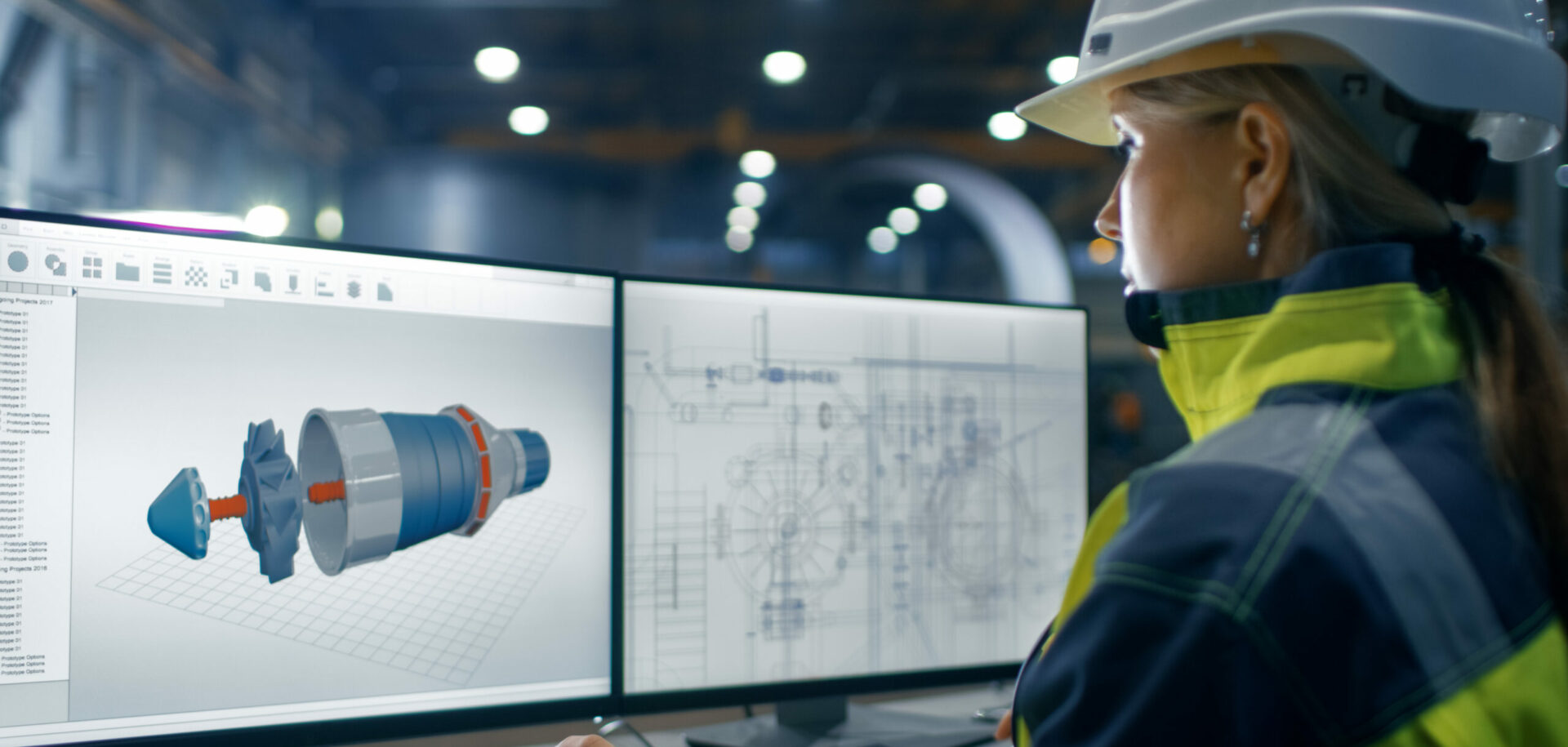
Damage mechanisms of indentations in raceways of rolling bearings
Indentation marks in rolling bearing raceways are known to be a source of surface damage, resulting in shorter bearing service life. SKF bearing life calculation has taken account of this for many years using the ηc contamination factor. Recently, SKF has developed advanced models and conducted experiments to predict the interaction of scratches and indentations, and the lubricant present in the raceways. This article explores in detail these interactions and the effect of sliding, to give a unique insight into the way the damage process takes place.
