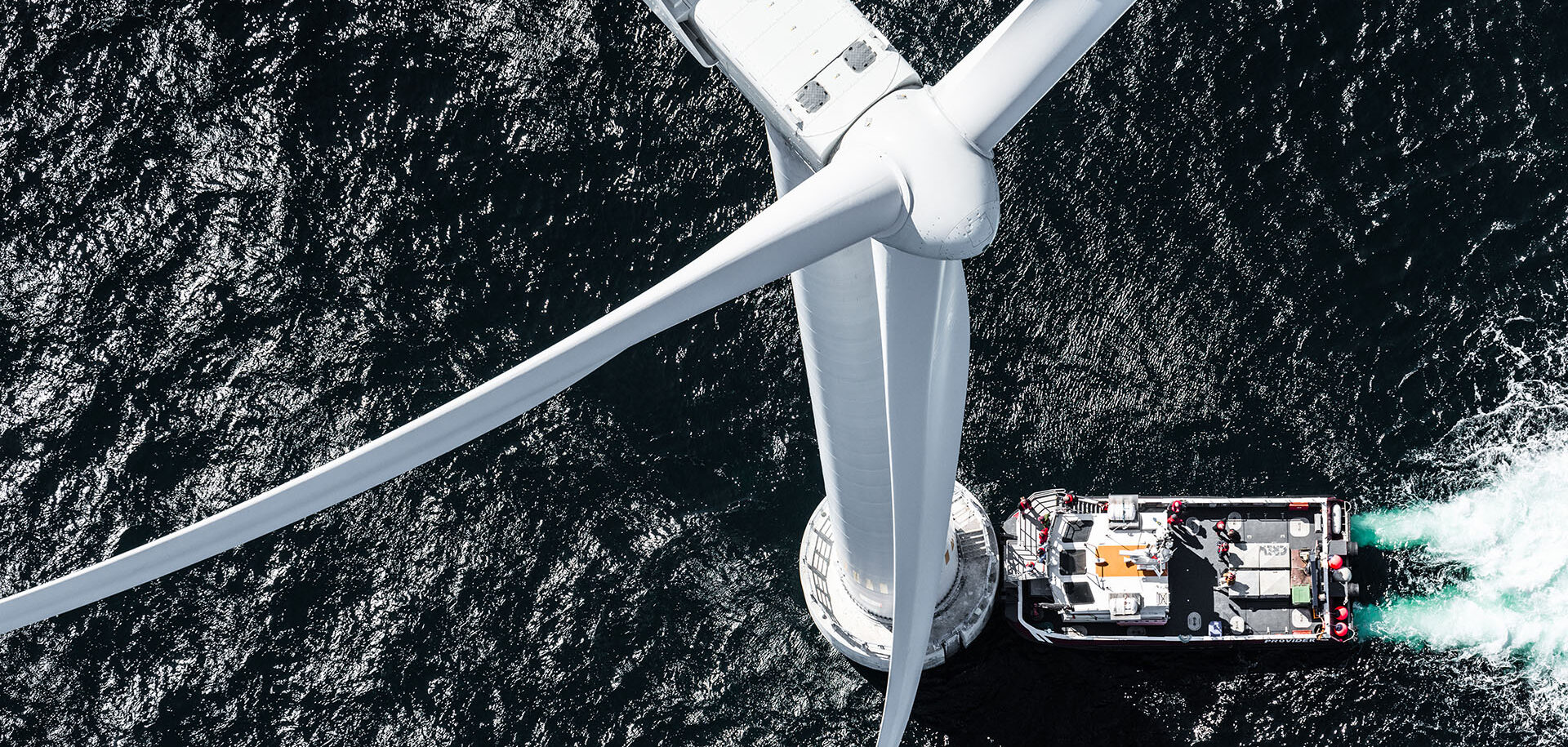
Boosting wind power with SKF condition monitoring
Green energy company RWE deploys condition monitoring across its network of wind turbines as it looks to take operations and maintenance completely in-house.

Wind power is on the rise and is an increasingly important part of the energy mix. In fact, the UK generated more electricity from wind farms than it did from gas-fired power plants in the first quarter of 2023, the first time this has happened.
The rise in wind power relies squarely on wind turbines and their ability to generate electricity smoothly and efficiently. This encompasses a multitude of factors, including design, engineering and operations & maintenance (O&M).
A condition monitoring system (CMS) is a well-established technology for maintaining performance on wind turbines, but this was not always recognized. “The use of CMS within the wind turbine sector has now reached a significant level of maturity,” says Rusmir Bajric, lead expert in CMS at RWE Offshore Wind. “However, I remember a time when it was questioned whether such systems are even needed.”
That, he says, is now history. Collecting data is vital to the smooth running of a wind farm at sea because of the benefits it can bring.
“Assets are large and any downtime is costly,” he says.
RWE has deployed more than 1,000 of SKF’s IMx units globally across its fleet of wind turbines. These collect “health” data on moving parts, such as bearing vibration, temperature and other metrics. Data gathering is crucial, but it is only beneficial if it can be analysed properly.
