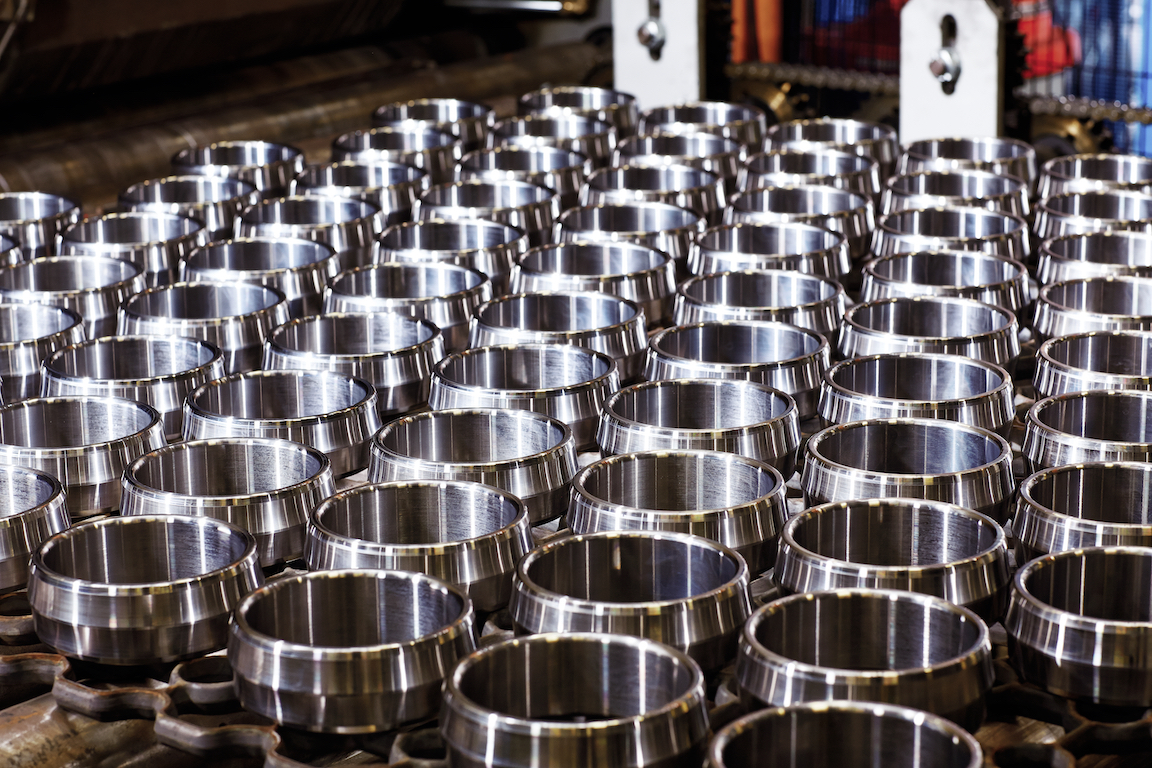
Il tocco finale
Una tecnologia innovativa dà ai pavimenti industriali migliore qualità e maggiore durata.
Da quando l’HTC Floor Systems li utilizza per rimuovere le imperfezioni e le impurità, i diamanti sono diventati i migliori amici dei pavimenti. Nella sua sede di Söderköping, in Svezia, la società HTC ha creato una vasta gamma di macchine e utensili diamantati per il trattamento di diverse tipologie di pavimenti.
I prodotti sono commercializzati tramite le società consociate in Francia, Germania, Regno Unito, Stati Uniti e i concessionari presenti in circa 60 paesi.
Tutto ebbe inizio nel 1987, quando un uomo di nome Håkan Thysell decise di lasciare l’impresa di pulizie presso cui lavorava. Insoddisfatto dei macchinari e dei metodi impiegati per pulire e rinnovare i pavimenti in pietra naturale, Thysell voleva trovare qualcosa di meglio. Fondò una nuova società che chiamò HTC, acronimo di Håkan Thysell Company, e cominciò a sperimentare.
Thysell voleva sviluppare una macchina potente, capace di molare velocemente vaste superfici. Chiese aiuto al fratello ingegnere, che mise a disposizione il garage dove i due elaborarono la prima macchina. Come racconta il figlio di Håkan Thysell, Karl, direttore Marketing, la macchina aveva qualche problema. “Era molto grande, misurava 80 centimetri di larghezza contro i 50 abituali. Quando fu il momento di collaudarla, cominciò a ruotare su se stessa come un frisbee e un dipendente la mandò a sbattere contro il muro”.
Nel 1991, tuttavia, il problema “ frisbee” venne risolto. Nacque così la DiaNova, oggi ribattezzata HTC 800 Classic. Collaudata e messa a confronto con macchine di altri produttori, l’HTC 800 era risultata quasi sempre la migliore, portando da 30 a 200 metri quadrati al giorno la capacità di trattamento di superfici in pietra naturale.