Overrolling of solid particles can produce surface indentations of raceways in rolling-sliding lubricated contacts. These indentations are known to increase the risk of contact failure. The failure process may be influenced by the amount of sliding present in the contact, gears being different from rolling bearings. In order to increase the understanding of the failure process and to develop preventive measures, a detailed analysis of the dynamic behaviour of indentations in rolling-sliding heavily loaded lubricated contacts has been carried out. The effect of pressures, stresses and surface distress around the indentations has been analyzed and the prediction of damage compared with experimental results. Studies of the influence of sliding in the contact have shown that for low sliding conditions, typical for rolling bearings, the failure process is dominated by film thickness reduction and surface distress around the shoulders of the indentation, while for high sliding (gears), a fatigue process due to superposition of two waves of pressure ripples is more likely. Surface geometrical disturbances (e.g., scratches, indentation marks, etc.) are known to be a source of damage in rolling-sliding heavily loaded lubricated contacts. These contacts generally work under elastohydrodynamic lubrication (EHL) conditions, but sometimes mixed lubrication can take place. The contacts are found in many machine elements, including gears and rolling bearings. Surface imperfections can generate local film thickness fluctuations and pressure ripples, causing stress concentrations. Surface stress induced by geometrical features passing through Hertzian-like (EHL) contacts have been studied by many researchers in the past with the use of numerical, experimental and semi-analytical methods. Current industrial trends of downsizing, low energy consumption and higher operating temperatures tend to increase the surface stress in rolling bearings. Thinner film thicknesses, higher (or very low) speeds and dynamic conditions in rolling bearings are common. All these factors are likely to increase the risk of bearing failure from raceway imperfections such as indentations. Oil cleanliness in bearings is an important factor to maximize durability. This is why the SKF bearing life model [1] and the ISO 281 standard [2] include lubricant cleanliness as an input parameter in bearing life calculations. In a previous article [3] the effects of lubricant cleanliness and its impact on bearing life have been discussed; here, a more detailed description of the indentation mark and lubrication conditions of the bearing raceway contact will be considered. Many authors have previously worked on the topic using lubricated and dry contacts and low and high sliding values, giving a rather unclear overall picture of the failure mechanism. Cheng et al. [4] carried out an experimental investigation on crack development in the region of artificially produced indentations in rolling-sliding contacts, such as dents and grooves under EHL lubrication conditions with a sliding factor S = ±0.24, i.e., S = 2 (u2-u1)/(u2+u1). The analysis was complemented with some numerical simulations using non-Newtonian fluid that showed that sliding changes the position and magnitude of the pressure ripple around the indentations, becoming higher in the front (leading edge) of the dent when the dented surface is travelling slower than the smoother one, and vice versa (see fig. 1 for nomenclature). Nélias and Ville [5], Ville and Nélias [6] have carried out numerous experimental observations and numerical simulations of indentations in EHL contacts with conditions of pure rolling and rolling-sliding. The numerical simulations in Nélias and Ville [5] with Newtonian fluids showed that any increase of sliding increases the maximum shear stress underneath the contact (e.g., higher sliding and higher friction as follows from a Newtonian fluid). It was observed that the higher the sliding imposed on the EHL contact, the higher the maximum shear stress in the subsurface and therefore the shorter the life around the indentation. In Ville and Nélias [6], further experiments were conducted and some simulations also carried out for S = ±0.015. The experiments confirmed earlier conclusions that the preferred site for spalls to develop depends on the friction direction. A dented slower surface tends to develop a spall at the leading edge of the dent, whereas a dented faster surface tends to develop the spall at the trailing edge of the dent. For pure rolling conditions, it is argued that the spall could appear on either side. From dry contact experiments (Xu et al. [7]) it was observed that the spall appears in the back side (trailing edge) of the dent on the driving surface; thus Xu et al. concluded that it is the friction force on the surface that is the main mechanism promoting spalling of dented surfaces. The basic indent geometry has been idealized in fig. 2. Assuming that the particle is entrapped in the contact (very large particles are not entrapped and very small particles go through the film without causing indentations), different indent shapes are produced – depending on the hardness of the particle, its geometry and the hardness of the indented material. Indentations of large size (ø) or very deep (hp) and with large shoulders (sp) are the most dangerous. Fig. 3 shows