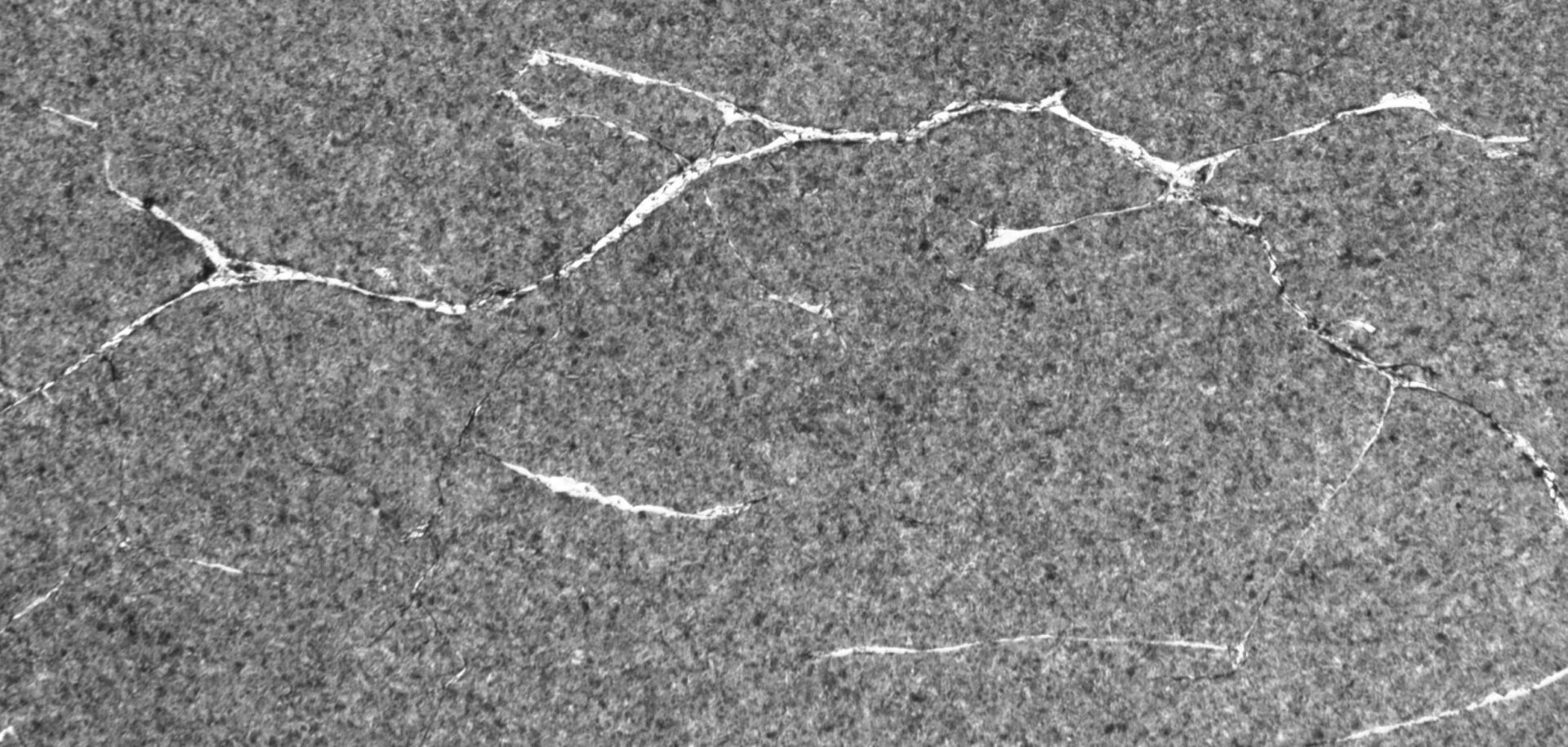
Les fissures de phase blanche WEC
Les roulements sont des pièces mécaniques qui jouent un rôle essentiel car ils supportent des charges et transmettent le mouvement. La course à la densité de puissance dans l’industrie moderne des équipements se traduit par des besoins toujours plus élevés en termes de capacité de charge et de fiabilité des roulements.
