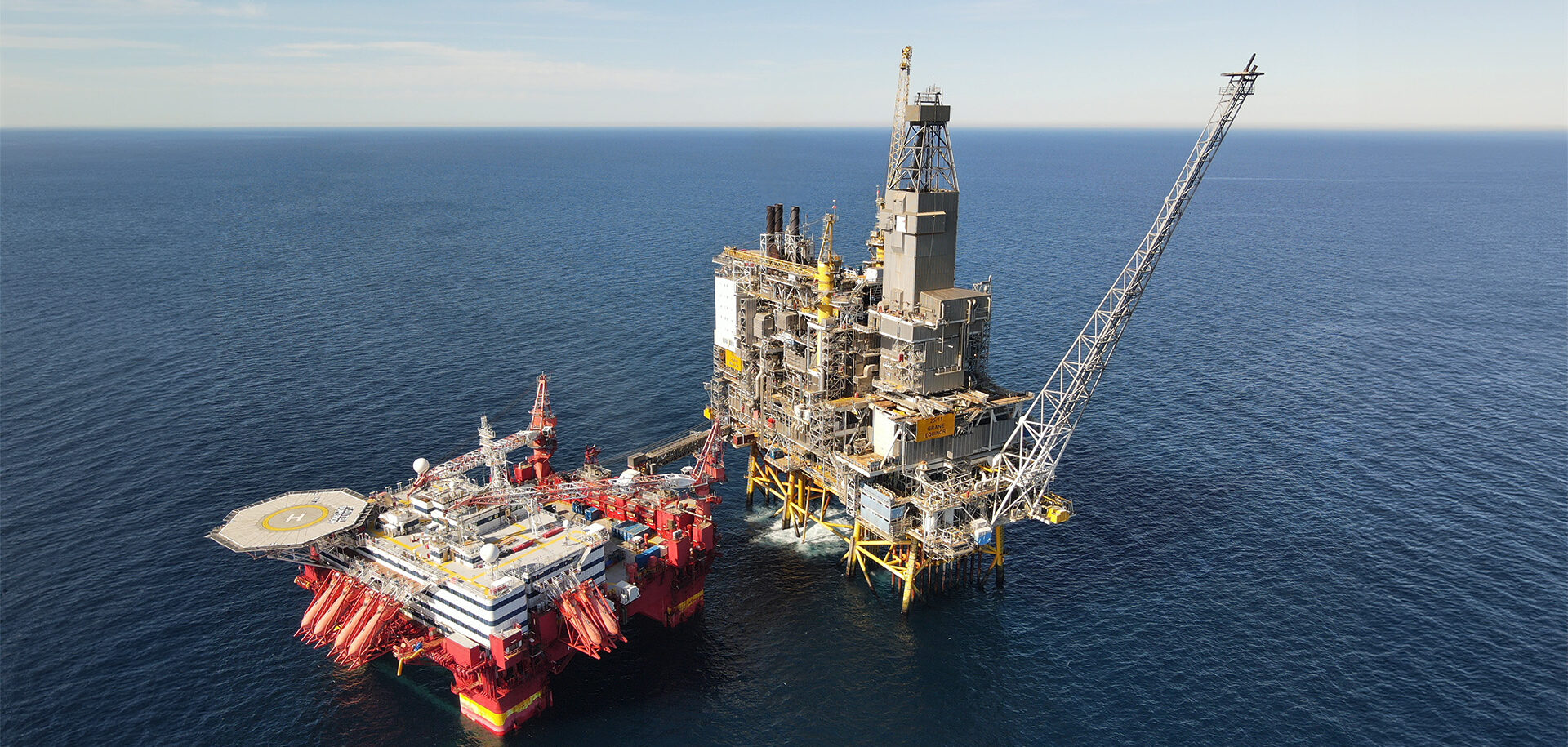
Las necesidades de mantenimiento de los hoteles marítimos se reducen a la mitad gracias al monitoreo inteligente
El sistema de monitoreo de la vibración de SKF ha ayudado a Floatel a alargar los intervalos de mantenimiento y a ahorrar costos para que pueda mantener sus plataformas hoteleras flotantes en alta mar durante más tiempo.
Las duras condiciones del entorno marino obligaban a Floatel International a llevar a puerto sus grandes plataformas hoteleras cada cinco años para someterlas a inspecciones y revisiones exhaustivas. Cuando SKF instaló un sistema de monitoreo de la vibración, se pudieron implementar procedimientos de inspección totalmente distintos que han permitido alargar los intervalos de mantenimiento.
“Hemos podido reducir casi a la mitad nuestras medidas de mantenimiento más significativas y costosas”, afirma Gustav Kinding, responsable de categoría para los propulsores de Floatel.
Floatel fue constituida en 2006 con la misión de suministrar plataformas de alojamiento para entornos marinos. La idea es ofrecer un alojamiento confortable en alta mar para el personal que trabaja en diversas plataformas, por ejemplo, para realizar trabajos de mantenimiento, construir instalaciones nuevas o desmantelar instalaciones obsoletas.
“Cuando nos contratan, trasladamos uno de nuestros hoteles y lo unimos a la plataforma con una pasarela”, explica Gustav Kinding. “Allí, los trabajadores duermen, comen, hacen ejercicio y van al cine. Luego, cuando tienen que ir a trabajar, simplemente cruzan la pasarela”.
Se mantienen en posición con propulsores
Las plataformas son propulsadas por entre cuatro y seis propulsores dotados de hélices y situados bajo los pontones, a unos 15 metros de profundidad. Raras veces las plataformas están ancladas en el suelo marino. En lugar de eso, los propulsores mantienen las plataformas en su sitio, contrarrestando los efectos del clima, el viento y las olas.
