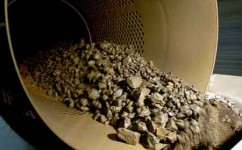
ЧИСТЫЙ УСПЕХ
РЕЗЮМЕ
— Разработка карьера Сагрекс Биз в Бельгии началась в 1848 г.
— В карьере работает 40 человек.
— В нем добывается 1 700 000 т известняка в год.
— Ассортимент продукции – от мелкого песка до 300-килограммовых бутовых камней.
— 60% продукции перевозится по реке, 40% – грузовиками.
— Карьером Биз владеет компания Sagrex, входящая в немецкую группуHeidelberg Cement.
Эксплуатация оборудования в условиях песчаной пыли в известняковом карьере требует постоянной бдительности и особой техники. Бельгийская компания, ведущая разработку карьера Сагрекс Биз, обратилась к SKF.
Издали ярко-желтые снующие туда и обратно грузовики выглядят, как детские машинки в гигантской песочнице. Но если подойти ближе, грузовики поражают одним только видом своих двухметровых колес, и начинаешь осознавать масштаб бельгийского карьера Биз, уходящего примерно на 80 м в глубину.
Известняковый карьер Сагрекс Биз находится в северной части Намюрского яруса – геологической структуры, которая сформировалась более 300 млн. лет назад. «Раньше эта часть центральной Бельгии находилась под водой, – поясняет Жан-Мишель ван Петехем, директор карьера. – Пласт известняка, который мы разрабатываем здесь, образовался из окаменевших известняковых отложений, оставшихся, когда плиты сдвинулись и вода ушла».
Занимающий более 85 га по берегам реки Маас карьер Биз разрабатывается с 1848 г., тогда использовали только силу людей и лошадей.
«Теперь у нас парк многотоннажных грузовиков, 40 работников, мы используем 2000 кг динамита в день и добываем примерно 1,7 млн т высококачественного известняка каждый год», – рассказывает ван Петехем. Разработка этого карьера разрешена еще в течение 5-10 лет. Потом добыча будет перенесена в другое место по соседству.
«Известняк, который мы добываем здесь, очень подходит для производства бетона, – поясняет ван Петехем. – Он используется в волноломах и при строительстве гаваней, в проектах строительства гражданских объектов, а также в химической промышленности, при производстве железа и стали и в сельском хозяйстве». В карьере производятся продукты из известняка – от мелкого песка до 300-килограммовых бутовых камней, которые используются для строительства дамб в Голландии.
Известняк взрывают на уступе карьера, собирают экскаваторами и перевозят грузовиками на обработку. Там его отправляют в щековую дробилку, где его дробят и сортируют камни по размерам.
Породу дробят для получения полной линейки различной продукции, но прежде она должна пройти через установку промывки с вращающимся ситом, чтобы удалить всю приставшую глину.
В Сагрекс Биз очень серьезное внимание уделяется процессу промывки. «Здесь много глины, и если ее не смыть надлежащим образом, бетон будет менее прочным, – поясняет ван Петехем. – Карьер не обязательно должен быть чистым, но если он чистый, будет меньше отходов, выше выработка и лучше конечная продукция, поступающая на продажу, поэтому мы вложили средства в эти вращающиеся промывочные установки. Немногие карьеры имеют такое оборудование, а наш – один из самых успешных, так что судите сами», – говорит он с заметной искоркой в глазах.
В карьере Биз имеются две промывочные установки с вращающимися ситами, которые установлены рядом друг с другом в специальном здании на рабочей площадке. Установки имеют диаметр 3 м и длину 10 м, и каждая из них установлена горизонтально на 2 рядах из 9 колес, механически соединенных друг с другом, один ряд приводится в движение 132-киловаттным электродвигателем и редуктором.
Известняк, смешанный с водой, подается с одного конца, и когда барабаны вращаются и камни бьются друг о друга, глина с них стирается.
«Мы установили промывочные установки в 1992 г., и они справлялись с работой хорошо, – говорит ван Петехем, – но подшипники регулярно выходили из строя, раз в три месяца, и каждый раз требовалось останавливать работу на восемь часов, чтобы заменить их». В 2007 г. он обратился в SKF и попросил специалистов компании посмотреть колеса и найти решение, позволяющее сократить простои и облегчить техобслуживание.
Решение, предложенное SKF, включало в себя конструкцию, подшипники, корпуса, уплотнения, валы и детали сцепления и охватывало колеса промывочных установок как со стороны привода, так и с противоположной стороны. В результате удалось добиться существенного сокращения времени простоя.
«Мы очень довольны решением SKF, – говорит ван Петехем. – Мы начали сотрудничать в 1980 г., и специалисты SKF всегда предлагали продуманные решения, давали ценные советы и поставляли высококачественные изделия, на которые мы можем положиться. Наше сотрудничество с отделом технической разработки этой компании по данному проекту стало большим успехом, и с тех пор, как оборудование было установлено, у нас не было никаких проблем, так что я доволен на 100 процентов. И я уверен, что так оно будет и в дальнейшем».
РАЗРАБОТКА НОВОГО РЕШЕНИЯ
SKF решила проблемы надежности промывочных установок в карьере Биз с помощью целого ряда мер.
«Мы разработали новые оси, позволяющие устанавливать стандартные подшипники SKF, что облегчило и ускорило замену деталей, – объясняет Юрген Мэттью, бизнес-менеджер по проектам разработки систем надежности бельгийского отделения SKF. – Использование разъемных корпусов подшипников означает, что весь комплект колес можно поднять, не снимая предварительно подшипники и корпуса».
Специалисты SKF выбрали подшипники с меньшим наружным диаметром, способные, однако, выдерживать более высокие нагрузки. Корпуса SKF оснащены эффективными уплотнениями, чтобы защитить подшипники в этих суровых условиях и сохранить достаточный уровень смазывания. В результате время простоя, которое требуется для замены колес, уменьшилось на 50%.
Со стороны привода наибольшую проблему представлял износ деталей механического сцепления между осями. «Сцепления осей вдоль всей длины установки не было, и приводной момент подавался только на два колеса. Поэтому оси изнашивались неравномерно, требуя регулярного ремонта и замены. Были и проблемы со снабжением, поскольку все детали были разного размера», – объясняет ван Петехем.
«Мы предложили решение с новыми стандартными и одинаковыми осями, а также с муфтой редуктора, так что вес оказывался равномерно распределен по всем колесам, и все колеса приводились в движение приводом, чтобы решить проблему неравномерного износа», – говорит Мэттью. Поскольку их диаметр меньше, чем диаметр диска, крепящегося болтами к валу, колеса можно заменять, просто отвинтив болты. Система была отрегулирована с помощью лазерного оборудования.