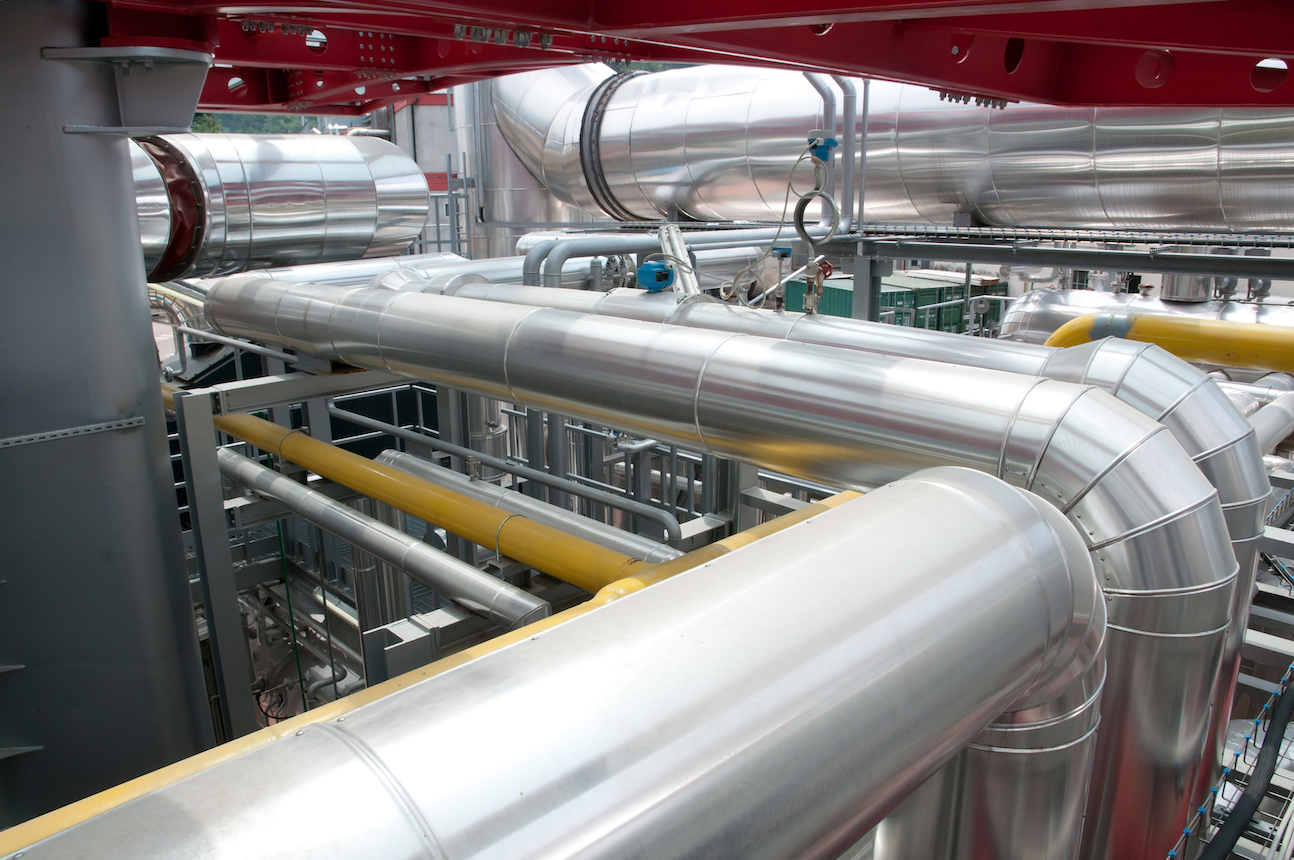
Inmersión total
SKF Blohm + Voss Industries ha logrado lo que nunca antes se había conseguido: desmontar el estabilizador de aleta de un barco sin sacarlo del agua.
Datos
MS Prinsendam
Armador: Holland America Line
Capacidad (pasajeros): 916
Capacidad (tripulación): 470
Tonelaje bruto: 39.051 toneladas
Eslora: 172 metros
Manga: 29 metros
HOLLAND AMERICA LINE
Sede: Seattle, Washington, EEUU.
Actividad: La flota de 15 barcos de la empresa ofrece cada año más de 500 cruceros que hacen escala en 415 puertos de 98 países, territorios o dependencias.
Estructura: Holland America Line forma parte de Holland America Group, una división de Carnival Corporation & plc.
Número de pasajeros al año: más de 800.000.
www.hollandamerica.com
Enlaces relacionados
Contacto de venta
Dieter Winkler, Dieter.Winkler@bv-industries.com
Cuando un crucero atraviesa aguas revueltas, apenas se nota. El secreto está en los estabilizadores, unas aletas móviles relativamente pequeñas fijadas al casco por debajo de la línea de flotación. Estos pequeños componentes son determinantes para el comportamiento del barco, ya que pueden reducir el balanceo en más de un 85%. Con forma de ala de avión, estas aletas giran hacia arriba o hacia abajo para ejercer una fuerza de sustentación negativa o positiva, contrarrestando el efecto de las olas.
SKF Blohm + Voss Industries (SKF BVI), parte del Grupo SKF, cuenta con más de 60 años de experiencia en el desarrollo y producción de estabilizadores de aleta retráctiles, habiendo entregado casi 600 pares en todo el mundo. La empresa también se encarga del mantenimiento y reparación de sus productos. Así que, cuando el estabilizador de estribor del MS Prinsendam resultó dañado en una colisión en plena temporada alta, la empresa de cruceros Holland America Line se puso en contacto con SKF BVI para pedirle que lo reparara.
