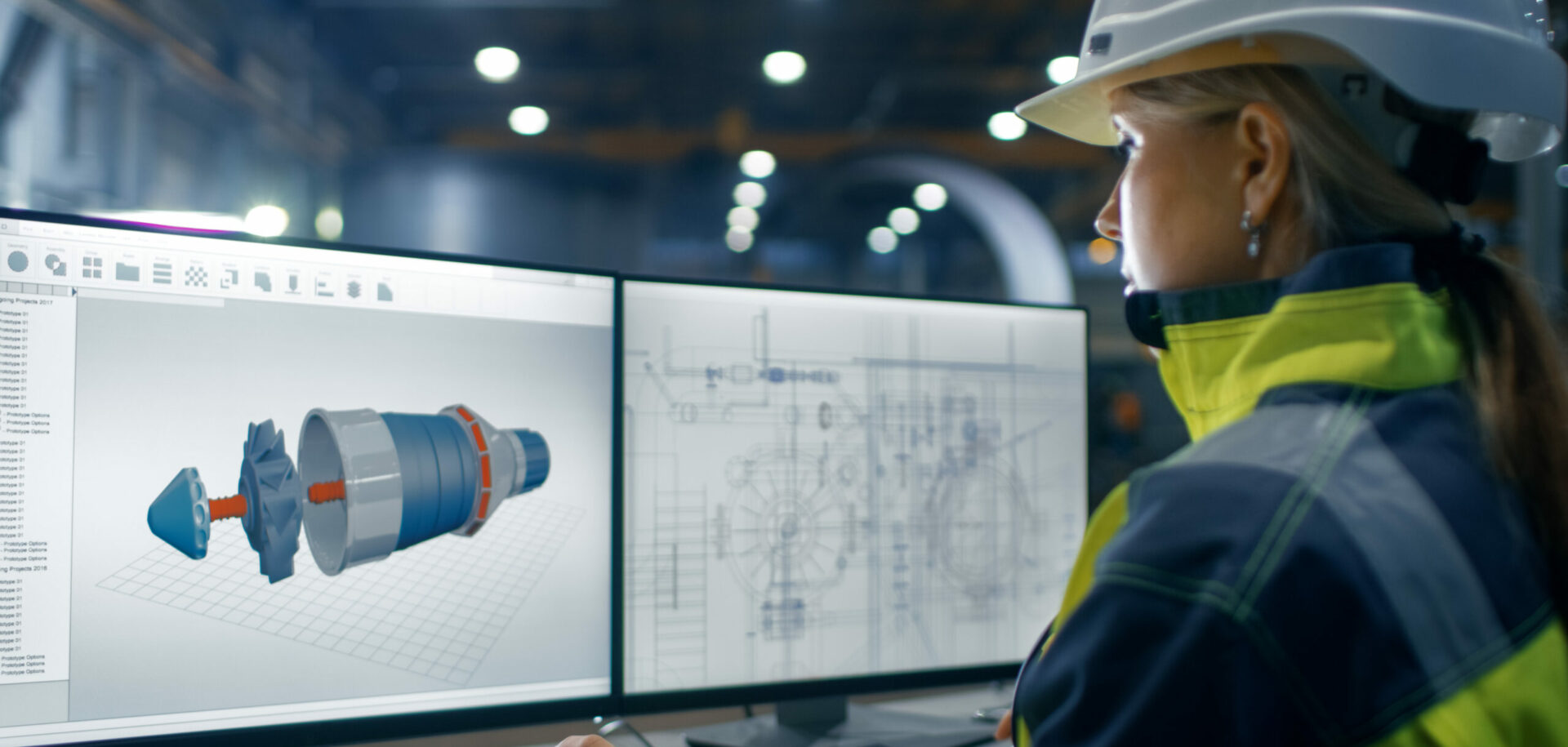
Rodamientos altamente fiables para la industria de procesamiento de hidrocarburos
Los requisitos del mercado a la industria de procesamiento de hidrocarburos obligan a las refinerías y a otras plantas a exigir una alta fiabilidad y un funcionamiento eficiente, además de un estrecho control sobre los costes de capital. SKF tiene una amplia experiencia en este mercado, al que ofrece desde instalaciones hasta mantenimiento y mejora.
Los requisitos del mercado a la industria de procesamiento de hidrocarburos obligan a las refinerías y a otras plantas a exigir una alta fiabilidad y un funcionamiento eficiente, además de un estrecho control sobre los costes de capital. SKF tiene una amplia experiencia en este mercado, al que ofrece desde instalaciones hasta mantenimiento y mejora.
Tecnología
El equilibrio crítico entre la oferta y la demanda en la capacidad de las refinerías, por ejemplo, ha ido disminuyendo con el paso de los años, al tiempo que ha aumentado la importancia de ofrecer un nivel de servicio extremadamente alto. Esto no sólo abarca el suministro de repuestos básicos, sino también la mejora y rediseño de equipos usados en procesos rotativos de importancia crítica para crear niveles de fiabilidad más altos .
