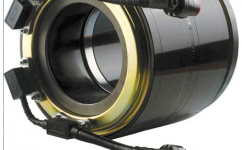
Soluzioni per il monitoraggiodei carrelli ferroviari
Con il monitoraggio delle condizioni dei carrelli ferroviari è possibile migliorare l’affidabilità e la sicurezza, ridurre i costi di manutenzione, rilevare danneggiamenti incipienti e prevenire cedimenti meccanici.
Con il monitoraggio delle condizioni dei carrelli ferroviari è possibile migliorare l’affidabilità e la sicurezza, ridurre i costi di manutenzione, rilevare danneggiamenti incipienti e prevenire cedimenti meccanici.
L’industria ferroviaria è alla costante ricerca di metodi e tecnologie che consentano di ridurre in modo significativo i costi di esercizio (LCC, Life-Cycle Costs) e i costi complessivi di possesso (TCO, Total Cost of Ownership). Per più di 150 anni – prima dell’introduzione dei concetti di LCC e TCO – per cercare di calcolare i costi dei veicoli ferroviari si è fatto ricorso a documentazioni frammentarie, riguardanti per esempio il costo di acquisto, il consumo di carbone per le locomotive a vapore, le ore-uomo in officina per una data percorrenza o i costi dei ricambi, spesso senza dare loro una configurazione razionale.
Sin dagli inizi, nella tecnologia ferroviaria si è sempre puntato sull’affidabilità e sulla sicurezza. Le tradizionali riparazioni sul posto sono state presto sostituite da programmi di manutenzione, basati sulla percorrenza e/o sul tempo. Talvolta ciò portava spesso a impostare intervalli di manutenzione troppo brevi, rinunciando a sfruttare le potenzialità residue del materiale rotabile in termini di percorrenza.
Tuttavia, in certe situazioni, intervalli brevi erano scelti di proposito – per esempio nel caso di veicoli impegnati in linee di montagna o su binari serviti da scarsa manutenzione, oppure nel caso di condizioni meteorologiche avverse o di possibile mancata notizia di deragliamenti negli scambi.
L’ESEMPIO DEGLI IMPIANTI EOLICI
C’è una sempre maggiore esigenza di affidabilità e sicurezza, che va di pari passo con quella della riduzione dei costi di manutenzione. Il monitoraggio delle condizioni è una tecnologia matura da cui l’industria ferroviaria non può che trarre grande beneficio. In altre industrie, come quella eolica, da anni i programmi di manutenzione si basano sui risultati del monitoraggio che consentono un approccio di tipo proattivo nel ridurre i costi di manutenzione.
I sistemi di monitoraggio online degli impianti eolici permettono di tenere sotto controllo sia le turbine e i sistemi d’ingranaggi singoli sia un’intera centrale, per prevedere quando la manutenzione è necessaria. Il sistema SKF WindCon acquisisce, analizza e mette insieme i dati di tipo meccanico per consentire una panoramica affidabile delle prestazioni, nell’intento di identificare danneggiamenti incipienti e prevedere l’eventualità di guasti futuri prima che si verifichino. Con tali informazioni è possibile pianificare in modo più efficace gli interventi di manutenzione ed estendere gli intervalli tra le costose ispezioni, specie nei siti offshore.
I dati sono presentati utilizzando un browser Internet e si ottengono informazioni pressoché istantanee. La versione web trae vantaggio dall’archivio di dati SKF WebCon e dai servizi del web stesso. Con questo strumento si può abbreviare l’intervallo fra il momento in cui scatta l’allarme e la soluzione del problema, dato che gli addetti possono fare il monitoraggio da qualsiasi luogo usando un PC o uno strumento portatile che abbiano l’accesso a Internet. La manutenzione semplificata e la maggiore affidabilità assicurate da SKF WindCon trovano un utile complemento nel sistema WindLub, relativo alla lubrificazione automatica centralizzata per le turbine eoliche.
Detto sistema si integra facilmente con SKF WindCon, fornendo agli operatori una panoramica completa del sistema di lubrificazione, oltre a quella dello stato delle pompe e del livello del lubrificante. Un gruppo di tecnici SKF si dedica esclusivamente agli aspetti del monitoraggio delle condizioni delle turbine eoliche e alla gestione delle centrali in attività. SKF WindCon è approvato da Allianz e certificato dal Germanischer Lloyd. Nell’industria eolica le principali compagnie di assicurazione richiedono espressamente il monitoraggio delle condizioni.
MONITORAGGIO DELLE CONDIZIONI IN FERROVIA
Per quanto riguarda le esigenze di affidabilità e manutenzione, tra le turbine eoliche e i veicoli ferroviari esistono analogie di base, ma anche profonde differenze. Le turbine sono ferme, mentre i treni no e operano in aree molto vaste, spesso estese a più paesi.
Ne derivano non solo situazioni geografiche diverse, ma anche esigenze tecniche diverse. Anche le norme e regolamenti possono essere molto diversi. La durata media prevista del materiale rotabile è molto maggiore di quella di una turbina, il che pone la soglia d’ingresso della nuova tecnologia nell’industria ferroviaria su livelli più elevati e impegnativi e comporta tempi più lunghi, specialmente se si vogliono ottenere miglioramenti significativi in termini di affidabilità, sicurezza e costi d’esercizio.
