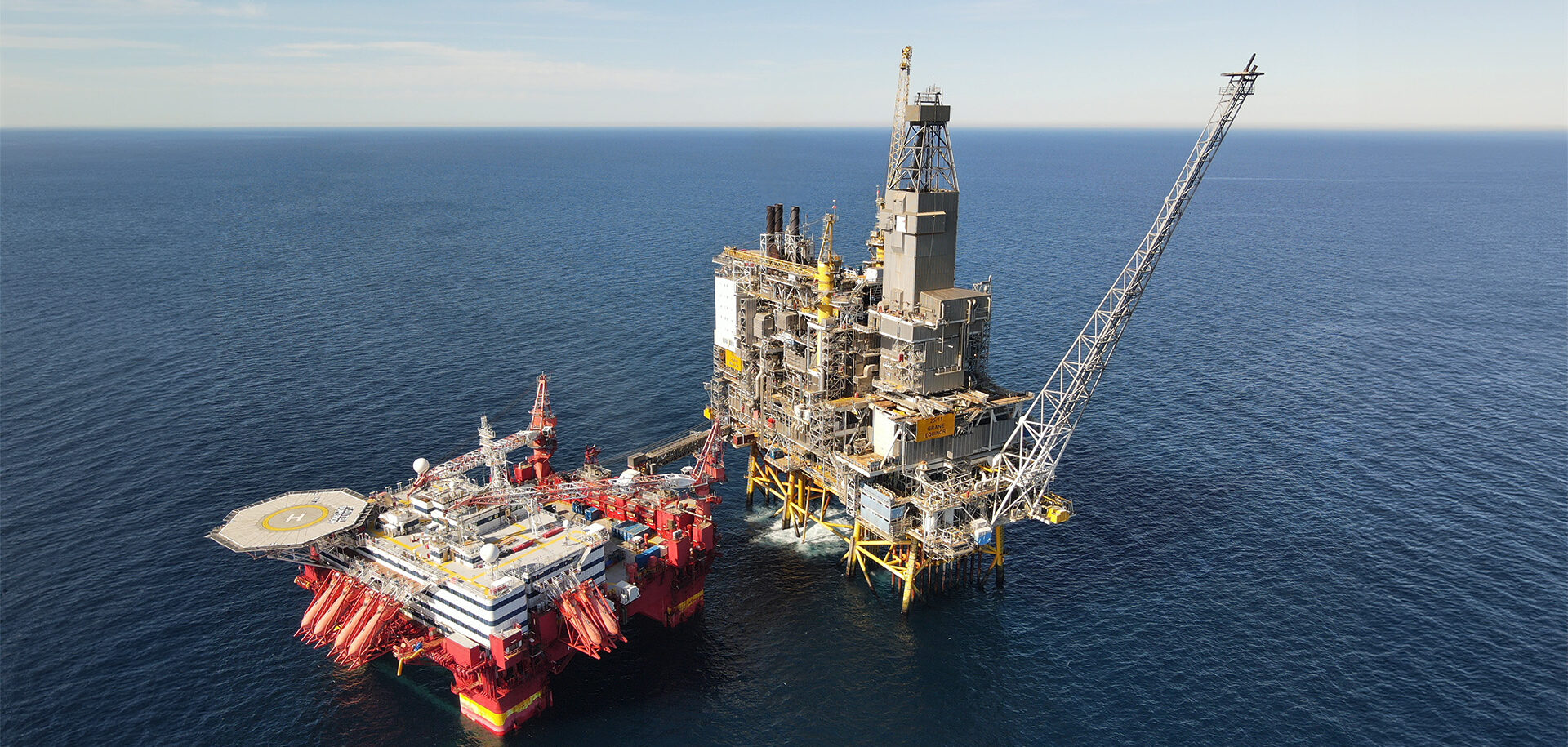
Smart monitoring halves service need for maritime hotels
SKF’s vibration monitoring system helped Floatel cut maintenance times and save costs to keep its floating hotel platforms offshore for longer.
The tough maritime environment forced Floatel International to move its large hotel platforms into port every five years for extensive inspections and servicing. When SKF installed a system for vibration monitoring, this gave rise to entirely different checking procedures and meant that service intervals could be extended.
“As a result, we are able to almost halve our most significant and expensive maintenance measures,” says Gustav Kinding, category manager for the thrusters at Floatel.
Floatel was established in 2006 with the business concept of supplying accommodation platforms in maritime environments. The idea is to offer comfortable accommodation at sea in connection with various platforms, for example, in association with maintenance work, new construction or decommissioning.
“When we are hired, we move one of our hotels out and link it to the platform with a gangway,” says Gustav Kinding. “The workers sleep, eat, exercise and go to the cinema in our facility. They then cross the gangway when they need to go to work.”