De nos jours, les avaries de roulements dues à la fatigue de contact roulant, appelée RCF (Rolling Contact Fatigue), sont plutôt rares et la durée de service réelle des roulements dépasse largement la durée nominale théorique. Cependant, dans certains cas, des avaries prématurées, à un stade représentant entre 5 et 10 % de la durée théorique du roulement, peuvent être observées. Nous appelons ici une avarie de roulement quand un écaillage apparaît soit sur l’une des pistes de roulement, soit sur un élément roulant.
Ces avaries prématurées se produisent généralement de manière très rapprochée dans le temps, les unes par rapport aux autres, ce qui se traduit sur le graphique de Weibull par une pente plus raide, par rapport à un essai de RCF (Fig. 2).
Bon nombre d’avaries prématurées se caractérisent par des réseaux étendus de fissures internes communément appelées fissures de phase blanche en raison de leur aspect blanc (Fig. 1). Ces fissures sont appelées WEC (White Etching Cracks). Elles se propagent vers la surface et provoquent un écaillage des pistes fréquemment observé au sein d’applications comme les multiplicateurs d’éoliennes [1], les transmissions, les alternateurs et les équipements auxiliaires automobiles [2][3], les machines à papier et les systèmes de propulsion de navires [4]. La Fig. 3 présente quelques exemples typiques. La cause de cette défaillance fait débat depuis une quinzaine d’années et plusieurs hypothèses, basées sur des approches différentes, circulent. Ces hypothèses sont passées en revue et analysées de façon exhaustive dans les références [5][6]. L’étude des avaries prématurées de roulements a permis une meilleure compréhension des aspects spécifiques de ce problème. Cependant, la cause et les mécanismes de défaillance ne font toujours pas consensus parmi les principaux spécialistes de la question.
Au cours des quatre dernières années, SKF a multiplié les études et recherches sur le phénomène de la fissuration WEC afin de clarifier le lien entre ces fissures et la fatigue RCF, ainsi que la fatigue accélérée (écaillage prématuré des roulements). Tandis que la communauté de la science des matériaux reste partagée sur cette question, les résultats des recherches menées par SKF appuient fortement la thèse selon laquelle la fissuration WEC se produit en bout de chaîne de défaillance et est une conséquence naturelle des réseaux de fissures préexistants dans les roulements victimes d’avarie prématurée. C’est le symptôme et non la cause profonde de la défaillance induite par la fatigue. Cet article reprend l’avis consensuel des experts SKF concernant les avaries prématurées et la fissuration WEC. Il propose en outre une définition des fissures WEC et un schéma de toutes les causes de défaillance à l’origine de ce phénomène.
Fissures de phase blanche (WEC)
Les fissures WEC sont des fissures de la microstructure de l’acier des roulements. Elles apparaissent sous forme de zones de phase blanche, appelées WEA (White Etching Area). Le terme de phase blanche se réfère à l’aspect blanc de la microstructure altérée d’un échantillon d’acier poli et ayant subi une attaque acide. Les zones touchées sont constituées de particules ultrafines de ferrite sans carbure nano-recristallisée ou de ferrite avec une très fine distribution de particules de carbure. Les zones WEA résultent de l’amorphisation due au frottement exercé sur les faces des fissures au passage des éléments roulants. Ces zones apparaissent blanches au microscope en raison de la faible réaction du matériau à l’attaque. Les zones de phase blanche autour des fissures présentent une dureté 10 à 50 % supérieure par rapport à la microstructure non altérée environnante.
