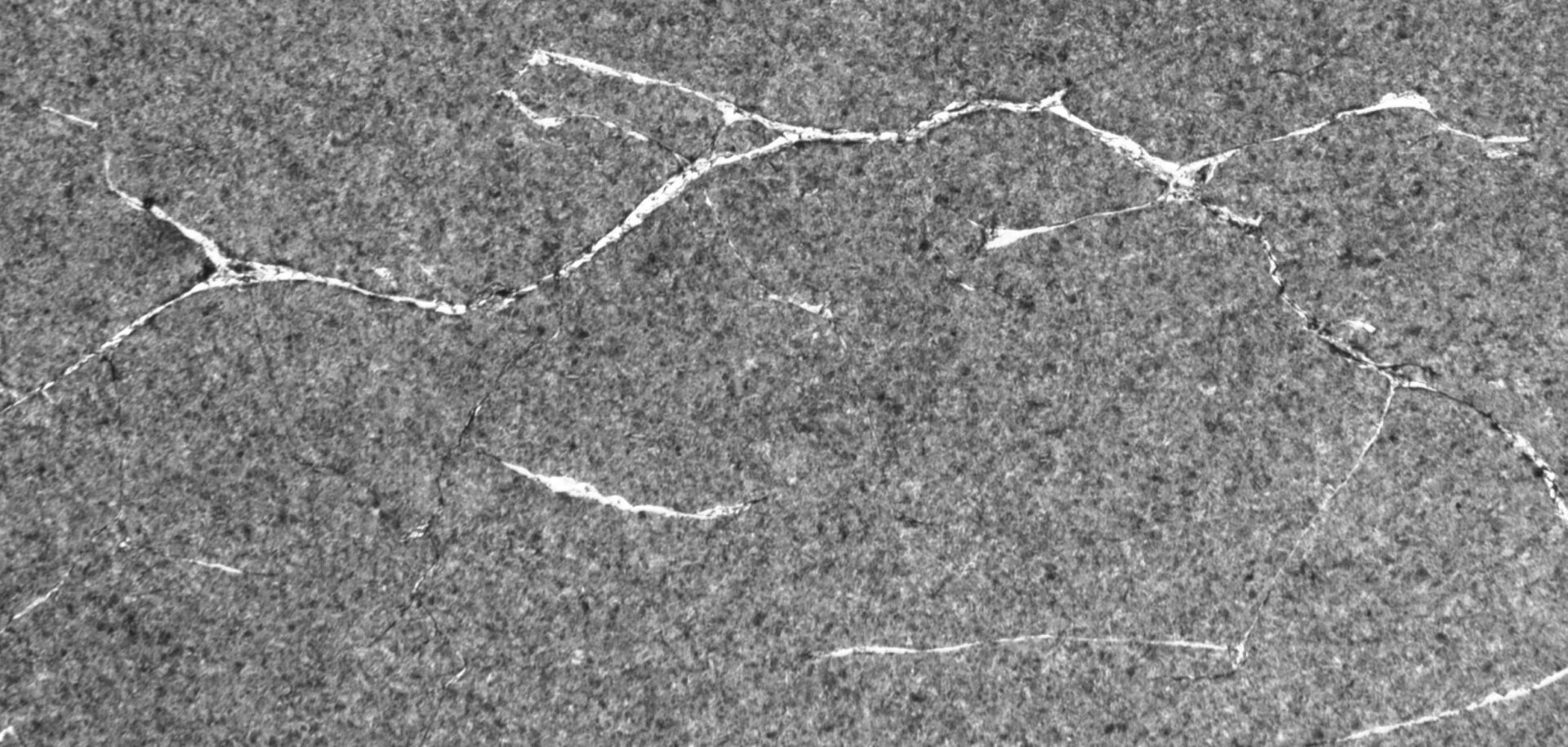
Grietas de corrosión blanca por ataque ácido
Los rodamientos son componentes fundamentales de máquinas para soportar cargas y transmitir el movimiento. El constante incremento de la densidad de potencia del equipo de producción moderno exige una mayor confiabilidad y una capacidad de soportar cargas más elevada.
