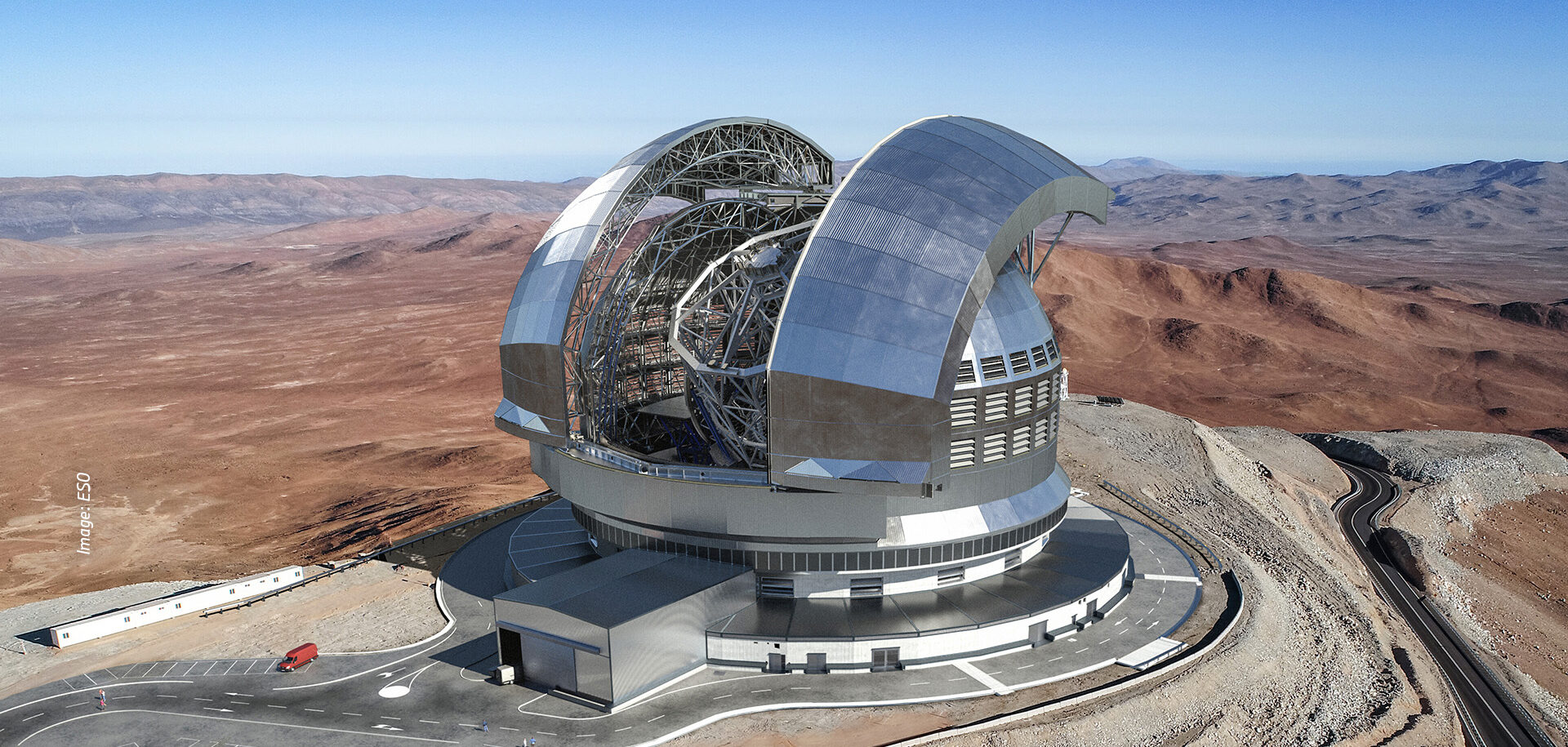
Head in the stars: under the dome of ESO’s Extremely Large Telescope
Construction of the world’s largest optical/near-infrared telescope is underway in Chile. A small component from SKF is playing a crucial role in its future accuracy and performance.
In the Atacama Desert in Chile, at an altitude of nearly 3,000 metres, an enormous construction is taking shape. ESO’s Extremely Large Telescope (ELT), including the dome structure that encloses the telescope, is a massive 86 metres in diameter. That’s roughly equivalent to the size of a football pitch. If we take the auxiliary building around the dome into consideration the diameter extends to 115 metres, with the height, at 80 metres, almost as tall as London’s Big Ben. The project is expected to be completed in 2028 at an estimated total cost of 1.4 billion euros. It has now reached the halfway point in its construction.
The ELT will, among other things, search for exoplanets around other stars, probe the universe’s dark sector and make detailed studies of early galaxies. Despite the magnitude of its size and scope, the ELT’s performance will rely in part on a set of adjustable chocks from SKF that are 80 millimetres in diameter.
