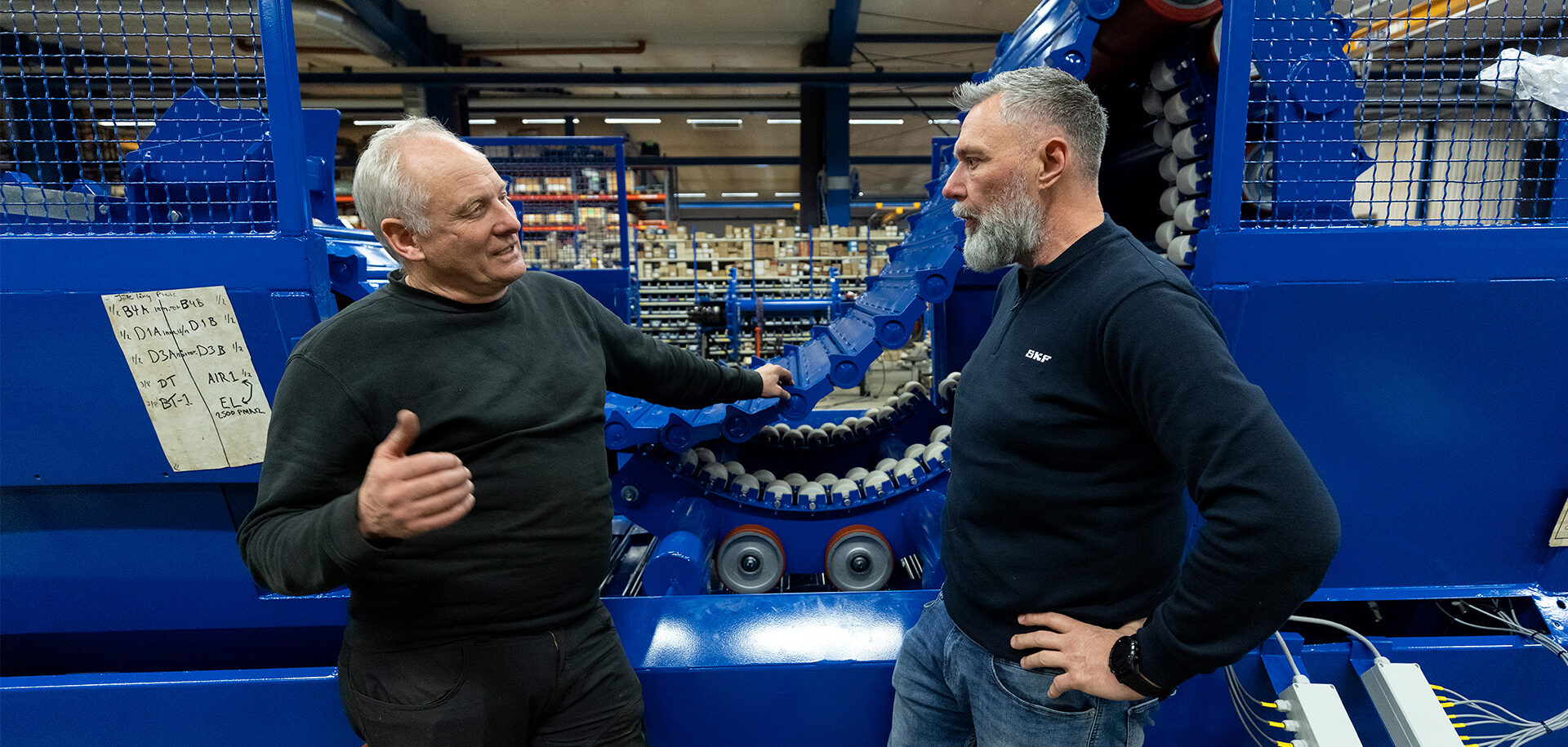
Bearing solution enhances life of compression baler
SKF’s three-barrier solution used in Flexus Balasystem’s baler simplifies maintenance for customers.