Les causes de l’apparition des fissures WEC
WEC et fatigue RCF
On sait que les petits roulements lourdement chargés et fonctionnant durant une longue durée peuvent passer par plusieurs phases de fatigue avant la défaillance (on parle de fatigue à très grand nombre de cycles) [7]. La première phase dite d’adaptation conduit à une micro-déformation plastique, un écrouissage et, au final, l’accumulation de contraintes résiduelles. Lors de cette phase d’adaptation, la surface du roulement peut également subir une micro-déformation plastique par aplanissement des aspérités. Démarre ensuite une nouvelle phase représentant la majeure partie de la vie du roulement et caractérisée par des modifications progressives de la microstructure [8]. Au cours de cette phase, la distribution des particules de carbure est modifiée en raison de la déformation plastique [9][10]. De plus, l’austénite résiduelle est susceptible de se décomposer, et toutes les modifications de la microstructure s’accompagnent d’une accumulation des contraintes résiduelles. À un stade avancé de fatigue de contact du roulement, des régions sombres (DER) peuvent être observées, ainsi que des bandes de phase blanche plus faiblement inclinées (LAB) et d’autres fortement inclinées (HAB) (Fig. 4, à gauche). Ces bandes HAB et LAB présentent un aspect différent de celui des fissures WEC irrégulières observées suite à une avarie prématurée. Nous pouvons donc en conclure que la formation des fissures WEC irrégulières n’est pas liée à la fatigue de contact (RCF). Toutefois, la microstructure de ces zones de phase blanche n’est pas très différente, en ce qui concerne les cristaux, de celle des zones de phase blanche observées dans les avaries prématurées.
En ce qui concerne les roulements de moyennes et grandes dimensions, les effets peuvent différer par rapport à ceux évoqués ci-dessus pour les roulements de petites dimensions lourdement chargés. Comme pour n’importe quelle autre pièce mécanique, une avarie de ces roulements est causée par une rupture du maillon le plus faible (défauts dans la structure du matériau, comme des inclusions ou des porosités). Comme cela est expliqué dans la norme ISO/TR 1 281-2:2008, la limite de fatigue diminue avec la taille du roulement à partir d’un diamètre moyen de 100 mm. En outre, si l’on compare les effets de la pression de contact entre des roulements de différentes dimensions, on s’aperçoit que le volume soumis à des contraintes en sous-couche ainsi que l’impact négatif des maillons faibles, augmentent avec la taille des roulements. Les inclusions, naturellement présentes dans tous les aciers pour roulements, en sont un exemple [11]. Un autre facteur déterminant est la pression de contact elle-même. Dans l’exemple illustré par la Fig. 4 où des bandes faiblement inclinées et d’autres fortement inclinées apparaissent, la pression de contact est relativement élevée (> 3,2 GPa). Dans de nombreux roulements de moyennes et grandes dimensions, les pressions de contact qui s’exercent sont nettement inférieures à 3GPa, autrement dit, la plage des contraintes de fatigue est différente et entraîne des dommages globalement inférieurs et plus localisés autour des inclusions non-métalliques.
Ces phénomènes de fissures WEC et de phase sombre dans des roulements sujets à la fatigue RCF ont été rapportés dès les années 1960 [12] et au sein de SKF dans les années 1980[13]. Des analyses réalisées sur des roulements de moyennes et grandes dimensions victimes d’avaries prématurées (lors d’essais HALT [Highly Accelerated Life Test] ou d’essais d’endurance standard) ont confirmé que l’apparition de réseaux étendus de fissures WEC irrégulières était une conséquence naturelle de la fatigue RCF dans les roulements à rouleaux (Fig. 4, à droite).
Fissures WEC et fatigue accélérée
La différence entre un écaillage prématurée (souvent considéré comme une avarie WEC) et une fatigue RCF classique réside dans la durée qui s’écoule entre les différents événements et le début de l’écaillage (Fig. 5). De plus, par rapport aux essais d’endurance ou à la fatigue RCF classique, les avaries prématurées sont souvent associées au déclenchement d’une fissuration en plusieurs endroits comme le révèle bien souvent l’analyse des causes de défaillance.
Le déclenchement de la fissuration dans l’acier pour roulements peut avoir différentes causes et la fissuration peut s’accélérer dans certains cas de contraintes supérieures ou d’altération de la résistance due à des facteurs externes au roulement (Fig. 6).
