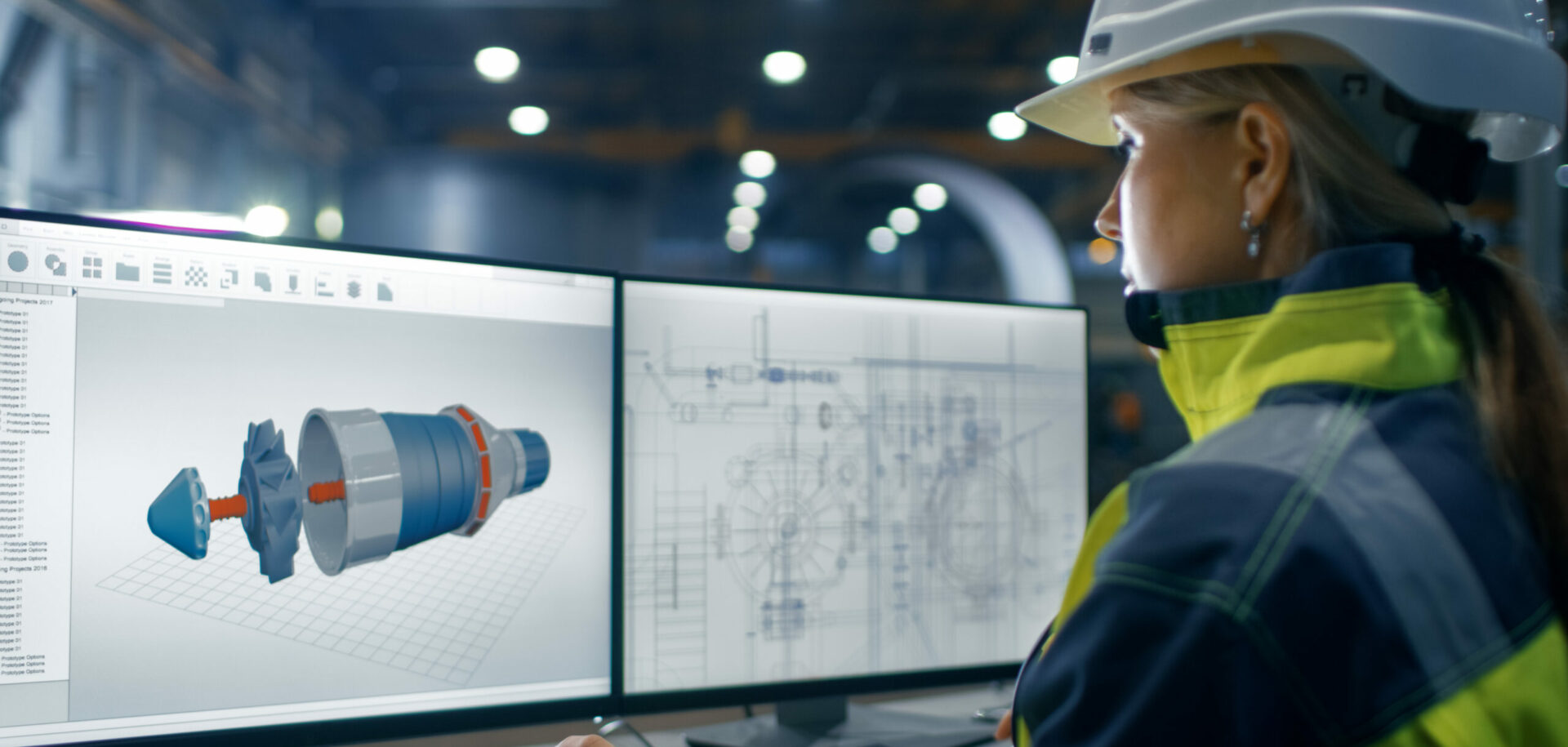
Electric moves – SKF acquisition adds expertise in electrical testing
Through the acquisition of the Baker Instrument Company, SKF continues to broaden its endeavours to support its traditional mechanical strengths by the addition of electrical motor testing expertise.
In July 2006 SKF acquired Baker Instrument Company, based in Fort Collins, Colorado, in the United States. This addition has enhanced SKF’s expertise outside its trad-itional mechanical base. The instruments produced in Fort Collins are developed around electric motor theory and are sold into the motor repair and industrial predict-ive maintenance industries.
Baker Instrument Company was founded by Tom Baker in 1961 and has developed into a market leader in electric motor testing instrumentation. Baker’s expertise in electrical testing of motors developed from the scientific work carried out by J L Rylander in 1926. Rylander developed early tests such as the surge test, which is widely used in industry today. This test measures a drop in voltage amplitude in the copper windings of a motor. When a weakness is registered, the instrument user is notified, and action can correct the problem prior to work stoppage. Baker Instrument Company has continually pushed the test’s ability to detect failures at higher degrees of sensitivity, making the predictive nature of the surge test greater. In some maintenance circles, the surge test is known literally as “the Baker test.”
