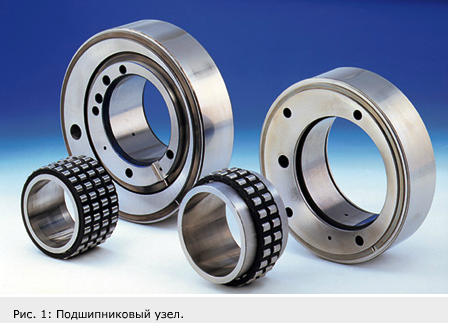
СИСТЕМЫ СМАЗЫВАНИЯ В ПЕЧАТНЫХ МАШИНАХ
Специализированные решения, позволяющие увеличить интервалы смазывания подшипников печатных машин, имеют хорошие перспективы.
РЕЗЮМЕ
Герметически закрытый корпус подшипникового узла печатного цилиндра состоит из подшипника, уплотнения и смазки. Еще несколько лет назад ожидать, что срок службы пластичной смазки может превышать пять лет, казалось нереальным. В результате прогресса, достигнутого в последние годы в области разработки подшипников для печатных машин, срок службы смазки был существенно увеличен. Результаты исследований, расчетов и испытаний показывают, что в будущем могут быть разработаны еще более совершенные решения. Дальнейшая разработка централизованных систем смазки может также способствовать снижению затрат и повышению качества услуг, предоставляемых клиентам.
СИСТЕМЫ СМАЗКИ СЕГОДНЯ
Повторное смазывание подшипников печатных машин
В настоящее время установленные в печатных машинах подшипники главного цилиндра смазываются маслом, пластичной смазкой (далее смазка) или один маслом, а другой – смазкой. Смазка должна также предотвращать проникновение загрязняющих веществ, включая моющие или чистящие растворы, которые могут вызвать вымывание смазки.
В принципе, точный расчет интервалов смазывания отдельного подшипника невозможен, т. к. срок службы смазочных масел подчиняется законам статистики.
В действительности интервал повторного смазывания во многом зависит от условий применения и в среднем составляет 6 месяцев.
Один из надежных методов расчета описан в Общем каталоге SKF, где интервал повторного смазывания рассчитывается с запасом для условий применения высококачественной смазки с литиевым загустителем при рабочей температуре 70°C.
Интервал повторного смазывания указывает на момент, когда 99% подшипниковвсе еще получают достаточное смазывание, т. е. срок службы используемой смазки L1 еще не истек.
Повторное смазывание должно производиться в тот момент, когда смазывающий эффект используемой смазки еще достаточно надежен. Повторное смазывание производится вручную или с помощью лубрикаторов. В современных лубрикаторах смазка подается под давлением непосредственно в каналы смазки, вытесняя отработанную смазку, которая перемещается в специальные емкости. Требуемое количество смазки зависит от типа и размеров подшипника.
Как базовое масло, так и загуститель пластичной смазки подвержены процессу старения. При разрушении структуры мыла, базовое масло вытекает, и смазывание становится невозможным. Старое базовое масло уже неспособно формировать структуру масляной пленки. Оба этих явления оказывают негативное воздействие и приводят к повреждению подшипника.
Различные средства помогают в оценке состояния отработанных смазочных масел, а также позволяют идентифицировать и классифицировать их в зависимости от их состояния. Одним из стандартных типов анализа является инфракрасная спектрография.
Выбор присадок, добавляемых в смазочные масла, зависит от требуемых характеристик. Например, стойкость к окислению, защита от коррозии или износа. Эти присадки также подвержены процессу старения. Оценка их эффективности производится с помощью специальных тестов, позволяющих произвести количественный анализ эффективности антикоррозийной защиты подшипниковой стали (ISO 11007) и меди (DIN 51811/ASTM D130-04), а также проверить совместимость с полимерными материалами. Эти методы основаны на количественном анализе загрязнений и примесей. В конечном счете именно результаты этих тестов позволяют определить целесообразность дальнейшего использования пластичной смазки в подшипнике. На рис. 2 показан подшипниковый узел печатного цилиндра Printing Cylinder Bearing Unit после проверки на испытательном стенде. После этого испытания было проведено исследование состояния пластичной смазки.
СМАЗОЧНЫЕ СИСТЕМЫ ЗАВТРАШНЕГО ДНЯ
Система печатного цилиндра – смазывание на длительный срок
В зависимости от конкретной области применения или характера нагрузки можно произвести подробный прогнозный расчет применительно к широчайшему спектру специализированных системных решений, называемых системами печатного цилиндра Printing Cylinder System (PCS) (рис. 3 и 4). Прогнозный расчет срока службы смазки, используемой для этих PCS, показывает, что при оптимальных условиях работы можно добиться существенного увеличения интервалов повторного смазывания.
