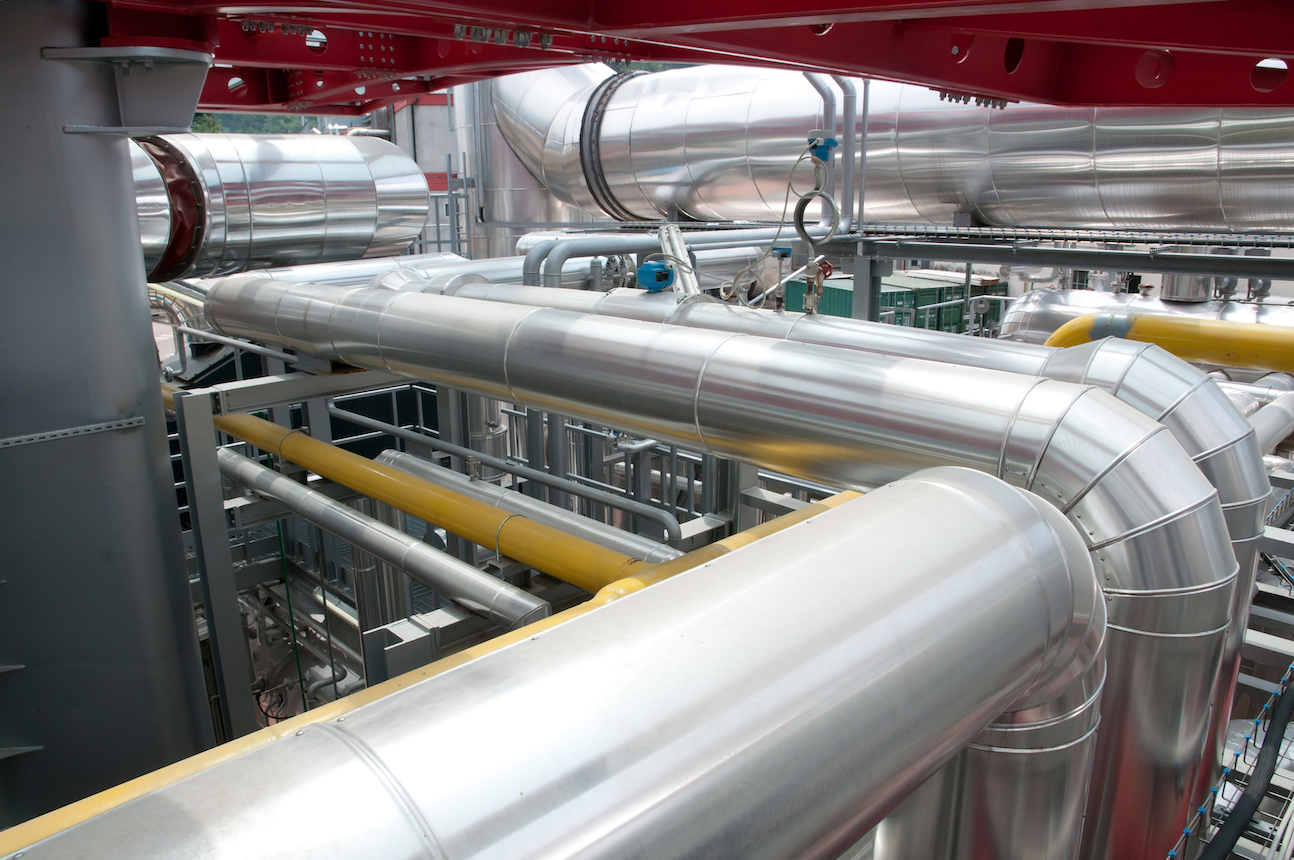
In the kiln zone
When Belgian mining company Argex wanted to replace the support roller units on its rotary kiln, it looked to long-time supplier SKF.