Predictive maintenance is practised worldwide in almost every industry. Locating, diagnosing and correcting problems are the universal goals of predictive maintenance. However, predicting motor problems requires a great deal of know-ledge, experience and the appropriate tools as well as a degree of luck. Electric motors have numerous components including copper winding wire, insulation systems, bearings and other mechanical and electrical features. These components combine with items such as drives, intake pumps, compressors, conveyors, among a long list of other items, to create the machines of industry.
Health checks for motors
This is where the equipment from Baker Instrument Company thrives. The static testers can provide definitive results on the health of the insulating systems of the motor, while the dynamic instrumentation looks at the total machine system.
The insulation system consists of a thin lamination over a copper winding or magnet wire and the ground wall insulation that protects the magnet wire inside of the slots in an electric motor stator. In order to have a more rounded electrical predictive main-tenance programme, it is important to perform static tests on not only the copper insulation but also all insulating systems within the motor. Standardized tests include insulation resistance, Meg-ohm, polarization index (PI), High Potential (HiPot) and the surge test. The insulation resistance measures the resistance of the copper wire of the motor circuit, whereas the Meg-ohm test looks for grounded motors. The Meg-ohm test is also valuable for finding wet and dirty motors. The PI test is much like the Meg-ohm test but is done for a longer period of time. This test looks at the slot liner insulation for moisture or contamination. The HiPot test determines the validity of the ground wall insulation and can be handled in several ways. Like the surge test, the HiPot test is carried out at a higher voltage than the operating voltage to simulate the environment that a motor sees when it is started. Rotating equipment can see up to five times its line operating voltage each time it is started, as the on-rush current is greater at this point. This on-rush current generates movement within the copper windings, which over time abrade the insulation, causing weakness. Left undetected, such weakness develops into a welded short, creating heat that causes motor failures. This is the realm of the surge test. Even slight insulation weaknesses can be detected prior to failure and can be repaired earlier, offering considerable savings.
On the other side of electrical testing of motors is the dynamic motor monitor. Since its introduction to the market in 1998, this instrument has become a desir-able tool because of its non-intrusive nature and information reporting capabil-ities. In most instances, a motor is part of a machine system comprising three com- ponents: the incoming power quality, the motor itself and the equipment being driven by the motor. This dynamic tool can define subtle issues within the mechanical or electrical systems that often go undiagnosed. Frequently motors are repaired or replaced and returned to service without the root cause of the problem being diagnosed. If this is the case, the motor will most likely fail in the same fashion, causing a repeat of the costly downtime. Issues such as harmonics, low or high voltage variations, voltage unbalances, rotor bar problems, bearing issues and misalignment are just some of the problems that can be identified. All of these issues can affect the motor system negatively, raising the cost of operation and lowering the efficiency of the overall operation.
Importance of electrical testing
Electric motors fail in many ways. Accord-ing to a study of the California-based Electric Power Research Institute in the US, bearings account for approximately 41 percent of all motor failures, while 36 percent are the result of the stator. Eighty percent of stator failures are initiated by an electrical problem, and approximately 29 percent of all electric motor failures are directly related to an electrical issue.
Many failures within these 29 percent can be avoided by periodic testing or monitoring of the motor. Unscheduled downtime can account for hundreds of thousands of euros an hour in expenses when critical motors fail. Avoiding these failures is the main goal of any predictive maintenance programme.
Bridging the gap
With the equipment offered by Baker Instrument Company, SKF has a complementary offering in terms of monitoring and predicting the health of industrial capital assets. Integrating these two core technol-ogies will enable the end user to reap benefits not seen until now. Through either services supplied or equipment acquired, the data collected will out-produce prior methods, effectively changing the face of predictive maintenance.
Through the combination of electrical and mechanical technologies, the future of predictive maintenance will change vastly. By offering a greater portion of the predictive maintenance tool chest, SKF can identify a majority of motor issues in the industrial workplace, thus making it a world-renowned force in plant efficiency. Enhancements of these two core areas through cohesive engineering teamwork will create instrumentation to surpass the expectations of the marketplace.
With efficiency of paramount import-ance to every industry, any equipment that can help plants meet governmental requirements will be in great demand. Worldwide, motors consume between 55 and 63 percent of all electrical energy produced. With this huge volume of consumption, plant operations continually work to reduce these expenses. Effectively tuning processes and using efficient motors are just part of the equation. Maintaining and eliminating plant downtime will help operations run more effectively. This is where the right tools for the job will become important. By combining the mechanical and electrical worlds, a complete offering is established, creating a new realm of customer support.