Nos entregan una solución completa, que va desde la fabricación de piezas hasta la instalación y el mantenimiento.
Gustav Kinding, responsable de categoría para los propulsores de Floatel
Imprescindibles tanto para el funcionamiento de las plataformas como para su seguridad, los propulsores también representan uno de los mayores desafíos para el mantenimiento. “El mantenimiento de los propulsores es una operación de envergadura”, admite Kinding. “Hay que llevar la plataforma a un muelle y, para ello, hacen falta buzos y grúas”.
A raíz de las estrictas normas impuestas por los organismos de certificación, la empresa debía cumplir con un ciclo de inspección quinquenal. Para ello, debía trasladar las plataformas a puerto, extraer todos los propulsores, comprobar su condición y realizar tareas de mantenimiento. Si la inspección daba un resultado satisfactorio, se concedía una nueva prórroga de cinco años. “En realidad, nunca se han detectado problemas importantes”, observa Kinding, “pero, previamente a la inspección, nunca sabíamos si después podríamos volver a llevar la plataforma al mar”.
En 2014, se inició una colaboración con SKF, consistente en la instalación progresiva de sistemas de monitoreo de la vibración para los propulsores de todas las plataformas. Ahora, los datos de medición son inspeccionados y analizados diariamente por el centro marítimo de SKF en Escocia. Una vez al mes, se entrega un informe de situación, que incluye recomendaciones sobre las medidas que se deben tomar. “Gracias a los controles continuos, podemos monitorear la condición de nuestros rodamientos y asegurar la continuidad de nuestras operaciones”, asegura Kinding.
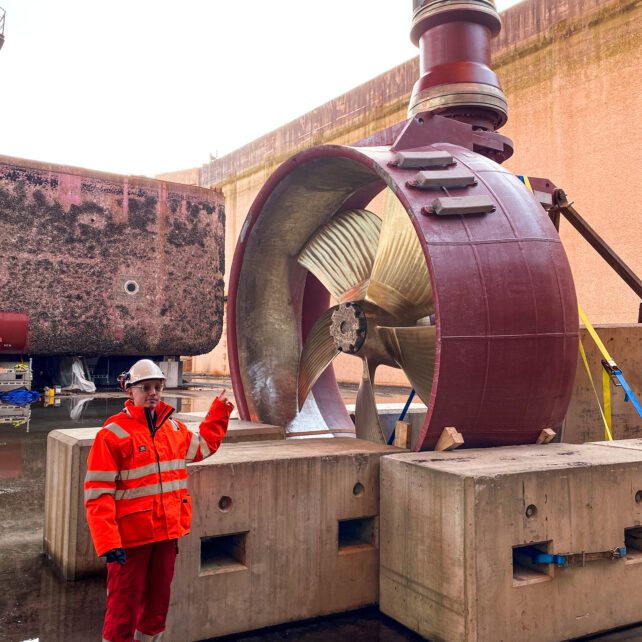
Mantenimiento planificado
Ya no es necesario realizar inspecciones cada cinco años. En su lugar, han surgido muchas más oportunidades para planificar paradas de mantenimiento programadas cuando son convenientes. La vida útil esperada de las plataformas suele ser de unos 25 años, explica Kinding, con cuatro paradas de mantenimiento importantes según el programa quinquenal. “Ahora transcurren unos ocho años entre cada una de nuestras auditorías exhaustivas, y, a veces, lo podemos alargar aún más. Eso nos brinda la posibilidad de reducir a la mitad nuestras operaciones de mantenimiento más costosas”, afirma. “Se trata de un ahorro financiero muy importante, sin ninguna duda”.
La colaboración con SKF se ha ido ampliando progresivamente para abarcar cada vez más productos y soluciones. Hoy, SKF no solo suministra rodamientos, sellos y lubricación, sino también servicios de mantenimiento, análisis y desarrollo. “Nos entregan una solución completa, que va desde la fabricación de piezas hasta la instalación y el mantenimiento”, dice Kinding. “De este modo, SKF participa en toda la cadena. Sabemos que son líderes mundiales en rodamientos y lubricación. El hecho de contar con unas competencias tan completas nos da mucha confianza”.
Colaboración en el desarrollo
En colaboración con SKF, se están llevando a cabo varios proyectos de desarrollo destinados a seguir mejorando la confiabilidad de los sistemas rotativos, tanto en lo que respecta a los rodamientos como a los sellos. En los últimos años, también se ha empezado a trabajar en el análisis y la evaluación de la lubricación. Se han instalado sistemas de lubricación automática, y cada tres meses, se extraen muestras de aceite de transmisión de los propulsores, y de aceite hidráulico del sistema de control de los propulsores, y se envían a SKF para analizarlas.
“Durante este análisis, podemos ver si hay trazas de agua o partículas, que indicarían la presencia de desgaste”, dice Kinding. “En caso de encontrarlas, tomamos las medidas oportunas”. Un nuevo problema que se ha descubierto hace poco es el paso de corriente desde los motores eléctricos regulados en frecuencia a través de las hélices. Explica Kinding: “SKF tuvo la idea de utilizar rodamientos híbridos con elementos rodantes no metálicos. Estos elementos actúan como aislantes e interrumpen el paso de la corriente”.
La colaboración entre SKF y Floatel es cada vez más estrecha. Kinding argumenta que no solo importa la competencia técnica, sino también la proximidad. “Trabajamos en Suecia y nos resulta muy práctico tener cerca al personal de SKF en Gotemburgo”, dice. “Basta hacer una llamada y concertar una reunión”. También valora el hecho de que SKF se haya sumergido en su negocio para conocer sus productos en profundidad y encontrar soluciones nuevas. “Hemos establecido una comunicación fluida”, continúa, “que nos permite probar ideas nuevas y apasionantes que hemos desarrollado juntos”.