Thrusters maintain position
The platforms are powered by four to six thrusters fitted with propellers. These are located under the pontoons, approximately 15 metres below the sea surface. The platforms are rarely anchored. Instead, once the platforms are in place, the thrusters maintain their position and counter the effects of the weather, wind and waves.
We get a complete solution, with everything from the manufacture of parts to installation and maintenance.
Gustav Kinding, category manager for the thrusters at Floatel
The thrusters are of vital importance for both operation and safety. They also represent one of the biggest challenges when it comes to maintenance. “Maintaining the thrusters is a major operation,” says Kinding. “We have to dock by a quay, and both divers and cranes are required.”
Due to the tough regulations laid down by the classification body, the company was previously tied to a five-year inspection cycle. They were forced to move the rigs into port, remove all the thrusters, inspect their condition and carry out servicing. As long as everything looked OK, it was possible to extend by a further five-year interval. “We never actually observed any major problems,” Kinding says, “but at the same time we didn’t know, prior to the inspection, whether we would be able to continue operating.”
In 2014, a collaboration was initiated with SKF, which gradually installed vibration monitoring of the thrusters on all the platforms. Measurement data is now inspected and analysed daily by SKF’s maritime centre in Scotland. A status report and recommendations regarding suggested actions are supplied once a month. “Through ongoing checks, we are able to monitor the condition of our bearings and rest assured as regards continuing operations,” says Kinding.
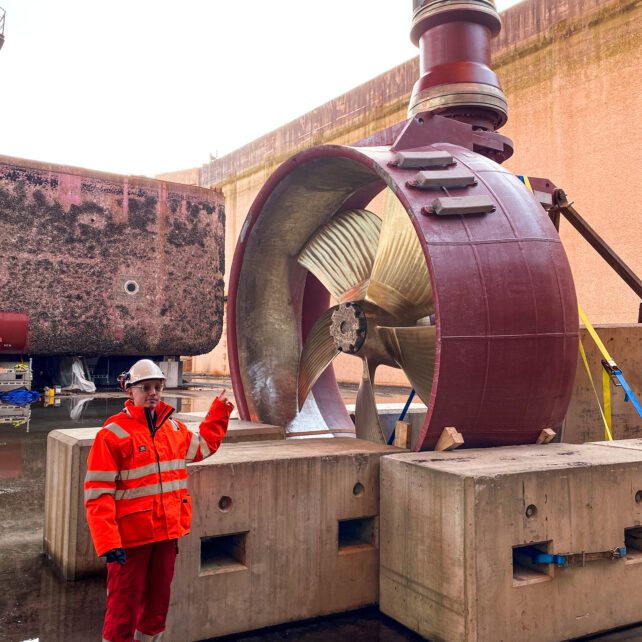
Planned maintenance
The five-year inspection intervals are no longer necessary. Instead, there are much greater opportunities to schedule maintenance stoppages at the relevant time. Kinding explains that the normal service life of a platform is estimated at approximately 25 years. This would mean four major maintenance stoppages at five-year intervals. “We now achieve around eight years between our major audits, and sometimes more than that, which means a potential halving our most expensive maintenance work,” he says. “A very large financial saving, in other words.”
The collaboration with SKF has gradually expanded and come to encompass more and more products and solutions. SKF now supplies not only bearings, seals and lubrication, but also servicing, analysis and development. “We get a complete solution, with everything from the manufacture of parts to installation and maintenance,” says Kinding. “As a result, SKF is involved in the entire chain. We know that they are world leaders when it comes to roller bearings and lubrication. Having access to such comprehensive expertise means that we feel extremely secure.”
Collaboration regarding development
In collaboration with SKF, a number of development projects are in progress aimed at further improving the reliability of the rotating systems, when it comes to both bearing solutions and seals. In recent years, work has also been initiated in relation to analysing and evaluating lubrication. Systems for automatic lubrication have been installed, and samples of the transmission fluid in the thrusters and the hydraulic fluid in the thruster control system are taken every three months and sent to SKF for analysis.
“During this analysis, we can see if there are any traces of water or particles, which indicate wear,” says Kinding. “If these are present, we can then take appropriate measures.” A new problem that has been discovered fairly recently is the passage of current from frequency-controlled electric motors out through the propellers. Kinding explains: “SKF came up with the idea of using hybrid bearings in which the rolling elements are non-metallic. In this way, they act as insulation, breaking the passage of current.”
The collaboration between SKF and Floatel is growing ever closer. Kinding says that it is not only the expertise that is important, but also the proximity. “For us working in Sweden, it’s very handy to have SKF’s personnel close at hand in Gothenburg,” he says. “It’s simply a matter of making a call and arranging a meeting.” Kinding says he also appreciates the fact that SKF has really immersed itself and tried to learn his products and find new solutions. “We have established a good level of communication,” he says, “where we can try out exciting new ideas that we have developed together.”