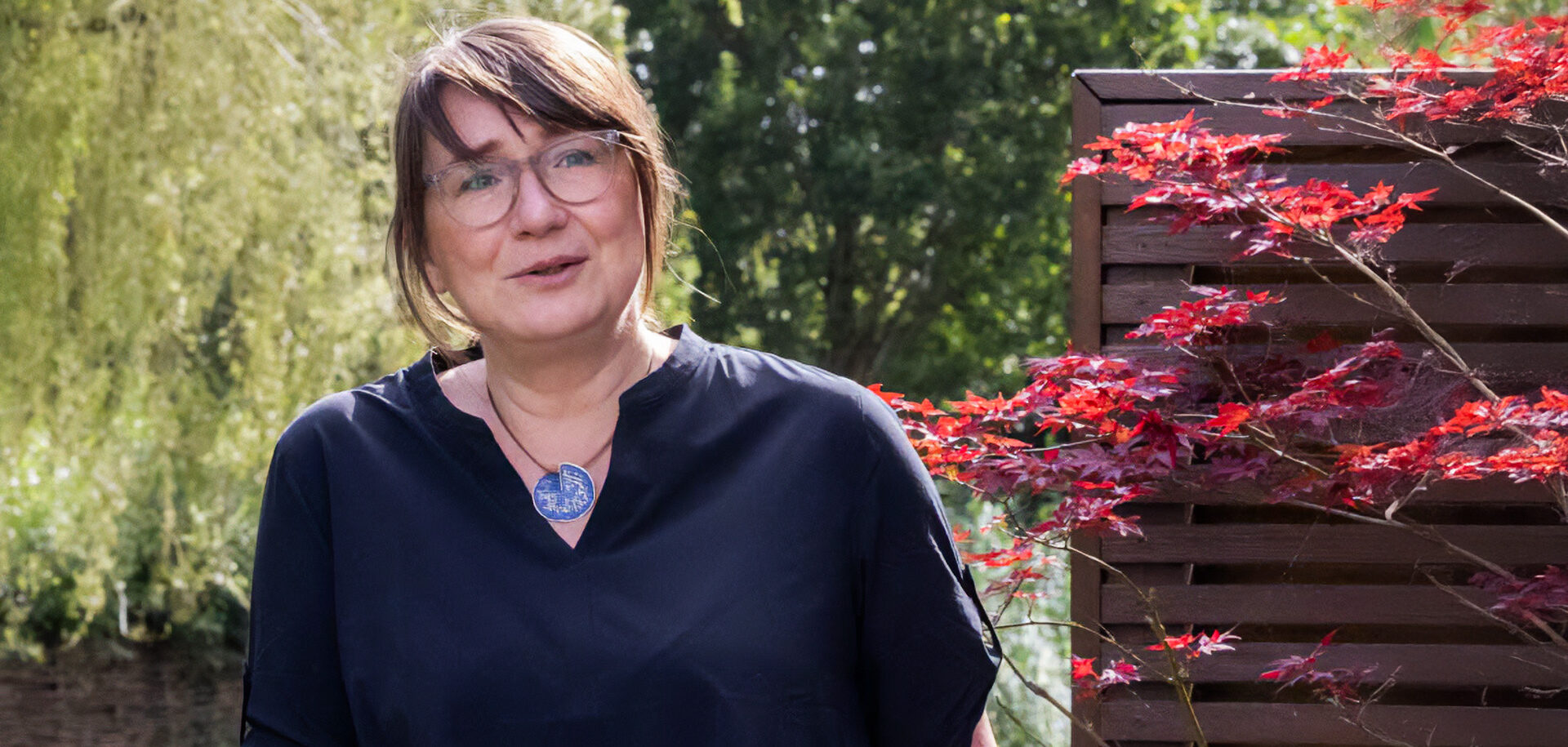
Die Keramik-Revolution
Seit mehr als zwei Jahrzehnten erforscht SKF die Geheimnisse der Hybridlager-Technologie. Jetzt kann das Unternehmen diese hochentwickelte Lösung auch für Mainstream-Anwendungen anbieten.