В особых случаях повторного смазывания подшипников вообще не требуется. В зависимости от размера подшипника и условий эксплуатации примерный срок службы смазки можно определить по графику 1.
Когда срок службы смазки (L10) не является критичным фактором, повторное смазывание не требуется. Иначе интервал повторного смазывания (L01) может быть определен по графику, используя приближение L01 = L10/2,7. Этот график действителен для некоторых типов смазок, используемых в условиях уплотненных и незагрязненных систем. На графике прослеживается влияние температуры подшипника на срок службы смазки и видны преимущества низкой рабочей температуры подшипника. Добиться понижения температуры подшипника можно применением правильного типа и количества смазки, которая, прежде всего, должна быть равномерно распределена в подшипнике. График 2 показывает стабильно низкую рабочую температуру 40°C (лишь на 20°C выше температуры окружающей среды) после сравнительно короткой обкатки подшипника. В неоптимальных условиях рабочая температура будет постоянно высокой и, следовательно, срок службы смазки будет меньше.
Должны быть предприняты меры по эффективному уплотнению подшипников, которые требуются, во-первых, для удержания смазки внутри подшипников и, во-вторых, для защиты от внешних загрязнений. Защита смазки, имеющей длительный срок службы, создает предпосылку к тому, чтобы еще на один шаг приблизиться к созданию системы долговременного смазывания на базе комплексного подхода к уплотнению и смазыванию подшипников.
Смазывание подшипниковых узлов переменного направления вращения (колебания) Oscillating Bearing Units (OBU)
Реализация комплексного подхода к уплотнению и смазыванию подшипников применительно к подшипниковым узлам качающегося привода (OBU) была аналогична системе печатного цилиндра Printing Cylinder System, равно как и объем проделанной работы. Наличие одновременных вращательных и качательных движений предъявляет особые требования к пластичной смазке и уплотнению системы.
Результатом этих исследований стало то, что возможность долговременного смазывания смазкой, как показано на графике 1, была подтверждена. Максимальный интервал первого повторного смазывания может составлять 5 лет с начала эксплуатации печатной машины. Этот срок ограничен, главным образом, старением смазки в смазочных каналах.
Второй и последующие интервалы повторного смазывания должны составлять 60% от промежутка времени между началом эксплуатации печатной машины и моментом первого повторного смазывания, но не более трех лет.
Заправка OBU (рис. 5) производится на заводе точно дозированным количеством требуемой смазки, которая вводится в строго определенные места подшипникового узла. Кроме того, монтаж этого узла производится в заводских условиях, где повышенная чистота уменьшает риск загрязнения.
Централизованная система смазки
Простые и экономичные централизованные системы смазки – это новая возможность ускорить появление машин, не требующих смазывания, повысить надежность и упростить техобслуживание печатных машин. Прекрасный тому пример – централизованная одноканальная система смазки (CLS) (см. рис. 6). Как и последовательное смазывание, одноканальное смазывание может использоваться практически во всех типах печатных машин. Области применения включают подшипники качения и контроллеры кривизны, которые, как правило, расположены на стороне оператора. В отличие от систем последовательного смазывания, системы одноканального смазывания могут быть выполнены в виде автономных модулей, устанавливаемых на печатных машинах, т. к. наличие главного распределительного канала не требуется. Их установка не требует сложного монтажа, что также означает отсутствие протяженной системы смазочных каналов.
Особым преимуществом этой системы является ее некритичность к многокомпонентным смазкам, которые нередко вытекают из систем последовательной смазки.
СИСТЕМЫ СМАЗКИ БУДУЩЕГО
Сплав опыта в области технологии подшипников, уплотнительных систем, смазочных материалов и систем смазывания открывает перспективы для дальнейшей разработки системного подхода к созданию машин, не требующих смазывания. Отличный пример – подшипниковый узел со встроенной системой смазывания (см. рис. 6).
Смазочный материал, оптимально соответствующий конкретным словиям применения, типоразмеру подшипника и типу смазывания, из смазочного картриджа непрерывно подается в точку смазывания.
Точно дозированная подача смазки в сочетании с большой емкостью контейнера для смазки обеспечивает смазывание в течение срока от трех до пяти лет в зависимости отконкретной области применения. Как только контейнер смазочного картриджа будет почти полностью пуст, он может быть легко заменен новым. Этот смазывающий картридж может быть установлен в любом месте и использован для смазывания любой точки подшипника. Подобная система уплотнения и смазывания подшипника, с одной стороны, облегчает сборку печатной машины заводом-производителем и, с другой – облегчает труд оператора за счет уменьшения объема техобслуживания.
Современные изделия, комплексные системы, системные решения, отвечающие конкретным нуждам потребителя, а также услуги, связанные с эксплуатацией подшипников качения, уплотнительных устройств, смазывающих систем, мехатронных изделий равно как услуги по сборке и доукомплектованию будут способствовать дальнейшему развитию печатной отрасли.