Il monitoraggio delle condizioni dei carrelli prevede l’uso di sensori per il rilevamento delle instabilità di funzionamento secondo i requisiti della Direttiva 96/48 EC della specifica europea TSI (Technical Specification for Interoperability), la quale stabilisce che il monitoraggio dell’instabilità sia continuo o almeno eseguito ad una frequenza che consenta un rilevamento affidabile e tempestivo del danneggiamento. Per i treni di Classe 1 il sistema deve essere anche collegato a un registratore diagnostico di dati installato a bordo per la tracciabilità.
Il monitoraggio delle ruote viene eseguito da un sensore di vibrazioni montato sul corpo boccola o integrato nel relativo cuscinetto per fornire informazioni utilizzabili a determinare le condizioni della ruota, quali appiattimenti o difetti di forma. Il calcolo in tempo reale utilizza anche le informazioni sulla velocità degli alberi. La manutenzione delle ruote è molto lunga e costosa. Con la manutenzione basata sulle condizioni la tempistica di tali operazioni può essere programmata ottimizzando la percorrenza del gruppo ruote senza compromettere affidabilità e sicurezza.
Da decenni i cuscinetti delle boccole ferroviarie sono monitorati per mezzo di sistemi statici di controllo della temperatura e della rumorosità montati sui binari. Normalmente tali sistemi sono installati a una certa distanza tra di loro in punti strategici, quali le salite nei tratti alpini, e forniscono indicazioni su fenomeni di forte usura o danneggiamento di componenti. In tali casi il treno viene fermato e il vagone difettoso sostituito e inviato presso l’officina di riparazioni più vicina, con conseguenti ritardi e costi aggiuntivi.
FREQUENZE DINAMICHE
Il sistema SKF IMx-R di controllo delle boccole installato a bordo può far parte del sistema di monitoraggio dei carrelli o può essere autonomo e soddisfa i requisiti della specifica TSI, la quale impone che le apparecchiature siano in grado di rilevare un deterioramento delle condizioni del cuscinetto di una boccola misurandone la temperatura e/o le frequenze dinamiche. L’ esigenza di un intervento di manutenzione è calcolata dal sistema, il quale, quando occorre, indica la necessità di modificare l’operatività in funzione dell’entità del danneggiamento. Il sistema di rilevamento opera in modo del tutto indipendente a bordo del treno,
inviando messaggi diagnostici al guidatore.
Sia i rulli e le piste dell’anello interno del cuscinetto di una boccola, sia le ruote dentate generano frequenze dinamiche caratteristiche, che possono essere rilevate e analizzate a patto di conoscere alcuni dati della geometria e la velocità dell’albero. Anche anomalie come le piccole erosioni di fatica possono essere scoperte assai tempestivamente tramite l’analisi degli spettri delle frequenze che sono stati generati.
Anche i componenti dei motori di trazione e dei riduttori, quali i cuscinetti e le ruote dentate, come pure gli alberi e i giunti, possono essere monitorati utilizzando i sensori di vibrazione facenti parte del sistema di controllo dei carrelli. Il controllo del livello e della temperatura dell’olio dei riduttori può essere incluso in tale sistema oppure essere autonomo. I diagrammi di vibrazione provenienti dai componenti della propulsione variano a seconda dell’effettivo sforzo di trazione applicato. Di conseguenza nell’elaborazione dei dati bisogna prendere in considerazione la velocità e i carichi del treno, unitamente a taluni parametri geometrici e al rapporto di trasmissione degli ingranaggi.
STATO DEI BINARI CON UN GPS
Mettendo insieme le informazioni sulle vibrazioni delle boccole e quelle ottenute da un GPS (Global Positioning System) è più facile definire in modo sufficientemente preciso lo stato di deterioramento nel tempo dei binari, visto dal gruppo ruote. Il sistema può incorporare qualunque tipo di sensore, ma soprattutto si usano quelli di vibrazione.
Inoltre il sistema acquisisce, analizza e archivia una serie di dati operativi, fornendo una panoramica attendibile dei danneggiamenti incipienti e prevedendo quando questi potrebbero tradursi in guasti gravi. In tal modo gli operatori possono impostare razionalmente le attività di manutenzione ed eseguire le necessarie ispezioni e riparazioni nel corso delle soste programmate. Si ha anche la possibilità di prolungare gli intervalli di manutenzione e ridurre i fermi macchina imprevisti con i relativi costi. I dati acquisiti permettono di eseguire l’analisi delle cause dei guasti, fornendo gli elementi per una modifica dei progetti originari al fine di migliorare il macchinario.
Con le informazioni sul veicolo disponibili a bordo e tutta una serie di sensori per monitorare i parametri operativi, si possono ridurre i costi di manutenzione e incrementare in modo significativo l’affidabilità e la sicurezza. Il sistema si può installare sui veicoli nuovi o su quelli da ammodernare. La SKF ha eseguito numerose prove in Europa e Asia su diversi tipi di treni, compresi quelli ad alta velocità. L’esperienza acquisita finora soddisfa le attese sia dei costruttori sia degli operatori.
SKFAxletronic è un marchio registrato del Gruppo SKF.