Im Zentrum dieser Forschungsreise stehen Hybridlager, die sich dank ihrer Kombination aus modernen Keramikwerkstoffen und herkömmlichen Stahlkomponenten in anspruchsvollen Anwendungen als äußerst leistungsstark erwiesen haben. Die Materialwissenschaftlerin Charlotte Vieillard spielt bei deren Entwicklung eine Schlüsselrolle. Sie kam nach Abschluss ihres Studiums zum SKF Forschungs- und Entwicklungscenter in den Niederlanden und brachte ihre Expertise im Bereich nicht-metallischer Werkstoffe ein. Ursprünglich gründete sich der gute Ruf von SKF auf der Verwendung von widerstandsfähigem, hochwertigen Stahl. Vieillard und ihre Kollegen konzentrierten sich jedoch darauf, auch das Potenzial von Keramikwerkstoffen zu nutzen.
Verglichen mit konventionellen Stahlkonstruktionen bieten Hybridlager insbesondere in Hochleistungs-Anwendungen zahlreiche Vorteile (siehe Kasten). So nutzten die ersten Anwender dieser Technologie Hybridlager unter extremen Bedingungen, zum Beispiel als Spindeln in Drehautomaten und Bearbeitungszentren mit sehr hohen Drehzahlen oder in Rädern und Getrieben von Formel-1-Rennwagen.
Im Laufe der Jahre, so erklärt Vieillard, seien Hybridlager dann in vielen weiteren Produkten zum Einsatz gekommen. Das Spektrum reiche vom schubkraftgetriebenen Überschallfahrzeug Thrust SSC und NASAs Space Shuttle über Lüftersysteme in Krankenhäusern, Anlagen für die Gebäudeklimatisierung und Windturbinengeneratoren bis hin zu Industriepumpen und -kompressoren. Der größte Wachstumsbereich ist laut Vieillard der Elektromotor, der in Autos, Motorrädern und anderen Mobilitätsanwendungen den Verbrennungsmotor ersetzen soll.
Dabei komme, so Vieillard, ein weiterer wichtiger Vorteil der Keramikwerkstoffe zum Tragen. Sie seien nämlich ausgezeichnete elektrische Isolatoren und machten die Lager dadurch weniger anfällig für Schäden durch Streuströme, die in Hochfrequenz-Maschinen eventuell durch sie hindurchfließen.
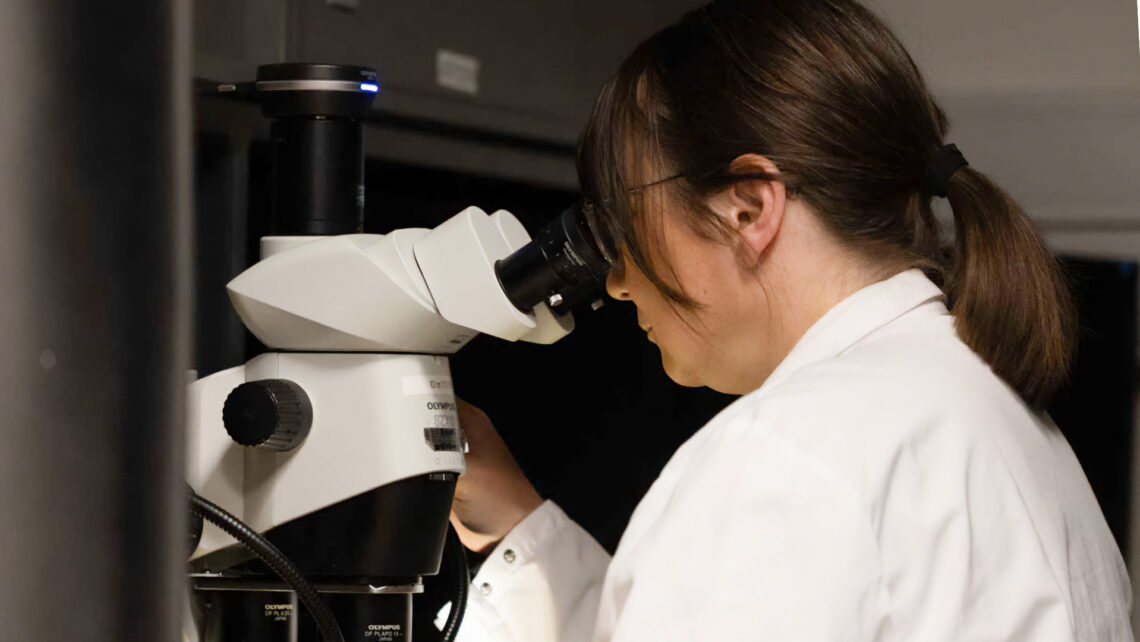
Harte Werkstoffe, schwierige Herstellung