“As our wind turbines portfolio has increased, so has the amount of data that we have to process,” he says. In order to raise productivity – a key factor for RWE – the company’s O&M team was requesting higher quality data. This meant more precision, using the data to predict problems more accurately. “The O&M team requires a minimum of false alarms, aiming for zero misdetection of issues if possible,” Bajric says. “However, it can be a challenge to cope with so much data and the high industry requirements.”
This is what the IMx units are there to do. They typically monitor components on the drivetrain, proactively looking for faults that can be corrected before they turn into problems. It is well known that maintenance accounts for a huge chunk of the cost of running a wind turbine. Minimizing this – by avoiding catastrophic failure, for example – is a critical factor behind efficient and profitable operation.
In-house maintenance
Maintenance is a critical process in wind energy. Large, rotating mechanical parts will inevitably fail over time, due in part to the harsh conditions. CMS helps to spot these signs as early as possible and is a critical factor behind RWE’s quest to support its O&M in-house. “Increasingly, we want to maintain and operate our wind assets by ourselves,” says Bajric. This means that RWE is responsible for the data flow from the sensors and how it is interpreted.
“The network, data infrastructure and data postprocessing are controlled completely by us with background support from SKF,” he says. This is a service that SKF often offers to its customers. In this case, RWE wants to break away from that. However, it does not mean that SKF has no involvement in the process.
“We want to stay on top of the latest version of the software and firmware, so we have better data collection and interpretation,” Bajric says. “We also want to stay connected to SKF, to exchange best practices and to integrate the data acquisition pre- and post-processing. This is the benefit of the collaboration.” There are several elements to this. SKF organizes training for RWE engineers, for instance, to help them improve their predictive maintenance capabilities.
There is also technical support. Bernd Heintz, condition monitoring engineer at SKF, says: “We know how our software works. We use workshops to get to know each other and to develop the standards that have been applied.”
Ongoing software upgrades can help to overcome “pain” points. “The latest version allows us to follow up certain damage cases and detect issues,” says Heintz.
SKF’s pedigree as a manufacturer of engineering components means that the agreement with RWE also includes the supply of a range of spare parts as well as stock rationalization and optimization and advanced mechanical engineering services.
For Bajric, the partnership with SKF is one of continual improvement. “We both accept the challenge of improving the wind turbine CMS,” he says. “We need to better understand and handle the data we are collecting. Better interpretation of data can help us to be more proactive and productive.”
Early warning
Early notification of problems is a critical benefit of using condition monitoring. In the wind industry, it is about much more than detecting early health warnings on a bearing.
Bajric explains, “It’s not beneficial for offshore wind farm operators to be told that a problem needs fixing immediately. Issues need to be flagged up in advance, so that maintenance can be scheduled in.”
RWE identified the need for this type of notification and has worked with SKF to close the gaps that were there and make the process more efficient.
The two companies are currently discussing the latest version of the software and how it can help to close these gaps. This is done to avoid failures, which can lead to such serious problems as a split gearbox. In this case, it is possible that oil from the gearbox could run from the nacelle and down the tower.
“The challenge is to receive very early notification that will prevent this,” he says. “This is one of our goals.”
Data is critical
For an engineering-based business such as RWE, information is critical to improving operations. “In the newest projects, we’ll have a very high-quality CMS that is proactively designed,” Bajric says. “Collaboration with internal CMS engineers will allow RWE to be more proactive in integrating that data.”
CMS can quickly provide insight into an asset’s condition, Bajric says, and the data can be used to employ a proactive maintenance programme. “Without data, we can’t really design any kind of maintenance philosophy or technique,” he says.
RWE has gone far beyond the point of weighing up the pros and cons of CMS, Bajric says. “Our industry is now mature enough not to make the mistake of running assets without CMS,” he says. “This is especially the case in offshore maintenance, where knowing the condition of the components is key to running the wind farms – staying competitive and operating and maintaining assets with minimum cost.”
Open platform
A key reason that RWE chose SKF as a partner was that its CMS platform – IMx units and the underlying software – is very open to end users, says Rusmir Bajric, lead expert in CMS at RWE Offshore Wind.
“SKF’s CMS support was open to collaboration,” he says. “It meant we could adapt it to what we needed. The hardware and software capabilities of IMx helped us detect or prevent problems much more proactively and with better accuracy.”
RWE uses mainly IMxs that are specially designed for the wind industry. These are designated IMx-W. Some of RWE’s turbines have recently been retrofitted with IMx-W and IMx-8/8 units. The IMx-W version uses the same CPU as standard units and is broadly comparable to them. However, the wind industry has a number of special certifications, which are fulfilled by IMx-W/8/16.
Bernd Heintz, a condition monitoring engineer at SKF, explains: “They’re perfectly designed for vibration data and connecting with tacho units. They also have special cabinets that are robust enough to withstand wind industry conditions.”
A typical example is the Multilog IMx-W, which has 16 analogue signal inputs. The dynamic signal inputs are configurable for a variety of sensors. With SKF @ptitude Observer software, the Multilog IMx-W can provide a complete system for a variety of tasks. These include early fault detection and prevention, automatic advice to correct existing (or impending) conditions, and advanced condition-based maintenance to raise reliability, availability and performance.