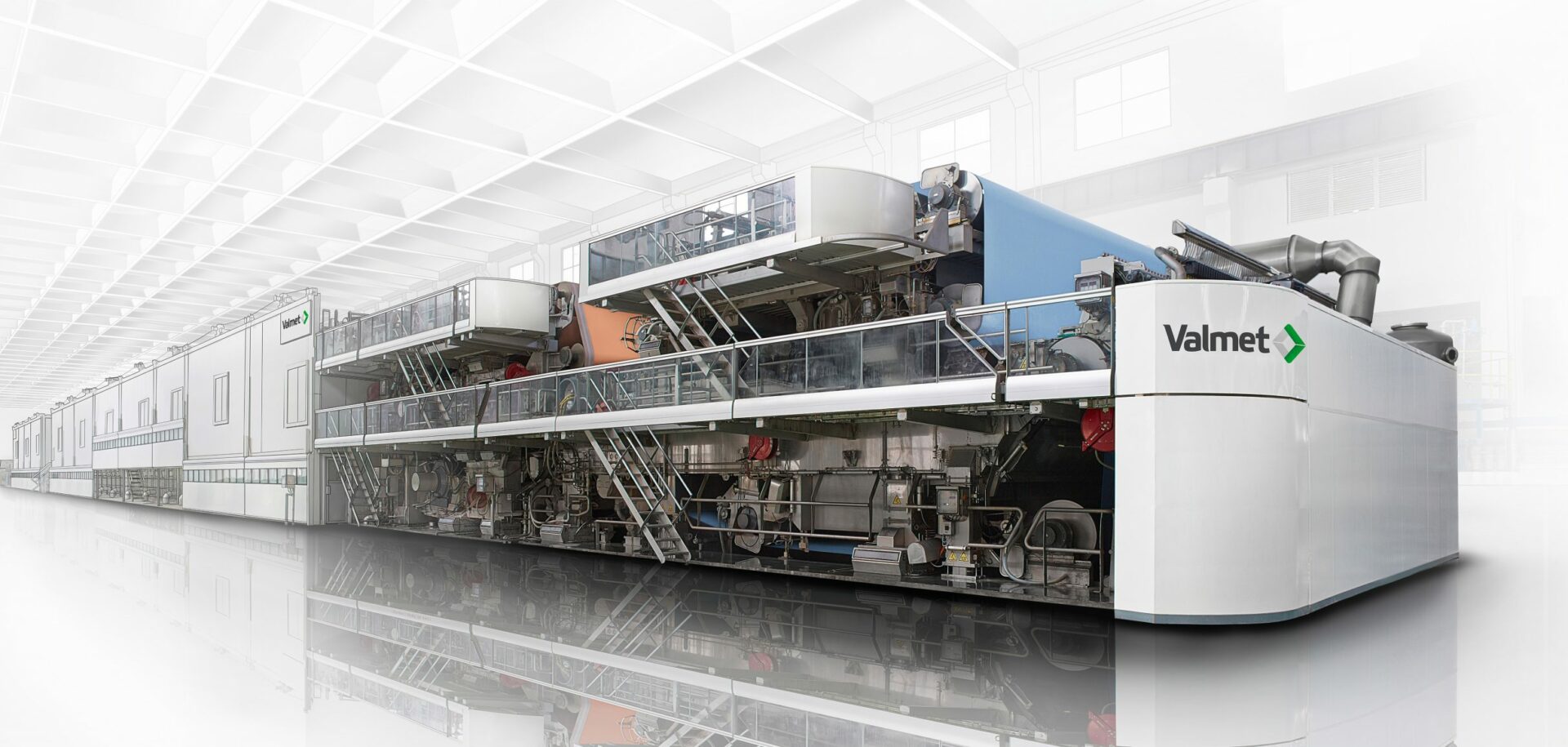
When smaller is better
Backed by its 200 years of industrial experience, Finnish company Valmet is rising to the challenges of the digital era.
The papermaking industry has changed dramatically in recent years. Sales in some of the most important traditional categories, such as newsprint, have declined in line with the rise of digital media and the associated changes in consumer behaviour. The rapid expansion of consumption in emerging markets, meanwhile, has fuelled demand for a host of paper-based products, from packaging to bathroom tissue.
Demand for renewable packaging solutions and emerging markets growth have contributed to increased demand for packaging grades.
Jyrki Laakkonen
Valmet’s category manager
“The demand for newsprint actually went down about a decade ago,” says Jyrki Laakkonen, Valmets category manager, Supply Chain. “Currently, newsprint represents slightly more than 5 percent of global paper and board demand. At the same time the demand for printing and writing papers has decreased slightly. On the other hand, growing global trade, e-commerce, demand for renewable packaging solutions and emerging markets growth have contributed to increased demand for packaging grades.”
It’s a completely new, modular way to build a board or paper machine, with significant savings in energy.
Jyrki Laakkonen
Valmet’s category manager
“It is a completely new, modular way to build a board or paper machine, with significant savings in energy, water and raw-material usage, built-in safety and usability, and a smaller carbon footprint through compact design,” says Laakkonen.
In a world where flexibility, efficiency, low cost of ownership and rapid return on investment are so important, every detail of its machine design is critical for Valmet. As it has done so often over the past 65 years, Valmet looks to partner with SKF to help it find innovative solutions for its latest generation of machines.
“The biggest, fastest machines [of the past] had design speeds of some 2,000 metres per minute,” says Arto Huttunen, global strategic account manager at SKF. “Bearing specifications for the loads and speeds involved often called for tailor-made solutions. With the modern, smaller machines that have design speeds of, say, 1,700 metres per minute, it becomes possible to use standard components, which can provide significant savings in capital and maintenance costs.”
However, using standard parts doesn’t mean Valmet relies any less on SKF expertise. SKF’s deep knowledge of materials science and rotating equipment helps Valmet’s engineers select precisely the right type and size of bearing for each application. Advanced bearing life calculation models are used to recommend the right product to suit the end customer’s operating conditions and lifetime requirements. “Frequently, that means they can use a solution that has a 50 percent lower cost than what they might have chosen if they’d relied on more traditional selection approaches,” says Huttunen.
Manufacturing costs and lead times are equally critical in the modern paper machinery sector. SKF’s global footprint is also of particular importance to Valmet, allowing the supply of locally manufactured components to the company’s production sites in China, for example, as well as ensuring that it can support its customers with service parts and analytical expertise all over the world.
Huttunen explains that designing and building equipment that is less costly and provides faster payback for customers is every bit as demanding as making those large, fast machines of the past. “Valmet has asked us to bring ideas from our experience with a wide range of different industries, from car manufacturing to wind power,” he says. “I’m sure that together we will be able to find many more innovative solutions.”