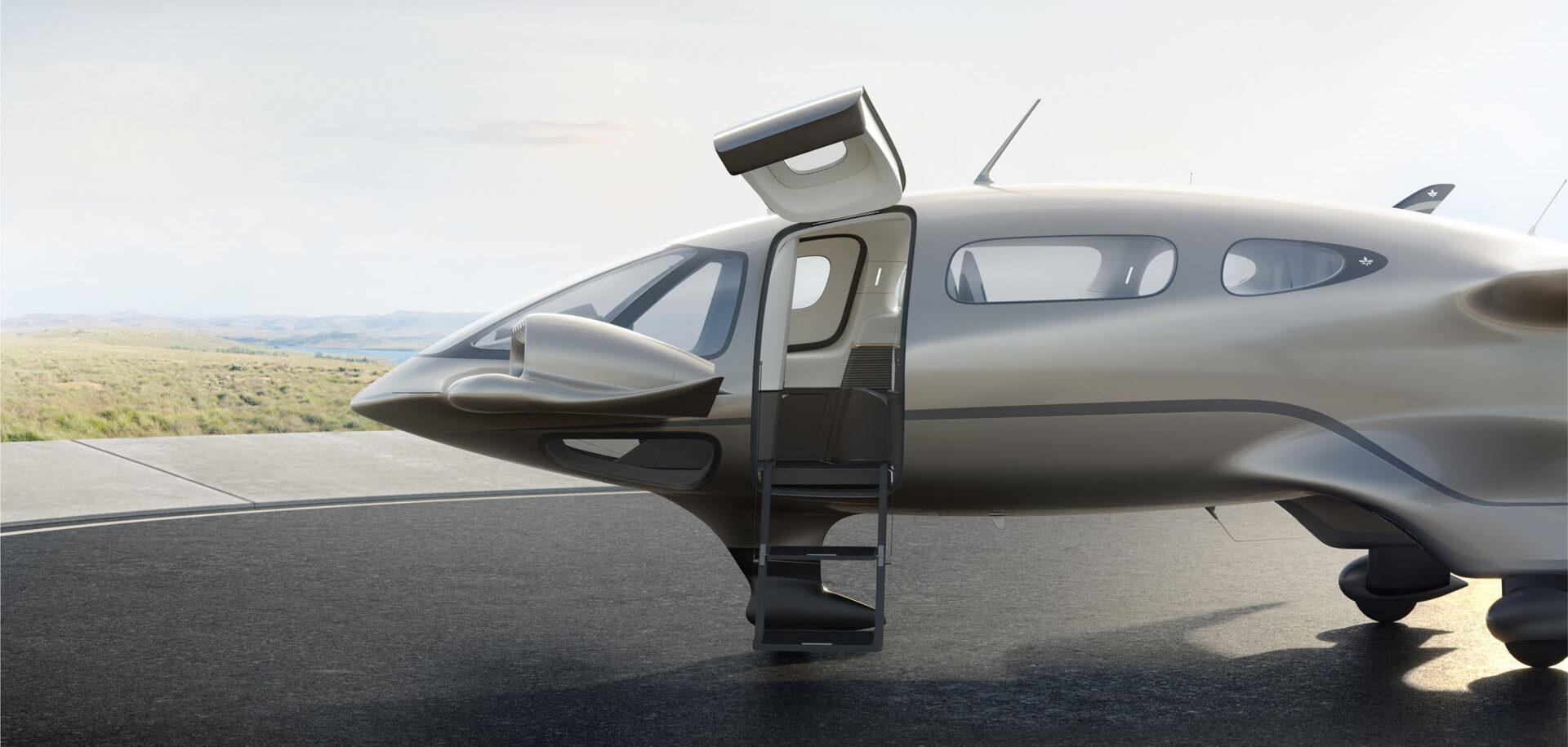
The next jet set
Electric aircraft maker Lilium has ambitions to transform air travel.
