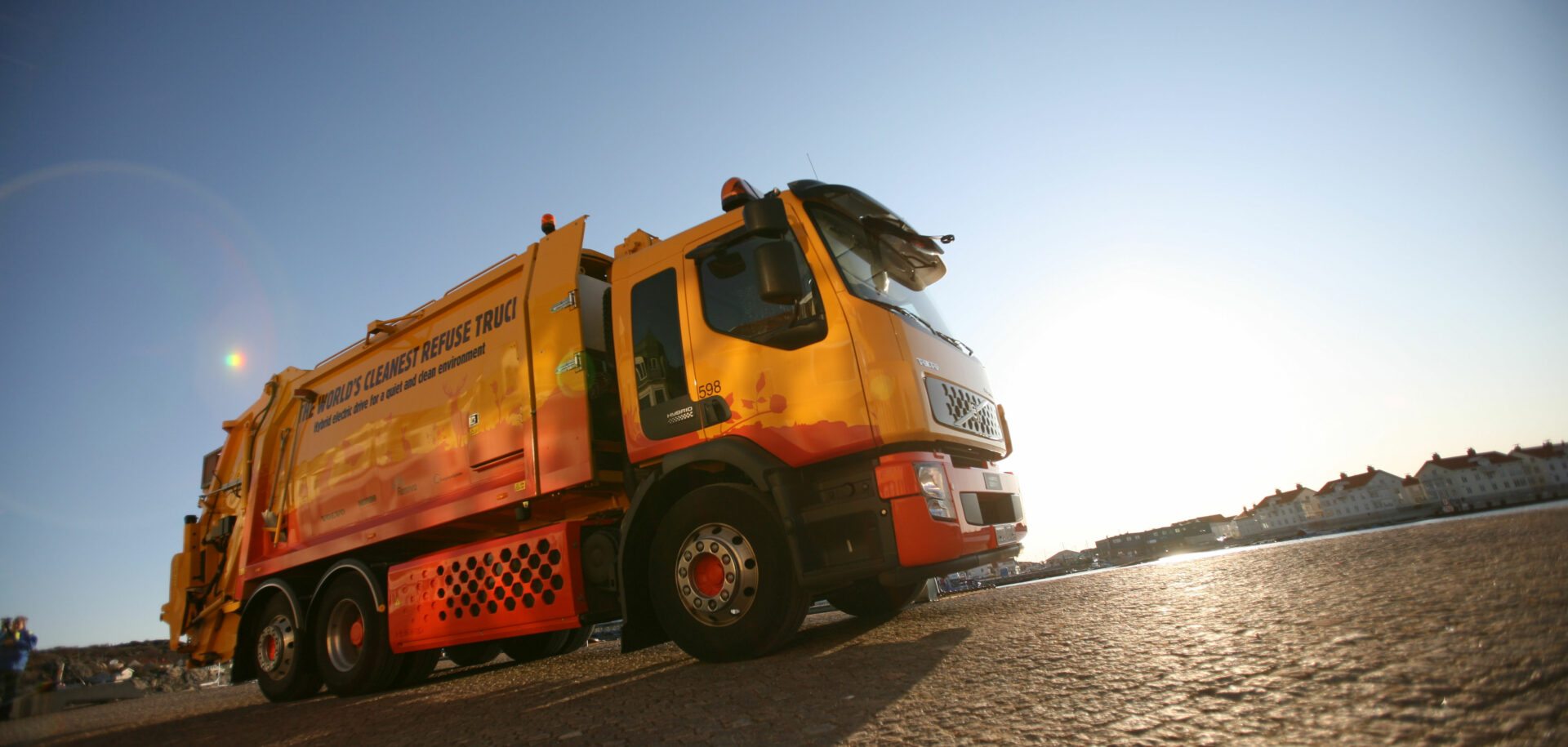
De l’utilité des déchets
Et si l’on considérait nos déchets autrement ? Grâce aux évolutions technologiques, Renova en fait une énergie très utile.
Dans l’ouest de la Suède, le centre de valorisation des déchets Renova fournit chaque année environ un tiers du chauffage urbain de la communauté de communes de Göteborg. Elle couvre également 5 % des besoins en électricité de Göteborg, deuxième ville du pays. Voilà qui n’est pas si mal étant donné que ces énergies sont produites à partir de déchets qui ne peuvent être recyclés.
Le groupe Renova
Le centre de valorisation thermique Renova de Sävenäs, en Suède, fait partie du groupe Renova, propriété de dix communes de l’ouest du pays. Le groupe propose des services de ramassage et de transport des déchets et des matériaux recyclables ainsi que des prestations, des conseils et des formations en matière de gestion des déchets aux propriétaires bailleurs et à l’industrie du bâtiment.
Les déchets qui arrivent à l’usine de Sävenäs sont incinérés et transformés en énergie. L’énergie tirée d’un kilo de déchets peut chauffer suffisamment d’eau pour une douche de sept minutes ou produire trois heures d’électricité pour un ordinateur.
