes of iron ore that we produce at LKAB,” says David Lövgren, senior manager Maintenance Technology, LKAB. “Annually, we produce and transport 27 million tonnes of iron ore at LKAB.” LKAB has a target to increase that annual transport to 37 million tonnes by 2015, a target that puts big demands on suppliers’ products and solutions to withstand the extra loads and the wear and tear. Two main issues for the railway are the wheelset bearings, which must handle very heavy axle loads, and the lubricant and sealing that must stand up to the cold temperatures. SKF worked together with LKAB to develop a new type of sealing solution specially designed to withstand the harsh climate. As for wheelset bearings, SKF bearings have been helping LKAB’s wagons roll since 1913. The first trials with SKF self-aligning ball bearings were made at the Malmberget mine. Today’s freight wagon wheelsets feature compact tapered roller bearing units. After about 800,000 kilometres of use, the bearing units are removed and sent to the SKF refurbishment centre in Gothenburg. The bearing units are dismantled, cleaned, analyzed, filled with new grease and fitted with a new sealing solution before being put back to service. The new seal, used in the tapered roller bearing units, operates with lower friction than previous designs and contributes to LKAB’s full train energy reduction target. LKAB aims to reduce its overall energy consumption in its operations by 2 percent. “We consider ourselves very energy efficient,” Nordmark says. “We have quite new locomotives that are regenerating energy back to the network when the brakes are applied to the train. With an 8,500-tonne train, you’re feeding a lot of power back into the engine, so in total we save about 25 percent of the energy used for one trip between Kiruna and Narvik.” On a single track, the trains must run reliably and without any breakdown. In addition to having equipment that is efficient and durable, it is essential to be one step ahead – to locate problems and stop the train before failure occurs. LKAB uses a predictive maintenance plan to do just that. “Within LKAB Malmtrafik, we use a predictive maintenance programme that helps plan the appropriate maintenance for our locomotives and wagons, depending on how long they’ve travelled,” Lövgren explains. “Condition monitoring with tools such as vibration analysis is used to ensure that our equipment has a high level of availability and reliability.” The remote condition monitoring of locomotives is still in the early stages, but it is on track to becoming the future of train maintenance. SKF works closely with LKAB on condition monitoring of assets, using a variety of technologies including SKF Insight, an innovation in intelligent wireless technologies that is integrated into SKF bearings (see image on page 2). LKAB has invested more than 5 billion Swedish kronor (570 million euros) over the past decade in new locomotives, wagons and expansion of rail terminals. Today, the priority is to use new technology and solutions to keep the Iron Ore Line operating reliably into the future. SKF Insight is a trademark of the SKF Group
SKF’s contribution to the Iron Ore Line
Locomotives:
Freight wagons:
Services: