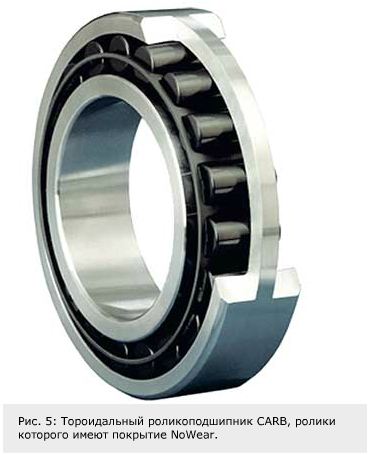
ТЕХНОЛОГИИ МОДИФИКАЦИИ ПОВЕРХНОСТИ ПОДШИПНИКОВ
К модификации поверхности подшипников прибегают, когда еобходимо улучшить электроизоляционные свойства, коррозионную стойкость, износостойкость и другие свойства. SKF имеет более чем 20-летний опыт в этой области и вывела на рынок несколько успешных продуктов – NoWear, INSOCOAT стали популярными торговыми марками.
К модификации поверхности подшипников прибегают, когда еобходимо улучшить электроизоляционные свойства, коррозионную стойкость, износостойкость и другие свойства. SKF имеет более чем 20-летний опыт в этой области и вывела на рынок несколько успешных продуктов – NoWear, INSOCOAT стали популярными торговыми марками.
Добавленная стоимость
Обычно модификация поверхности используется для подшипников, изготовленных из обычной подшипниковой стали. Модификация путем нанесения покрытий из материалов, обладающих требуемыми свойствами, превращает подшипник в товар с добавленной стоимостью.
Некоторые покрытия наносятся оченьтонкими слоями, иногда в несколькомикрон, что позволяет использоватьстандартные подшипники без необходимости дорогостоящей переналадки оборудования для изменения допусков.
Обзор технологий модификации поверхности подшипников
На рис. 1 показаны технологии модификации поверхности подшипников, используемые SKF. Четкого разграничения между процессами нанесения покрытий и обработкой не существует (так, например, диффузия и легирование относятся, в основном, к процессам нанесения покрытий).
В данном обзоре представлены как весьма традиционные технологии (погружение и жидкое распыление, химическая конверсия, оцинковывание и процессы химического восстановления), так и более современные технологии, включая газотермическое напыление, конденсацию из газовой фазы (PVD), диффузионную модификацию, легирование.
Газотермическое и плазменное напыление
Суть процесса плазменного напыления состоит в напылении расплавленного материала на поверхность в целях формирования ровного и плотного покрытия. Материал в виде порошка подается в высокотемпературный плазменный факел, где частицы материала быстро нагреваются и разгоняются до высокой скорости. При cтолкновении с поверхностью субстрата раскаленные частицы материала быстро остывают, формируя покрытие. Преимущество данного метода заключается в том, что он позволяет напылять материалы, имеющие очень высокую точку плавления, например, Al2O3.
Торговая марка SKF INSOCOAT была присвоена подшипникам с электроизолирующим покрытием Al2O3, которое способно выдерживать напряжение пробоя до 3 000 Вт постоянного тока. Подшипники INSOCOAT успешно продаются на рынке вот уже более 20 лет (рис. 2).
Композитные покрытия PTFE
Покрытия на основе PTFE используются для предотвращения проскальзывания и возникновения фреттинг-коррозии на посадочной поверхности колец подшипников. Еще одна область применения – зона скользящего контакта необслуживаемых шарнирных подшипников.
Для обеспечения прочной адгезии слоев PTFE с технологическими поверхностями используются три основных метода: спеченый бронзографитовый композитный материал, ткань с волокнами PTFE (рис. 3) и композитный материал на основе PTFE. Композитный материал из спеченого бронзографита состоит из стальной подложки с медным покрытием и тонкого слоя спеченого бронзографита (0,3 мм). PTFE с MoS2 проникает в пористую структуру и образует слой толщиной 10-30 μm (рис. 3).
Более распространенный метод – это использование ткани с волокнами PTFE (рис. 3). Волокна PTFE переплетают со стекловолокном в двухстороннюю ткань. Дополнительную подложку изготавливают из чистого стекловолокна. Две ткани пропитывают синтетическим каучуком, прокатывают, чтобы получилась ткань толщиной 0,6 мм, и склеивают.
Композитный материал PTFE представляет собой стеклонаполненный полиамид с включениями PTFE. Предельно допустимая удельная нагрузка и диапазон рабочих температур полиамидных покрытий меньше, чем у покрытий, нанесенных двумя вышеуказанными методами.
PVD (конденсация из газовой фазы)
Компоненты, удерживаемые специальными приспособлениями, помещают в подогретую вакуумную камеру, где их поверхности подвергаются бомбардировке ионами аргона в целях очистки. Затем на ионный источник подается высокий отрицательный потенциал. Ударяя в источник, газовые разряды испаряют материал покрытия, частицы которого переносятся химически активным газом и осаждаются на поверхности мишени (рис. 4).