Chiffre d’affaires : 124 millions d’euros.
Effectif : 780 salariés.
Déchets traités : 1 140 000 tonnes.
Production de chaleur urbaine :
1 500 000 MWh.
Production d’électricité :
250 000 MWh.
(chiffres 2016)
Implantée dans la zone industrielle de Sävenäs, l’usine incinère des déchets toute l’année, 24h/24. Chaque tonne brûlée produit 3,3 MWh d’énergie sous forme d’électricité et de chaleur.
Aujourd’hui, nous avons amélioré la fiabilité opérationnelle.
Göran Klamas, directeur de l’usine Renova
Trois fours géants se chargent de cette mission. Chacun d’eux est équipé de ventilateurs primaires, lesquels injectent de l’oxygène pour maintenir la combustion à une température stable de 1 000 °C. Des ventilateurs secondaires font circuler l’air dans la chambre de combustion et des ventilateurs de recirculation sèchent les déchets.
Ces ventilateurs sont indispensables au bon fonctionnement de l’usine. La panne d’un seul d’entre eux peut coûter jusqu’à 100 000 euros à Renova. Leur fiabilité est donc déterminante. À cette fin, Renova et SKF collaborent depuis une dizaine d’années pour éviter tout arrêt imprévu. « Avant, les interventions urgentes pour réparation pouvaient nous faire perdre jusqu’à 1 000 heures de production par an, rappelle Göran Klamas, directeur de l’usine pour la division recyclage du groupe Renova. Aujourd’hui, notre fiabilité opérationnelle s’est accrue et nous n’arrêtons tout que pour les opérations d’entretien programmées. Ceci a considérablement amélioré notre productivité. »
La maintenance proactive (PRM)
Comme son nom l’indique, le programme de maintenance proactive (PRM) SKF recherche l’origine des défaillances et propose des mesures pour éviter leur répétition. SKF diagnostique de manière systématique les causes des dysfonctionnements en mettant en place des activités de maintenance préventive découlant des bonnes pratiques ainsi que d’autres procédures. Grâce au contrat de service PRM, SKF aide le centre de valorisation thermique Renova dans l’ouest de la Suède à améliorer son rendement opérationnel par des relevés, des activités d’entretien et l’analyse des roulements et des lubrifiants.
Cette réussite peut être largement attribuée à la collaboration entre les deux partenaires.
Au cœur de celle-ci, un contrat de service de maintenance proactive (PRM) SKF a largement relevé la stabilité opérationnelle des machines tournantes du centre (voir encadré).
Conformément aux termes du contrat, SKF a répertorié et catalogué près de 40 machines stratégiques Renova et peut transmettre rapidement des bilans sous forme de rapports et autres représentations visuelles montrant là où des interventions supplémentaires sont nécessaires. Ces relevés donnent au service de maintenance une image claire des éventuels problèmes à venir dans certains équipements et lui permettent d’intervenir avant toute aggravation de la situation. « Il peut s’agir d’un défaut d’alignement sur une machine auquel on a remédié à maintes reprises, mais qui persiste, explique Jennie Lindahl, coordinatrice de l’entretien chez SKF qui procède aux relevés dans l’usine depuis de nombreuses années. En mesurant les formes de flexion en fonctionnement [ODS], nous pouvons identifier la cause, laquelle peut être, par exemple, l’irrégularité d’un sol qui doit être rectifiée. »
Imposée par les règles strictes entourant la protection de l’environnement, l’analyse des lubrifiants peut également contribuer à détecter des problèmes. « Elle peut révéler des causes aux arrêts-machines complètement différentes de ce que l’on pensait. Il peut s’agir d’une lubrification incorrecte, de témoins de présence d’eau ou de températures de roulements trop élevées, ce qui peut accroître le risque de formation de substances chimiques nocives. La graisse peut s’oxyder, la viscosité peut changer et il peut se former un acide qui endommagera la surface des roulements. » En fait, de telles analyses peuvent contribuer à éviter une éventuelle catastrophe.
Heureusement, on peut éviter des complications aussi graves en mettant en place des activités de maintenance proactive. En 2016, l’usine Renova n’a connu aucun arrêt d’urgence contre cinq il y a dix ans. Grâce au contrat de service PRM, deux interventions de maintenance planifiées seulement ont eu lieu en 2016, soit moitié moins que dix ans auparavant.
Les améliorations apportées à la fiabilité opérationnelle se sont traduites par une baisse des coûts de maintenance pour Renova, libérant ainsi des ressources financières pour d’autres investissements. « La perte de production d’énergie [due aux arrêts non planifiés] s’élève à environ 100 000 euros par jour, précise Göran Klamas. Aujourd’hui, les ventilateurs sont stables et on peut consacrer plus de temps à la recherche de solutions pour obtenir une combustion encore plus performante et respectueuse de l’environnement. »