Hoy, las fallas de rodamientos debido a fatiga por contacto rodante son, en general, poco frecuentes, y generalmente la vida útil final que alcanzan supera con creces la vida nominal calculada. No obstante, en aplicaciones específicas, hay casos donde, a veces, los rodamientos fallan prematuramente entre el 5 y el 10% de su vida nominal calculada.
Las fallas de rodamientos prematuras se producen, por lo general, una tras otra en intervalos muy breves; es decir, la distribución de Weibull muestra una gran inclinación en comparación con la fatiga normal por contacto rodante (fig. 2).
Un rasgo característico de muchas fallas prematuras son las amplias redes de grietas debajo de la superficie con aspecto de “corrosión blanca por ataque ácido”, o WEC (white etching cracks) (fig. 1). Esas grietas generalmente se propagan hasta la superficie, y causan el desconchado del camino de rodadura, que comúnmente se ha observado en devoluciones de campo de aplicaciones como cajas de engranajes de turbinas eólicas [1], trenes de potencia automotrices, alternadores y equipo auxiliar periférico [2][3], papeleras y sistemas de propulsión marina [4]. En la fig. 3, se muestran algunos ejemplos típicos. La causa raíz de esta falla se ha analizado ampliamente durante unos 15 años, y se han presentado diversas hipótesis basadas en exámenes desde diferentes perspectivas. En [5][6] pueden encontrarse análisis y revisiones integrales de las diversas hipótesis. El hecho de que la falla prematura del rodamiento se haya abordado desde diferentes perspectivas durante las últimas décadas ha conducido a una mayor comprensión de aspectos específicos del problema. Sin embargo, entre los principales miembros de los grupos que analizan las fallas en los rodamientos todavía no hay consenso sobre su causa raíz y mecanismos de falla.
Durante los últimos cuatro años, SKF ha intensificado los estudios, análisis e investigaciones de los fenómenos de la corrosión blanca por ataque ácido, a fin de esclarecer su papel en relación con la fatiga por contacto rodante de los rodamientos, así como la fatiga acelerada (desconchado prematuro de los rodamientos). Mientras este tema se debate todavía en la comunidad científica de materiales, los hallazgos de SKF respaldan fuertemente que la corrosión blanca por ataque ácido se produce al final de la cadena de fallas, y es una consecuencia natural de las redes de grietas en rodamientos que fallan prematuramente. La corrosión blanca por ataque ácido se considera más bien un síntoma que la causa raíz de las fallas por fatiga. En el presente artículo, se expone una visión de consenso que es mayoritaria entre los expertos de SKF sobre las fallas prematuras y la corrosión blanca por ataque ácido (WEC). También se propone una definición de este tipo de corrosión, se debaten sus orígenes y se presenta un esquema de todas las causas de falla que conducen a la corrosión blanca por ataque ácido.
Grietas de corrosión blanca por ataque ácido (WEC)
Estas grietas aparecen dentro de la microestructura del acero de rodamientos. Están decoradas por zonas blancas de corrosión ácida (white etching areas, WEA). La corrosión blanca por ataque ácido se refiere al aspecto de la microestructura modificada de una probeta de acero pulida y mordentada. Las zonas afectadas constan de ferrita ultrafina, nanocristalina, exenta de carburos, o ferrita con una distribución muy fina de partículas de carburos. Las zonas blancas de corrosión ácida o WEA se forman por la amorfización debida a la fricción de las caras de la grieta durante la rodadura. Estas zonas son blancas observadas por un microscopio óptico, debido a su baja respuesta al agente mordiente. Las zonas de corrosión blanca por ataque ácido alrededor de las grietas son de un 10 a un 50% más duras que la microestructura circundante no afectada.