Electric aviation is taking off. Around the world, startups and established aerospace companies are pouring billions of dollars into entirely new categories of aircraft. Their technical concepts and business models are diverse, but the overarching goal is the same: to achieve flight that is environmentally and financially sustainable.
Switching from internal combustion engines and fossil fuels to electric motors and batteries is one way to address the harmful emissions associated with conventional aviation. The challenge for electric aviation pioneers is to find a profitable market niche for electric aircraft built with currently available technologies.
Even with today’s best batteries, control systems and motor technologies, electric aircraft can’t yet store enough energy to directly replace conventional passenger aircraft. Instead, electric aircraft companies are focusing on less energy-intensive applications. That means trips with shorter ranges, lower speeds and lighter payloads.
Many players in the sector believe that air taxi services are the application that best fits the capabilities and limitations of electric flight. They are developing machines that can carry one to four passengers on trips of a few miles. Designed with vertical takeoff and landing capabilities, they will be able to operate in urban environments, shuttling passengers between city centres and suburbs.
Going long
Lilium, a German electric air mobility company and a pioneer in electric aviation , has submitted a different flight plan. Founded in 2015 by four graduate engineering students at the Technical University of Munich, the company is developing an aircraft that can carry a pilot and as many as six passengers over distances of up to 175 kilometres.
Within the next 15 to 20 years, we will be able to build a conventional electric airliner with 80 seats and a range of more than 2,000 kilometres.
Daniel Wiegand, a founder of Lilium and the company’s chief engineer for innovation and future programmes.
“The mission of our company is to make regional aviation sustainable and as accessible as possible,” says Daniel Wiegand, one of Lilium’s founders and now the company’s chief engineer for innovation and future programmes. Dense, highly developed cities, like many in Europe, don’t provide the right environment for short-haul air taxi services, he says. “If you have to go from car to plane and back to car – with all the hassle of changing modes – you don’t get the time savings you need to make the flight worthwhile.”
Instead, Lilium’s focus is on intercity travel. “In regional aviation, you don’t spend five minutes on the plane like you do on a city trip, you’re there for 30 to 60 minutes,” he says. “So you need a different type of aircraft, one that gives you more capacity and a bigger cabin so you can spread the cost over more seats. You want something more comfortable. And you want to fly faster.”
Above all, electric regional aviation needs an extremely efficient aircraft that can fly for long periods of time using as little energy as possible. The need for efficiency has informed every aspect of Lilium’s design. The company’s current model, the Lilium Jet, has an architecture closer to a conventional fixed-wing aircraft than to the rotary-wing designs favoured by air taxi designers.
The aircraft has a canard configuration, with main wings at the rear of the fuselage, balanced by shorter “fore planes” at the nose. With large wings and a smooth, aerodynamic shape, the jet has all the right ingredients for efficient level flight.
Swing low
To provide passengers with true point-to-point comfort, the Lilium Jet must be able to operate from helipads like a helicopter does. The aircraft accomplishes this by swinging its engines down towards the ground, converting thrust into lift for vertical takeoff and landing manoeuvres.
“Compared to open rotors, our technology is much more efficient in cruise flight than in hover flight,” says Wiegand. “That’s why we focus on regional air mobility [RAM]. During cruise flight, for the 30 to 60 minutes, we get all the benefits of higher efficiency, lower noise and higher speed.”
The thrust vectoring design unlocks several other benefits for the electric aircraft manufacturer. The moving engines can also steer the Lilium Jet, allowing it to eliminate the control surfaces required by conventional aircraft. This saves valuable weight and simplifies production, operation and maintenance.
Choosing power
In choosing a suitable engine configuration, Lilium was both conventional and radical. The easy choice, says Wiegand, was whether the electric propulsion system should mimic the open propeller turboprop design or the ducted fan used in modern jet engines.
“Most passengers prefer the jet experience,” he says. “They have less vibration and less noise. They’re a little safer. They fly faster. They have more range and capacity.”
The radical choice was the number of engines installed on the Lilium Jet. Conventional fixed-wing jets have two to four engines. The Lilium Jet has an astonishing 30 engines, spread across its wings and canards.