Ein Faktor erschwert laut Vieillard jedoch die breitere Anwendung von Hybridlagern: Keramik-Wälzkörper sind schwierig und kostenaufwändig in der Herstellung. „Die kontinuierliche und systematische Fertigung von hochwertigen Siliziumnitrid-Wälzkörpern, die den extremen Beanspruchungen an den Kontaktstellen eines Lagers standhalten, ist eine echte Herausforderung“, erklärt die Forscherin. „Man braucht dafür sehr gutes Material und weil Keramik-Werkstoffe spröder sind als Stahl, muss man eine spezielle Mikrostruktur entwickeln, um hohe Zähigkeit und Festigkeit sicherzustellen.“
Keramikkomponenten werden mit Sintertechnik oder ähnlichen Verfahren, wie sie in der Pulvermetallurgie zum Einsatz kommen, hergestellt. Dabei vermengt man feines Siliziumnitridpulver und andere Zusatzstoffe, presst sie in eine Form und erhitzt sie anschließend unter hohem Druck, bis das Material zu einem festen homogenen Werkstoff gesintert ist. Die Rohlinge werden dann in einem Schleif- und Feinstbearbeitungsverfahren zu hochgenauen Kugeln und Rollen geformt. Die Produktion erfordert in jedem Fertigungsschritt engmaschige Kontrollen mehrerer Parameter, um die gewünschte Struktur und Qualität des Endprodukts sicherzustellen.
„Viele Unternehmen produzieren Siliziumnitridteile“, sagt Vieillard, „aber nur wenige können derzeit die konstant hohe Qualität liefern, die wir für die Fertigung von Lagerkomponenten benötigen.“
Bei den ersten Hybridlageranwendungen wurden die hohen Herstellungskosten noch eher akzeptiert. Kunden im Luft- und Raumfahrtsektor zum Beispiel brauchten nur relativ kleine Mengen und konnten die höheren Kosten für die Hybridlager durch die sich daraus ergebenden Leistungsvorteile ausgleichen.
Für Vieillard war es immer wichtig, dass die Kunden bei jedem von SKF gelieferten Hybridlager auch von dessen Vorteilen profitierten. Dafür musste sie die Leistung der Werkstoffe und der fertigen Komponenten, das Verhalten der Hybridlager, die detaillierten Bauteilspezifikationen sowie die Inspektions- und Charakterisierungsprozesse verstehen. Genauso wichtig waren rigorose Qualitätskontroll- und Prüfverfahren, um zu gewährleisten, dass jede Fertigungscharge der Lager sämtliche Spezifikationen erfüllte.
