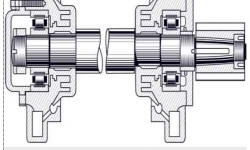
100 anni di evoluzione dei cuscinetti a rulli cilindrici
In più di 100 anni di evoluzione dei cuscinetti il disegno di quelli a rulli cilindrici ha subito una serie di miglioramenti. Grazie all’ampia esperienza, questi tipi di cuscinetti sono in grado di offrire minore attrito, elevata capacità di carico, maggiore durata e “downsizing”.
I perfezionamenti dei cuscinetti a rulli cilindrici fanno parte della storia dello sviluppo dei cuscinetti volventi, iniziato nella seconda metà dell’ottocento, quando vennero fondate le prime fabbriche di biciclette, che avevano bisogno di questi prodotti. La parallela domanda di cuscinetti a sfere e a rulli da parte di tutta l’industria meccanica portò all’avvento di aziende in grado di progettarli e costruirli.
Sin dai primi tempi era evidente la capacità dei cuscinetti volventi di far risparmiare energia. In una ricerca condotta nel 1905 a New York, W. P. Graham della Syracuse University mise a confronto i consumi di due vetture, una munita di bronzine e l’altra di cuscinetti a rulli, dimostrando che con questi ultimi si poteva risparmiare un 52 % di energia.
IL PRIMO MODERNO CUSCINETTO A RULLI CILINDRICI
Nel 1909, il Dr. Ing. Josef Kirner, un ingegnere della Norma Compagnie GmbH di Cannstatt in Germania, brevettò un già moderno cuscinetto a rulli cilindrici che, per evitare le dannose sollecitazioni di estremità in corrispondenza delle testate dei rulli, aveva le piste bombate (fig. 1). I rulli erano corti, lavorati con cura e guidati con precisione tra gli orletti, cosa che portava con sé numerosi vantaggi dell’importanza dei quali Kirner si rese conto, nonostante le perplessità di molti colleghi.
Nel 1914, in Svezia, la SKF di Göteborg acquistò metà delle azioni della Norma Compagnie GmbH, incorporandola nel Gruppo SKF. Da allora la storia del cuscinetto a una corona di rulli cilindrici si intrecciò con quella della SKF e fu contrassegnata da numerose pietre miliari.
Il periodo tra il 1920 e il 1925 è caratterizzato dal riconoscimento generale dell’importanza del cuscinetto a rulli cilindrici, tanto che molti concorrenti cominciarono a copiarlo. Gli anni venti videro importanti sviluppi nelle applicazioni ferroviarie (fig. 2): l’accoppiata delle esecuzioni NU e NH per i motori da trazione – tuttora in uso – e quella delle esecuzioni WJ e WUJ per le boccole.
Negli anni trenta, la SKF promosse la standardizzazione delle dimensioni d’ingombro dei cuscinetti a rulli cilindrici, che divennero identiche a quelle dei tipi standard radiali a sfere. Il diametro dei rulli dei tipi delle serie strette divenne uguale alla loro larghezza, mentre il rapporto lunghezza-diametro di quelli dei tipi delle serie larghe diventò pari a circa 1,5. Vennero fissate quasi tutte le odierne classiche esecuzioni di base.
Il rullo B vide la luce negli anni cinquanta. Nei dieci anni precedenti erano state elaborate le prime descrizioni teoriche del profilo ideale dei corpi volventi e comparve il rullo bombato con profilo costituito da un arco di cerchio. Il profilo bombato trovò la sua conferma nella teoria di Lundberg e infine portò alla nascita appunto del rullo B che aveva un profilo rettilineo nella parte centrale e leggermente bombato verso le estremità. Una volta utilizzato nella pratica i progressi non mancarono. Era infatti possibile determinare in modo più preciso l’entità dell’altezza della bombatura. Questa doveva però ancora essere valutata in presenza di disallineamento.
L’introduzione negli anni novanta dei cuscinetti tipo E fu una pietra miliare nella storia del cuscinetto a rulli cilindrici. L’esecuzione E consentiva di ottimizzare la sezione trasversale dei cuscinetti, inserendo non solo rulli più grandi e più lunghi (figg. 3ae 3b), ma anche un numero maggiore di questi (figg. 4a e 4b). Ne conseguiva una capacità di carico maggiore – in media del 35% – e una durata assai più lunga.