Causas de la formación de grietas de corrosión blanca por ataque ácido
Corrosión blanca por ataque ácido producida por fatiga por contacto rodante
Es sabido que los rodamientos pequeños de funcionamiento prolongado sometidos a grandes cargas pueden pasar por diversas etapas de fatiga hasta llegar a fallar (ciclo de fatiga muy elevado) [7]. La primera etapa es el período de rodaje, que conduce a la deformación microplástica, al endurecimiento por deformación y, gradualmente, a la formación de tensiones residuales. Durante la etapa de rodaje, la superficie del rodamiento también puede sufrir una cierta deformación microplástica durante la cual se alisan las asperezas. Después del rodaje, se inicia la mayor parte de la vida útil del rodamiento, que se caracteriza por cambios graduales en su microestructura [8]. Durante esta etapa, la distribución del carburo cambia debido a deformación microplástica [9] [10]. Asimismo, la retención de austenita puede disminuir, y todos los cambios en la microestructura van acompañados de una formación de tensiones residuales. En un estado avanzado de fatiga por contacto rodante en el rodamiento, pueden observarse regiones oscuras afectadas por el ataque ácido (dark etching regions, DER) así como bandas de ángulos pequeños (low angle bands, LAB) y grandes (high angle bands, HAB) (fig. 4, izquierda). Aun cuando las HAB y LAB son también de corrosión blanca por ataque ácido, tienen un aspecto diferente en comparación con formaciones WEC irregulares observadas en fallas prematuras de rodamientos. Esto apunta hacia la conclusión de que la formación de corrosión blanca irregular no constituye una parte de la fatiga por contacto rodante (rolling contact fatigue, RCF). Sin embargo, la microestructura de esas zonas de corrosión blanca no es muy diferente en estructura cristalina de las zonas de corrosión blanca que se observan en fallas prematuras.
En rodamientos de tamaño medio a grande, los efectos antes mencionados no se producen necesariamente de la misma manera en rodamientos pequeños, sometidos a grandes cargas. Al igual que otros componentes mecánicos, esos rodamientos fallan en general debido a la fractura del eslabón más débil (p. ej., desviaciones preexistentes en la estructura del material como inclusiones y porosidades). Tal como se explica en ISO/TR 1281-2:2008, el límite de fatiga disminuye con un tamaño de rodamiento superior a un diámetro medio de 100 mm. Además, al comparar los efectos de la presión de contacto entre rodamientos pequeños y grandes, el volumen de tensiones afectado aumenta en los rodamientos grandes, al igual que las influencias negativas de eslabones débiles. Un ejemplo son las inclusiones, que constituyen una parte natural de todos los aceros de rodamientos [11]. Un factor adicional que juega un papel es la presión de contacto propiamente dicha; en el ejemplo presentado en la fig. 4, donde se generan bandas de ángulos pequeños y grandes, la presión de contacto es relativamente alta (> 3,2 GPa). En muchos rodamientos de tamaño medio a grande, las presiones de contacto aplicadas son muy inferiores a 3 GPa, lo cual significa que la carga de fatiga queda dentro de otro régimen, lo que conduce a menos daños globales y más daños localizados alrededor de inclusiones no metálicas.
Ya se dieron a conocer casos de corrosión blanca y oscura por ataque ácido en rodamientos con fatiga por contacto rodante en la década del sesenta [12], y en SKF en la década del ochenta [13]. Investigaciones posteriores de rodamientos de tamaño medio a grande que fallaron prematuramente (de ensayos de vida útil altamente acelerados o de ensayos de resistencia estándar) han confirmado que la aparición de redes amplias e irregulares de corrosión blanca es un subproducto natural en rodamientos con fatiga por contacto rodante (fig. 4, derecha).
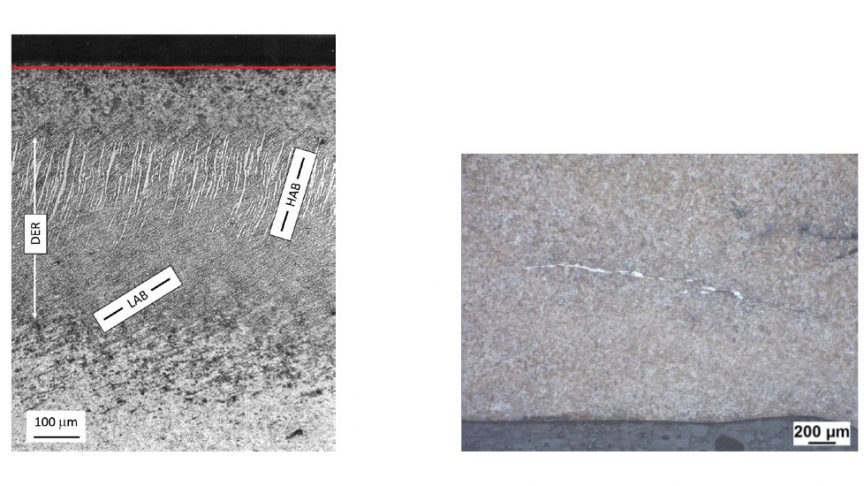
Grietas de corrosión blanca en fatiga acelerada (desconchado prematuro)
La diferencia entre el desconchado prematuro (en la industria, frecuentemente interpretado como fallas de corrosión blanca por ataque ácido o WEC) y la fatiga normal por contacto rodante en el rodamiento puede encontrarse en el tiempo que se precisa para que los diferentes acontecimientos se produzcan antes de iniciarse el desconchado (fig. 5). Asimismo, en comparación con los ensayos de resistencia o la fatiga normal por contacto rodante, las fallas prematuras suelen asociarse a iniciaciones de grietas en varios puntos/zonas tal como revelan los análisis de fallas en los rodamientos.
