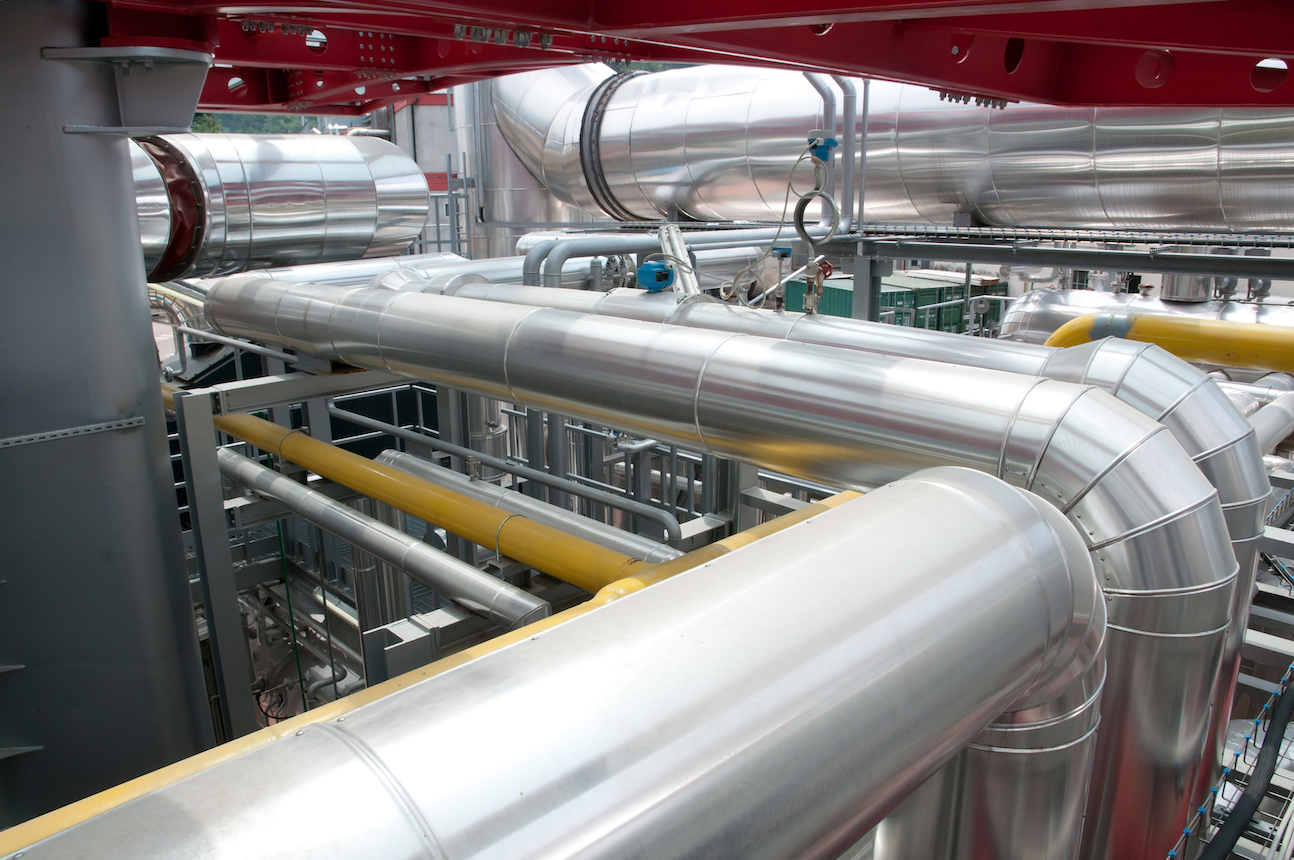
Rulli di appoggio
Per sostituire i rulli di appoggio del forno rotativo, la società mineraria Argex si è rivolta alla SKF, che da anni è suo fornitore.
Fatti
Fatti SKF
Ogni rullo di appoggio fornito dalla SKF comprende:
- 1 albero in acciaio di alta qualità
- 1 rullo temprato di appoggio vero e proprio, avente diametro esterno di 1.500 mm
- 2 cuscinetti orientabili a rulli di grandi dimensioni – diametro foro 500 mm
- 2 sopporti in due metà
- 1 sopporto su misura
- 1 sistema di lubrificazione centralizzata
In Belgio, nella verde regione delle Fiandre, ad appena 10 chilometri a sud di Anversa, ha sede lo stabilimento della Argex, che sorge sulle rive del fiume Schelda. Dal lato opposto, nel 1965 aprì i battenti un cementificio che sperimentò la produzione di argilla espansa utilizzando quella estratta nella vicina cava. Il cementificio oggi è chiuso, ma la Argex, fondata anch’essa nel 1965, estrae ogni giorno quasi 1.000 tonnellate di argilla e il suo impianto ha una capacità produttiva annua di 500.000 metri cubi di granuli di argilla espansa.
“I granuli di argilla espansa della Argex sono aggregati leggeri multiuso per l’edilizia, che trovano impiego in svariate applicazioni”, dice Johny Bultheel, responsabile dello stabilimento della Argex. “Sono utilizzati come materiale di riporto in progetti di ingegneria civile quali strade, blocchi in calcestruzzo, ferrovie, idrovie, e si rivelano idonei anche per realizzare campi sportivi, terrazzamenti di giardini, pavimenti isolanti e prodotti industriali”.
Argex è un’azienda business-to-business, la cui produzione è destinata per il 95 percento all’industria edile e per il restante 5 percento ai settori della costruzione di giardini e della coltivazione idroponica. Quasi il 50 percento della produzione totale è esportato nei paesi confinanti e in alcuni paesi extraeuropei.