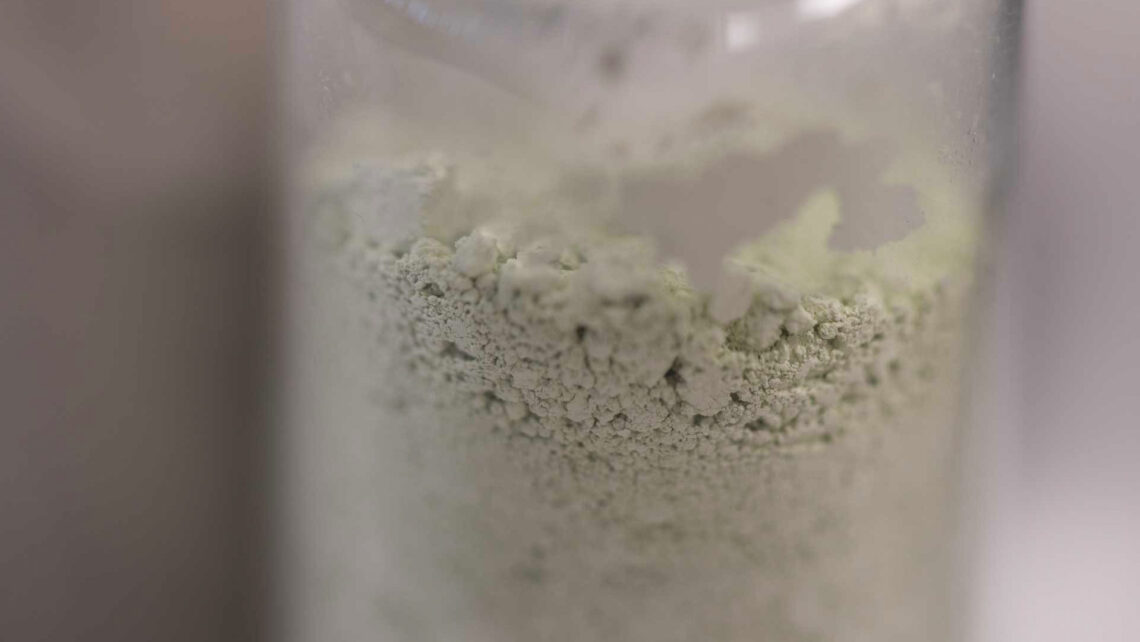
Vom Nischenprodukt zur Mainstream-Anwendung
Heutzutage kommen Hybridlager immer häufiger auch in Mainstream-Anwendungen wie etwa in Antriebssträngen von Kraftfahrzeugen zum Einsatz. Dies stellte Vieillard und ihr Team vor größere Herausforderungen. So investierte SKF in einen kompletten Fertigungszyklus vom Siliziumnitridpulver bis zum Endprodukt und bietet damit – parallel zu strategischen Zulieferern – die gesamte Wertschöpfungskette unter einem Dach. Außerdem entwickelte das Unternehmen für diese neue Lagergeneration größere Produktionssysteme.
Kontinuierlich arbeitet man auch daran, Leistungspotenzial und Lebensdauervorhersage dieser Produkte zu verbessern und kostenoptimierte Spezifikationen bereitzustellen. Besonders wichtig ist es aber momentan, sich auf die Optimierung der einzelnen Verfahrensschritte und die Auswirkungen auf die Qualität des Endprodukts zu konzentrieren.
Das Keramik-Team von SKF, bestehend aus Forschenden, Konstrukteuren, Entwicklern und Fertigungspersonal, hat nun die Aufgabe, durch Prozessverbesserungen und Innovationen innerhalb der gesamten Wertschöpfungskette die Kosten zu reduzieren. Das reicht von der Wahl des Rohpulvers über Automatisierungsprozesse und verbesserte konturnahe Verdichtungs- oder Sinterverfahren bis zur Inspektion des Endprodukts.
„Wir brauchen noch mehr Forschung, um viele dieser Möglichkeiten zu entdecken und zu verstehen“, schließt Vieillard.
Zwei Werkstoffe, viele Vorteile
Hybridlager kombinieren Stahllaufbahnen mit Wälzkörpern aus dem keramischen Werkstoff Siliziumnitrid. Dank dieser Kombination haben Hybridlager einzigartige und überzeugende Eigenschaften. „Keramik ist um 60 Prozent leichter als Stahl“, erklärt Charlotte Vieillard, Materialwissenschaftlerin bei SKF. „Dadurch lässt sich vor allem bei größeren Lagern Gewicht einsparen. Die leichteren Wälzkörper reduzieren erheblich die zusätzlichen Fliehkräfte, die normalerweise bei sehr hohen Drehzahlen auf das gesamte Lager einwirken. Das bedeutet, ein Hybridlager ermöglicht einen Betrieb mit wesentlich höheren Drehzahlen.“
„Keramik zeichnet sich zudem durch eine sehr harte, glatte Oberfläche mit nur geringer Haftreibung im Kontakt mit Stahl aus“, fährt Vieillard fort. „Das reduziert Reibung und Oberflächenschäden, insbesondere bei schwierigen Betriebsbedingungen, bei denen kein vollständiger Schmierfilm die Wälzkörper von den Laufbahnen trennt.“
Diese Mechanismen erhalten das Wärmegleichgewicht der Oberflächen unter Kontrolle, was wiederum die Gebrauchsdauer von Schmierfett und Wälzlager verlängert.