Les contraintes exercées dans les roulements peuvent être plus élevées que prévu. Quelques exemples :
- une charge élevée de courte durée peut être causée par des phénomènes dynamiques ou thermiques inattendus entraînant des déformations importantes dans le mécanisme, des charges de bord, etc. ;
- des contraintes supplémentaires dans le matériau du roulement (générées par exemple par des écarts de forme des portées, défauts d’alignement ou d’autres facteurs) viennent accroître les contraintes globales [14] ;
- des conditions de contact tribologique difficiles (épaisseur du film lubrifiant insuffisante et/ou conditions de glissement) combinées à certains lubrifiants peuvent induire une augmentation des contraintes qui s’exercent sur les pistes [15].
La résistance du matériau d’un roulement peut être altérée par des facteurs externes soupçonnés de générer de l’hydrogène [16]. Parmi ces facteurs, citons :
- la contamination par l’eau,
- la corrosion [17] et
- les courants vagabonds.
Dans de telles situations, des conditions de charge modérée peuvent conduire à une avarie prématurée.
Des essais ont été réalisés chez SKF afin de vérifier les facteurs de fatigue accélérée identifiés en lien avec des contraintes supérieures et une résistance plus faible du matériau.
Une fois qu’une fissure a pris naissance (associée parfois à des régions de phase sombre [DER]), le frottement exercé sur les faces de la fissure entraîne un transfert de matériau d’un côté de la fissure vers l’autre [18]–[22]. Il en résulte une fissure sinueuse avec accumulation d’une microstructure de phase blanche sur la face de la fissure.
Le développement de zones WEA dépend également de l’orientation de la fissure en sous-couche et donc des modes de déformation et des forces qui s’exercent sous la surface. C’est la raison pour laquelle ces zones sont plus souvent observées dans des fissures orientées horizontalement (c’est-à-dire parallèles aux pistes), tandis que les parties des fissures orientées verticalement présentent moins de WEA (Fig. 7). La formation de WEA dépend également de l’espace entre les faces des fissures, du nombre de cycles de contraintes, ainsi que des conditions de contraintes internes.
Exemples de fissuration WEC due à des contraintes élevées
Les Fig. 8, 9 et 10 montrent deux cas de fissuration WEC générée par des contraintes. Les résultats présentés sur les Fig 8 et 9 se rapportent à un banc d’essai conçu pour introduire artificiellement des contraintes ou déformations de matière du roulement par ondulation de la surface de la portée du roulement. Il en résulte des contraintes de traction locales au niveau de la bague intérieure du roulement. L’essai est réalisé sur un roulement à rouleaux cylindriques dont la bague intérieure (de 220 mm de diamètre d’alésage) est montée avec un serrage à ajustement normal sur un manchon présentant cinq ondulations et lui-même monté sur un arbre avec un ajustement serré. Ce manchon ondulé, obtenu par usinage, génère cinq zones de contraintes de traction d’environ 205 MPa à proximité de la surface de la piste de la bague intérieure. Le roulement utilisé pour le test a été adapté à la capacité du banc d’essai afin d’obtenir les contraintes de contact requises : il est doté d’une seule rangée de huit rouleaux cylindriques, au lieu de deux rangées de 24 rouleaux, dans la partie centrale de la bague intérieure (Fig. 8). Le matériau du roulement est l’acier SAE 52100 (100Cr6). Le roulement présente une trempe martensitique avec jusqu’à 7 % (en volume) d’austénite résiduelle et une dureté de 62 HRC.
Les roulements ont été testés sous une pression de Hertz maximum de 1,8 GPa et avec une valeur kappa d’environ 2. L’essai a été mené jusqu’à l’avarie.
Sur l’un des roulements monté sur portée ondulée, une fissure axiale est apparue sur la piste au bout de 1 150 heures (soit 6,35X108 cycles de contrainte). Sur le deuxième roulement, deux fissures axiales sont apparues au bout de 1 570 heures (soit 8,67X108 cycles de contrainte). La position circonférentielle des fissures axiales coïncide avec l’un des pics d’ondulation où une zone de contraintes de traction est présente.
