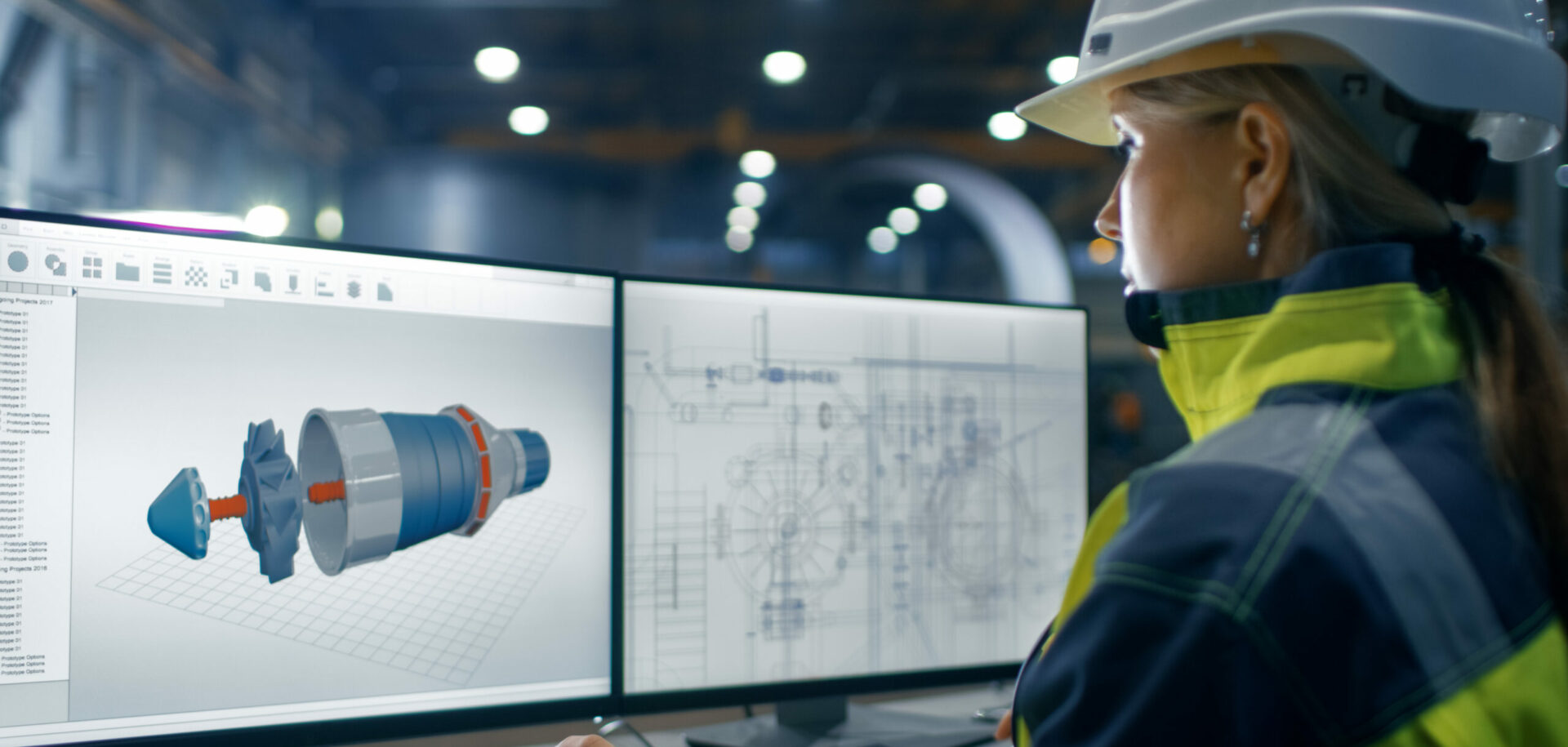
Getting the inside view of bearing loads, thanks to a little touch of magic
SKF has developed techniques that provide engineers with a better insight into the conditions within a bearing when the equipment into which it is fitted is in operation. This has resulted in two distinct products that are proving their worth in a range of applications from wind-power generation to paper making.
