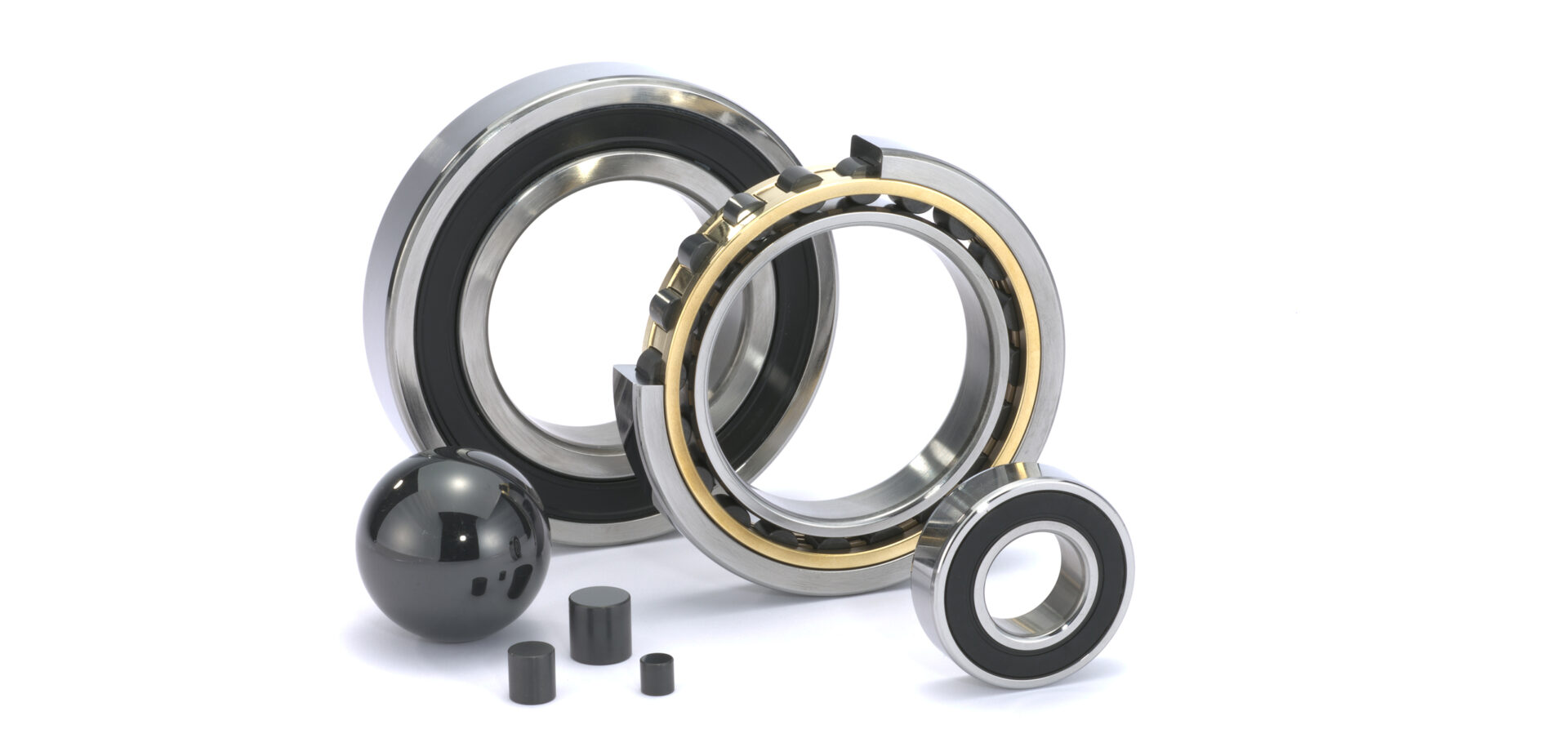
Nuevos métodos de prueba de los elementos rodantes de cerámica
En la fabricación de bolas y rodillos de nitruro de silicio para rodamientos híbridos, distintas formas de procesamiento conducen a microestructuras diferentes y, por tanto, a diferentes propiedades mecánicas [1]. Ello hace necesario que no solo se sometan a prueba barras de muestra especiales para pruebas de flexión, sino que también se realicen pruebas individuales de las bolas o rodillos para comprobar que el componente real del rodamiento haya obtenido las propiedades mínimas de resistencia, tenacidad a la fractura y requisitos de microestructura.
Los rodamientos que constituyen una combinación de aros de acero y elementos rodantes de cerámica, llamados rodamientos híbridos, son la mejor solución en determinadas aplicaciones altamente exigentes.