Construction to Italian consortium
In 2016, the ACe consortium led by Cimolai, a leading construction company in the design and construction of large steel structures, won a contract from the European Southern Observatory, the intergovernmental organization that builds the ELT, to design, manufacture, transport and commission the telescope’s dome and main structure. The dome covers and protects the main structure and includes two enormous sliding roof doors that open at night and close during the day, sealing the interior from wind, rain, dust and light. An internal air conditioning system ensures thermal stability for the telescope and its optomechanical units.
Cimolai is involved in several elements of the ELT, including the mechanisms that open and close the dome’s roof. The company has also incorporated antiseismic design elements in both the dome and the main structure, as the observatory is situated in one of the world’s most seismically active areas. It also needed to take into account deformations due to such factors as gravity, wind, temperature, concrete shrinkage and settling of soil.
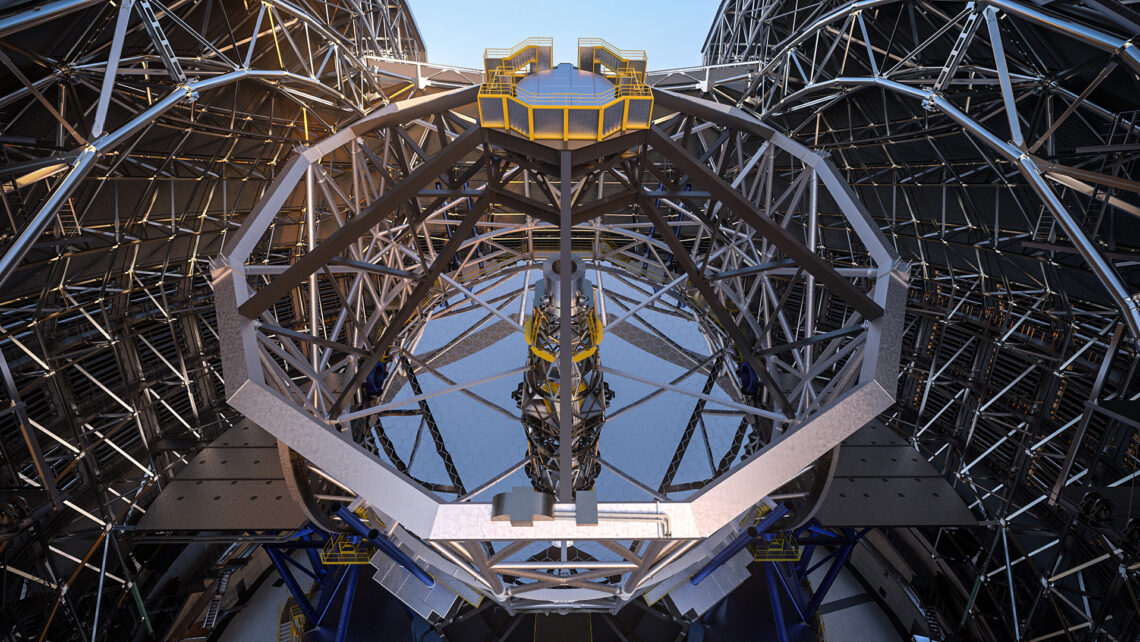
The main mirror is crucial
A critical part of the ELT is the main mirror, the M1 mirror, which collects the light from the sky. “It’s crucial to the whole operation of the telescope,” says Marco Colussi, senior structural engineer at Cimolai and the project design manager.
The ability to adjust and readjust is key to the success of the telescope.
Marco Colussi, senior structural engineer at Cimolai and the project design manager
The mirror is 39 metres wide and is made from 798 separate hexagonal segments, which must be fitted together onto a base structure. Cimolai must ensure that they are accurately assembled onto the huge steel substructure, to provide optimal mirror performance. This is where the adjustable chocks come in.
“Each mirror segment is supported by three steel flanges,” Colussi says. “Each flange sits on four SKF Vibracon adjustable chocks.” The flange/chock arrangement acts as an interface plate between each mirror segment and the underlying steel support structure. “The ability to adjust and readjust is key to the success of the telescope,” he says.
Delicate adjustment
Each SKF Vibracon adjustable chock, a low-profile version, allows up to 12 millimetres of adjustment. However, the application itself required more than 12 millimetres of adjustment, meaning that the design had to be tweaked in a number of ways.
Firstly, Cimolai inserted additional washers – allowing the adjustment range to be extended to more than 12 millimetres. “Each individual flange must be installed and adjusted with the accuracy of tenths of a millimetre – across the 39-metre width of the mirror,” Colussi says. The chock also had to fit within a limited design space, so it could not be greater than 25 millimetres in height.
Special projects sometimes call for special solutions. One of the most surprising aspects was that the chocks needed to be installed upside-down. “This helped us meet the stiffness requirements of the system,” says Colussi.
