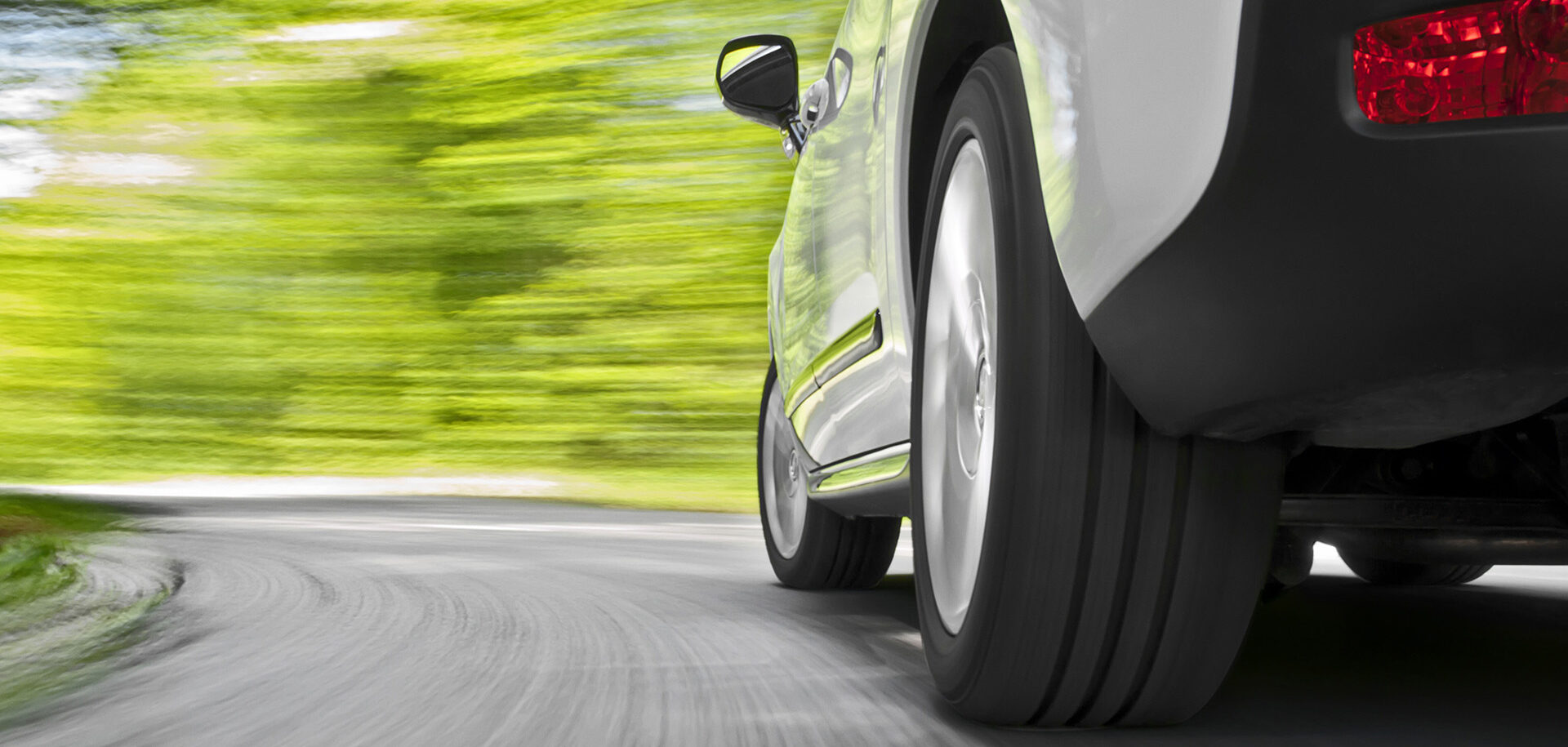
Efficient seals boost sustainability
A challenge in seal design is to achieve the lowest friction possible while maintaining the sealing ability to keep lubricants in and contaminants out. Lowering friction torque by using SKF Virtual Seal platform helps reduce energy consumption and cut carbon emissions.
The seal is a major contributor to friction in rotating equipment – up to 60 % of the total friction torque in some applications. The downward trend in power consumption across all applications and industries has for several years been a global movement, and this is expected to continue for many more years to come, as seen in the global trend. Lowering seal friction torque is thus one of the main customer requirements to improve system efficiency, reduce energy consumption and cut overall carbon emissions.
The main challenge in engineering the optimal seal design is reaching the lowest friction possible while maintaining the sealing ability to retain the lubricant inside and keep contaminants out of the system. Stricter CO2 regulations increasingly translate into requirements to further lower the friction level generated by the proposed sealing solution during operations.
This article focusses mainly on the friction losses of the sealing system in use, which falls indirectly in the Scope 3 downstream category according to the Greenhouse Gas Protocol and more precisely the subcategory “Use of Sold Products”.
For most SKF applications, frictional power losses, as part of the Scope 3 downstream, are the main contributors to the overall CO2 emissions of our bearing products, as illustrated through this link.
