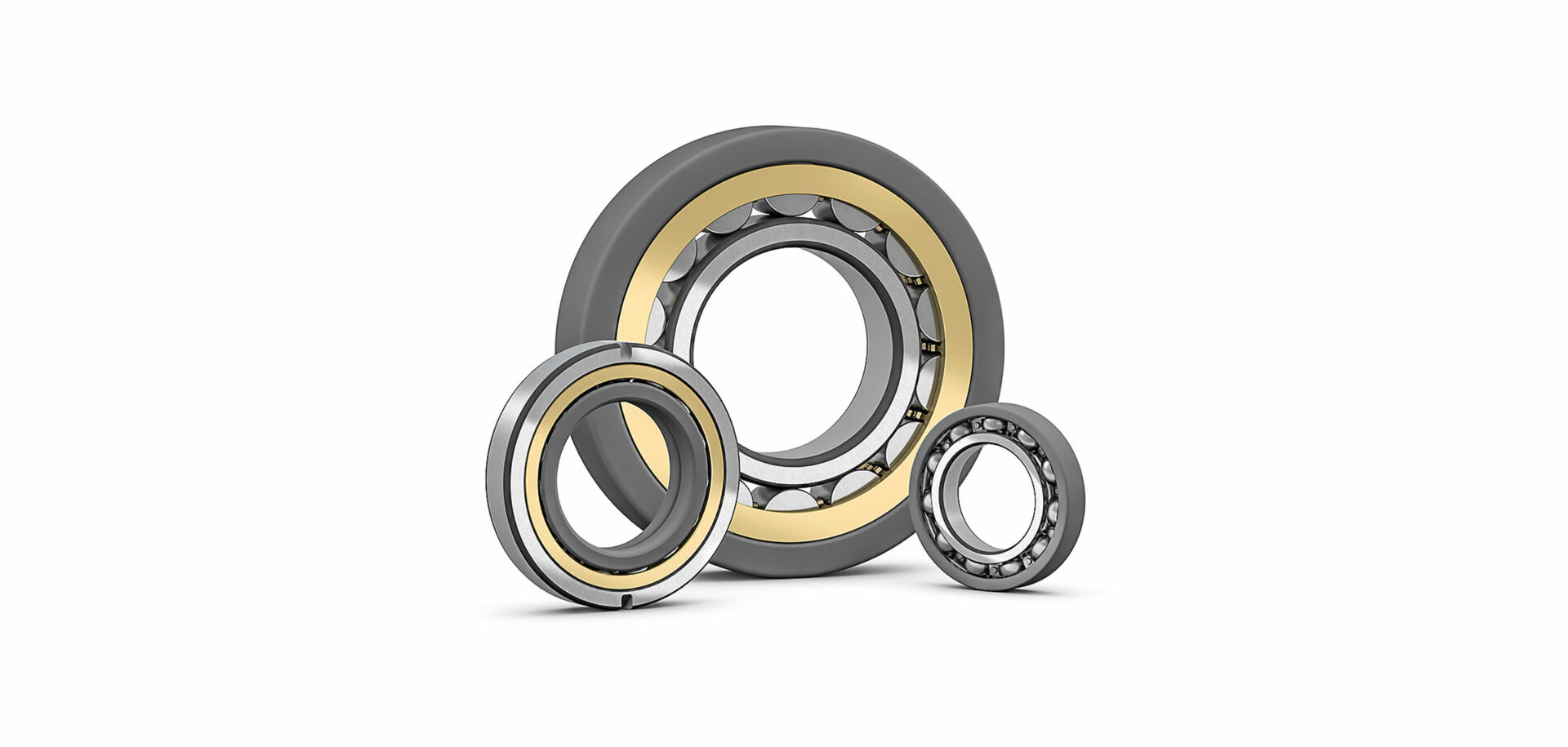
Vermeidung von elektrischen Stromschäden
Isolierte Lager verhindern frühzeitige Lagerausfälle, die letztendlich durch elektrische Streuströme verursacht werden. Deren Isolationseigenschaften müssen – unabhängig von den Umgebungsbedingungen – stabil bleiben, insbesondere bei Lagerung, Handhabung und Betrieb in feuchter Umgebung.
Warum isoliert man Lager?
Lagerschäden können auftreten, wenn elektrische Ströme den Wälzkontakt als leitende Verbindung nutzen.
Es gibt heute eine Reihe von Publikationen, die sich mit dieser Thematik befassen, darunter auch Diskussionen über Schadensursachen und Gegenmaßnahmen [1, 2, 3, 4].
Das Tribosystem eines Lagers bestimmt das elektrische Verhalten des Wälzkontaktes und die daraus folgenden Konsequenzen.