SKF ofrece una amplia gama de productos y servicios a las plantas de la industria de procesamiento de hidrocarburos (HPI) e instalaciones en yacimientos de petróleo y de gas, desde rodamientos y lubricación, hasta equipos de monitorización de la condición y servicios y análisis afines. Atender a este mercado exige una estrecha colaboración con los usuarios finales y los proveedores de sistemas de proceso, al igual que con los fabricantes de primeros equipos, Distribuidores Oficiales de SKF y otras empresas, a fin de ofrecer soluciones altamente fiables que comporten un gasto de capital bajo al usuario final.
SKF puede personalizar mejoras apropiadas partiendo de su extensa plataforma de ingeniería para equipos de maquinaria rotativa (fig. 2). Además, se puede conseguir una notable mejora de la fiabilidad y el rendimiento de los rodamientos utilizando soluciones basadas en materiales más avanzados, como rodamientos híbridos (con elementos rodantes cerámicos), aceros inoxidables superresistentes, recubrimientos de baja fricción NoWear, recubrimiento eléctricamente aislante INSOCOAT, recubrimientos anticorrosivos y jaulas de varios materiales de vanguardia como poliéter-éter-cetona (PEEK), o jaulas de latón enterizas mecanizadas, sin tensiones internas. Estas soluciones de rodamientos personalizadas pueden soportar o prevenir la corrosión general, la corrosión tensional, el deterioro de la lubricación, la selección errónea del lubricante, el desgaste, indentaciones de partículas, el paso de corriente, los gripados y daños secundarios a los soportes y rotores.
Mejora de sistemas de rodamientos
La mejora de los sistemas de eje rotativo en la industria de procesamiento de hidrocarburos con rodamientos nuevos avanzados, suele ir impulsada por la necesidad de incrementar la fiabilidad, la disponibilidad y la seguridad de los procesos, en combinación con un control minucioso del gasto de capital en instalaciones de procesos nuevas o perfeccionadas. Esto redunda en mayores ingresos y menores costes operativos, acortando el plazo de amortización de las inversiones. La aplicación de una estrategia de diseño apropiada puede determinarse considerando una gama de criterios basados en equipos de rendimiento deficiente, reduciendo el mantenimiento no planificado, disminuyendo los costes de capital y mejorando el rendimiento del equipo. Puede tratarse de:
Mejoras de maquinaria inefectiva.– Normalmente implica abordar aspectos de una o varias instalaciones que son la causa de pérdidas de producción importantes, ya sea a causa de tiempo improductivo o averías frecuentes, o por ser motivo de multas por emisiones elevadas, como en reactores químicos o compresores de gas de cola de importancia crítica.
Mejora del parque de maquinaria.– Normalmente implica trabajos en grandes instalaciones de compresores o bombas cuyos tiempos medios entre averías (MTBF) son demasiado breves, en comparación con lo que se podría obtener, por ejemplo, con compresores colectores de gas e instalaciones de bombas en refinerías. Esto ocasiona costes de mantenimiento adicionales y pérdidas de ingresos, impidiendo que ingenieros y técnicos cualificados puedan trabajar en aspectos operativos con vistas al futuro.
Ingeniería basada en el análisis de riesgo.– Constituye una oportunidad de adoptar un enfoque preventivo para descubrir riesgos en nuevos equipos de importancia crítica de demostrada inefectividad, como bombas de puesta en marcha submarina y compresores.
Diseños con bajo gasto de capital.– Este enfoque permite el uso de equipos de bajo coste empleando rodamientos altamente fiables en instalaciones antes ignoradas, como compresores de tornillo de aceite provistos de rodamientos que funcionan en concentraciones de sulfuro de hidrógeno (H2S) extremadamente altas.
Mejora de rendimiento.– El objetivo es incrementar el rendimiento y la fiabilidad de los equipos instalados para permitir, entre otras cosas, una mayor producción o tratamiento de nuevos estados de proceso, mediante, por ejemplo, la sustitución de una unidad de reserva por una segunda unidad de producción, o el incremento de la presión o el flujo en un diseño existente.
Debido a que SKF interviene, para todos los casos citados, en la selección, desarrollo y suministro de soluciones de rodamientos avanzadas en el sector de HPI y de extracción de petróleo y gas, la empresa cuenta con una lista de referencia en constante aumento. Normalmente, SKF aplica su Programa de soluciones documentadas (DSP) para el análisis de costes-beneficios a fin de asegurar que los clientes obtengan un alto valor de sus mejoras.
