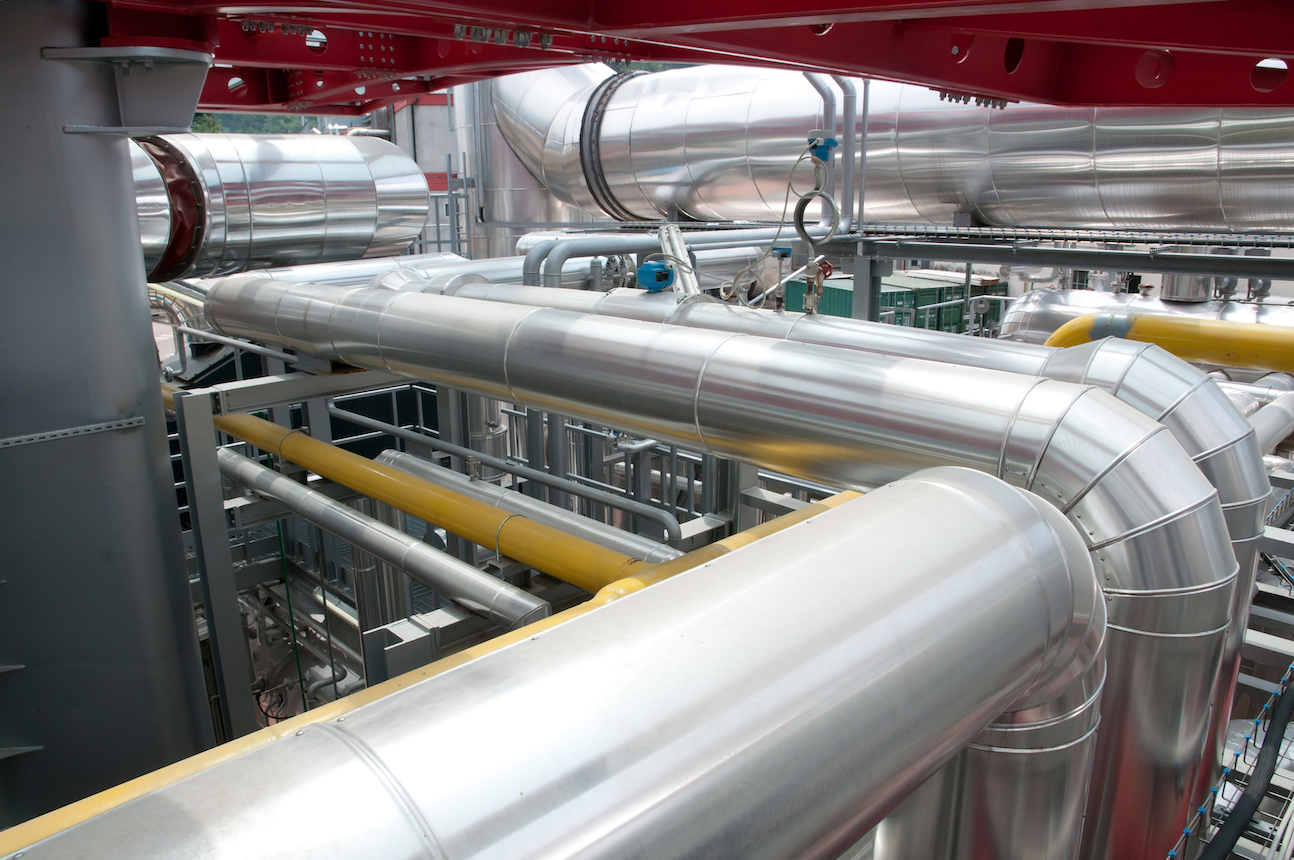
A steady flow
The Swedish state-owned company Vattenfall is one of Europe’s largest electricity producers, with operations in the Nordic countries, Germany, France and Britain. To prevent unplanned and costly turbine stoppages at its facilities in Trollhättan, Sweden, it relies on SKF condition monitoring.