Los motivos de la iniciación de grietas en el acero de rodamientos pueden ser diferentes, y las grietas pueden acelerar en casos de tensiones elevadas o reducción de resistencia debido a efectos medioambientales (fig. 6).
Las tensiones que afectan a los rodamientos pueden ser más altas de lo esperado. Ejemplos de estas situaciones:
- Las cargas cortas y pesadas pueden causarlas efectos dinámicos inesperados o efectos de la temperatura, y generar una intensa precarga de deformaciones estructurales, carga de bordes, etc.
- Tensión estructural en el material del rodamiento (p. ej., causada por desviaciones de forma, desalineación u otros factores) que incrementará la tensión en el material [14].
- Un incremento de la tensión en los caminos de rodadura también puede causarlo unas condiciones severas de contacto tribológico (p. ej., deslizamiento y/o espesor de película deficientes) en combinación con determinados lubricantes [15].
La resistencia del material de un rodamiento puede sufrir la influencia negativa de factores medioambientales que se sospeche que generen hidrógeno [16]. Entre ellos podrían citarse:
- contaminación de agua
- corrosión [17] y
- corrientes eléctricas parásitas
En esos casos, unas condiciones de carga moderadas pueden conducir a una falla prematura.
Los impulsores identificados que favorecen una fatiga acelerada, tanto los relacionados con mayores tensiones como con menor resistencia del material, se han verificado en SKF en ensayos especiales con rodamientos.
Una vez que se han generado los núcleos de grieta (a veces asociados con la aparición de regiones oscuras afectadas por el ataque ácido [DER]), un proceso de frotación en las caras de la grieta [18]–[22] conduce a la transferencia de material de un lado de la grieta al otro. Esto da como resultado una grieta serpenteante, que acumula una microestructura de corrosión blanca en el lado receptor de la grieta.
El desarrollo de la zona de corrosión blanca también depende de la orientación de la grieta debajo de la superficie, que puede relacionarse con la actuación de fuerzas internas y modos de deformación. Es por ello que las zonas de corrosión blanca (WEA) se encuentran con mayor frecuencia en grietas de orientación horizontal (paralelas al camino de rodadura), mientras que las partes de la grieta orientadas verticalmente suelen mostrar menos indicaciones de WEA (fig. 7). Además, la generación de WEA depende del espacio intermedio entre las caras de la grieta y el número de ciclos de tensión, así como del estado de tensiones internas en el material.
Ejemplos de generación de WEC debido a tensiones muy altas
Las figs. 8, 9 y 10 muestran dos ejemplos de iniciación de corrosión blanca por ataque ácido relacionada con tensiones. Los resultados presentados en las figs. 8 y 9 proceden de un banco de pruebas de rodamientos diseñado para introducir artificialmente tensiones o deformaciones estructurales en el asiento del rodamiento a través de ondulación. Esto da como resultado tensiones por tracción locales en el aro interior del rodamiento. En el ensayo, interviene un rodamiento de rodillos cilíndricos con su aro interior (diámetro de agujero de 220 mm) montado con apriete normal en un manguito con ondulación en cinco lóbulos, fijo a un eje con interferencia. Un manguito de este tipo con ondulación, fabricado mediante torneado duro, inducirá cinco zonas de tensiones por tracción de alrededor de 205 MPa cerca de la superficie del camino de rodadura del aro interior. El rodamiento del ensayo es un ejemplar de dos hileras de rodillos cilíndricos modificado, provisto de una hilera de ocho rodillos –en lugar de dos hileras de 24 rodillos– en la parte central del aro interior, a fin de adaptarse a la capacidad del banco de pruebas para alcanzar la tensión de contacto requerida (fig. 8). El material del rodamiento es acero SAE 52100 (100Cr6). La microestructura de los rodamientos es martensita revenida con una retención de austenita de hasta el 7% (volumen) y una dureza de 62 HRC.