Un costruttore svedese che lesse della nuova macchina su un giornale locale contattò l’HTC per sapere se questa fosse idonea anche per il trattamento di pavimenti in calcestruzzo. “L’abbiamo provata e ha funzionato!”, dice Karl Thysell. “Inaspettatamente, oltre ai pavimenti di marmo e altre pietre naturali, l’HTC cominciò a trattare anche quelli in calcestruzzo”.
L’HTC aveva messo a punto un metodo per rendere lucido anche il più opaco dei pavimenti in calcestruzzo e, ben presto, trovò anche il modo per eliminare l’acqua dal processo, rendendolo più pulito e più ecocompatibile.
Rispetto ad altri metodi, il processo di molatura della HTC oltre a generare meno rumore e meno polvere, non prevede l’impiego di sostanze chimiche. Il consumo energetico orario è pari a 1,7 kilowatt per metro quadrato, ben inferiore ai 50 kilowatt di altri metodi. Thysell sottolinea che le tecniche di molatura e lucidatura messe a punto dall’azienda riducono fino a 190 volte le emissioni di CO2.
Operare in un ambiente di lavoro pulito e luminoso è sempre più importante affinché le persone lavorino volentieri. “Le aree di produzione sono diventate belle come uffici. Le persone che ci lavorano sono più a loro agio e dimostrano più cura. È un grosso cambiamento per gli ambienti industriali. Il calcestruzzo lucido fa tendenza, e non avremmo mai immaginato quanto”, commenta Thysell.
Oltre alla facilità di manutenzione, i pavimenti in calcestruzzo molati e lucidati offrono altri vantaggi. Dopo il trattamento, un cliente aveva riscontrato meno problemi con l’elettronica dei carrelli elevatori a forche. Daniel Gustafsson, che lavora nel settore R&S dell’HTC, racconta: “L’elettricità statica era stata diminuita. Inoltre i carrelli elevatori erano meno rumorosi e producevano minori vibrazioni perché la nostra macchina aveva rimosso le irregolarità e i dislivelli del pavimento. Per giunta, una pavimentazione altamente riflettente aumenta di molto la luminosità, riducendo i costi di illuminazione e il consumo di energia elettrica”.
Il reparto R&S dell’azienda è formato da dieci persone, che hanno da poco sviluppato la molatrice più grande del mondo – larga 2,5 metri – per lucidare i pavimenti in modo più economico e più veloce. Le ambizioni dell’HTC non si fermano qui. L’azienda infatti collabora con l’istituto svedese di ricerca sul traffico per collaudare nuove macchine per la manutenzione di strade e ponti.
“Abbiamo creato un mercato che non esisteva e ne siamo diventati i leader”, puntualizza Thysell, accennando alle centinaia di brevetti dell’azienda. “Noi ci definiamo ‘gli innovatori’, mentre alcuni dei nostri concorrenti si dicono orgogliosi di essere i nostri ‘imitatori’ ”.
Durata ed efficienza
Cliente da oltre quindici anni, l’HTC utilizza per le sue molatrici le unità mozzo, i cuscinetti e le tenute della SKF. La molatura di superfici particolarmente dure comporta forti sollecitazioni con conseguente usura dei componenti delle macchine, oltre a generare polvere e impurità che danneggiano l’attrezzatura.
L’HTC desiderava un soluzione che offrisse durate maggiori rispetto ai cuscinetti tradizionali (circa 300 ore). I cuscinetti in ceramica presentano caratteristiche migliori ma hanno un costo più elevato, perciò la SKF optò per un’altra soluzione. “Le unità mozzo ruota che utilizzavamo nelle applicazioni automobilistiche si erano rivelate efficaci anche nelle applicazioni di macchine agricole che usuravano i cuscinetti tradizionali”, dice Johan Fritzon, key account manager, SKF Industrial Market – Regional Sales and Service. “Quindi decidemmo di provarle sulle macchine dell’HTC”.
L’esperimento funzionò. Con le unità mozzo SKF, l’HTC era riuscita ad aumentare significativamente la durata del macchinario, da 300 a 7.000 ore in un caso, e fino a 100.000 ore in un altro. Essendo cuscinetti prodotti in grandi quantità per l’industria automobilistica, l’HTC ebbe anche un vantaggio in termini di costi.
“Eravamo soliti costruire le nostre macchine partendo dal motore”, commenta Daniel Gustafsson, R&S dell’HTC. “Ma le unità mozzo della SKF ci hanno permesso di procedere in senso inverso, partendo dal basso. Si è trattato di un miglioramento notevole”.
Attualmente sono due le unità mozzo SKF impiegate dall’HTC, in funzione della dimensione delle macchine. L’unità più grande ha una durata di 6.000 ore, mentre quella più piccola supera le 100.000 ore. “Le unità mozzo ruota SKF durano più a lungo delle nostre macchine”, osserva Karl Thysell, direttore marketing dell’HTC.