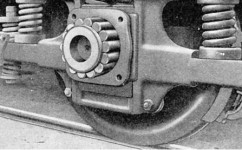
ЭВОЛЮЦИЯ ТЕХНОЛОГИИ ЖЕЛЕЗНОДОРОЖНЫХ БУКС
В первой из двух статей о конструкции железнодорожных букс мы расскажем об истории этого ключевого узла подвижного состава. Как компания с долгой традицией конструктивных разработок для букс, SKF всегда уделяла внимание экологическим моментам, а именно – сбережению энергии и смазочного материала.
РЕЗЮМЕ
Вместе с развитием железнодорожного транспорта росло стремление уменьшить трение и износ и снизить энергозатраты. Развитие буксовых подшипниковых узлов и подшипников стало главной частью усилий в этом направлении. SKF была одним из первых представителей науки трибологии, которая занимается изучением и применением основ трения, смазывания и износа для создания конструкций подшипников, которые принесли и продолжают приносить прибыли предприятиям, эксплуатирующим железные дороги.
В первой из двух статей о конструкции железнодорожных букс мы расскажем об истории этого ключевого узла подвижного состава. Как компания с долгой традицией конструктивных разработок для букс, SKF всегда уделяла внимание экологическим моментам, а именно – сбережению энергии и смазочного материала.
Cамого начала применения на железной дороге буксовые подшипниковые узлы экономили энергию и смазку. Сегодня бóльшая часть железнодорожного подвижного состава оборудуется передовыми конструкциями на основе буксовых подшипников или подшипниковых узлов колёсных пар, корпусов букс и встроенных датчиков. Теперь SKF поставляет на железнодорожный рынок дополнительные решения – мониторинг состояния и пакеты услуг, включая организацию технического обслуживания, переоборудование и обучение персонала.
Основной конструкционный замысел железнодорожных колёс оставался неизменным за всю историю железных дорог. Узел из двух колёс и оси обычно называют колёсной парой, которая вращается на так называемых буксовых подшипниках. Подшипники размещаются в буксах или оснащаются специальными адаптерами, связанными напрямую или через пружины рессорного подвешивания с ходовой частью, в большинстве случаев представляющую собой тележку. Букса – это один из главных узлов, определяющих безопасность железнодорожного подвижного состава.
При помощи трибологии – науки о трении, смазывании и износе – инженеры и учёные многое узнали о взаимодействии поверхностей при взаимном перемещении. Примеры использования трибологии можно найти и в области транспорта. Первые попытки конструирования колёс и букс для железнодорожных нужд прошли путь от первых антифрикционных подшипников для букс до развития новейших высокосложных буксовых подшипниковых узлов и сложных наборов конструкторских решений для подшипников, уплотнений, систем смазки, мехатроники (например, датчиков эксплуатационных параметров или рабочих характеристик) и полного набора техобслуживания.
Первые железные дороги
Один из ранних примеров энергосбережения – конно-железная дорога Линц (Австрия) – Будейовице (Чехия), построенная, в основном, для перевозки соли, которая тогда стоила очень дорого. Линия длиной в 130 км открылась в 1832 г. В то время это было самое длинное железнодорожное сообщение в мире. На рис. 1 видно, что рельсовая система могла выдерживать нагрузку, превышающую нагрузку на дорожный транспорт в 8–10 раз.
Буксовые подшипниковые узлы
Существует несколько ранних патентов, но доказательств их практического применения нет. Одним из первых документированных случаев применения букс с подшипниками качения были трёхосные пассажирские вагоны, выпущенные в 1903 г. Вагоны были оснащены буксами, каждая из которых несла два радиальных шарикоподшипника (рис. 2а). Тяговое усилие для двухвагонной сцепки общим весом 33,15 тонны составило 4,4 кН с подшипниками скольжения, и только 0,62 кН с шарикоподшипниками, то есть оказалось меньше на 86% (рис. 2b). Подшипники и буксы были сделаны компанией Deutsche Waffen- und Munitionsfabriken A.G. (DWF)в Берлине, Германия. Позже компания стала частью Vereinigte Kugellagerfabriken (VKF), которую впоследствии купила SKF.
Дальнейшие испытания проводились в США в 1905 г. профессором Грэмом из Сиракузского университета в Нью-Йорке. Он исследовал энергопотребление в сравнительном полевом испытании двух поездов, один был оснащён подшипниками скольжения, а другой – подшипниками качения (рис. 3a). Потребление энергии на пути следования поезда с подшипниками скольжения составило 6,45 кВт, сравнительно с 3,10 кВт для поезда с подшипниками качения. Экономия энергии составила 52% (рис. 3b). В 1907 г. оператор компании Syracuse Rapid Transit сообщил филадельфийской компании – производителю подшипников Standard Roller Bearing (SRB) – что после 4,5 лет эксплуатации и пробега около 400 000 км у подшипников качения не было признаков износа. Годовая экономия угля для производства необходимой электроэнергии на вагон составила 260 долларов, что соответствовало 390 г золота. Компания Standard Roller Bearing позже стала частью корпорации Marlin Rockwell (MRC). SKF купила MRC в 1986 г.
Навстречу скорости
Скорость стала сутью железной дороги с момента появления первого паровоза в 1804 г. SKF всегда активно разрабатывала конструкции, отвечающие жёстким требованиям создателей и операторов высокоскоростных поездов – развивала, конструировала и испытывала подшипники колёсных пар (рис. 4а и 4b). К 1930 г. поезда в Европе и Северной Америке уже достигли крейсерской скорости 130 км/ч при максимальной скорости 160 км/ч. Сегодня высокоскоростным железнодорожным транспортом по некоторым европейским стандартам считается подвижной состав, развивающий максимальную скорость более 200 км/ч.
Экономия смазочного материала
Подшипниковые смазки – масла и пластичные смазки – получают из минеральных масел. При техническом обслуживании после долгих лет службы использованную смазку приходится собирать и специально утилизировать подобно другим продуктам, содержащим минеральные масла. Очевидно, что уменьшение количества смазки будет положительно сказываться на окружающей среде.
На заре железнодорожного транспорта применялись смазываемые маслом подшипники скольжения. Первичная заправка маслом буксы типичного немецкого товарного вагона составляла 1,3 кг, из которых 500 г использовались для заполнения смазочной прокладки и 800 г для заполнения масляного резервуара. Приходилось часто проверять уровень масла из-за непрерывного расходования её в работе; потери масла сильно загрязняли железнодорожные пути и окружающую среду. На 1000 км расходовалось около 200 г масла.
Большим шагом вперёд стало внедрение подшипников качения с пластичной смазкой. Заполнение смазкой проводится при сборке, в последующем смазывании в большинстве случаев нужды нет. В 1930-е гг. количество смазки в типовой буксе немецкого товарного вагона, оснащённой цилиндрическим роликоподшипником, составляло примерно 1,7кг. За последние десятилетия было выполнено множество исследований, подтвердивших, что количество смазки можно радикально уменьшить без риска развития состояния смазочного «голодания». В 1950-х гг. количество смазки было уменьшено до 1,2 кг. Позже оно снизилось до 1 кг и достигло к настоящему времени 700 г для смазывания открытого цилиндрического роликоподшипника. Следующим большим шагом в уменьшении потребления смазки стало введение предварительно смазанного цилиндрического роликоподшипника CRU со встроенным уплотнением, которому нужно было всего от 200 до 300 г смазки. Снижение количества смазки оборачивается снижением рабочей температуры, что продлевает ресурс смазки и подшипника.
Во второй части статьи описана разработка современных буксовых узлов.