Once again, this was a decision driven by the quest for efficiency. “Large engines have to be mounted in a nacelle that hangs under the wings,” Wiegand explains. “That adds a lot of weight and drag. Instead, we have divided our power requirements into many small engines. We can do that because it’s an electric propulsion system that scales very nicely into different sizes with the same efficiency.”
By integrating small engines into the wings, Lilium’s design reduces drag and saves significant weight. “The surface of the nacelles of our engines are part of the wing,” says Wiegand. “They generate lift for the aircraft.”
Hybrid endurance
The fast-spinning heart of each Lilium electric jet engine rotates on two bearings, one just behind the fan, the other at the back of the engine. As with every other component, Wiegand says, Lilium engineers wanted to minimize the size of these bearings as part of their effort to deliver the smallest, lightest package possible.
Prototype motors used standard bearings, but the Lilium team was always aware that production versions would require a more specialized solution. “Our requirements for the bearings were clear,” says Wiegand. “We need a very efficient unit to minimize power loss and heat generation. We don’t have an oil lubrication or cooling system, so the bearing must operate with grease lubrication and air cooling only. And we don’t expect our engines to require regular rebuilds, so the bearings must work for the life of the aircraft.”
The search for a product that could meet all these requirements led Lilium to SKF about three years ago. Since then, the two companies have been working together to refine a design that meets all of Lilium’s requirements. Through calculations, simulations and physical tests, the SKF team identified a bearing design that could meet the demanding requirements for efficiency and longevity and that was robust enough to withstand shock and vibration tests.
The final design, now undergoing bench testing at Lilium’s headquarters in Bavaria, Germany, is a hybrid deep groove ball bearing with steel rings and ceramic balls. It is lubricated with an advanced grease formulated for high temperatures and high speeds. Carefully selected seals ensure environmental protection and grease retention, whether the engine is operating horizontally in normal flight or vertically for takeoff and landing.
On the runway
Lilium started production of the first Lilium Jet at the end of 2023 and is getting ready for the first manned flight. The SKF bearings are among thousands of production-ready components that Lilium is assembling in its first certification aircraft. This aircraft, which will be joined by six others, will be used in an 18-month flight test campaign.
After 1,000 flight hours of compliance demonstration, customer deliveries are expected to begin in 2026. Lilium has pre-orders for more than 700 aircraft, with 106 confirmed orders and reservations.
There’s still a lot of work to be done, but as chief engineer for innovation and future programmes, Wiegand is already looking beyond the Lilium Jet. He predicts that improvements in battery and engine technology will soon make it possible to power larger aircraft with electricity. “Everyone is looking for ways to decarbonize aviation,” he says, and adds that other possible solutions, such as e-fuels or green hydrogen, only address half of the climate impact challenge because they don’t deal with high-altitude emissions from contrails and the clouds they create.
“Batteries are improving at 5 or 6 percent a year,” Wiegand continues. “Within the next 15 to 20 years, we will be able to build a conventional electric airliner with 80 seats and a range of more than 2,000 kilometres. That would allow 80 percent of the world’s commercial flights to be replaced with this quieter, cleaner technology.”
Simply powerful
The detailed design of Lilium’s electric jet engines evolved from the company’s overriding need for simplicity and light weight. The engines each contain only one main moving part comprising the fan, main shaft and motor magnets. The inverter and electronic control components are integrated and cooled by air drawn through the engine. Acoustic ducting minimizes noise from outside the motor.
The electric motor inside the engine continues the theme of doing more with less. Weighing just 4.5 kilograms, each motor can deliver 130 kW at peak power. At top speed, the motor shaft and 350-millimetre-diameter fan rotate together at 13,000 rmin.
Like any engine certified for use in commercial aviation, the Lilium Jet’s engines must be able to withstand the rigours of both normal and abnormal operating conditions. Examples of the latter include the ability to withstand ice build-up on the fan blades and the impact of bird strikes.