Los rodamientos se sometieron a ensayo a una presión de contacto herciana máxima de 1,8 GPa y un valor kappa de aproximadamente 2. El ensayo se llevó a cabo hasta que los rodamientos fallaron.
Un rodamiento falló con una grieta axial visible en el camino de rodadura después de 1 150 horas (correspondientes a 6,35×108 ciclos de tensión) en el manguito con ondulación de cinco lóbulos. El segundo rodamiento falló con dos grietas axiales visibles después de 1 570 horas (correspondientes a 8,67×108 ciclos de tensión). La posición de las grietas axiales coincide circunferencialmente con uno de los picos de ondulación, donde existe una zona de tensión por tracción.
Hay que tener en cuenta que cuatro rodamientos iguales se habían sometido a ensayo previamente en las mismas condiciones usando un ajuste de eje estándar (sin ondulación introducida artificialmente), ninguno de los cuales falló hasta finalizar el ensayo después de alrededor de > 2 200 horas (correspondientes a 1,21×109 ciclos de tensión), y que durante análisis posteriores no se detectaron ni grietas superficiales ni debajo de la superficie de corrosión blanca por ataque ácido.
Los análisis posteriores constan de ensayos no destructivos (non-destructive tests, NDT) por prueba ultrasónica (ultrasonic test, UST) y penetración de colorante, medición de la redondez del aro, análisis fractográfico y examen metalográfico en microscopio.
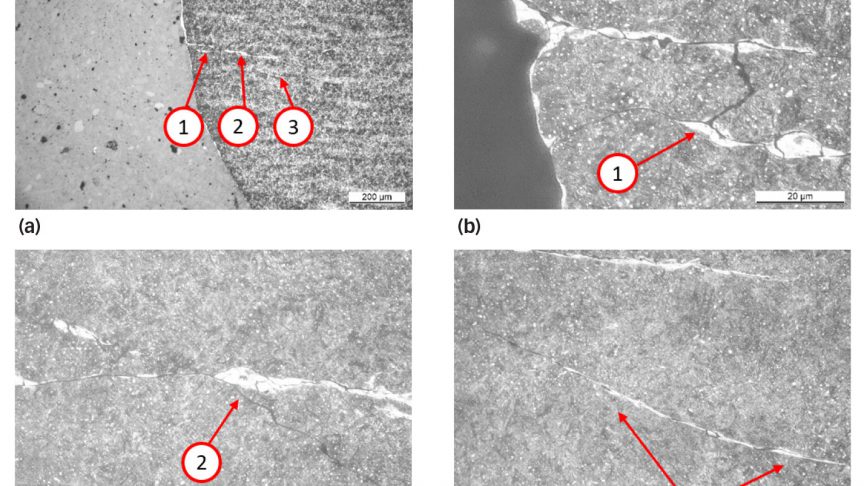
Se hizo una sección paralela en la muestra con una grieta abierta, tal como se indica en la fig. 9. Después del ataque ácido, puede observarse que la grieta principal es blanca en el microscopio óptico, y que a una profundidad de unos 500 µm debajo de la superficie, la grieta se había ramificado. Las grietas ramificadas también eran con corrosión blanca por ataque ácido que se había propagado en una dirección paralela al camino de rodadura unos 400 µm desde la grieta principal. Una ampliación de las grietas ramificadas (fig. 9b, c y d) respalda la tesis de que las grietas se interconectan entre sí, y forman redes de WEC debajo de la superficie. También se hicieron secciones paralelas en otras dos posiciones circunferenciales que corresponden a los picos del eje con manguito ondulado. Aun cuando no se observaron grietas en la superficie, se encontraron WEC múltiples debajo de la superficie de esas regiones, donde las tensiones por tracción inducidas por la ondulación estuvieron presentes durante el ensayo. Para obtener más detalles, véase [14].
