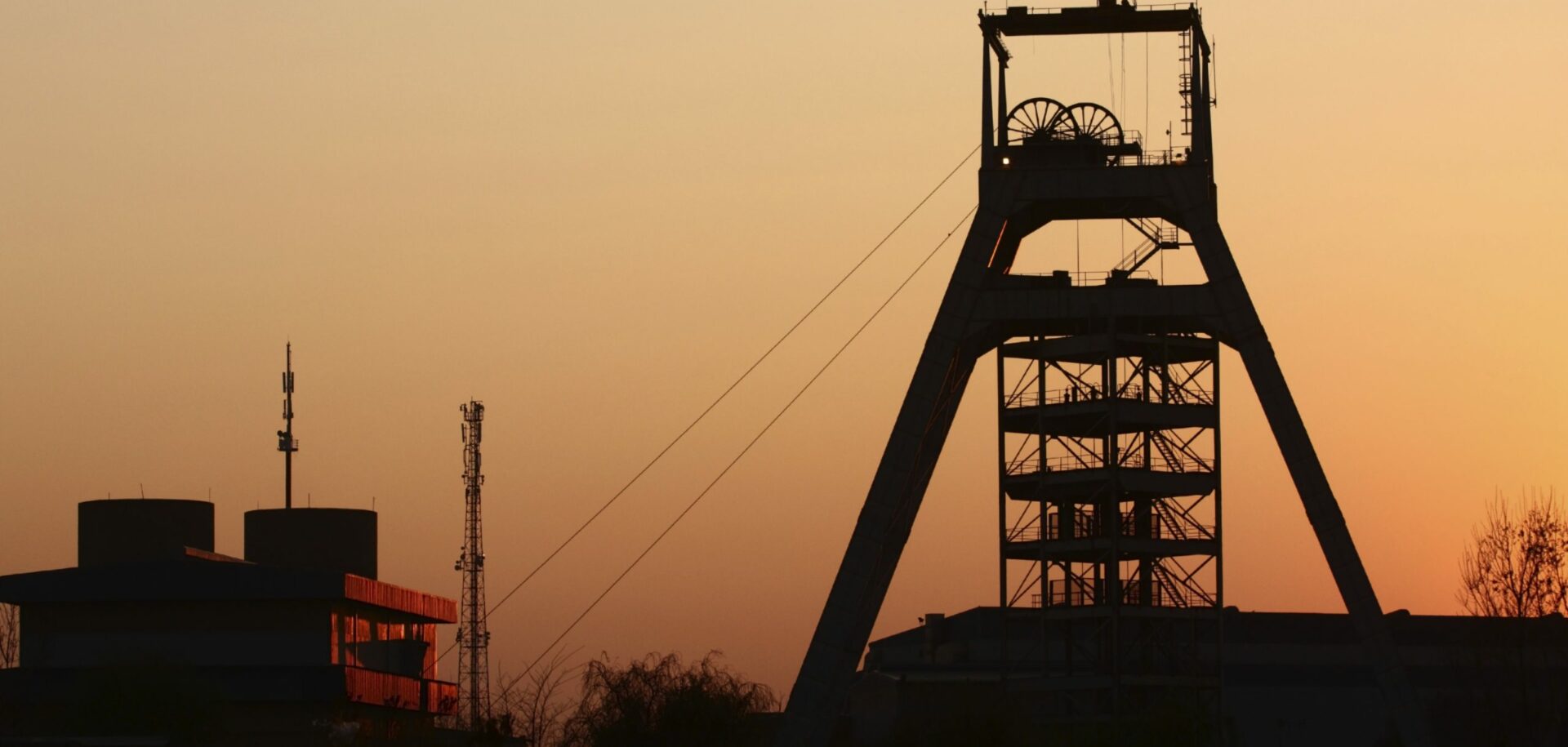
Digging deep
When it comes to moving ore up and men and material up and down a mineshaft, three factors are crucial: reliability, safety and speed. At Czech company INCO Engineering’s high-tech development centre these factors hold sway.