El nitruro de silicio de calidad para rodamientos es un material cerámico muy diferente de la cerámica usada en el hogar. Su gran dureza, tenacidad y resistencia son propiedades decisivas en el rendimiento. Las especificaciones de SKF para este material también incluyen tolerancias muy ajustadas.
En la fabricación de bolas y rodillos de nitruro de silicio para rodamientos híbridos, distintas formas de procesamiento conducen a microestructuras diferentes y, por tanto, a diferentes propiedades mecánicas [1]. Ello hace necesario que no solo se sometan a prueba barras de muestra especiales para pruebas de flexión, sino que también se realicen pruebas individuales de las bolas o rodillos para comprobar que el componente real del rodamiento haya obtenido las propiedades mínimas de resistencia, tenacidad a la fractura y requisitos de microestructura.
En este artículo, se presentan distintos nuevos métodos de prueba de propiedades específicas de los materiales cerámicos. Se están desarrollando en SKF con la colaboración de investigadores externos y ya se usan parcialmente para respaldar la producción, y se han definido en normas internacionales. El objetivo es siempre obtener datos que contribuyan a predecir y asegurar el rendimiento de componentes cerámicos en rodamientos híbridos.
Prueba de resistencia al rayado
Distintas calidades de material de nitruro de silicio han demostrado poseer claras diferencias en aptitud de rectificado, y en nucleación y propagación de grietas. Para investigar sistemáticamente los efectos del desgaste deslizante en materiales de nitruro de silicio, se puede utilizar un dispositivo de prueba de resistencia al rayado. Históricamente, la prueba de resistencia al rayado se desarrolló para comprobar la adhesión de los revestimientos, pero también se emplea para probar el material. En esta prueba, una punta de diamante bien definida geométricamente se guía a una velocidad determinada en un intervalo de 1 a 20 mm/s a través de una superficie con una carga que se incrementa linealmente. Esto crea una raya que puede evaluarse mediante un microscopio. La disposición se muestra en la fig. 1, y en la fig. 2 se presentan ejemplos de rayas.
Al aplicar la carga, se forman grietas elípticas debajo del penetrador. Durante la descarga, se producen grietas laterales a causa de la relajación de las tensiones en la zona de contacto. A un cierto nivel de carga, aparecen grietas, y estas se alargan al incrementarla. Con cargas más altas, se inicia un desconchado. Se sabe que varias propiedades del material afectan este comportamiento del desgaste deslizante: la dureza, la transformación de fase, la elasticidad, la resistencia a la propagación de grietas, la fricción, la humedad, la lubricación y el deslizamiento repetido desempeñan un papel en el aspecto de la raya [2–4]. Al mismo tiempo, esta indentación por una punta definida con una carga específica es similar a una prueba de resistencia típica, tal como se manifiesta en la correlación entre ancho de raya y dureza, que se muestra en la fig. 3.
Un factor importante para la implementación exitosa y eficaz de un nuevo material es su aptitud de rectificado, un término general que abarca la tasa de extracción de material, el desconchado, la fuerza de rectificado, el acabado superficial, las tolerancias y la integridad de la subsuperficie [4]. La evaluación estadística de distintos materiales de nitruro de silicio mediante pruebas de rayado permite clasificarlos en concordancia con el tamaño medio de las virutas en función de la carga aplicada a la punta del diamante, tal como se muestra en la fig. 4. Esto mantiene una buena correlación con los parámetros de rectificado, como la presión y la velocidad.
Prueba cuasiestática de resistencia a la fractura
Con las bolas terminadas, un primer enfoque en la industria de rodamientos es realizar una simple prueba de compresión de dos o tres bolas superpuestas. Esto da una estimación muy aproximada de una “capacidad de carga estática”. La resistencia del material a las grietas y daños por contacto herciano se prueba mediante indentaciones con esferas de carburo de tungsteno o mediante pruebas de resistencia a los impactos.
Utilizando herramientas modernas y análisis de datos, puede evaluarse la fractura por fragilidad de las bolas de cerámica, un método que se está desarrollando actualmente en SKF. Tres bolas de cerámica se alinean en una célula de carga mecánica, tal como se muestra en la fig. 5. La carga de compresión se incrementa lenta y linealmente mientras se mide la deformación y emisión acústica. Se han realizado pruebas similares concentradas en el análisis de la formación de grietas [5].