Im Stillstand weist das Lager einen niedrigen ohmschen Widerstand auf, es befindet sich in einem gut leitenden Zustand. Aufgrund des relativ guten elektrischen Kontakts (Metall/ Metall) sind nur sehr hohe Stromstärken wie Schweißströme in der Lage, die Laufbahnoberfläche zu zerstören.
Der ohmsche Zustand liegt vor, wenn das Lager unter Mischreibung einen erhöhten ohmschen Widerstand zeigt. In diesem Fall sind schon schwache elektrische Ströme von wenigen Ampere potenziell gefährlich.
Im kapazitiven Zustand befindet sich das Lager unter Vollschmierung und verhält sich wie ein elektrischer Kondensator mit einer bestimmten Durchschlagspannung. Wenn die im Schmierfilm der Kontaktzone anliegende elektrische Feldstärke hoch genug ist (über dem Schwellenwert), treten elektrische Entladungen auf, welche als EDM (Electric Discharge Machining)-Ströme bezeichnet werden.
Allen Schadensfällen ist eines gemeinsam: Die Kontaktfläche der Laufbahn wird lokal aufgeschmolzen und die Materialeigenschaften des Stahls in diesem Bereich werden verändert. Außerdem können sich die Schmierstoffeigenschaften verändern. Dies hat negative Auswirkungen auf die Lagerleistung in Form von Laufbahn- und Schmierstoffschäden und führt zu erhöhtem Verschleiß und zunehmenden Lagervibrationen. In den Bildern 1 und 2 ist die Wirkung von EDM-Strömen dargestellt, die sich als Mikrokrater aufgrund von hochfrequenten Lagerströmen zeigen. Diese Schädigung wird heute am häufigsten bei Anwendungen mit Frequenzumrichtern beobachtet. Eine Möglichkeit, den potenziell zerstörerischen Auswirkungen schädlicher elektrischer Ströme entgegenzuwirken, ist die Verwendung einer im Lager integrierten elektrischen Isolierung.
INSOCOAT – Ein Lager mit integrierter thermischer Spritzschicht
Bei den INSOCOAT Lagern von SKF sind die Außenflächen des Außen- oder Innenrings mit einer elektrisch isolierenden Beschichtung versehen, wodurch eine elektrische Isolation in das Lager integriert ist. Die Beschichtung besteht aus einem oxidkeramischen Material (Bild 3) und wird durch ein thermisches Spritzverfahren auf das Lager aufgebracht. Am häufigsten handelt es sich dabei um reines Aluminiumoxid (Al2O3). Manchmal werden auch Oxidgemische verwendet, da unterschiedliche elektrische und mechanische Eigenschaften der daraus resultierenden Beschichtungen erwünscht sind [5, 6]. Beim thermischen Spritzen werden die Oxidpartikel in einem heißen Plasmastrom transportiert und geschmolzen. Dieser heiße Strom transportiert den Großteil der geschmolzenen Partikel zum vorbehandelten Substrat, wo sie abkühlen und die gewünschte Beschichtung bilden.
Nach dem Spritzvorgang weist die Beschichtung eine gewisse Anzahl offener und miteinander verbundener Poren auf. Dies ist eine allgemeine Eigenschaft von thermischen Spritzbeschichtungen. Anzahl und Aussehen der Poren sind stark abhängig von den Parametern des Beschichtungsprozesses. Der „Versiegelung“ der Poren kommt beim thermischen Spritz-verfahren eine zentrale Bedeutung zu. Dadurch werden die Korrosionsgefahr verringert, die mechanischen Eigenschaften verbessert und die Isoliereigenschaften konstant gehalten, was in feuchten Umgebungen sehr wichtig ist.
Bild 5 zeigt ein Beispiel für geschlossene Poren. Es handelt sich hierbei um eine typische Pore, die mit kleineren Poren in einer thermischen Spritzbeschichtung verbunden ist. In der Literatur wurden bereits viele verschiedene Versiegelungsstrategien diskutiert [5, 6, 7]. Bei elektrisch isolierenden thermischen Spritzbeschichtungen ist ein Versiegeln mit organischen Sieglern am zweckmäßigsten. Mögliche Versiegelungsstoffe haben unterschiedliche Eigenschaften in Bezug auf Viskosität, Aushärtungstemperatur, Verdampfungseigenschaften, Schrumpfung etc. Der gesamte Prozess des thermischen Spritzens und Versiegelns muss sorgfältig analysiert werden, um die gewünschten Beschichtungseigenschaften zu erzielen.
Alte INSOCOAT Generation: Manko ausgemerzt
Bei einer Reihe von Anwendungen der bisherigen INSOCOAT Lagergeneration wurden in sehr heißen, feuchten Umgebungen niedrige Isolationswiderstandswerte festgestellt. Der Widerstand elektrischer Isolatoren ist immer eine Kombination aus Oberflächen- und Volumenwiderstand [8]. Neben den Materialeigenschaften sind beide Faktoren von der Luftfeuchtigkeit und der Temperatur abhängig. Während der Oberflächenwiderstand auf eine Klimaänderung sofort reagiert, verändert sich der Volumenwiderstand über einen längeren Zeitraum. Wenn die Isoliereigenschaften außerhalb des gewünschten Bereichs liegen, muss das gesamte isolierende Beschichtungssystem verbessert werden [5, 6, 7].