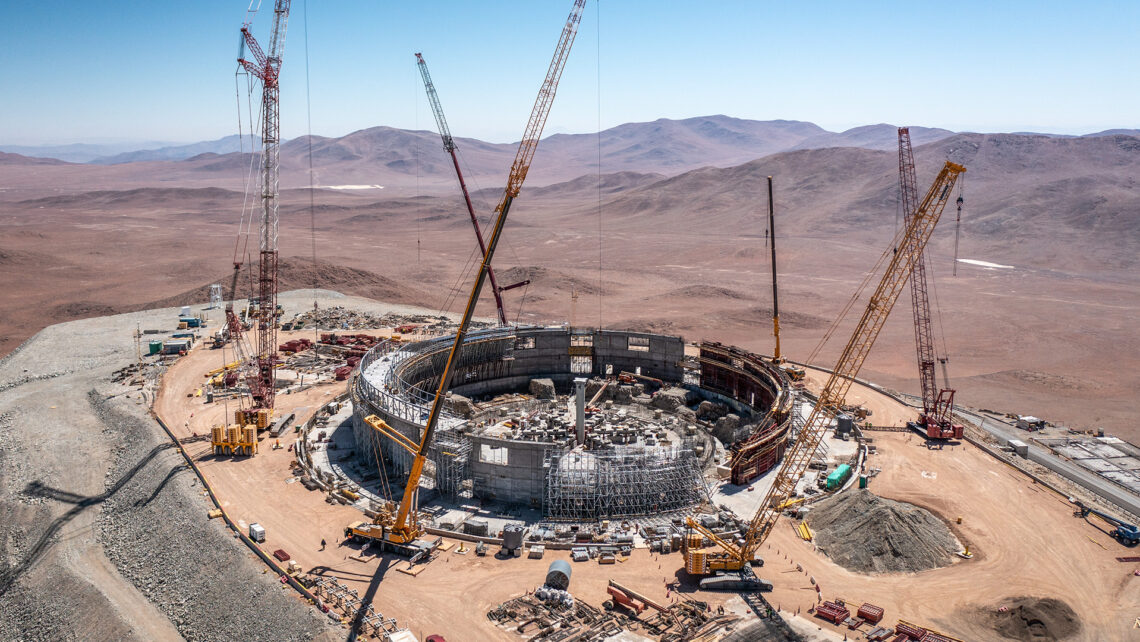
Upside down installation
Usually, the smaller diameter of the chock is at the top. However, installing it this way would have had a negative impact on the stiffness of the interface plate – causing it to lose stiffness. Installing the chock upside-down helped to direct the load path correctly and maintain a higher stiffness. High stiffness is critical because it helps to save an enormous amount of weight. “If the plates were less stiff, we would need to make them thicker,” says Colussi.
Thicker plates – three for each mirror segment – would add a huge amount of weight to the structure and would be detrimental to the telescope’s performance: a heavier M1 mirror support would increase the deflection of the complete support construction, reducing the performance of the mirror. “The dynamic behaviour of the entire telescope would also suffer,” Colussi says, explaining that if the foundation is not precise, stiff and stable it will not guarantee the severe requirements of deformation and repeatability over time, meaning the structure above it, the mirror, will not work properly.
Updated Vibracon improved the design
By happy coincidence, the design of the Vibracon chock itself was updated during the design phase, and the changes helped to improve the design of the telescope. The rated load was increased from 90 to 140 kN and the bottom ring was made thicker. Overall, the combination of adjustability, stiffness and weight savings made for a more streamlined design, helping to enhance the operation of the M1 mirror.
For Cimolai, taking on such a huge project is something of a new departure. “This is the first telescope that we’ve designed and manufactured,” says Colussi, “and we’d like to expand in this field. The M1 mirror is one of the most critical parts of the telescope, and the SKF Vibracon chocks play a key role in the design.”
Micron tolerances
For its enormous size, the Extremely Large Telescope, or ELT, requires extremely precise engineering tolerances to probe the mysteries of the universe successfully.
“It’s the size of a football stadium, but requires micron-level accuracy,” says René Vermeulen, senior engineering sales manager at SKF. “It’s basically a Swiss watch on a huge scale.”
The M1 mirror is one of the most challenging subsystems within the whole ELT design – with thousands of sophisticated components, including more than 9,500 SKF Vibracon SM 16 ELP-ASTR low-profile chocks, 12 for each mirror segment.
Adjustability is critical if the mirror is to capture images accurately. Indeed, mirror alignment must be guaranteed over the entire lifetime of the telescope, during hundreds of thousands of movements and in a harsh and highly seismic environment.
The chocks are individually surface treated, to give them a consistent quality and extend their performance in such a demanding environment.
Vermeulen says the new configuration of Vibracon chock was developed during the design phase. “We were adding features to our own product, which made it better for the project,” he says. “It also allows more adjustment: by reducing the play, it’s more accurate. It matched Cimolai’s needs for the design.”
In 2022 SKF developed a hook spanner that is 2 millimetres thick. The spanner provides easier adjustment of the chocks when mounted upside down.
ELT statistics
Light-collecting area: 978 square metres
Number of main mirror segments: 798
Weight of main structure: 4,600 tonnes
Weight of dome: 6,100 tonnes
Weight of steel used in project: around 10,000 tonnes
Weight of glass-ceramic Zerodur® in telescope mirrors: 140 tonnes
Planned duration of design-construction phase: 12 years
Estimated lifespan: 30+ years
Total budget: 1.4 billion euros