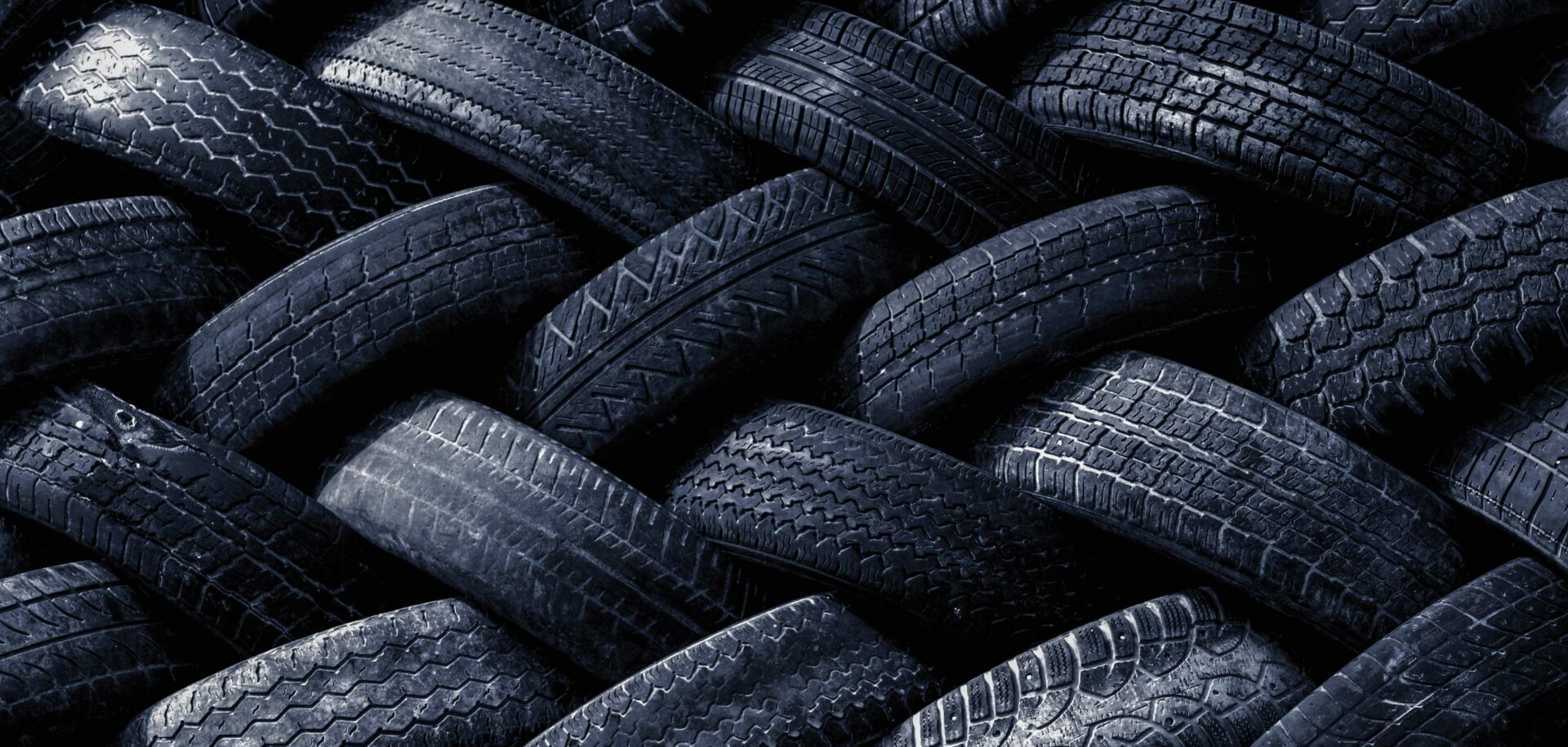
Waste reaction
A Swedish entrepreneur turns waste such as used automotive tyres and plastics into gold. Black gold!
On the inlet side of the patented reactor, a screw conveyor feeds shredded waste tyres into the machine. On the outlet side, a spigot on the machine spews light crude oil into a tank.
This is Brent-quality crude oil, or better. We are ready with the technology. In two years, we’ll be able to deliver 20 of these reactors annually.
Anders Olsson
founder of Cassandra Oil
“This is Brent-quality crude oil, or better,” says Olsson, referring to a trading classification of light crude oil. He holds up a bottled specimen as if it were a fine liqueur. “We are ready with the technology,” he says. “In two years, we’ll be able to deliver 20 of these reactors annually.”
Cassandra Oil’s business model is to make eco-oil from scrap – and charge a premium for it. The name “Cassandra” stems from the Trojan princess in Greek mythology who was known for her prophecies. For Olsson, his 20 colleagues and various financial backers, recycling the world’s hydrocarbon-based waste into usable crude oil is an enticing dream, laden with potentially stupefying riches and environmental goodwill.
Could this be a solution to the islands of plastic floating around on water, the tar sands problems in North America, the oil lakes in the Middle East, the mountains of used car tyres visible from space?
It could be part of the solution at least, says Olsson. “What we need is scale,” he says. The reactor in Västerås, however, is ready and available for delivery.
“Like any business we need to be single-minded, think long-term and be patient.
“In the Western world, we consume one tyre per person every year,” he continues. “That’s one billion tyres! The handling and disposal of used tyres poses a monumental environmental problem, and until now there have been no viable technol-ogies for recycling tyres. As a result, our planet is cluttered with mountains of them.”
Olsson holds patents to 15 innovations. He has also been involved in exporting various products to the Middle East, which is where he saw the need for oil decontamination technologies. He envisions using the CASO reactor as a mobile recovery unit for oil shale and oil sands as well as for the spillage and discharge caused by oil exploration. It could also be applied to the recycling of electronic waste.
The CASO reactor could be packed into two or three shipping containers for deployment anywhere in the world within a few weeks, Olsson says.
For the moment, though, Cassandra Oil’s business concept is to produce environmentally friendly processing plants for the recovery of oil and gas from more easily accessible and hydrocarbon-rich materials such as tyres and non-PET plastics, and to establish partnerships with market-leading waste management companies.
“On the one hand, the supply of raw materials is considered to be almost inexhaustible,” Olsson says. “On the other, the recovered oil can be sold at a premium on the open oil market because it is environmentally friendly, or directly to energy-intensive industries, as well as used for production of oil-based products such as new plastic, tyres or diesel.
“Cassandra Oil aims to be an im-portant link in this new global circular economy where hydrocarbons get re-cycled,” says Olsson.
Cassandra Oil is listed on Nasdaq First North, Stockholm.