different particle characteristics associated with the corresponding indentations. Soft or malleable (ductile) particles (fibre or metal) produce shallow indentations with shoulders. Brittle, hard particles shatter into many very small particles and produce a cluster of tiny indentations. Friable tough particles produce a large agglomerate of material that dents the steel, producing sharp shoulders. To better understand the interaction of indentations with surrounding lubricant entrapped in a heavily loaded contact, SKF has developed detailed models and conducted experiments [8, 9] to study the phenomena associated with this problem. Here, the process of an indentation or any other geometrical surface disturbance entering the contact is described. Surface geometrical disturbance entering the heavily loaded lubricated contact When a surface disturbance enters the EHL contact, it generates two different pressure and film thickness waves. The first one is the associated pressure wave produced by the steady-state elastic deformation of the surface disturbance. This wave is accompanied by an opposite wave in the film thickness, and it travels inside the contact with the same speed as the surface that produces it (e.g.,u2); it is called “particular integral”. The second wave is produced by the disturbance at the inlet of the contact, since any geometrical disturbance on one of the surfaces will act as a flow valve regulating the lubricant flow that enters the contact. This wave has film thickness and pressure ripple components that are propagated inside the contact with the average speed of the lubricant ( ū = (u2+ u1)/2). Called the “complementary function”, the final pressure and film thickness ripples are the combination of those two components (fig. 4). Low sliding conditions are typical for the centre of raceway rolling bearing contacts (S < 0.05). Using the detailed SKF model, it is possible to simulate the passage of an indentation geometry through a heavily loaded lubricated contact and calculate the generated deformed geometry inside the contact and the generated pressure ripples. Fig. 5 shows the initial “model” indentation imposed on the upper contact surface and the centre-line profile of the isolated deformed indentation and the generated pressure ripple at the centre of the contact calculated under pure rolling conditions. Increasing slightly the sliding in either direction (–0.05 < S < 0.05) will considerably alter the results. Fig. 5 shows that the film thickness deformed shape exhibits a collapse in film thickness in the frontal part of the dent (leading edge). Slightly higher pressures, however, are found in the back (trailing edge) of the dent. This suggests that when there is a good lubricating film, the indentations are likely to fail first on the trailing edge of the dent, since the pressures are higher and not from metal-to-metal contact in the leading edge of the dent. However, if the lubrication is poor, wear and possibly surface distress can be expected at the leading edge of the dent. This result is in full agreement with the experimental results (fig. 6) carried out at the SKF Engineering & Research Centre laboratory using full ball-bearing tests with artificially made indentations on the raceway. Here, a zone of surface distress (microspalls) can be observed in the trailing edge of the dent while substantial wear occurs at the leading edge, possibly caused by the local film collapse. Moderate sliding conditions (S ~ 0.1) can be present in gear contacts. Using the detailed SKF model with non-Newtonian fluid behaviour (increasing sliding does not increase friction), it is possible to simulate the passage of an indentation in the lubricated contact with these sliding conditions. Fig. 7 shows the isolated pressure ripples, film thickness and subsurface normalized von Mises stresses calculated for a heavily loaded contact with two different moderate sliding conditions (S = 0.1 – lower smooth surface travelling faster than upper dented surface and S = –0.1 – lower smooth surface travelling slower than upper dented surface). It can be seen that for this moderate sliding condition, inverting the sign of the sliding inverts the location of the maximum pressure ripple, and thus the location of the first possible failure. This perhaps explains some apparently contradictory experimental results reported in the literature. High sliding conditions (S > 0.1) are not present in the central part of bearing raceways; however, they may be present in gear contacts. Using the detailed SKF model with a realistic behaviour of the lubricant as a non-Newtonian fluid (increasing sliding does not increase friction) it is possible to simulate the passage of an indentation in the lubricated contact with these sliding conditions as it moves inside the contact. Fig. 8 shows the isolated pressure and film thickness ripples as a function of time for one high sliding condition (S = –0.5 – the smooth lower surface moving faster than the upper dented surface). It can be seen in fig. 8 that the original position of the dent follows the minimum value of the pressure ripple (Δp); however, since sliding is high, there is enough time for the two wave components to separate from each other over time, as both pressure and film thickness ripples. At the latest time (Δt), the film thickness ripple (Δh) generated at the inlet