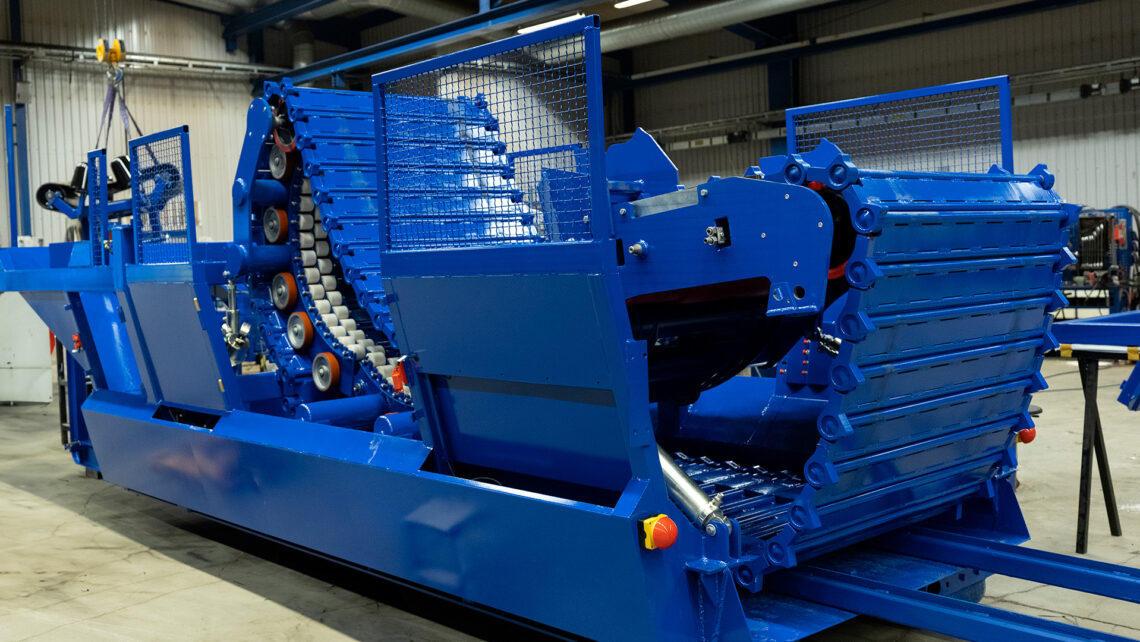
Swedish company Flexus Balasystem is working with SKF on a bearing solution for its compression baler that combats grime, the most common cause of baler breakdown, and minimizes maintenance.
Central to the Flexus Balasystem baler is a patented flexible metal chain that compresses waste. This metal chain is the baler’s most delicate component, requiring a good bearing solution and careful maintenance.
“The company is now testing a sealed ball bearing, developed in collaboration with SKF, that is does not require relubrication and therefore is maintenance-free,” says Bo Ansbjer, CEO and owner of Flexus Balasystem in Nossebro, Sweden.
Now, we’ve minimized the need for lubrication, since the new bearings are sealed and maintenance-free.
Bo Ansbjer, CEO and owner of Flexus Balasystem
The company has been manufacturing all-in-one compression balers, primarily for waste management, since 1993. Waste management in particular places stringent requirements on the robustness of the machinery at all stages. Being able to handle various types of waste is not enough, since other materials also end up in the baler. Combating these various materials was the greatest challenge for Bo and his brother Jan when, together with their employees, they developed their first prototype.
“We began testing and didn’t actually have a blueprint,” Bo Ansbjer recalls. “We drew the first sketches in the dust on the floor.”
In 1993, the brothers applied for a patent for their technology: a round baler – the only one of its kind in the world – for compressing and baling materials including waste. The patent applied to the compression chain and the unique driver.
“What makes it unique is that when the chain rolls the material together, the heads move along with it, which allows for better compression and cylindrical bales,” Ansbjer says.
Since its start, Flexus Balasystem has manufactured some 220 balers, exporting them to about 50 countries around the world. The company’s round baling technology for waste remains unique to this day. The company manufactures some 10 round balers each year, says Ansbjer, and the order book is full for at least six months.
The basic design has stayed the same over the years, but the chain that compresses the material has been changed and improved. The chain consists of multiple small segments attached with bearings, allowing the chain to flex like a wave and compress the material.
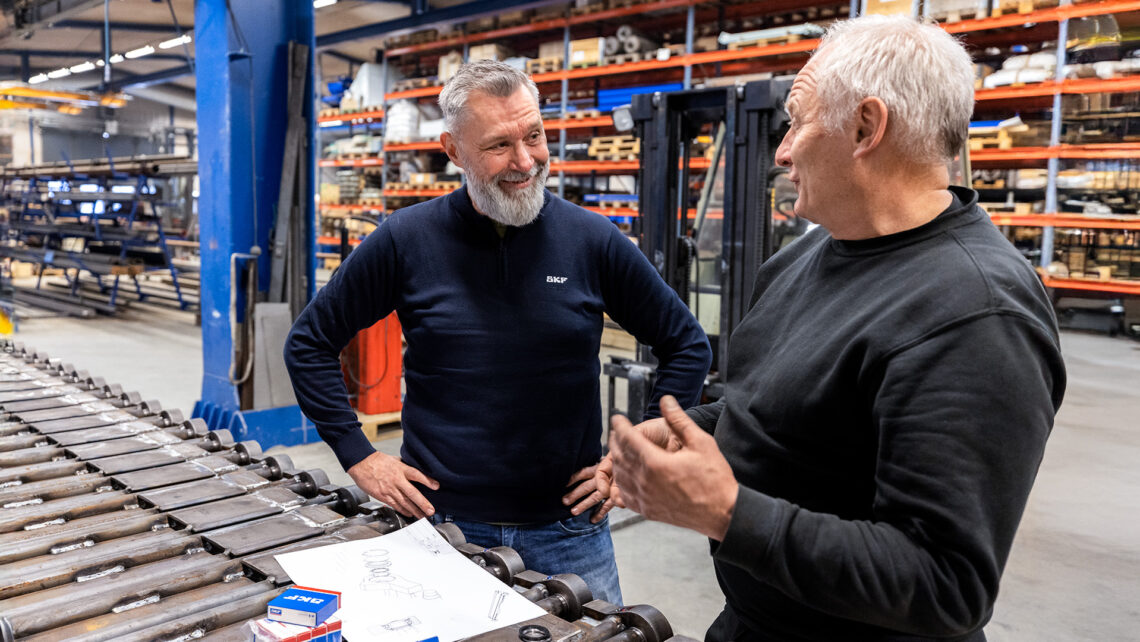
New solution
One of the main challenges has been extending the service life of the chain. The bearing solution is important, but how the end customer maintains the equipment is equally important.