Rodamientos: materiales, diseños y disposiciones
Los sistemas de rodamientos están formados normalmente por una posición de rodamiento «fija» y otra «libre». La fija consta en muchos casos de dos rodamientos, uno para soportar sólo las cargas radiales y otro para fijar el eje y soportar sólo las cargas axiales. La fig. 3 muestra una disposición de rodamientos típica, instalada en muchos compresores de tornillo de aceite.
Como rodamientos fijos, en compresores, bombas y unidades de accionamiento eléctricas de alto rendimiento, normalmente se usan rodamientos de bolas. Se trata de rodamientos de bolas de contacto angular dispuestos espalda con espalda (O), rodamientos de bolas de cuatro puntos de contacto angular o rodamientos rígidos de bolas. SKF puede suministrarlos fabricados de acero para rodamientos de temple total o, para aplicaciones que exijan alta fiabilidad, con aros de acero inoxidable de gran resistencia con temple total.
Normalmente, un rodamiento libre es de rodillos cilíndricos (fig. 3), o consta de uno o más rodamientos de bolas axialmente libres en el alojamiento. Para estas disposiciones pueden suministrarse rodamientos de rodillos cilíndricos cerámicos hasta tamaños bastante grandes, para modernizar la mayoría de los rodamientos usados actualmente en compresores de tornillo de aceite. En algunos casos, debido a limitaciones de fabricación, se considera más apropiado rediseñar dichos sistemas con un rodamiento de rodillos cilíndricos, incorporando rodillos de acero inoxidable con recubrimiento NoWear, o sustituyéndolos por un diseño de rodamiento de bolas axialmente libre.
Además, SKF es el inventor del rodamiento de rodillos toroidales CARB, que puede incorporarse en diseños en los que sea preciso soportar la flexión y el desplazamiento axial del eje debidos a la dilatación del mismo. Los rodamientos CARB pueden suministrarse fabricados de acero inoxidable, con recubrimiento NoWear en los rodillos. Una disposición apropiada, por ejemplo, podría constar de dos rodamientos CARB combinados con un rodamiento de bolas de cuatro puntos de contacto angular (fig. 4, arriba) o, si se trata de una combinación de cargas axiales y radiales pesadas, un paquete de rodamientos axiales de bolas de contacto angular (fig. 4, abajo). Estas disposiciones pueden ser apropiadas, por ejemplo, para bombas de proceso «entre rodamientos» donde se presentan grandes cargas radiales. Por ejemplo, un grupo de nueve bombas de proceso pesadas incrementó su MTBF de 2 200 a más de 7 700 horas, introducido como el plazo libre de mantenimiento, al utilizar esta disposición con rodamientos SKF convencionales.
También existen varias disposiciones de rodamientos radiales y axiales con zapatas, a veces combinadas con rodamientos para soportar las fuerzas axiales. En muchos casos, la incorporación de acero inoxidable de gran resistencia para rodamientos (por ejemplo, cuando hay grandes concentraciones de sulfuro de hidrógeno), permite cambiar estos voluminosos diseños de alta fricción con capacidad de soporte de fuerzas axiales limitada y sensibles al funcionamiento en seco, por rodamientos híbridos de bolas de contacto angular.
Para instalaciones criogénicas y de alta temperatura, SKF ha desarrollado una variante especial de la versión básica de acero inoxidable de gran resistencia, mediante el empleo de un tratamiento térmico. Ello ha incrementado la estabilidad dimensional a largo plazo a temperaturas criogénicas y elevadas, y aumentado la dureza a temperaturas muy altas. Este acero se ha incorporado en un rodamiento que SKF ha diseñado especialmente para bombas criogénicas, apto para aplicaciones que funcionan con productos varios en contacto con diversos gases licuados, como petróleo (LPG), etileno (LEG), gas natural (LNG) e hidrógeno (LH2). Las mejoras de bombas criogénicas en funcionamiento continuo (fig. 1) han demostrado incrementos del tiempo medio entre averías superiores al 300%, en comparación con lo que se logra con los rodamientos totalmente de acero inoxidable actuales.
Mantenimiento centrado en la monitorización de la condición
y la fiabilidad
Las industrias del petróleo y gas, y de HPI, tienen un sinnúmero de aplicaciones que usan rodamientos en los equipos de procesos, como bombas, compresores y reactores químicos. La función de esos equipos varía, abarcando desde instalaciones básicas con unidades de reserva, hasta maquinaria de importancia crítica en el proceso, situada en lugares extremadamente exigentes sin posibilidad de disponer de equipos de reserva. Por ejemplo, se usan bombas en condiciones bastante estables en refinerías, mientras que las bombas de puesta en marcha submarina o las criogénicas en continuo funcionamiento en terminales de LNG, plantas de gas y químicas, funcionan en condiciones problemáticas. A través de su grupo de sistemas de fiabilidad, SKF cuenta con amplios conocimientos para detectar problemas futuros a través de la monitorización de la condición. La monitorización de la condición de los equipos rotativos puede realizarse estudiando la tendencia de las señales, en combinación con análisis de frecuencias mediante filtros, etc., para reforzar señales específicas de componentes de rodamientos u otras piezas de los equipos, o señales relacionadas con los procesos.