Normalmente, la reparación supone trasladar el barco a dique seco, donde es más fácil retirar el estabilizador y la cruz. Sin embargo, la empresa no podía hacerse con un dique en plena temporada (éstos se suelen reservar con dos años de antelación) y había que encontrar otra solución. ¿Podría desmontarse el estabilizador durante un crucero, mientras el Prinsendam estaba amarrado a puerto?
Nunca antes se había hecho una extracción semejante bajo el agua. Además, al tratarse de un crucero, hasta los componentes más pequeños son enormes. La aleta y la cruz que había que sacar pesaban unas 25 toneladas.
Holland America Line pidió ayuda al especialista en reparaciones subacuáticas Subsea Global Solutions. Bajo la supervisión de Jens Miesner, consultor técnico de SKF BVI, ambas empresas se pusieron manos a la obra. Según Rick Shilling, de Subsea: “Diseñamos un sistema complejo basado en el diseño del estabilizador, utilizando unos aparejos fijos y flotantes para aguantar la carga. El proceso era muy parecido a lo que se hace en dique seco. Simplemente lo adaptamos para que lo pudieran hacer buzos debajo del agua”.
Había que soldar unos anillos metálicos, conocidos como “pasacuerdas”, al casco para sostener los aparejos durante la extracción. De eso se encargaron los buzos mientras el crucero paraba en distintos puertos. “No fue nada fácil”, dice Miesner. “Los pasacuerdas de la caja de la aleta no estaban soldados, como sería lo normal. Otro problema era el poco espacio disponible para maniobrar y mover una unidad de 25 toneladas”.
Los buzos soldadores de Subsea Global Solutions utilizaron un procedimiento puntero para realizar la soldadura subacuática. Los pasacuerdas se diseñaron para poder doblarse como bisagras y evitar que se golpearan contra la caja de la aleta. Los buzos también extrajeron varios pernos del estabilizador para agilizar la extracción en cuanto el Prinsendam llegara a Ámsterdam. (En un principio, estaba previsto que la extracción se realizase en el puerto de Warnemünde, en Alemania, pero tuvo que aplazarse por cuestiones operativas.)
Evidentemente, sacar un componente del casco supone impedir la entrada de agua. Desde el interior se aislaron las superficies de contacto de la cruz con una ataguía interna de construcción especial. Para el exterior, Subsea diseñó unas cubiertas con bandas de impermeabilización especiales capaces de convertir las 7,8 toneladas de presión del agua en un sistema de obturación.
“Básicamente, abrimos un agujero en el barco e intentamos que el agua no entrase y el combustible no se escapase”, dice Shilling. “Parte del proceso consistió en equilibrar las presiones en los sistemas y limpiar la unidad de fluidos. Además, contábamos con equipos capaces de encapsular los fluidos residuales bajo el agua y bombearlos a la superficie”.
El equipo presentó un análisis de riesgos a las autoridades competentes para que aprobaran el procedimiento. “Somos una empresa conocida en el sector”, dice Shilling, “y presentamos los planes de reparación, análisis de riesgos y contingencia necesarios. Gracias a eso no fue difícil obtener el visto bueno de las autoridades portuarias y otras autoridades competentes”.
Cuando el barco atracó en Ámsterdam, grupos adicionales de buzos estaban listos para realizar la extracción. “Lo que más nos preocupaba era el desacoplamiento interno del conjunto de la cruz”, dice Shilling. “Cuando hay componentes dañados, siempre planea cierta incertidumbre. Aunque se hizo una inspección pormenorizada del estabilizador después de la colisión, es imposible verlo todo. Habíamos previsto todas las contingencias posibles. En el peor de los casos, volveríamos a colocar los pernos y lo intentaríamos de nuevo en algún otro momento”.
Afortunadamente, hizo buen tiempo y el mar estaba tranquilo. Se decidió empezar con la extracción y los preparativos previos dieron su fruto: los buzos fijaron el aparejo al estabilizador, utilizando cadenas pesadas para atar los equipos a un pontón flotante. Sacaron los pernos que quedaban y utilizaron técnicas especiales de sujeción y control de flotabilidad para colocar cuidadosamente el estabilizador en un punto que permitía que la grúa lo sacara del agua. Todo el proceso de extracción en puerto duró unas 55 horas.
“Muchas navieras siguieron la maniobra con atención, porque , en un futuro, podría ahorrar mucho tiempo”, explica Miesner.
El estabilizador se envió a SKF BVI para su reparación y volvió a instalarse en el Prinsendam unos meses después. Hoy el barco vuelve a surcar los mares con su estabilidad habitual.
Cómo se quitó el estabilizador
1. Varios días antes de que el barco llegara a Ámsterdam, el “puerto de extracción”, un equipo de expertos de SKF BVI y SubSea Global Solutions prepararon el barco desde el interior. Una ataguía especialmente diseñada aisló los puntos de conexión del estabilizador/casco del resto del interior.
2. Al mismo tiempo, el equipo fue siguiendo al barco por distintos puertos para realizar los preparativos en el exterior e interior del casco. Un equipo de buzos soldó unos innovadores pasacuerdas con efecto bisagra para fijar los aparejos al casco. Se extrajo el mayor número posible de pernos del estabilizador y de los puntos de unión para ahorrar tiempo más adelante, durante la extracción.
3. En el último puerto esperaban más buzos para realizar la extracción. Utilizando cadenas pesadas, ataron la aleta a un pontón flotante.
4. Los buzos sacaron los pernos que quedaban, y se extrajo el estabilizador utilizando un sistema de aparejo avanzado (basado en el diseño del estabilizador) y teniendo en cuenta el control de flotabilidad.
5. El estabilizador y la cruz se trasladaron al punto que permitía que la grúa los sacara del agua.