“We have set the requirement that a chain should be able to process 50,000 bales before it needs to be replaced, but depending on how the customer handles maintenance this figure could vary from 20,000 to 150,000 bales,” Ansbjer says.
Previously, high-capacity double-row spherical roller bearings were used, but these required regular lubrication of the nearly 200 lubrication points along the chain.
Now, Flexus Balasystem has developed a solution in collaboration with SKF in which the spherical roller bearings have been replaced by double-row self-aligning ball bearings, with the same dimensions but lower capacity. The bearings are filled with grease and sealed to keep out grime. In addition, the bearings are encapsulated in grease, creating an additional seal, a “three-barrier” solution that simplifies maintenance work for customers.
“Now we’ve minimized the need for lubrication, since the new bearings are sealed and maintenance-free,” Ansbjer says, explaining that SKF proposed this customized solution to meet the requirements identified by Flexus Balasystem and SKF.
Recently, Ansbjer ordered 5,000 double-row self-aligning ball bearings from SKF. He explains that the SKF bearings provide the good quality and good functionality that are critical. “Price is always part of the discussion,” he says, “but if we find an effective solution in collaboration with a partner whose prices are not completely outrageous, we’re not going to run to a neighbouring supplier to try to get an even lower price.”
Ansbjer says he also appreciates that SKF was closely involved, working to learn about his company’s products and to find new solutions. “Naturally, they want to make a sale and earn money, but we have had good communication and can now try new and exciting ideas that we came up with together.”
The SKF three-barrier solution
- Outer seal – the first line of protection against grime and contamination
- Grease-filled housing – grease in the housing cavity provides a second protective barrier
- Bearing seal – the bearing seal is the final barrier, the purpose of which is to retain the bearing’s lubricant and keep contaminants out.
The SKF three-barrier solution
Outer seal – the first line of protection against grime and contamination
- Grease-filled housing – grease in the housing cavity provides a second protective barrier
- Bearing seal – the bearing seal is the final barrier, the purpose of which is to retain the bearing’s lubricant and keep contaminants out.
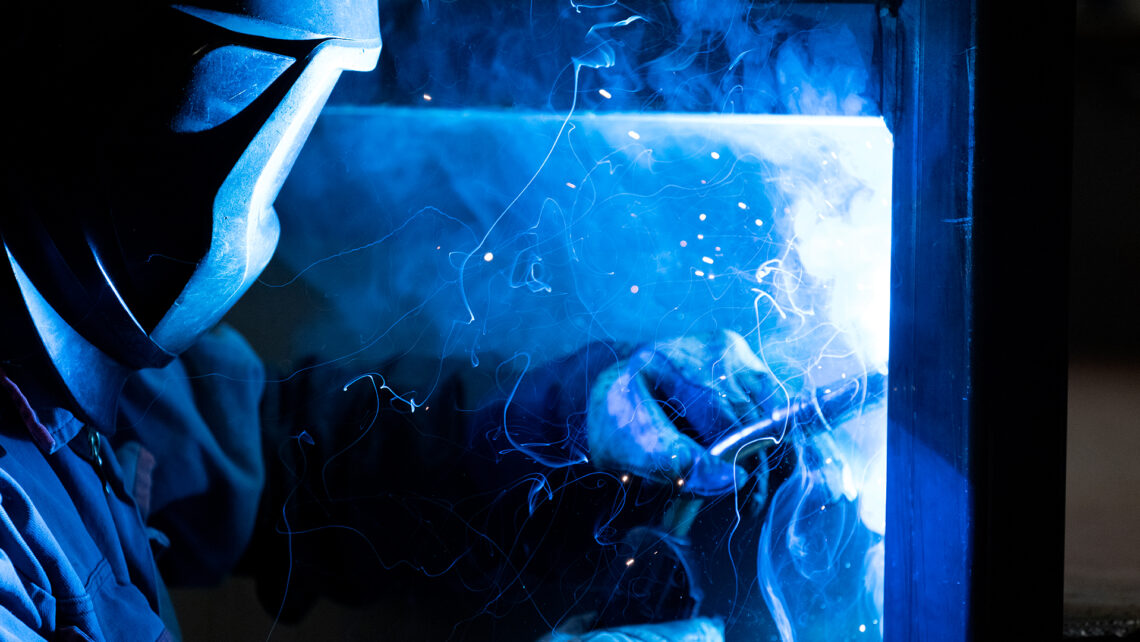