Los resultados presentes en la fig. 10 proceden de un ensayo con rodamientos de rodillos a rótula 23024 expuestos a cargas pesadas a corto plazo.
Durante la carga pesada a corto plazo, el rodamiento se expone a una presión de contacto superior a 3 GPa durante unos 15 minutos en condiciones de buena lubricación (valor kappa de aproximadamente 3,5).
El rodamiento expuesto previamente a una carga pesada a corto plazo se monta luego en un banco de pruebas radial. Allí, se aplica una presión de contacto moderada, de unos 1,7 GPa y un valor kappa de aproximadamente 2. En estas condiciones, la prueba se interrumpe después de 3,3×107 ciclos, o los rodamientos han fallado antes. La fig. 10 muestra un corte circunferencial y aro exterior sometido a prueba de ácido con nital. El rodamiento falló después de 1,9×107 ciclos debido al desconchado de la zona sometida a carga del aro exterior.
Ejemplos de generación de WEC debido a menor resistencia del material
Un ejemplo de corrosión blanca por ataque ácido debajo de la superficie en un rodamiento con carga de hidrógeno ya se ha mostrado en la fig. 7. En [22] puede encontrarse un análisis posterior detallado de rodamientos de bolas de contacto angular y rodamientos rígidos de bolas con y sin carga de hidrógeno.
Ejemplos de generación de WEC bajo influencia combinada de fricción y lubricante
Se ha encontrado corrosión blanca por ataque ácido en rodamientos axiales de rodillos cilíndricos 81212 fallados al realizar ensayos de evaluación de aceite usando bancos de prueba FE8 [23]. Hasta la fecha, las condiciones del ensayo, una combinación de fricción y alto deslizamiento cinemático (no representativo de rodamientos de rodillos radiales), no indican resultados concluyentes. Por ahora, no puede presentarse una conclusión final sobre si los WEC en los ensayos de FE8 son más bien una consecuencia de fatiga iniciada en la superficie (donde el lubricante también desempeña un papel importante) o el resultado de la penetración de hidrógeno, o una combinación de ambas cosas.
Se han realizado ensayos utilizando rodamientos axiales de rodillos cilíndricos 81212 de acero contra acero. El material del rodamiento es acero de rodamientos estándar según SAE 52100, con templado martensítico, que contiene una retención de austenita < 3% y una dureza de alrededor de 60 HRC. Estos rodamientos se han sometido a ensayos con cargas moderadas (presión de contacto máx. de alrededor de 1,9 GPa) y condiciones de lubricación inadecuadas (valor kappa de aproximadamente 0,3).
Se han realizado ensayos de diferentes aceites y mezclas de aceites. En la fig. 11, se muestra el aspecto de una falla típica.
Aun cuando no se muestra con detalle aquí, en todos los ensayos realizados, los rodillos fallaron en su mayor parte y las arandelas con poca frecuencia. Los ensayos se efectuaron hasta la falla (desconchado) o se interrumpieron. En los rodamientos que fallaron por desconchado y en los que se encontró WEC, se supone que, antes de cualquier desconchado, ya podían haberse desarrollado grietas debajo de la superficie decoradas de corrosión blanca por ataque ácido. Esto es porque, a veces, también se han encontrado grietas debajo de la superficie en componentes no desconchados. Para obtener más detalles, véase [15].
Análisis
Los resultados antedichos explican por qué pueden encontrarse grietas de corrosión blanca por ataque ácido en todo tipo de industrias, todo tipo de rodamientos y todo tipo de tratamiento térmico (materiales totalmente templados y cementados) [1], debido a que las WEC se producen al final de la cadena de fallas y son una consecuencia natural de redes de grietas en rodamientos que fallan prematuramente.
La clave para identificar las causas raíz de la falla prematura de rodamientos no es solo estudiar las WEC, sino más bien averiguar los efectos de debilitamiento relevantes (relacionados con tensiones más elevadas o menor resistencia del material) que conducen a una fatiga acelerada.