Процесс PVD обычно используется для напыления очень тонких слоев металла и углерода. Продуктами данного метода являются покрытия NoWear (рис. 5) и твердосмазочные покрытия MoS2.
Электрохимическое осаждение
При растворении металлической соли в воде образуются положительно заряженные ионы, электролит. При подаче достаточного количества электротока ионы металла образуют на технологической поверхности твердый металл. Данный процесс известен как гальванопокрытие или электрохимическое осаждение.
Электрохимическим способом можно наносить покрытия из таких металлов, как Ni, Cr, Zn/Fe, Ag и Au; nTDC (мелкозернистый плотный хром) – коррозионноустойчивое покрытие с низким коэффициентом трения.
Легирование
С помощью специального процесса холодного распыления микрочастицы твердого смазочного материала проникают в материал на глубину несколько микрон и проникают в подповерхностный слой материала. Оборудование для ионного легирования как правило состоит из источника ионов и мишени. Ионы требуемого химического элемента ускоряются в электрическом поле и направляются на поверхность мишени. (рис. 7).
Процесс легирования ионами MoS2 был запатентован компанией Microseal Industries Inc (суффикс обозначения SKF VL049) и известен под названием Microseal. Используется для уменьшения трения и износа.
Контроль качества и методы измерения
В некоторых случаях использовать обычные методы измерения для определения свойств покрытия не представляется возможным из-за малой толщины слоя покрытия и различных комбинаций материалов. Вследствие этого были разработаны новые методы измерения.
Измерение коэффициента трения и износостойкости
Главными элементами измерительной установки являются шар и диск с независимым вращением (рис. 6). Качение или проскальзывание в зоне контакта создается регулировкой частоты вращения. Величина коэффициента трения вычисляется по формуле μ=Fr/Fn, где Fr – сила трения и Fn – нормальная сила. Коэффициент износа определяется по времени сквозного износа покрытия. Признаком полного износа покрытия является изменение величины коэффициента трения.
Твердость
Твердость тонких слоев определяется по глубине вдавливания металлического шарика. Величина диагонали пирамидального отпечатка является основой для расчета твердости по формулам Викерса.
Важно отметить, что глубина вдавливания не должна превышать 10% толщины покрытия, в противном случае на результат окажет влияние материал субстрата. Какого-либо стандарта для измерения микротвердости тонких покрытий не существует.
Адгезия
Наиболее распространенными методами определения адгезии являются испытание по Роквеллу (Rockwell C test) и метод нанесения царапин.
Испытание по Роквеллу (Rockwell C test VDI 3824) проводится так же, как стандартное испытание на твердость по Роквеллу (рис. 8). Размер и тип дефекта покрытия в самом отпечатке и вокруг него исследуется под оптическим микроскопом и сравнивается с серией фотографических изображений.
Еще один метод – определение адгезии царапанием VDI 3824. На поверхность образца наносится царапина конусом Роквелла (рис. 9) с постепенным увеличением нагрузки. След царапины исследуется под микроскопом на предмет определения величины критичной нагрузки. Показателем критичной нагрузки является расстояние между началом царапины и точкой нарушения целостности покрытия. Критичная нагрузка достигается в момент начала отслаивания покрытия.
Толщина покрытия
Одним из неразрушающих методов измерения является рентгенофлюоресцентный анализ (XRF) VDI 3824. Поверхность образца подвергается рентгеновскому облучению. Расчет толщины покрытия производится по интенсивности рентгенофлюоресцентных линий спектра анализируемого образца на основе заранее построенной градуировки.
Разрушающий метод (метод Кало) основан на измерении толщины покрытия на металлографическом шлифе с помощью светооптического микроскопа (рис. 10). Сферический шлиф на поверхности субстрата изготавливается с помощью шарика и алмазной пасты. Измерение толщины покрытия на кромках образовавшегося кратера позволяет рассчитать толщину покрытия.
Заключение
Некоторые покрытия уже успешно представлены на рынке. Так, например, NoWear четко позиционируется на рынке как покрытие, уменьшающее усталостный износ и коэффициент трения в подшипнике.
Для расширения бизнеса, связанного с модификацией поверхности подшипников, достаточно всего лишь рассматривать модификацию поверхности не только как экстренное средство, когда подшипник вышел из строя. Еще важнее уже на ранней стадии разработки технических решений проанализировать возможность использования подшипников со специальным покрытием с тем, чтобы упредить возможные отказы в работе подшипниковых узлов.
Поскольку на рынке уже имеется большое количество различных покрытий, успех разработки новых решений будет зависеть от того, насколько они будут удовлетворять потребностям клиентов.