Vattenfall’s Magnus Carlson looks out over the fast flowing river Göta älv. The river, which originates in Sweden’s largest lake, Vänern, and stretches all the way to Gothenburg and out into the sea, carries the greatest volume of water of any river in Sweden. A few hundred metres upstream, wedged into the mountainside, stands Hojum hydroelectric power station, which the water flowing past us has travelled through. “Every drop that goes past here has been converted to energy,” Carlson says. “That’s renewable energy that hasn’t affected the water quality. It feels good to work with hydroelectric power, especially these days when energy and environmental issues are being so hotly debated.” Carlson is Vattenfall’s head of operations and maintenance for its hydropower stations in southern Sweden. His office is located in Trollhättan in south-western Sweden, a historic location. It was here that Vattenfall, a state-owned company and one of Europe’s leading energy companies, had its origins a little more than 100 years ago, when Kungliga Vattenfallsstyrelsen (Royal Waterfall Board) was created. And it was here that one of the first large hydroelectric facilities, Olidan, was built at the start of the 20th century. In the ruddy brown brick building standing behind Carlson most of the original Olidan turbines are still spinning despite more than 100 years of service producing energy for Sweden. At the beginning of the 1940s, the Hojum hydroelectric power station was added a short distance away from Olidan. Due to the political instability in Europe in the late 1930s and early 1940s, it was constructed underground. It’s equipped with more modern, vertical Kaplan turbines (as opposed to Olidan’s horizontal Francis-type turbines). The three turbines at Hojum together produce about 1,000 GWh during a typical year, and they are currently in the process of receiving an upgraded condition monitoring system, produced by SKF. “Over the years we’ve had very few breakdowns, but we have also been extremely conscientious about taking care of our equipment,” Carlson says on the way into the cavern under Göta älv. “An unplanned stoppage has extremely serious consequences, and for this reason monitoring is extremely important. As a result we’re currently upgrading the condition monitoring system of the turbines at Hojum.” The three turbines are equipped with plain bearings and run at 136 revolutions per minute, making them relatively slow moving compared with many other types of rotating machinery. SKF condition monitoring engineer Björn Mathiasson explains that the SKF IMx collection units now need to be upgraded and supplemented. The software Vattenfall uses, however, is already up to date. “We’ll finish with accelerometers along with additional displacement sensors, which will enable a better and more detailed overview,” he says as he picks up a sensor that is lying on a stool, ahead of being fitted. There’s a muffled hum from the monotonous operation of the turbines. The space around them is clean and tidy, with every loose tool and object standing or hanging in its marked place. Nowadays, ongoing condition monitoring is conducted remotely, meaning it’s never necessary to have personnel in the underground cavern. By simultaneously measuring vibration levels in all directions you get a meticulous snapshot of how the shaft and bearings are behaving. The system can detect the smallest change in the machine condition and stop the machine when the operating conditions are inadequate or when sudden damage occurs. Then the analyzing program compiles all the data in a graphic image. “We have enjoyed a long and fruitful collaboration with Vattenfall,” Mathiasson says. “And we’re dependent on their feedback. The relationship with Vattenfall has definitely been significant in terms of our development work.” One such area has been the development of new features in the software for online monitoring, SKF @ptitude Observer. Mathiasson displays diagrams of the various measurement points on the screen in the control room and explains that when the system’s alarm sounds Vattenfall conducts the first check. If required, SKF is contacted to continue the investigation.
Out in the sunshine again, the roar can be heard from water gushing forth beneath the power station. Carlson believes that hydroelectric power will become increasingly important as society develops other renewable energy sources, such as wind and solar power. Energy is a perishable product that must be produced when it’s required, and both wind and solar energy are subject to external factors over which we have no control. “It’s not always sunny and the wind isn’t always blowing,” he says. “Hydroelectric is likely to become a prerequisite for large-scale conversion to renewable energy because it can complement other energy sources and enable a more even production of energy.” @ptitude is a registered trademark of the SKF Group. SKF’s remote condition monitoring service consists of equipment for data acquisition, software for the easy-to-survey management of information, and SKF maintenance services for expert analysis. Data collection can be conducted using SKF Microlog mobile equipment for inspection patrols or alternatively using SKF IMx’s permanently installed sensors that conduct continuous measurements and transmit information on anomalies and changes, as well as logging data for long-term analyses. The @ptitude Software Suite helps with the diagnosis and analysis of measurement data, as well as the communication of important information over the Internet and support for planning and decision making.Remote condition monitoring