Il convient de noter que quatre roulements similaires avaient été testés antérieurement dans des conditions identiques avec un serrage standard sur l’arbre (sans ondulation artificielle) et qu’aucun n’avait présenté de défaillance avant l’arrêt de l’essai au bout de 2 200 heures (1,21×109 cycles de contrainte). Aucune fissure superficielle ni fissure WEC en sous-couche n’avait par ailleurs été détectée lors de l’examen postérieur.
Cet examen a consisté en des essais non destructifs aux ultrasons et avec produit d’imprégnation coloré, une mesure de la circularité de la bague, une étude fractographique et un examen métallographique au microscope.
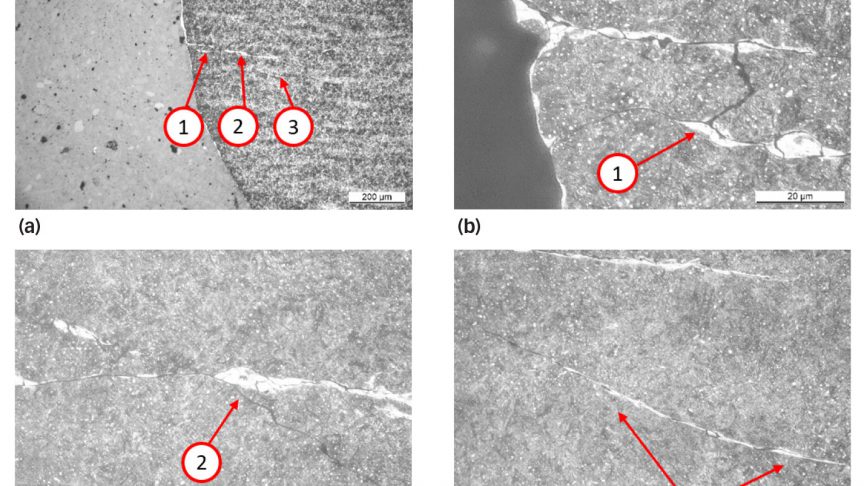
Sur une coupe parallèle de l’échantillon présentant une fissure ouverte (Fig. 9), on observe, qu’après attaque, une partie de la fissure principale présente un aspect blanc visible au microscope et qu’à une profondeur d’environ 500 µm sous la surface, la fissure s’est ramifiée. Les fissures ramifiées sont également des WEC qui se sont propagées dans une direction parallèle à la piste à environ 400 µm de la fissure principale. Le grossissement des fissures ramifiées (Fig. 9b, c et d) corrobore la thèse selon laquelle les fissures sont connectées ensemble et forment un réseau de WEC sous la surface. Des coupes parallèles ont également été réalisées à deux autres positions circonférentielles qui correspondent aux pics d’ondulation du manchon. Tandis qu’aucune fissure n’était visible en surface, une multitude de WEC ont pu être observées en sous-couche dans ces régions où des contraintes de traction étaient présentes pendant le test, induites par l’ondulation. Pour plus de détails, consultez la référence [14].
Les résultats présentés sur la Fig. 10 se rapportent à un essai réalisé sur des roulements à rotule sur rouleaux 23024 exposés à des charges élevées de courte durée.
Sous la charge élevée de courte durée, le roulement subit une pression de contact supérieure à 3 GPa pendant environ 15 minutes dans des bonnes conditions de lubrification (valeur kappa d’environ 3,5).
Après avoir été brièvement exposé à une charge élevée, le roulement est ensuite installé sur un banc d’essai radial. Ce dernier permet d’exercer une pression de Hertz modérée de 1,7 GPa avec une valeur kappa d’environ 2. Dans ces conditions, les roulements atteignent la fin de l’essai d’une durée de 3,3×107 cycles ou sont victimes d’une avarie avant ce stade. La Fig. 10 présente une coupe circonférentielle et une attaque au nital d’une bague extérieure. Le roulement en question a présenté une défaillance après 1,9×107 cycles en raison d’un écaillage dans la zone chargée de la bague extérieure.