Se ha comprobado que la dependencia de la deformación plástica permanente en función de la carga máxima es casi lineal y característica para diferentes clases de materiales cerámicos (fig. 6). Además, la carga mínima de deformación plástica permanente y la carga crítica de formación de grietas (del análisis de señal de emisiones acústicas) permite la clasificación de distintas calidades de material de la misma composición química y mantiene una buena correlación con la solidez y la resistencia a los impactos.
Prueba de bola y rodillo con muesca
La resistencia, como propiedad central de los materiales, tradicionalmente se mide en barras de flexión especialmente fabricadas. Esto puede ser problemático, debido a que el corte y acabado de estas barras es diferente del de los elementos rodantes. Como alternativa, SKF, junto con la universidad Montan, de Leoben, Austria, ha desarrollado un nuevo método de prueba denominado “ensayo de bola con muesca”. En esta prueba, se corta centralmente una muesca en el plano ecuatorial de un componente acabado, lo cual simplifica el proceso y proporciona valores más relevantes sobre el componente cerámico en cuestión.
En la prueba de resistencia subsiguiente, se aplica una carga en los polos de la bola con muesca, perpendicular a la muesca, a través de dos yunques paralelos (fig. 7). Las caras con las muescas se comprimen juntas, y se generan tensiones de tracción en la superficie opuesta a la de la raíz de la muesca. Entonces la carga se incrementa uniformemente hasta la fractura. La resistencia del material se calcula partiendo de la fuerza de la fractura [6–9]. Los resultados de la resistencia de unas 30 muestras se representan en una curva de resistencia respecto a la probabilidad de fallas, lo que se denomina diagrama de Weibull, tal como se representa en la fig. 8. Según la teoría de Weibull, la resistencia está relacionada con el volumen efectivo o la superficie efectiva. Por tanto, se tienen que hacer estos cálculos para poder compararse con otros métodos de medición de la resistencia. El punto de partida de esta labor de desarrollo fue la “prueba de esfera C”, que se elaboró en el Oak Ridge National Laboratory, Estados Unidos [10]. La diferencia es que para la prueba de bola con muesca se utiliza una geometría de muesca delgada (del 5 al 15% del diámetro de la bola), en comparación con el 50% del diámetro de la bola que se emplea en la prueba de la esfera C. Esto permite una preparación más fácil de las muestras puesto que es más pequeña la cantidad que ha de cortarse de material cerámico de alta resistencia usado para bolas de cerámica en rodamientos.
Para las pruebas de rodillos, una muesca larga y estrecha similar con una profundidad de alrededor del 80% del diámetro de un rodillo cilíndrico se corta simétricamente a lo largo del plano central a través del eje del rodillo, perpendicularmente a las caras de los extremos. En la prueba de resistencia en la que se utilizan estas muestras de rodillos con muescas, se aplica una carga en los puntos de contacto de la línea del diámetro del rodillo con muesca (fig. 9). Debido a la mayor complejidad de la geometría, el modelo subyacente es más extenso, pero la ejecución práctica es bastante similar a la prueba de bola con muesca [11,12].
Conclusión
La implementación de cerámica de alto rendimiento en aplicaciones de rodamientos exige un conocimiento profundo del comportamiento del material durante el procesado y del producto terminado. Juntas, las pruebas presentadas permiten una caracterización integral y complementaria de los elementos rodantes en cuestión, e identificar pequeñas diferencias en aptitud de rectificado, resistencia a la fractura y solidez, según la microestructura del material, el tamaño del componente y el acabado de la superficie del elemento rodante.
Referencias
[1] G. Ziegler et al., Journal of Materials Science 22 (1987) 3041—3086
[2] D. M. Kennedy et al., Journal of Materials Processing Technology 77 (1998) 246—253
[3] M. G. Gee, Wear 250 (2001) 264—281
[4] O. Desa & S. Bahadur, Wear 225 (1999) 1264—1275
[5] S. K. Lee, Journal of the American Ceramic Society 80 (1997) 2367—2381
[6] P. Supancic et al., Ceramic Transactions 210 (2010) 327—36
[7] P. Supancic et al., Journal of the European Ceramic Society 29 (2009) 2447—2459
[8] P. Supancic et al., Key Engineering Materials 409 (2009) 193—200
[9] ÖNORM M 6341:2013, Notched ball test
[10] A.A. Wereszczak et al., Journal of the American Ceramic Society 90 (2007) 1843—1849
[11] S. Strobl et al., Journal of the European Ceramic Society 34 (2014) 2575—2584
[12] S. Strobl et al., Journal of the European Ceramic Society 34 (2014) 4167—4176