L’argilla grezza proviene dalla vicina cava. “Ogni giorno ne vengono estratte circa 1.000 tonnellate, ma la cava può durare ancora per altri 25 anni, quindi non pensiamo di poterlo farlo ancora a lungo”, dice Bultheel. Nella fase di preparazione l’argilla viene additivata con ossido di ferro e talvolta acqua per ottenere la densità desiderata. Prima di essere inviata all’impianto di cottura, viene sottoposta a estrusione e frantumazione.
Il forno rotativo in due parti, che consiste in un tubo lungo 76 metri, funzionante giorno e notte, cuoce circa 50 tonnellate di granuli all’ora e ha una capacità produttiva giornaliera di 1.800 metri cubi. È il più grande nel suo genere in Europa e il suo profilo si staglia contro il piatto orizzonte. Riscaldato mediante lignite, il forno è fatto funzionare per due o tre mesi consecutivi e poi viene sottoposto agli interventi di manutenzione, che durano da due a quattro settimane.
Inizialmente i granuli giungono nella prima parte del forno, l’essiccatore, che ruota alla velocità di 1 giro/min, dove rimangono per circa 2,5 ore a una temperatura compresa tra 300 e 800 °C. Successivamente vengono trasportati nella seconda parte, l’espansore, che ruota a 5,2 giri/min e dove rimangono per 30 minuti alla temperatura di 1.100 °C che ne provoca l’espansione. L’argilla così espansa viene convogliata in un raffreddatore fluidizzato, dove viene raffreddata mediante aria a una temperatura compresa tra 80 e 100 °C.
Il processo di essiccazione produce granuli di dimensioni diverse, che vanno da 1 a 25 millimetri di diametro, ciascuna delle quali prevede un impiego specifico. Dopo la suddivisione granulometrica, le diverse granulometrie sono inviate ai sili di stoccaggio.
Il forno è sostenuto da otto rulli di appoggio o di supporto, ciascuno dei quali contiene due cuscinetti, che tradizionalmente sono boccole o cuscinetti radenti. Tre anni fa, però, la Argex optò per un cambiamento, a cominciare dalla prima serie di rulli.
“Siamo stati spinti in primo luogo dall’inaffidabilità dei cuscinetti radenti, che mette a repentaglio la sicurezza”, spiega Bultheel. “Dopo la sostituzione di un rullo di appoggio è necessario eseguire l’allineamento dei cuscinetti in modo assolutamente perfetto, prima di riavviare il forno. Altrimenti c’è il rischio che i cuscinetti surriscaldino il lubrificante e che questo prenda fuoco”. Nella storia recente della Argex è capitato due volte che i rulli s’incendiassero a causa del disallineamento delle boccole. A volte il surriscaldamento avviene subito, ma può succedere che ci voglia una settimana prima di rilevare il problema. A quel punto è necessario fermare la produzione per apportare le dovute correzioni. Non ultimo, la perizia indispensabile per allineare i cuscinetti radenti più datati è andata perdendosi dato il ricambio generazionale dei lavoratori.
“Un altro motivo che ci ha indotti a passare ai cuscinetti volventi è il consumo energetico, a cui abbiamo sempre prestato attenzione. Volevamo una soluzione più moderna, che offrisse una lubrificazione migliore, e quindi un minore attrito, in grado di aiutarci a ridurre i costi”.
Per questo la Argex si è rivolta alla SKF. Per Bultheel, “la SKF ci è sembrata la scelta più ovvia, in parte perché eravamo già loro clienti, ma soprattutto perché sono i migliori: non avevamo bisogno di cercare nessun altro”.
Cominciato nel 2008 sotto la supervisione di George Cant del settore manutenzione, il progetto ha necessitato di tempo poiché alla SKF fu chiesto di fornire oltre ai cuscinetti anche i rulli stessi di appoggio, il relativo albero, i sopporti e le piastre di base, che dovevano avere le stesse dimensioni complessive della soluzione precedente per facilitare l’installazione e contenere i costi. I nuovi rulli di appoggio, ciascuno del peso di circa 23 tonnellate ed equipaggiato con un sistema di lubrificazione automatica SKF, sono stati installati nell’agosto 2010.
“I nuovi rulli di appoggio funzionano perfettamente e tutto fila liscio da quando li abbiamo installati. Avevamo chiesto alla SKF una soluzione più semplice e più affidabile e abbiamo ottenuto un sistema che ci permette anche di ridurre i consumi di energia fino al 10 percento. Considerato l’investimento fatto, ci auguriamo che i rulli di appoggio durino il più a lungo possibile”, auspica Bultheel. La Argex sta valutando di sostituire anche la seconda serie di rulli di appoggio del forno rotativo e spera di raggiungere molto presto un accordo con la SKF.
ARGEX
- Fondata nel 1965 84 dipendenti
- Processo continuo (24 ore su 24, 7 giorni su 7)
- Capacità produttiva: 500.000 m³/anno
- Produzione giornaliera 1.800/m³ di granuli
- Estrazione giornaliera di argilla 1.000 tonnellate
Il prodotto
I granuli di argilla Argex sono:
- ecologici, 100 percento argilla
- leggeri, densità compresa tra 320 e 750 kg/m³
- isolanti (termicamente e acusticamente) inerti, chimicamente neutri, capaci di reggere carichi elevati, non infiammabili, insensibili sia al calore sia al gelo, molto drenanti
Argex in cifre
tonnellate di granuli/ora 50
Lunghezza del forno in metri 76
tonnellate di argilla/giorno 1.000
m3 di granuli/giorno 1.800
temperatura max nel forno (oC) 1.200