Exemples de fissuration WEC due à une résistance inférieure du matériau
Un exemple de WEC en sous-couche dans un roulement chargé en hydrogène a déjà été donné à la Fig. 7. La référence [22] fournit une post-analyse détaillée relative à des roulements rigides à billes et des roulements à billes à contact oblique chargés en hydrogène et sans hydrogène.
Exemples de fissuration WEC en conditions de frottement mixte et impact du lubrifiant
Des analyses du lubrifiant réalisées au moyen de bancs d’essai FE8 sur des butées à rouleaux cylindriques 81212 victimes d’avarie ont révélé la présence de fissures WEC [23]. Les conditions de l’essai, à savoir un frottement mixte combiné à un glissement cinématique élevé (conditions non représentatives pour les roulements à rouleaux radiaux) ne permettent pas à ce jour de tirer des conclusions. Il n’est pas possible pour le moment de déterminer si les fissures WEC lors des essais sur banc FE8 sont plutôt la conséquence d’une fatigue sous-jacente (dans laquelle le lubrifiant joue également un rôle important) ou le résultat d’une pénétration d’hydrogène, ou encore les deux à la fois.
Des essais ont été réalisés sur des butées à rouleaux cylindriques 81212 acier/acier. Leur matériau est un acier pour roulements standard conformément à la norme SAE 52100, trempé martensitique, à teneur en austénite résiduelle <3 % et d’une dureté d’environ 60 HRC. Ces roulements sont testés sous des charges modérées (pression de contact max. d’environ 1,9 GPa) et dans des conditions de lubrification médiocres (valeur kappa autour de 0,3).
Différentes huiles et mélanges ont été testés. La Fig. 11 montre l’aspect typique d’une avarie.
Même si cela n’est pas montré ici de façon détaillée, sur l’ensemble des tests réalisés, il apparaît que les rouleaux sont souvent sujets à des avaries, tandis que les rondelles le sont rarement. Les essais ont été réalisés jusqu’à l’avarie (écaillage) ou interrompus. Concernant les roulements qui ont présenté une avarie par écaillage et sur lesquels des fissures WEC ont été observées, on estime que les fissures WEC internes ont pu se développer avant tout écaillage. En effet, des fissures internes sont parfois également présentes dans des éléments non écaillés. Pour plus de détails, consultez la référence [15].
Discussion
Les résultats ci-dessus expliquent clairement que si une fissure WEC peut être observée dans tous types d’applications, sur tous types de roulements soumis à tous types de traitements thermiques (la trempe à cœur comme la cémentation) [1], c’est parce qu’elle se produit en bout de chaîne de défaillance et qu’elle est une conséquence naturelle des réseaux de fissures dans les roulements victimes d’avarie précoce.
La clé pour identifier les causes de défaillance prématurées des roulements ne réside pas seulement dans l’étude des fissures WEC, mais plutôt dans la recherche de facteurs affaiblissants (par rapport à des contraintes supérieures à celles estimées lors de la conception de la machine ou une résistance inférieure du matériau dû, par exemple, à la présence d’hydrogène, de passage de courant, etc.) à l’origine d’une fatigue accélérée.