Experimente mit INSOCOAT Lagern der bisherigen Generation bestätigten die im Feld festgestellten niedrigen Werte durch Analyse des elektrischen Widerstands in direktem Kontakt mit Wasser1. Es stellte sich heraus, dass die Beschichtung über einen langen Zeitraum Wasser absorbierte und dieser Effekt nach dem Trocknen vollständig reversibel war. Aufgrund der langen Zeitdauer der Widerstandsabnahme wurden Oberflächenströme, offene Porosität oder Risse als Ursache ausgeschlossen. Daher konnte nur das Beschichtungsmaterial, das Oxid und/oder der Versiegelungsstoff selbst die Ursache sein. Bei umfangreichen Forschungs- und Prüfaktivitäten wurden verschiedene Beschichtungs- und Versiegelungsstrategien evaluiert. So wurden beispielsweise verschiedene Spritzpulver, Versiegelungsstoffe und thermische Spritzstrategien getestet. Eine erste Auswertung erfolgte, wie oben erwähnt, in direktem Kontakt mit Wasser. Obgleich dieser Test unrealistische Bedingungen darstellt (in realen Anwendungen wird das Lager oder der Motor nicht in Wasser getaucht), gibt er eine sehr schnelle und genaue Rückmeldung über einen möglichen Erfolg oder Misserfolg. Bild 6 zeigt einige Prüfergebnisse von guten (V1 & V2) und schlechten Beispielen (V3), und zwar stets im Vergleich zur bisherigen INSOCOAT Lagervariante. V2 war der beste Kandidat für die neue INSOCOAT Generation.
Neue INSOCOAT Lager
Bild 7 zeigt die elektrische Leistungsfähigkeit der neuen INSOCOAT Lager im Vergleich zur bisherigen Variante unter realen Bedingungen. Dies bedeutet, dass die Lager wie im praktischen Einsatz eingebaut und in einer Klimakammer unterschiedlichen klimatischen Bedingungen ausgesetzt wurden. In Bild 8 ist der Messaufbau dargestellt. Die neue INSOCOAT Lagervariante ist wesentlich unempfindlicher gegen Feuchtigkeit als die bisherige Lagergeneration.
Conclusio – Die neue Generation von INSOCOAT Lagern
Die neue INSOCOAT Lagergeneration wurde dahingehend optimiert, dass auch in sehr feuchten Umgebungen ein hoher und stabiler elektrischer Isolationswiderstand gewährleistet ist. Bei der Validierung wurden Bedingungen gewählt, die auch extreme Klimabedingungen simulierten. Neben den hier aufgeführten Angaben wurden weitere Parameter überprüft und validiert, wie beispielsweise das Niedrig- und Hochtemperaturverhalten (-40 °C bis +150 °C), die mechanische Leistungsfähigkeit (Schichthaftung, Ein-/Ausbaubeanspruchung, Schlagfestigkeit), das Hochspannungsverhalten bis 6 kV DC und die Medienverträglichkeit.
Selbst bei einer relativen Luftfeuchtigkeit von über 90 % bei einer Temperatur von 30 °C, bleibt der ohmsche Widerstand des getesteten Lagers 6316/C3VL0241 bei über 2000 MΩ, während er bei der bisherigen Lagervariante auf knapp über 50 MΩ sinkt.
INSOCOAT ist eine eingetragene Marke der SKF Gruppe.
1 Wasser mit einer bestimmten Leitfähigkeit
Literatur
[1] Preisinger, G.: Vermeidung von Elektroerosion in Wälzlagern, SKF Evolution, #2-2001
(http://evolution.skf.com/de/vermeidung-von-elektroerosion-in-wlzlagern/)
[2] Mütze, A.: Bearing currents in inverter-fed AC-motors, TU Darmstadt, 2004
[3] SKF: Bearing damage and failure analysis, 2017
[4] ISO 15243: Rolling bearings – damage and failures – terms, characteristics and causes, second edition, 2017
[5] Fauchais, P.L.: Thermal Spray Fundamentals, Springer, 2014
[6] Pawlowski, L.: The science and engineering of thermal spray coatings, Wiley, 2008
[7] Knuuttila, J.: Sealing of thermal spray coatings by impregnation, ASM, 1999
[8] IEC 62631-3-3: Dielectric and resistive properties of solid insulating materials – Part 3-3: Determination of resistive properties (DC methods) – Insulation resistance, 2015