Il cuscinetto tipo E comportò un notevole impegno per le fabbriche, dato che si avevano rulli con dimensioni diverse e nuove gabbie. Tutti i cuscinetti delle serie dimensionali 2, 22, 3 e 23 vennero convertiti all’esecuzione E. Alcuni tipi delle altre serie vennero completamente ridisegnati.
Il 1981 vide l’introduzione del cuscinetto a rulli cilindrici di esecuzione EC, con contatto modificato tra le estremità dei rulli e gli orletti. La geometria degli orletti era di tipo “aperto” (fig. 5); mentre le estremità dei rulli erano trattate in superficie per migliorare l’efficacia del lubrificante, ridurre l’attrito e abbassare la temperatura, con conseguente minore necessità di manutenzione. Con un migliore contatto tra le estremità dei rulli e gli orletti, per i cuscinetti che hanno questi ultimi su entrambi gli anelli, si ha una maggiore capacità di carico assiale.
Un’altra miglioria nelle condizioni di contatto si ebbe con l’introduzione nel 1984 del profilo logaritmico delle piste dei rulli, che assicura una distribuzione ottimale del carico tra i rulli e le piste, tale da ridurre notevolmente il rischio di avere sollecitazioni di estremità e da migliorare l’affidabilità operativa anche nelle applicazioni in cui si hanno disallineamenti e inflessioni dell’albero (fig. 6).
UNA PIETRA MILIARE NELLE PRESTAZIONI
Il nuovo millennio è cominciato con una realizzazione assai importante, l’introduzione dei cuscinetti a rulli cilindrici SKF Explorer (fig. 7), che sono il risultato di molti anni di intense ricerche da parte di un team internazionale di scienziati e tecnici SKF. In tutto questo tempo gli specialisti SKF in materiali e tecnologie di fabbricazione, insieme ai responsabili della produzione, hanno introdotto con successo numerosi perfezionamenti, in particolare:
-
L’acciaio dei cuscinetti si presenta estremamente puro e omogeneo, con valori delle inclusioni veramente minimi. Il tenore di ossigeno, che è un indicatore della purezza dell’acciaio, è stato portato a valori bassissimi: in tal modo cresce la resistenza alla fatica nei contatti di rotolamento e la durata del cuscinetto aumenta.
-
Nei trattamenti termici le nuove procedure sono atte a rendere ottimale la resistenza dei cuscinetti nei confronti delle condizioni operative e delle temperature, senza influire sulla stabilità dimensionale.
-
La durezza degli anelli e dei rulli è stata scelta in modo tale da rendere tali componenti meno sensibili alle sostanze contaminanti e portare la durata di esercizio a valori molto elevati.
-
Il miglioramento dei processi di fabbricazione ha contribuito a un significativo progresso nella qualità dei prodotti. Gli anelli presentano una migliore rotondità, mentre è stato ulteriormente ridotto lo scostamento dei rulli dalla forma ottimale. L’esistenza di tolleranze più ristrette può non essere materialmente visibile, ma in realtà i cuscinetti si presentano molto più silenziosi e con minori vibrazioni.
-
Il profilo logaritmico di contatto dei rulli è stato ulteriormente affinato. I cuscinetti sono così meno sensibili ai piccoli disallineamenti e posso reggere carichi maggiori.
-
Nei cuscinetti SKF Explorer sono anche stati ottimizzati i contatti tra le estremità dei rulli e gli orletti.
-
L’andamento della zona di transizione tra la sezione cilindrica e la rastrematura del profilo logaritmico è stato reso ottimale.
-
La finitura superficiale delle piste di rulli e anelli è stata ulteriormente perfezionata e assicura migliori condizioni di lubrificazione, tanto che i cuscinetti possano funzionare più a lungo anche quando queste sono scarse.
-
I cuscinetti SKF Explorer sono disponibili con gabbie di forme e materiali diversi per tenere conto delle varie condizioni di lavoro. La forma costruttiva di tutte le gabbie usate nei cuscinetti SKF Explorer tende a ottenere una buona lubrificazione di tutte le superfici in contatto relativo, anche in occasione di eventuali interruzioni dell’afflusso di lubrificante.