En general, la falla de cualquier componente mecánico se debe a la ruptura del eslabón más débil. Esto es cuando la tensión local excede la resistencia local. La falla prematura es el resultado de un debilitamiento significativo del eslabón más débil. La confiabilidad de los rodamientos usados en diversas aplicaciones obedece al principio del eslabón más débil. Siempre hay puntos débiles dentro del material o en la superficie de contacto de trabajo. Un rodamiento falla si se rompe el eslabón más débil. Cuando las condiciones de lubricación son deficientes o la superficie es áspera (p. ej., por indentaciones de partículas), el eslabón más débil puede muy bien hallarse en la superficie y el rodamiento falla debido a daños en ella como deformación o desgaste. Con buenas condiciones de lubricación, el eslabón más débil puede encontrarse debajo de la superficie, debido a la presencia de defectos en el material, como inclusiones y alto esfuerzo cortante como resultado de contacto herciano, y la falla del rodamiento es una consecuencia de la iniciación de grietas y propagación de defectos preexistentes en el material. En los rodamientos, la resistencia del eslabón más débil puede estar relacionada con una carga o tensión límite conocida como el límite de fatiga. Un rodamiento falla si se excede el límite de fatiga. Se produce una falla prematura de los rodamientos cuando el límite de fatiga es considerablemente menor o, en otras palabras, cuando la resistencia del eslabón más débil es notablemente más baja. El debilitamiento debido a tensiones más elevadas o a menor resistencia del material causa la iniciación prematura de grietas y la propagación de grietas acelerada, lo cual conduce a una falla prematura, pero no a WEC. Cuando no hay debilitamiento, un rodamiento puede fallar como resultado de fatiga por contacto rodante normal mediante una sola escama desconchada que muestre una baja aparición de WEC o ausencia de esta, porque las grietas se propagan rápidamente cuando el material llega al final de su vida útil [7]. En otras palabras, no queda tiempo para la transformación de material dentro del sistema de grietas. Con mayores niveles de debilitamiento, el rodamiento puede fallar prematuramente en forma de extensas WEC, debido a que el material en sistemas de grieta iniciados tiene tiempo de transformarse localmente de DEA a WEA. Con mayores niveles de severidad, pueden producirse grietas axiales con decoración de WEA menos extendida o incluso fractura sin decoración de WEA, debido a que las grietas se propagan demasiado rápidamente [14].
Recomendaciones
Cada falla prematura de un rodamiento es un caso único. Si se observa nuevamente la fig. 6, puede verse que las razones de desconchado prematuro pueden ser muy diferentes. No existe una sola causa raíz; cada caso de falla debe revisarse a la luz de las correspondientes condiciones de funcionamiento.
En función de la categorización de los impulsores del debilitamiento en “mayores tensiones” y “menor resistencia de material”, pueden darse recomendaciones muy generales, tal como se muestra en la tabla 1. La tabla distingue entre recomendaciones para la aplicación propiamente dicha (el sistema de rodamientos, el proceso de diseño) y posibilidades de incrementar la robustez del rodamiento. La mejor opción para prevenir que sucedan fallas prematuras depende de las circunstancias específicas de la aplicación. Para obtener más asesoramiento, comuníquese con el servicio de ingeniería de aplicaciones de SKF.
Referencias
[1] K. Stadler, A. Stubenrauch, Averías prematuras en los rodamientos de las multiplicadoras eólicas y grietas WEC, SKF Evolution #2, 2013, http://evolution.skf.com/es/averias-prematuras-en-los-rodamientos-de-las-multiplicadoras-eolicas-y-grietas-wec/
[2] K. Tamada, H. Tanaka, Occurrence of brittle flaking on bearings used for automotive electrical instruments and auxiliary devices, Wear 199 (1996) 245–252.
[3] N. Kino, K. Otani, The influence of hydrogen on rolling contact fatigue life and its improvement, JSME Rev. 24 (2003) 289–294.
[4] B. Carr, More bearing failures for cruise ship pod drives, The eBearing News, http://www.ebearing.com/news2006/052201.htm, Mayo 2006.
[5] M.H. Evans, An updated review: white etching cracks (WECs) and axial cracks in wind turbine gearbox bearings, Mat. Sci. Tech., DOI: 10.1080 / 02670836.2015.1133022, 2016, 1-37.
[6] K. Stadler, J. Lai, R.H. Vegter, A review: the dilemma with premature white etching crack (WEC) bearing failure, J. ASTM Int. (2015), STP1580.