Bemerkenswertes, so Vieillard, könne man auch an der Schnittstelle zwischen Keramik und Stahl beobachten. „Da der Siliziumnitridwerkstoff wesentlich härter und steifer als Stahl ist, hat dieser Lagerkontakt noch einen weiteren Vorteil: Er kann Verunreinigungen und Mängel auf der Laufbahnoberfläche besser bewältigen.“
In einigen Fällen, so Vieillard, seien Keramik Wälzkörper in der Lage kleine Dellen und Fehler an der Innen- und Außenringlaufbahn abzuflachen und so einen möglichen Schaden zu mindern, bevor dieser die Leistungsfähigkeit der Einheit Wälzlager bedroht. Berücksichtigt man zudem die Tatsache, dass Stahl und Keramik nicht so leicht aneinanderhaften, hat man eine optimale Lösung für ein äußerst langlebiges und strapazierfähiges Lager.
Dank der Verwendung von Stahlringen sind Hybridlager außerdem eine benutzerfreundliche Option sowohl für die Hersteller als auch für die Endanwender, da sie sich auf ähnliche Weise montieren und einbauen lassen wie herkömmliche Stahllager. Das vereinfacht die Fertigung und macht Hybridlager zu einer Plug-in-Lösung für viele Anwendungen.
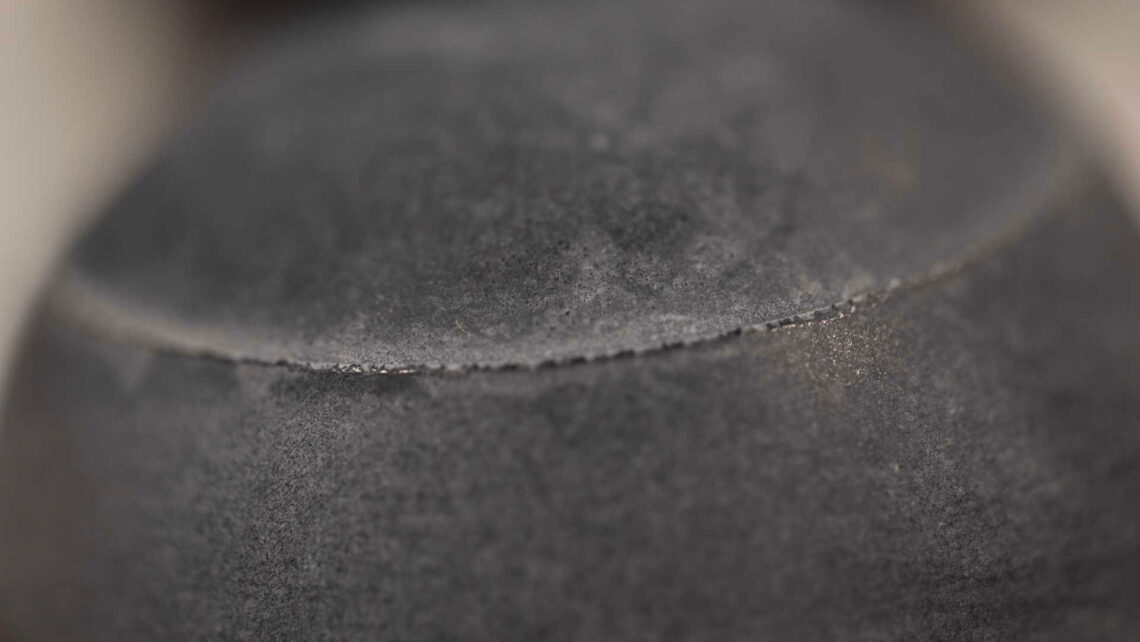