In the green Flanders countryside just 10 kilometres south of Antwerp in Belgium, the Argex factory sits on the banks of the river Scheldt. A cement factory on the other side of the river opened up the site in 1965 to experiment in the production of expanded clay granules from the clay mined from a nearby pit. The cement factory has closed now, but Argex, founded in 1965, continues – mining around 1,000 tonnes of clay every day for a production capacity of 500,000 cubic metres of expanded clay granules every year. “Argex expanded clay granules are a lightweight aggregate multipurpose building material that has many different potential applications,” explains Johny Bultheel, plant manger at Argex. “It can be used as filling for civil engineering projects such as roads, lightweight blocks, railways and waterways and is also excellent for sports fields, garden terra-cing, insulating floors and industrial products.” Argex’s business is B2B, with 95 percent of production going to building and construction applications. The remaining 5 percent is used for landscaping and hydroculture. Some 50 percent of the total production is exported to neighbouring countries and to a few countries outside Europe. The raw clay is mined from the neighbouring clay pit. “We take out around 1,000 tonnes each day,” says Bultheel, “but the pit is good for another 25 years, so we won’t be thinking about having to ship any in for a few years yet.” It is mixed with iron oxide and sometimes thinned with water to obtain the right consistency before being extruded and chopped, ready for baking. The granules are baked in a two-part rotary kiln, an enormous tube that is 76 metres long and turns day and night, processing around 50 tonnes of granules every hour with a production capacity of 1,800 cubic metres per day. This is the biggest kiln of its type in Europe, standing out against the sky in the flat landscape. Heated using lignite, the kiln runs for two to three months at a time before being stopped for a maintenance interval of two to four weeks. The pieces of clay are firstly conveyed into the drying oven part of the kiln, which rotates at a speed of one r/min. The granules spend around 2.5 hours here, at a temperature of 300 to 800 degrees Celsius. They are then conveyed into the second part, the burning kiln, which rotates at 5.2 r/min, where they are heated for 30 minutes to a temperature of 1,100 degrees, causing expansion to take place. The expanded clay is then conveyed into a fluidized cooler where it is air-cooled to a temperature of 80 to 100 degrees Celsius. The drying process naturally breaks the granules into different sizes, ranging from one to 25 milli-metres in diameter, each size having its own specific target usage. They are sorted and then moved onto stockpiles. The kiln is supported by eight support roller units, each containing two bearings. Historically, these were equipped with bushings or sliding bearings, but three years ago Argex decided to replace the support roller units, beginning with a first set of two. “The main reason for this is the safety issue stemming from the unreliability of the sliding bearings,” explains Bultheel. “When we restart the kiln after replacing the support roller, the bearings have to be aligned absolutely perfectly. If this isn’t done accurately, the lubrication doesn’t function correctly; they can heat up the lubricant and ignite.” Indeed, the Argex plant has seen two roller fires in recent history due to misalignment in the bushings. Sometimes this overheating happens immediately, but other times it can take a week before the problem is detected. Then, production must be shut down while the necessary adjustments are made. Moreover, the skills needed to adjust these older sliding bearings are gradually being lost as the workforce is renewed over time. “Another driver for converting to roller bearings is energy consumption, which is something we always keep an eye on,” says Bultheel. “We were looking for a more modern solution with a better lubrication system and thus lower friction that could help reduce costs.” So, Argex turned to SKF. “An SKF bearing solution was the obvious choice for us,” Bultheel says. “We were already a client, and in any case, SKF is the best; we didn’t feel we needed to look anywhere else.” The project was begun in 2008 under the supervision of George Cant from the mainten-ance department. The study took some time as SKF was asked to supply not just the bearings, but also the support roller and shaft, housings and base plates, with exactly the same overall dimensions as the previous solution, to facilitate and minimize the cost of the installation. The new support roller units, each weighing some 23 tonnes, were installed in August 2010. The units are also equipped with an automated SKF lubrication system. “From the moment we agreed on the deal, everything went perfectly smoothly, and since we installed them, the bearings have worked perfectly,” says Bultheel. “What we wanted from SKF was a simpler, more reliable solution. In addition, this new bearing system reduces energy consumption by up to 10 percent. Given the significant investment we’ve made, we’re hoping for as long a life from the roller units as possible.” Argex is currently looking to replace the second set of support roller units on its rotary kiln and hoping to strike a deal with SKF to do so very soon.