I perfezionamenti sono stati avvalorati da estese prove di durata.
C’è da essere certamente molto orgogliosi dei risultati ottenuti: i cuscinetti SKF Explorer a una corona di rulli cilindrici fissano nuovi standard in termini di prestazioni e durata. Essi possiedono una maggiore capacità di reggere i carichi dinamici e una durata che è fino a tre volte quella dei precedenti tipi standard, che è già superiore a quella di tutti i cuscinetti a rulli cilindrici tradizionali. Recentemente, alcuni cuscinetti di medie dimensioni sono stati riprogettati e aggiunti alla classe di prestazioni SKF Explorer. Sono contrassegnati dal suffisso /PEX nell’appellativo.
Il miglioramento delle prestazioni dei cuscinetti SKF a rulli cilindrici nel corso di un secolo ha permesso un significativo “downsizing”, pur conservando alle applicazioni le prestazioni desiderate (fig. 8). Un minore
attrito e una sensibile riduzione della massa consentono di ridurre i consumi di energia.
Tuttavia il progresso non si ferma qui. Per ottenere una grande affidabilità operativa in alcune applicazioni, quali quelle dell’industria mineraria e dei riduttori, specie dell’industria eolica, è della massima importanza l’elevata capacità di carico. La SKF ha realizzato cuscinetti a rulli cilindrici ad elevata capacità di carico (figg. 9a e 9b). Questi cuscinetti SKF Explorer presentano un maggior numero di rulli rispetto ai cuscinetti SKF Explorer standard, pur mantenendo le stesse dimensioni d’ingombro e le principali dimensioni interne. Lo spessore delle pareti rimane invariato per conservare l’esecuzione E che ha dato buona prova di sé per 45 anni.
Le gabbie sono frutto di grande innovazione. Nei cuscinetti a rulli cilindrici ad elevata capacità di carico è sistemata molto sopra o sotto il diametro primitivo del cuscinetto ed è guidata sugli orletti degli anelli. Quella a feritoie in acciaio è molto robusta rispetto a quella massiccia e in due pezzi, pur consentendo di avere un numero maggiore di rulli.
Rispetto ai cuscinetti standard e a seconda dalla forma costruttiva della gabbia, il numero di rulli può essere aumentato di due unità nei cuscinetti della serie 23 e di tre in quelli delle serie 22.
Dopo studi teorici e simulazioni questa esecuzione è stata provata per un anno. Il test finale di validazione è durato 1.000 ore. Tipi SKF di varie dimensioni a rulli cilindrici con elevata capacità di carico stanno funzionando con successo da anni nelle turbine eoliche. Varie indagini ne hanno dimostrato le prestazioni superiori in queste applicazioni.
Infine, per soddisfare le esigenze crescenti di un sempre minore attrito per ridurre i consumi, nel 2007 la SKF ha introdotto i cuscinetti ad alta efficienza energetica. Il primi cuscinetti a rulli cilindrici di questo tipo (E2, fig. 10) sono di medie dimensioni e appartengono alla serie NJ. Rispetto ai cuscinetti standard SKF, i nuovi cuscinetti a rulli cilindrici SKF E2 presentano una riduzione dell’attrito che può arrivare all’85% nelle applicazioni caricate assialmente (fig. 11) e una più elevata capacità di carico dinamico grazie al mantenimento delle caratteristiche SKF Explorer. Questi cuscinetti a bassissimo attrito servono per un’ampia gamma di applicazioni, ma soprattutto per gli organi di trasmissione industriali e dell’industria eolica.
La caratteristica più importante è dunque il minore attrito, che porta con sé minori temperature di lavoro, migliori condizioni di lubrificazione e maggiore capacità di carico assiale. Tutto ciò va di pari passo con i minori consumi di energia, i maggiori rendimenti, i minori costi, le minori emissioni e le maggiori velocità ammissibili (siamo sul +10 % rispetto agli standard). Questa recente evoluzione dei cuscinetti a rulli cilindrici offre maggiori durate di esercizio e maggiore affidabilità. Essa appartiene alla lunga tradizione dei cuscinetti SKF che sono sempre stati in grado di soddisfare le esigenze del mondo contemporaneo.