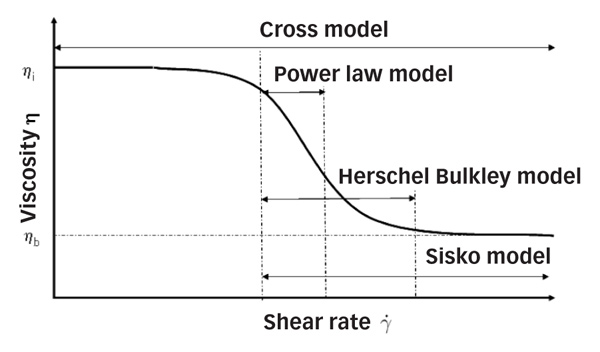
Механизмы смазывания пластичной смазкой подшипников качения
Смазывание пластичной смазкой имеет ряд явных преимуществ по сравнению со смазыванием маслом – утечка такой смазки происходит реже, она обладает уплотняющими свойствами и защищает поверхности подшипников от коррозии. Основными недостатками пластичной смазки являются ограниченный срок службы и ограниченная охлаждающая способность. Помимо этого, в некоторых случаях возникает риск смазочного голодания, что приводит к уменьшению смазочной плёнки. Однако при выборе правильной смазки, уплотнительной и/или смазочной системы смазывание пластичной смазкой имеет очевидные преимущества. Эта статья основана на новой книге, написанной инженерами SKF [12]. Она содержит сводные данные о механизмах смазывания пластичной смазкой подшипников качения.
РЕЗЮМЕ
Смазывание пластичной смазкой имеет множество преимуществ по сравнению со смазыванием маслом, но выбор подходящей пластичной смазки — сложный процесс. Понимание механизмов смазывания позволяет выбрать подходящую пластичную смазку в правильном для конкретного применения количестве, чтобы обеспечить ожидаемый срок службы подшипника. Механизмы смазывания пластичной смазкой описаны инженерами SKF в новой книге, опубликованной в январе 2013 года в издательстве John Wiley & Sons Ltd. [12].
ССЫЛКИ НА ТУ ЖЕ ТЕМУ
Этапы смазывания пластичной смазкой
Смазывание пластичной смазкой – динамический процесс, который можно разделить на три основных этапа, как показано на рис. 1.
После первоначального заполнения или повторного смазывания пластичная смазка находится между роликами, что приводит к большим потерям на перемешивание при запуске или приработке. На этом этапе, также называемом этапом перемешивания, смазка выталкивается в свободный объём подшипника (на уплотнения или на заплечики колец) или останется прикреплённой к сепаратору. С этих участков смазка постепенно попадёт на дорожки качения за счёт маслоотделения или сдвига. На данном втором этапе маслоотделения смазочная плёнка будет формироваться в ходе процесса пополнения и расхода [20], во время которого на дорожки качения из резервуаров поступает смазка, но в то же время дорожки теряют смазку из-за бокового потока и окисления. Это может привести к смазочному голоданию, особенно в уплотнённых подшипниках, в которых резервуары пластичной смазки меньше. Ещё один механизм подачи смазки – периодическое пополнение в результате смягчения смазки возле контактных поверхностей из-за локального тепловыделения [14], которое, опять же, возникает при периодическом нарушении смазочной плёнки.
В определённый момент времени содержимое резервуаров может быть израсходовано или произойдёт ухудшение его свойств до такой степени, что дальнейшее пополнение будет невозможно. Если не пополнить резервуары, произойдёт значительное нарушение целостности смазочной плёнки, которое называется завершением срока службы смазки, при котором через некоторое время произойдёт повреждение и выход подшипника из строя.
Образование запаса пластичной смазки в резервуаре
Скорость образования запаса пластичной смазки в резервуаре зависит от характеристик текучести пластичной смазки, также называемых реологическими свойствами. От этих свойств также зависит износ смазки.
Пластичная смазка обладает упругой вязкостью. Это означает, что вязкость смазки зависит от сдвига и от скорости сдвига. На pис. 2 показано отношение вязкости к скорости сдвига в различных часто используемых моделях. На нём видно, что при низких скоростях сдвига вязкость очень большая. Это означает, что сопротивление потоку будет очень большим при отсутствии контакта со смазкой, например, когда она находится в свободном объёме. Это свойство также называется консистентностью. На этапе перемешивания смазка может стать менее пластичной. Это свойство называется механической стабильностью.
Вязкость пластичной смазки на очень низких скоростях сдвига настолько большая, что происходит только деформация ползучести, а смазка, очевидно, находится в твёрдом состоянии. Как показано на pис. 2, смазка проявляет признаки псевдопластичности, т.е. значительного уменьшения вязкости с увеличением усилия сдвига.