De manière générale, l’avarie d’une pièce mécanique est due à la rupture du maillon le plus faible. Celle-ci se produit lorsque les contraintes locales dépassent la résistance locale. Une avarie prématurée est le résultat d’un affaiblissement significatif du maillon le plus faible. La fiabilité des roulements dans diverses applications obéit au principe du maillon le plus faible. Il y a toujours des points faibles au sein du matériau ou sur la surface de contact active. L’avarie du roulement se produit à la rupture du maillon le plus faible. Lorsque la lubrification est insuffisante ou que la surface est rugueuse (empreintes causées par des impuretés par ex.), le maillon le plus faible peut très bien se situer sur la surface. L’avarie dans ce cas est causée par une altération de la surface, comme la fatigue de surface ou l’usure. Dans des conditions de lubrification satisfaisantes, le maillon le plus faible peut se trouver sous la surface, en raison de la présence de défauts dans le matériau comme des inclusions ou de contraintes de cisaillement élevées induites par la pression de Hertz. Dans ce cas, l’avarie résulte du déclenchement et de la propagation de fissures par les défauts pré-existants dans le matériau. En ce qui concerne les roulements, la résistance du maillon le plus faible peut être liée à la limite de charge ou de contrainte appelée limite de fatigue. Une avarie se produit lorsque la limite de fatigue est dépassée. Une avarie prématurée de roulement est le résultat d’une diminution considérable de la limite de fatigue, autrement dit d’une réduction significative de la résistance du maillon le plus faible. C’est l’affaiblissement, dû à des contraintes supérieures ou à une altération de la résistance du matériau, qui est à l’origine du déclenchement et de la propagation accélérée de fissures, et non les fissures WEC. En l’absence d’affaiblissement, un roulement peut présenter une avarie résultant d’une fatigue RCF classique due à un simple écaillage avec peu de, voire aucune, fissures WEC, car les fissures se propagent rapidement lorsque le matériau est en fin de vie [7]. Autrement dit, le matériau n’a plus le temps de se transformer au sein du système de fissures. En cas d’affaiblissement important, le roulement peut être victime d’une avarie précoce sous forme d’un réseau de fissures WEC étendu, car le matériau au sein du système de fissures a le temps de se transformer localement, passant d’une zone sombre DEA à une zone WEA. Avec un niveau de sévérité croissant, des fissures axiales avec une zone WEA moins étendue voire une fracture sans zone WEA peuvent apparaître du fait d’une propagation trop rapide des fissures [14].
Recommandations
Chaque avarie prématurée de roulement est unique. Si l’on reprend la Fig. 6, il apparaît que les causes d’un écaillage prématuré peuvent être extrêmement variées. Il n’y a pas une seule cause et chaque cas d’avarie doit être examiné en tenant compte des conditions de service.
Le Tableau 1 fournit des recommandations très générales basées sur le classement des facteurs d’affaiblissement entre « contraintes supérieures » et « résistance du matériau altérée ». Il fait la distinction entre les recommandations relatives à l’application proprement dite (le système de roulement, le processus de conception) et celles visant à renforcer la robustesse du roulement. Le choix de la meilleure option pour éviter les avaries précoces dépend des conditions particulières de l’application. Pour des conseils plus détaillés, veuillez contacter le Service Applications SKF.
Références
[1] Défaillances prématurées des roulements dans les multiplicateurs d’éoliennes et fissures de phase blanche (WEC),
SKF Evolution n°2, 2013, http://evolution.skf.com/fr/defaillances-prematurees-des-roulements-dans-les-multiplicateurs-deoliennes-et-fissures-de-phase-blanche-wec/
[2] K. Tamada, H. Tanaka, Occurrence of brittle flaking on bearings used for automotive electrical instruments and auxiliary devices, Wear 199 (1996) 245–252.
[3] N. Kino, K. Otani, The influence of hydrogen on rolling contact fatigue life and its improvement, JSME Rev. 24 (2003) 289–294.
[4] B. Carr, More bearing failures for cruise ship pod drives, The eBearing News, http://www.ebearing.com/news2006/052201.htm, mai 2006.
[5] M.H. Evans, An updated review: white etching cracks (WECs) and axial cracks in wind turbine gearbox bearings, Mat. Sci. Tech., DOI: 10.1080 / 02670836.2015.1133022, 2016, 1-37.
[6] K. Stadler, J. Lai, R.H. Vegter, A review: the dilemma with premature white etching crack (WEC) bearing failure, J. ASTM Int. (2015), STP1580.
[7] A. Voskamp, « Microstructural Changes during Rolling Contact Fatigue, » Ph.D. thesis, Delft University of Technology, 1996.