La información de vibraciones de este tipo puede usarse para requerir mantenimiento cuando se alcanzan niveles de vibraciones cercanos al valor que causa daños secundarios graves al equipo. El ejemplo incluido en la fig. 5 muestra la tendencia de las vibraciones de un compresor de paletas para gases de nafta usado en una planta de procesamiento venezolana en un yacimiento petrolífero explotado por Chevron y PDVSA. Monitorizando el compresor, el personal de SKF in situ pudo aplicar procedimientos de mantenimiento antes de que las vibraciones alcanzaran un nivel peligroso, con lo cual la reparación pudo programarse con más eficiencia y se redujeron significativamente los costes de reparación.
Asimismo, SKF efectúa análisis de riesgo y dirige la implementación de programas de mantenimiento centrados en la fiabilidad en instalaciones de proceso a través de sus empresas de servicio activas en el sector del petróleo y el gas.
Mejora adaptada al sulfuro de hidrógeno
En el norte de Alberta, en Canadá, hay varias explotaciones a gran escala de arena petrolífera, con plantas de concentración y refinado para obtener petróleo bajo en azufre. Una de las mayores instalaciones de la zona es la de la empresa conjunta Syncrude, que alcanza una producción de 315.000 barriles diarios. Los hidrocarburos pesados extraídos de la arena petrolífera contienen azufre. Se aplica craqueo por hidrógeno para obtener hidrocarburos más ligeros, pero durante el proceso también se forma sulfuro de hidrógeno (H2S). La eliminación del sulfuro de hidrógeno es sumamente importante y se realiza mediante un proceso denominado stripping. No obstante, queda gas de cola que se tiene que comprimir antes de su tratamiento ulterior. En el proceso Syncrude el gas es comprimido por un compresor de tornillo de aceite, adaptado al flujo de gas. Este diseño tiene muchas ventajas técnicas y económicas en comparación con otros compresores alternativos, como las variantes de pistón y las exentas de aceite que, además de tener un coste inicial alto y un mantenimiento dificultoso, sufre averías problemáticas. Debido a un cambio del proceso, la concentración de sulfuro de hidrógeno en el gas de cola experimentó un crecimiento significativo hasta entre el 30 y 40%, provocando graves perturbaciones en el funcionamiento del compresor de tornillo, debidas a daños en los caminos de rodadura y elementos rodantes ocasionados por mecanismos de agrietamiento producidos por tensiones. Estas averías en los rodamientos provocaron trastornos caros en la refinería debido a la desconexión de compresores y fallos causados por vibraciones que conducían a averías de rodamientos.
Por ello el personal de ingeniería de Syncrude empezó a estudiar mejoras potenciales del sistema de rodamientos y las condiciones del proceso. En colaboración con SKF y BC Bearings, Distribuidor Oficial SKF, se decidió personalizar una solución, que comprendía el uso de varias tecnologías de nuevos materiales en curso de desarrollo en SKF. La mejora abarcaba un nuevo acero inoxidable de gran resistencia para rodamientos, y un diseño de rodamientos híbridos de gran tamaño para los rodamientos de bolas de cuatro puntos de contacto angular y rodamientos de rodillos cilíndricos. Esta solución ha demostrado tener un comportamiento excelente en cuanto a la vida útil del rodamiento (que ha pasado de un MTBF de 3.800 horas a más de 23.000 horas sin averías) y los niveles de vibración, además de la resistencia a interrupciones del aceite lubricante. Ello ha incrementado notablemente la fiabilidad y disponibilidad de la mejora y del proceso de refinado, y reducido considerablemente las emisiones de dióxido de azufre (SO2) causadas por la combustión.
Conviene destacar que el caso del sulfuro de hidrógeno constituye una mejora avanzada, que comprende una instalación de compresor con rodamientos personalizados para la máquina en servicio y repuestos. En muchos otros casos, será posible usar soluciones de rodamientos de SKF disponibles (por ejemplo, rodamientos SKF Explorer, rodamientos PumPac con un par dúplex de 40º y 15º, rodamientos aislados eléctricamente INSOCOAT, jaulas de PEEK poliméricas, etc.) para bombas, compresores y unidades de accionamiento, o rodamientos híbridos con aros de acero para rodamientos convencional o versiones NoWear de rodamientos estándar con rodillos de baja fricción recubiertos.
SKF está bien preparada para proveer a la maquinaria rotativa de las industrias de HPI y del petróleo y gas de rodamientos con un mayor rendimiento, a fin de abordar los requisitos cada vez más elevados de fiabilidad, disponibilidad y seguridad.