При очень больших скоростях сдвига вязкость смазки может приблизиться к вязкости базового масла. Такие большие скорости сдвига возникают в смазочных плёнках между телами и дорожками качения. Наряду с маслоотделением это является причиной того, что толщина смазочной плёнки в подшипниках с пластичной смазкой обычно рассчитывается по вязкости базового масла, ηмасл.
Реологические свойства пластичной смазки можно описать с помощью различных моделей, которые изображены на pис. 2.
Толщина смазочной плёнки
Известно, что в подшипник попадает как базовое масло, так и загуститель [2]. Толщина смазочной плёнки в подшипниках с пластичной смазкой определяется пограничными слоями, которые формирует загуститель hR, и гидродинамическим действием базового масла hEHL (EHL – упругогидродинамическая смазка) [4]. В последнем случае на основании ранее указанных причин также можно рассматривать базовое масло. Следовательно, толщина плёнки, hT, рассчитывается следующим образом:
hT = hR + hEHL (1)
Подшипники, смазываемые пластичной смазкой часто работают в условиях так называемого смазочного голодания, в которых имеются только очень тонкие слои масла, и толщина смазочной плёнки в основном зависит только от толщины этих слоёв (pис. 3). Изменение толщины этих слоёв рассчитывается как разность между скоростями потоков подачи (маслоотделение [3,21]) смазки на дорожки качения и потери смазки на них [20]. Потери масла на дорожке происходят из-за бокового потока, который возникает из-за высокого давления в местах контакта тел и дорожек качения [18]. Может происходить частичное восполнение смазки [6]. Однако, за исключением очень низких скоростей и базовых масел с малой вязкостью, оно происходит очень медленно [7]. Вероятно, большее воздействие окажет сдвиг и граничное трение из-за вращения тел качения [5]. Вращение тел качения и меньшие размеры участков соприкосновения облегчают процесс пополнения в шарикоподшипниках по сравнению с роликоподшипниками. Это одна из причин, по которым пластичная смазка для роликоподшипников должна отделяться более интенсивно, чем смазка для шарикоподшипников [11]. При более высоких температурах на толщину смазочной плёнки будут влиять окисление и испарение. Потеря материала будет происходить из-за окисления и испарения [19, 15]. Однако это также изменит вязкость и смазочные свойства.
Динамические свойства
В условиях смазочного голодания толщина смазочной плёнки уменьшается до тех пор, пока в подшипнике больше не будет достаточного количества смазки. Сухое трение металла по металлу приведёт к повреждению подшипника или может привести к тепловыделению, которое уменьшит вязкость смазки возле контактных поверхностей и приведёт к недостаточному пополнению, что, в свою очередь, станет причиной неисправности. В последнем случае толщина плёнки опять увеличится и смазывание будет происходить в достаточной степени до следующего происшествия. Это может произойти несколько раз в зависимости от способности смазки к восстановлению, которая зависит от способности смазки сохранять свою текучесть. На pис. 4 приведён пример температурного профиля цилиндрического роликоподшипника, работающего при температуре, обусловленной его работой [14].
Срок службы смазки и повторное смазывание
Срок службы смазки определяется моментом времени, в который смазка больше не способна смазывать подшипник. Этот момент может наступить через очень длительное время, поэтому при стендовых испытаниях подшипника его определить затруднительно. Чтобы ускорить проведение этого испытания, наружное кольцо испытываемого подшипника нагревается, что ускоряет процесс износа и уменьшает вязкость пластичной смазки. Пример такого испытательного стенда – устройство для определения срока службы пластичной смазки R0F+ [13].
Температурные условия
Пластичные смазки рассчитаны на работу в ограниченном диапазоне температур. Максимальная температура, называемая верхним температурным пределом (HTL), определяется по температуре каплепадения, при которой смазка необратимо теряет свою структуру. Эту температуру не следует превышать. Значение максимальной безопасной температуры ниже, оно называется верхним пределом рабочих температур (HTPL).
Нижний температурный предел (LTL) – минимальная температура, при которой пластичная смазка обеспечивает нормальную работу подшипника. Он обычно измеряется при проверке пускового крутящего момента. Следовательно, значение минимальной безопасной температуры выше, она называется нижним пределом рабочих температур (LTPL) [1]. При работе в диапазоне этих допустимых температур срок службы смазки является функцией от температуры. Как правило, срок службы смазки уменьшается в два раза при каждом увеличении температуры на 15 °C.