Smart combination of simulation tools
Accurate seal friction and temperature performance prediction requires a combination of advanced material, tribological, lubrication and heat dissipation models. The SKF Seals Global Research and Innovation team has developed an advanced simulation platform – SKF Virtual Seal (SAMBA) – that couples the Abaqus FEA (finite element analysis) solver with SKF Seals proprietary analytical model equations, thereby enabling the prediction of seal frictional heat generation and system thermal evolution (fig. 1).
SKF has developed a CO2 emissions estimator that, when coupled with the frictional torque and temperature results obtained via SKF Virtual Seal, demonstrates how more sustainable sealing solutions can be virtually enabled with the aid of advanced simulation platforms.
SKF Virtual Seal, a complex multi-physics approach
The transient evolution of the temperature in a sealing system stabilizes when there is an equilibrium between the amount of heat generated by the seal frictional torque and the amount of heat dissipated to the surrounding of the sealing system. Thus, it is crucial to consider both the frictional heat generation and thermal transfers together to ensure a realistic prediction. More than a hundred variables involved in the seal torque prediction are interdependent, which makes predictive modelling even more complex. The integration of the SKF Virtual Seal modelling equations into a finite element analysis (FEA) package allows for consolidation of all the interdependent variables at each increment of time in the simulation.
Both the implementation of the required complex models and their interactions with the FEA solver use various non-standard numerical processes, which require advanced competences. A user interface has been developed to facilitate and accelerate the deployment and usage of the SKF Virtual Seal platform. The role of the interface is to allow the user to easily provide specific application parameters.
Once all inputs are defined through the interface, a Python script modifies the standard FEA model and connects all parameters to a pre-compiled routine where the analytical equations are programmed. This also automatically generates, in the background, the bidirectional coupling between the FEA solver and the SKF Virtual Seal analytical equations. The engineer’s next step is to then run a simulation via the FEA software as is commonly done, except that a now-upgraded semi-analytical solver is silently being used in the background during the simulation.
Experimental validation
Towards sustainable performance
The friction level, predicted by SKF Virtual Seal, can be converted into a level of CO2 emissions via the SKF sustainability tool, the CO2 emissions estimator, to allow for a virtual method of selecting the best-in-class seal candidate based on a tangible sustainability criterion. The emissions due to frictional losses are then calculated based on the regional amount of CO2 emissions per kWh of energy for the chosen geographical location.
The benefit of such a tool is to provide estimates and is a step further towards raising awareness based on a concrete measurement method of the impact of our products.
From theory to real-world application
To highlight the potential of virtual prediction of carbon emissions in early development stages, see the following two concrete examples in the automotive and railway industries.
Automotive wheel-end case
In this first example, an automotive manufacturer requests a new cassette seal design for a SKF Hub Bearing Units (HBU) with lower friction. The target requirement is a 20 % friction reduction, compared with the previous generation of HBU cassette seals.
Based on the SKF Virtual Seal simulation results, the optimization of the sealing grease predicts a friction reduction of 28 %:
- 0.33 N.m for the solution using the original grease (grease A)
- 0.24 N.m for the solution using the new low-friction grease (grease B).
This solution exceeds the customer’s friction reduction target. Moreover, experimental results coming from the product validation tests confirm the SKF Virtual Seal predictions, as illustrated (fig. 3).
From torque to CO2 emissions
By injecting the torque results into the SKF CO2 emissions estimator, one can estimate the effect of the performance improvements of our new HBU seal solution on the Scope 3 downstream product emissions. The proprietary sustainability tool translates the seal frictional power losses into expected CO2 emissions. The resulting comparison between the newly designed HBU cassette seals solution with an optimized grease and the existing solution for car wheel-end application is illustrated (fig. 4).
Railway bearing-application case
This second real-world example comes from a new partnership programme initiated between a railway manufacturer and SKF to develop a whole new bearing system for the new generation of regional trains in a major European city. The target of the new train bearing unit (TBU) is a 30 % friction reduction compared with the previous generation.
As in the automotive case illustrated earlier, the new TBU seal design is improved with the support of the SKF Virtual Seal platform with a forecast of 44 % friction reduction level:
- 0.77 N.m for the original solution
- 0.43 N.m for the enhanced solution.
As shown in fig. 5, the experimental results coming from the product validation tests match once more with the SKF Virtual Seal modelling predictive results.
From torque to CO2 emissions
In a similar way, the proprietary sustainability tool translates the seal frictional power losses of the TBU seal into expected CO2 emissions. The resulting comparison between the newly designed TBU sealing solution and the original solution is illustrated in fig. 6.
Conclusion
The undeniable urgency to act on climate change is driving an increased focus on sustainability. It is therefore paramount to discuss and raise awareness with all involved parties across the complete value chain, such as suppliers, manufacturers and customers, about the environmental impact of our products.
Environmental sustainability has a very broad definition, as outlined by the Scope 3 Greenhouse Gas Protocol. The examples in this article illustrate one of SKF’s many necessary actions to reduce its impact on the planet via products with lower CO2 emissions while remaining competitive.
Part of this effort involves creating web-based calculation tools such as the SKF Sustainability tool – CO2 estimator and advanced modelling platforms such as SKF Virtual Seal to estimate product environmental impact from early design to product selection phases and beyond, thereby paving the way for more environmentally friendly practices.