Mining is a 24/7 business,” says Antonín Jaroš, CEO and co-owner of INCO Engineering, a Prague-based mining transport technology company.
At the moment he is overseeing the final testing of INCO’s most recent equipment, two enormous shaft hoists destined for India’s largest gold mine, and he’s talking over the din.
“Delays must be reduced to a minimum,” he shouts, as the hoists’ electric motors reach full throttle. “Without any accidents!”
The two mammoth machines – a four-rope 1.3-megawatt AC motor friction hoist for transporting ore and equipment and a 5.8-metre-diameter, 2.4-megawatt DC motor double-drum hoist to transport workers to and from the workface – operate on contrasting mechanical principles.
Friction hoists are either surface-mounted or mounted right above the mine shaft. The lifting medium passes over a pulley, with the load connected to one end of the lifting medium. The friction between the pulley and the lifting medium aids in the raising.
With drum-type hoisting devices, the lifting medium is continuously wrapped around a drum mounted to the side of the shaft in one or several layers. A headframe and sheaves centre the hoisting medium in the shaft compartment.
The contract for the hoists, which will serve one of India’s deepest mine shafts (at the Hutti Gold Mine in south-west India’s Karnataka state), comprises “equipment design, production, delivery, on-site assembly and start-up,” explains Tomáš Nebáznivý, INCO’s director of sales for Asia.
That is par for the course for Jaroš and his team. They pride themselves on offering clients a one-stop shop: INCO is the single point of contact, with sole responsibility for execution.
“We are just as much a project manager as a producer,” Jaroš explains. Indeed, INCO outsources some 35 percent of any job to companies such as SKF, a partner for the past 20 years. SKF supplied not only spherical roller bearings with sleeves and housings for the equipment but also lubrication systems for the bearings.
“We also provided supervision during assembly, because the correct mounting of large-size bearings on tapered sleeves is crucial for bearing life,” adds Michal Stuchlík, heavy machinery segment manager for SKF. “It was a specialized job – the kind of thing that Mr Jaroš often trusts us with.”
A big, bearded bear of a man, Jaroš – now age 74 – has spent a working lifetime preparing for his role as mining’s “Mr Fixit”.
Most of his career he spent steadily rising through the ranks at ČKD, a giant Czech engineering conglomerate. In his spare time, as a young man, he moonlighted as an enforcer for a well-known ice hockey club.
Since founding INCO in 1994 as the successor to ČKD’s mining equipment arm, he has had to apply his hustling rink style to the task of drumming up new business.
Historically, Jaroš explains, most of ČKD’s wares were earmarked for the former Soviet Union; even today, some 90 percent of INCO’s production ends up in Russia. But expansion into new markets has lowered his company’s exposure to the vagaries of the Russian economy.
Today, INCO products can be found in Ukraine and Poland, and also as far afield as China and Vietnam (where INCO won a long-term contract to be the exclusive supplier of technical equipment for all the country’s underground coal mines).
Apart from hoisting machinery, INCO provides other specialist equipment for underground mines, such as loading stations, wagon pushers, shaft ventilators, mine-signalling systems, skips and cages. The company also boasts a healthy sideline in modernizing outdated equipment.
But it is INCO’s high-tech development centre that has enabled it to match the mining sector’s demands for ever-higher capacity and faster winding rates.
For example, INCO is at the project preparation stage for one of the largest hoists ever produced – an eight-rope friction hoist of 12 megawatts.
Also in the pipeline is an air-cooled inverter for synchronous motors that has almost no need for maintenance.
One popular add-on is a hoist management system. The system’s easy-to-use graphic interface enables remote access over the Internet to facilitate monitoring and diagnostics and identify problems – often before they arise.
It is all a long way from the early times of the rust-and-dust “workers’ paradise” where the young Jaroš cut his professional teeth. “People still see mining as a dirty, old-fashioned affair, but it’s quite the opposite,” he says. “Modern mining is clean and high-tech.”
Those who don’t understand that, he says, should dig elsewhere for their money.