Моделирование срока службы смазки
Существует ряд моделей, которые можно использовать для расчёта срока службы смазки (или интервалов повторного смазывания). Все модели являются эмпирическими, они основаны на испытаниях на срок службы смазки. Срок службы смазки определяется как срок L10 – время, за которое 10 % большой выборки подшипников стали неисправными. Повторное смазывание нужно проводить до окончания срока службы смазки, чтобы не произошло повреждения подшипника. Модель повторного смазывания SKF основана на L01, времени, за которое только 1 % подшипников станет неисправным. При этом предполагается, что L10 = 2,7 L01. Повторное смазывание не является простой задачей. При слишком большом количестве пластичной смазки подшипник останется на этапе перемешивания с большими потерями на трение и высокими температурами. На pис. 5 показана зависимость срока службы смазки для закрытых шарикоподшипников в условиях малой нагрузки от частоты вращения, среднего диаметра подшипника, рабочей температуры и типа смазки (фактор результативности смазки). Влияние нагрузки можно учесть посредством поправочных коэффициентов. Модели для других типов подшипников основаны на этой модели с применением других поправочных коэффициентов. Они приведены в каталоге подшипников качения SKF [1].
Старение
В процессе трения и окисления механические и химические свойства пластичной смазки изменяются. Тип окисления зависит от условий работы – физическое старение преобладает при меньших температурах и высоких скоростях, а химическое старение преобладает при высоких температурах [5]. Физическое старение приводит к изменению реологических свойств, и, в результате, к утечкам, ухудшению характеристик маслоотделения и ухудшению способности пополнения смазки в зоне контакта. Химическое старение в основном является результатом окисления. Антиоксиданты замедляют этот процесс, но когда они заканчиваются, окисление приводит к потере смазочного материала в результате превращения в летучие продукты и лак, который не может смазывать подшипник [9].
Механизмы смазывания уплотнений пластичной смазкой
Основные различия при смазывании уплотнений пластичной смазкой и маслом связаны с нехваткой (пополнением смазки на кромке уплотнения) и образованием граничной плёнки из загустителя. Пополнение смазки на точке контакта происходит за счёт сдвига и отделения масла из пластичной смазки. Уплотняющие свойства пластичной смазки обусловлены её густотой, что означает, что пластичная смазка будет стойко держаться на уплотнении. Кроме того, пластичная смазка формирует карманы в многокромочных уплотнениях, в которых поток частиц загрязняющих веществ будет очень медленным. При разности давлений на уплотнении перетечёт только часть пластичной смазки, вызвав перемещение частиц загрязняющих веществ.
Системы смазывания
В тех ситуациях, когда пластичная смазка не может обеспечить достаточный срок службы подшипника в случае попадания загрязняющих частиц или воды, повторное смазывание можно обеспечить посредством систем смазывания. Эти системы состоят из насосов, трубопроводов, клапанов, распределителей и контроллеров. Пластичная смазка с оптимальными для подшипника свойствами часто может отличаться от той, которую эффективно может перекачивать система смазывания. Система смазывания должна быть рассчитана на перекачку оптимальной для подшипника пластичной смазки.
Конструкция определяется характеристиками текучести пластичной смазки, также называемыми прокачиваемостью. SKF разработала программу испытаний на прокачиваемость пластичной смазки, в которой учтены различные аспекты, перечисленные ниже (метод испытаний SKF приведён в скобках):
1. Перекачка
(a) Сопротивление потоку (FTG5 и Lincoln Ventmeter)
(б) Сжимаемость (FTG1)
(в) Сброс давления (FTG3 и Lincoln Ventmeter)
2. Текучесть
(a) Давление потока
(б) Пенетрация без перемешивания
(в) Индекс производительности насоса (FTG4)
(г) Работа насоса
3. Маслоотделение (и затвердевание):
Затвердевание пластичной смазки под давлением (FTG2)
Мониторинг состояния
Обычно для определения состояния подшипника (смазки) в режиме реального времени измеряются уровни вибрации. Однако всё большее распространение получают акустико-эмиссионные методы [16]. Для определения состояния пластичной смазки в автономном режиме используются методы измерения маслоотделения, содержания масла, консистенции, загрязнения частицами и окисления (инфракрасная спектроскопия с преобразованием Фурье). Существуют способы определения остаточного срока службы пластичной смазки на основе результатов, полученных с помощью указанных методов [10].
Заключение
За последние несколько десятилетий уровень знаний SKF о пластичных смазках значительно увеличился. Сегодня с высокой степенью уверенности можно предсказать срок службы пластичной смазки и контролировать оставшийся срок службы. Уплотнение продлевает срок службы подшипника в условиях загрязнённости, при этом пластичная смазка обеспечивает дополнительный уплотнительный эффект. Системы смазывания можно использовать для периодического заполнения подшипника свежей пластичной смазкой.