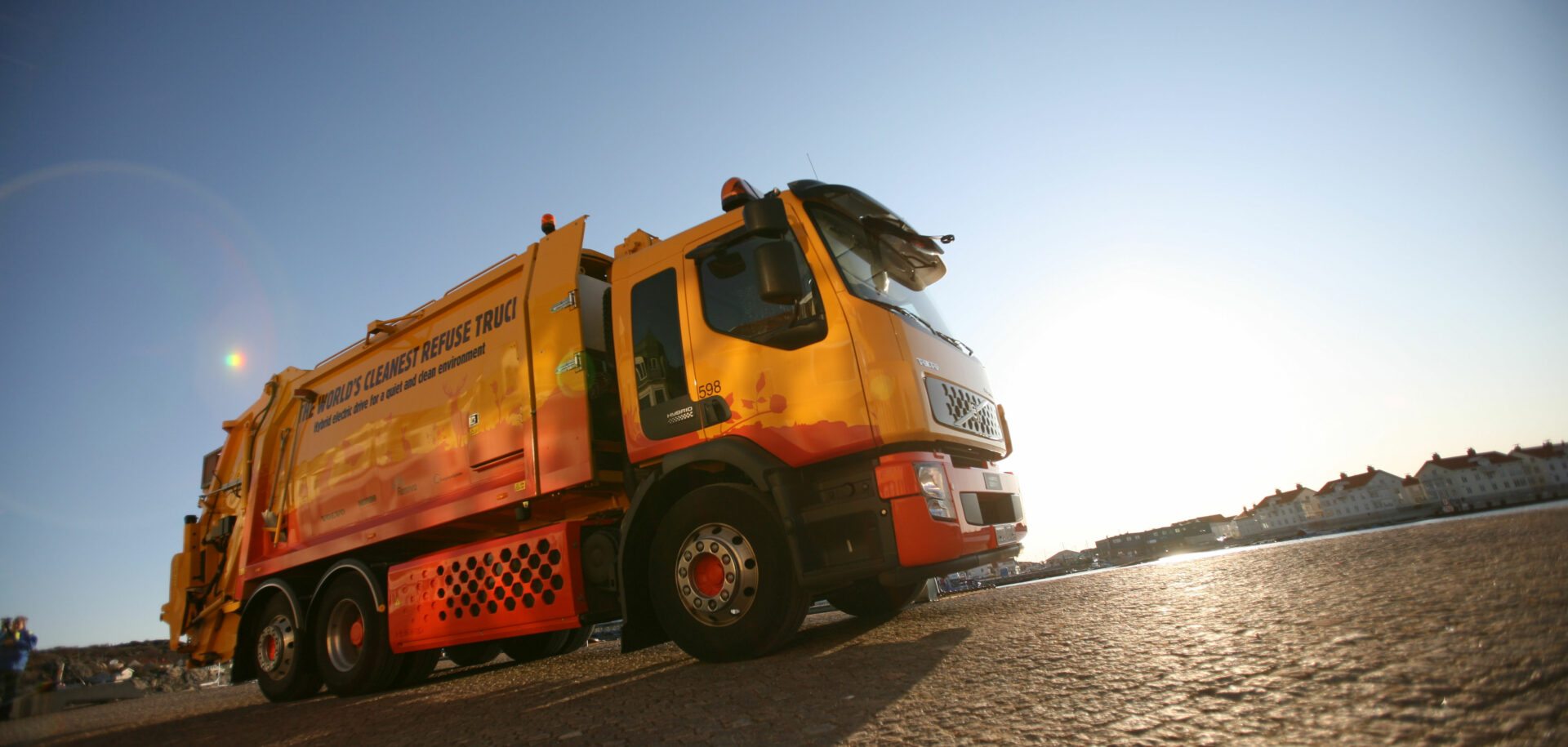
Making the most of waste
It’s amazing what can be achieved with waste. Thanks to advances in technology, Renova is transforming waste into valuable energy.
Every year, the Renova waste-to-energy plant in western Sweden provides about a third of the district heating for the Gothenburg region. It also supplies 5 percent of the electricity needs of Gothenburg, Sweden’s second-largest city. That’s not bad considering it’s all generated from waste that can’t be recycled.
Today we have increased operational reliability.
Göran Klamas
Renova plant manager
The waste is incinerated in three giant furnaces. Each furnace includes primary fans, which oxygenate the fires at an even 1,000 degrees Celsius. Secondary fans circulate the air within the fire chamber, and recirculation fans dry the waste.
These fans are critical for the plant’s operations. If a single fan stops circulating, it can cost the plant 100,000 euros. Ensuring the reliability of this rotating equipment has been crucial for the plant; to that end, Renova and SKF have been working together for the past 10 years to ensure that there are no unplanned maintenance stops.
Proactive Reliability Maintenance
“In the past we could lose about 1,000 hours a year in production due to urgent maintenance measures,” says Göran Klamas, Renova’s plant manager, business area recycling. “Today, we have increased operational reliability, and we stop for planned service. This has significantly increased productivity.”
This success can be largely attributed to the collaboration between Renova and SKF. At the heart of this collaboration is SKF’s Proactive Reliability Maintenance (PRM), which has significantly improved operational stability in the plant’s rotating equipment. (See sidebar.)
Through PRM, SKF has identified and classified close to 40 critical Renova machines and can provide quick overviews in the form of reports and other visual displays, indicating where extra maintenance measures are required. The measurements provide the maintenance department with a clear picture of possible upcoming problems in equipment so they can take corrective action before an emergency situation occurs.
“It may be a misalignment that is repeatedly addressed on a machine, but the error persists anyway,” says Jennie Lindahl, service coordin-ator at SKF, who has been carrying out measurements at the plant for many years. “By conducting an ODS [operating deflection shape] measurement, we can identify the cause, which could be for example an unevenness in the ground that requires correction.”
Lubricant analyses, which are conducted mainly because of strict environmental demands, can also be helpful for identifying operational issues.
“Lubricant analysis can identify entirely different causes of downtime than what was previously thought to be the cause,” says Lindahl. “It could be improper lubrication, water indicators or bearing temperatures that are too high, which can increase the risk of dangerous chemical substances forming. The grease can oxidize, the viscosity can change and acid can be formed that damages the bearing surfaces.” Essentially, such analyses can help avoid a possible disaster.
Fortunately, such acute maintenance issues can be avoided through the PRM activities. In 2016 the Renova facility experienced not a single emergency stop, compared with five emergency stops 10 years ago. With the PRM contract in place, just two planned maintenance actions were carried out in 2016, half as many as a decade ago.
The improvements in operational reliability have resulted in lower maintenance costs for Renova, freeing up resources for other investments. “The daily energy loss [from unplanned stops] cost about 100,000 euros,” Klamas says. “Today the fans are stable so we can spend more time looking into how we can have even more efficient and environmentally friendly combustion.”