of the contact has already left the contact while the pressure ripple is still inside. Here, the failure of the contact will depend on how the pressure waves overlap and combine in the many cycles of fatigue. The failure could appear quite distant from the indentation. As shown in fig. 6, surface distress (microspalls) is often seen around indentations in rolling bearings (shoulder area). The surface distress in general appears first on the edge where the pressure ripple is the highest. If there is a thicker film thickness, surface distress around the indentation will take a very long time to develop or may never develop. However, if the lubrication conditions are not good, surface distress will easily develop. The surface distress model developed by SKF [9] can also be applied to surface indentations. The model uses the hydrodynamic pressure calculation described in this article but modified to take into account partial lubrication (areas with metal-to-metal contact). In this section, simulations are carried out to show that the surface distress development around indentations has the same physical basis as the normal raceway surface distress in poor lubrication conditions. Experimental and simulation results are shown in fig. 6 and fig. 9. The experimental results are shown in fig. 9a after 2,250 million overrolling cycles. Fig. 9b shows a pressure profile and subsurface stress map along x in the mid-plane. Fig. 9d shows the progress of the surface distress as predicted by the model for this case after 2,250 million overroling cycles. Fig. 9c shows the simulation of the surface distress damage after 750 million overrolling cycles. A comparison with the experimental picture of fig. 6 shows the results are very much alike. Indentations in rolling-sliding heavily loaded lubricated contacts represent a significant risk for the service life of machine elements (e.g., rolling bearings, gears, etc.). In the present study, simulations with the SKF advanced model were performed for the analysis of experiments carried out in full-bearing tests at the SKF Engineering & Research Centre in order to enhance the understanding of the effect of the hydrodynamic pressure fluctuations from dents passing through rolling-sliding contacts. The simulations explain well the presence of the glazed area formed at the leading edge of the contact (see results in fig. 6 compared with fig. 5, showing the prediction of the lubricant film collapse at the leading edge of the contact). The severe surface distress of the trailing edge of the dent is also consistent with the model prediction shown in fig. 5 (with S = 0). Indeed, in all computed cases the trailing edge of the dent is always the one affected by the highest pressure level. It was also observed that for nominal zero sliding, the glazed area of the leading edge of the dent is absent. (See fig. 6 of reference [8].) Instead, a light form of microspalling is generated. This is explained by the presence of a microslip due to the microscopic elastic deformation of the contacting bodies, which in practice also cannot be avoided in the case of Hertzian contacts under nominal zero slip conditions. Under elastohydrodynamic lubrication or partial EHL, due to the piezo-viscous properties of the lubricant and boundary friction, this microscopic amount of slip is sufficient for the generation of the surface traction required for the formation of surface distress (however, it is insufficient for a polishing action). The calculation of the surface distress progression with the amount of overrolling for the case of rolling bearings is shown in fig. 9. Here, it can be seen that the model predictions also agree well with the experimental observations. Only a few experimental microphotographs of dents are shown in the article. They represent the essence of many more tests, the results of which are all consistent with the experimental samples reported here. Therefore, the good match between the model prediction and test results represents a robust conclusion from the experimental validation point of view. From the above observations the following conclusions can be drawn: There are three main measures that can offer a reduction in the risk of generating indentations.
Summary
Understanding what triggers and propagates different types of damage to bearing surfaces can lead to methods to reduce the incidence or severity of such damage. In this article, SKF engineers explain the theoretical and experimental work related to the occurrence and development of indentations. They have created advances to SKF bearing theory models that agree well with experimental results that explain the underlying causes of surface damage. This work also points out the importance of cleanliness, proper bearing mounting and appropriate lubrication in reducing the risk of surface damage caused by indentations.
Indentations produced by different particles
Interaction between indentations and lubricant
Surface geometrical disturbance in rolling-sliding contacts with low sliding conditions (rolling bearings)
Surface geometrical disturbances in rolling-sliding contacts with moderate sliding conditions (gears)
Surface geometrical disturbances in rolling-sliding contacts with high sliding conditions (gears)
Surface distress around indentations in rolling bearings
Discussion and conclusions
Ways of reducing risk of indentations