[7] A. Voskamp, “Microstructural Changes during Rolling Contact Fatigue,” Ph.D. thesis, Delft University of Technology, 1996.
[8] R.H. Vegter y J.T. Slycke, ‘Metal Physics and Rolling Contact Fatigue Testing’, presentado en el Noveno Simposio Internacional de Tecnologías de Acero de Rodamientos: Advances in Rolling Contact Fatigue Strength Testing and Related Substitute Technologies, 17 y 18 de noviembre de 2011, Tampa, FL, EE. UU., publicado en ASTM STP 1548 (editor J.M. Beswick), ASTM International 2012.
[9] J.-H. Kang y P.E.J. Rivera-Díaz-del-Castillo, ‘Carbide dissolution in bearing steel’, Computational Materials Science, 67 (2013) 364-372.
[10] J.-H. Kang, B. Hosseinkhani, R.H. Vegter y P.E.J. Rivera-Díaz-del-Castillo, ‘Modelling dislocation assisted tempering during rolling contact fatigue of bearing steels’, International Journal of Fatigue, volumen 75, junio de 2015, págs. 115–125.
[11] T. Lund, Sub-Surface initiated rolling contact fatigue-influence of non-metallic inclusions, processing history, and operating conditions. J ASTM Int 2010;7(5):81–96.
[12] D. Scott, B. Loy y G.H. Mills, “Metallurgical Aspects of Rolling Contact Fatigue, Proceedings of the Institution of Mechanical Engineers,” IMechE Arch., Vol. 181, n.° 15, 1966, págs. 94–103.
[13] P.C. Becker, Microstructural changes around non-metallic inclusions caused by rolling contact fatigue of ball-bearing steels, Metals Technology, Fatigue of ball-bearing steel, 234-243, 1981.
[14] J. Lai, K. Stadler, Investigation on the mechanisms of white etching crack (WEC) formation in rolling contact fatigue and identification of a root cause for bearing premature failure, http://dx.doi.org/ 10.1016/j.wear.2016.08.001, Wear, 2016.
[15] K. Stadler, R.H. Vegter, M. Ersson, D. Vaes, Causes for premature failures and the role of white etching cracks, Proceedings of the “Tribologie-Fachtagung 2016”, Gesellschaft für Tribologie (GfT), 2016.
[16] R.H. Vegter, J.T. Slycke, The role of hydrogen on rolling contact fatigue response of rolling element bearings. J ASTM Int 2009;7(2):1–12.
[17] I. Strandell, C. Faiers, T. Lund, Corrosion – one root cause for premature failure, in: Proceedings of the 37th Leeds-Lyon Symposium on Tribology, Leeds Trinity University, Leeds, UK, del 7 al 10 de septiembre de 2010, Elsevier, Nueva York, 2012.
[18] W. Solano-Alvarez, H.K.D.H. Bhadeshia, White-etching matter in bearing steels. Part I: controlled cracking of 52100 steel. Metall Mater Trans A 2014;45A:4906–15.
[19] W. Solano-Alvarez, H.K.D.H. Bhadeshia, White-etching matter in bearing steels. Part II: distinguishing cause and effect in bearing steel failure. Metall Mater Trans A 2014;45A:4916–31.
[20] Y. Kadin, M.Y. Sherif, Energy dissipation at rubbing crack faces in rolling contact fatigue as the mechanism of white etching area formation, International Journal of Fatigue 96, 114-126, 2017, http://dx.doi.org/ 10.1016/j.ijfatigue.2016.11.006.
[21] B. Gould, A. Greco, K. Stadler, X. Xiao, An analysis of premature cracking associated with microstructural alterations in an AISI 52100 failed wind turbine bearing using X-ray tomography, Material and Design 117, 2017, http://dx.doi.org/10.1016/j.matdes.2016.12.089.
[22] S.W. Ooi, A. Gola, R.H. Vegter, P. Yan, K. Stadler, Evolution of white-etching cracks and associated microstructural alterations during bearing tests, Material Science and Technology, http://dx.doi.org/10.1080/02670836.2017.1310431, 2017.
[23] H. Surborg, Einfluss von Grundölen und Additiven auf die Bildung von WEC in Wälzlagern, Dissertation, Otto-von-Guericke-Universität Magdeburg, 2014