[8 R.H. Vegter et J.T. Slycke, ‘Metal Physics and Rolling Contact Fatigue Testing’, présenté dans le cadre du neuvième International Symposium on Bearing Steel Technologies: Advances in Rolling Contact Fatigue Strength Testing and Related Substitute Technologies, 17-18 novembre, 2011, Tampa, FL, USA, publié dans ASTM STP 158 (éditeur J.M. Beswich), ASTM International 2012.
[9] J.-H. Kang et P.E.J. Rivera-Diaz-del-Castillo, ‘Carbide dissolution in bearing steel’, Computational Materials Science, 67 (2013) 364-372.
[10] J.-H. Kang, B. Hosseinkhani, R.H. Vegter et P.E.J. Rivera-Diaz-del-Castillo, ‘Modelling dislocation assisted tempering during rolling contact fatigue of bearing steels’, International Journal of Fatigue, Volume 75, juin 2015, pages 115–125.
[11] T. Lund, Sub-Surface initiated rolling contact fatigue-influence of non-metallic inclusions, processing history, and operating conditions. J ASTM Int 2010;7(5): 81–96.
[12] D. Scott, B. Loy et G.H. Mills, « Metallurgical Aspects of Rolling Contact Fatigue, Proceedings of the Institution of Mechanical Engineers, » IMechE Arch., Vol. 181, No. 15, 1966, pp. 94–103.
[13] P.C. Becker, Microstructural changes around non-metallic inclusions caused by rolling contact fatigue of ball-bearing steels, Metals Technology, Fatigue of ball-bearing steel, 234-243, 1981.
[14] J. Lai, K. Stadler, Investigation on the mechanisms of white etching crack (WEC) formation in rolling contact fatigue and identification of a root cause for bearing premature failure, http://dx.doi.org/ 10.1016/j.wear.2016.08.001, Wear, 2016.
[15] K. Stadler, R.H. Vegter, M. Ersson, D. Vaes, Causes for premature failures and the role of white etching cracks, Proceedings of the « Tribologie-Fachtagung 2016 », Gesellschaft für Tribologie (GfT), 2016.
[16] R.H. Vegter, J.T. Slycke, The role of hydrogen on rolling contact fatigue response of rolling element bearings. J ASTM Int 2009;7(2):1–12.
[17] I. Strandell, C. Faiers, T. Lund, Corrosion – one root cause for premature failure, in: Proceedings of the 37th Leeds-Lyon Symposium on Tribology, Leeds Trinity University, Leeds, UK, 7–10 September, 2010, Elsevier, New York, 2012.
[18] W. Solano-Alvarez, H.K.D.H. Bhadeshia, White-etching matter in bearing steels. Part I: controlled cracking of 52100 steel. Metall Mater Trans A 2014;45A:4906–15.
[19] W. Solano-Alvarez, H.K.D.H. Bhadeshia, White-etching matter in bearing steels. Part II: distinguishing cause and effect in bearing steel failure. Metall Mater Trans A 2014;45A:4916–31.
[20] Y. Kadin, M.Y. Sherif, Energy dissipation at rubbing crack faces in rolling contact fatigue as the mechanism of white etching area formation, International Journal of Fatigue 96, 114-126, 2017, http://dx.doi.org/ 10.1016/j.ijfatigue.2016.11.006.
[21] B. Gould, A. Greco, K. Stadler, X. Xiao, An analysis of premature cracking associated with microstructural alterations in an AISI 52100 failed wind turbine bearing using X-ray tomography, Material and Design 117, 2017, http://dx.doi.org/10.1016/j.matdes.2016.12.089.
[22] S.W. Ooi, A. Gola, R.H. Vegter, P. Yan, K. Stadler, Evolution of white-etching cracks and associated microstructural alterations during bearing tests, Material Science and Technology, http://dx.doi.org/10.1080/02670836.2017.1310431, 2017.
[23] H. Surborg, Einfluss von Grundölen und Additiven auf die Bildung von WEC in Wälzlagern, Dissertation, Otto-von-Guericke-Universität Magdeburg, 2014