SKF has developed techniques that provide engineers with a better insight into the conditions within a bearing when the equipment into which it is fitted is in operation. This has resulted in two distinct products that are proving their worth in a range of applications from wind-power generation to paper making.
The Magic Roller system and the load measuring plate have the common job of measuring load. Measuring load is an important parameter because it provides information about what a bearing system is experiencing and can affect bearing type, size and capacity.
Bearings are fundamental components in machines transmitting power and forces between its internal components. The designer’s choice of a bearing and its size is often determined by laboratory tests or simulations, including a number of assumptions and safety factors. If the designer has hard facts as input to his dimension criteria, he can refine his product and create a more optimized product in terms of weight, efficiency and safety.
So, the ability to know the true loads acting in a machine provides opportunities not only for improving the machine design but also for controlling the machine process.
Measuring the bearing forces in a machine gives a precise indication of how much the machine is loaded. Take a machine where raw material is fed into a process involving, for example, pressing, crushing or rolling between two large rolls. The force exerted on the bearings of the rolls can be measured and enables the determination of the most effective feed rate of the raw material. A further example is web tension, where paper, textile or foil is stretched and wound between rolls. The stress tension of the material is crucial, and the load in the bearings supporting the rolls is directly proportional to the tension.
Another use of measuring load is the monitoring ability. Continuous logging of load gives the possibility of detecting overloading and time of event from a predetermined limit long after it has taken place, similar to a “black box” in aircrafts.
The Magic Roller and the measuring plate represent different approaches to load measurement. The measuring plate has been developed mainly for on-line measuring and quantifying radial loads. It is a product that does not require any redesign of the bearing that it is measuring.
The load measuring plate, which will be launched soon, is a new product development for which SKF has obtained a patent. A unique tailored plate with sensors is integrated with the SKF plummer block housing into one unit. It has been designed to overcome problems associated with traditional load measuring blocks related to size and matching of these components with the housings. The plate is bolted onto the foundation and followed by attachment of the housing onto the plate.
At two positions, equally positioned inside the plate, two strain gauge bridges are attached to an internal beam. While loaded, the shear strain in the beams is measured and a signal proportional to the load applied to the plate is received. From this the radial load and the direction of radial load is displayed on-line. Alternatively, the load direction or the vertical and horizontal components of the load can be given. The accuracy is excellent, with an error of less than 0.5 %. An analogue or digital output signal can be chosen, which can serve most common customer control systems. The maximum plate size has not yet been determined, but the complete assortment of SNL housings up to housing size 532 will be covered, which means a plate size of up to 550 x 160 mm.
For many applications such as in the paper industry, for example, where material is transported through rolling movement, the control of the process is handled by measuring the web tension. With the SKF plate and housing, the height and weight of the measuring and adaptor plates can be considerably reduced, making it a simple and straightforward technique.
By contrast, the Magic Roller is a complex product that opens up the opportunity to measure a range of load parameters. Because of its sophistication and the fact that the roller has to be tailored to the specific application, it is a product that has to be designed within the application. This requires close collaboration between customer and SKF engineers.
The first Magic Roller tests were made in 1998, and a number of applications have been developed incorporating the system.
The SKF Magic Roller enables load measurements to be collected at special bearings to provide a unique load measuring system that can be used in a great variety of applications. One roller per bearing row is equipped with a sensor to measure roller load, and as they orbit inside the bearing, the rollers communicate the roller load through radio signals, which are logged continuously by a portable computer.
The roller itself serves as an excellent measuring device because of its geometrical precision and is provided with a strain gauge bridge inside a hollow compartment.
A telemetry unit is mounted onto the roller, together with a module for electric powering. These two components constitute a transmitter of 40 mm diameter and 35 mm length.
Since the small module for power rotates and needs external electric supply, this is transferred through an air gap using the induction principle via a larger coil outside the bearing ring.
The radio signal transmitted from the bearing outside is recognized by a receiver and converted in to an analogue signal and recorded on a portable computer. Data acquisition is performed according to customer requirements and sent to SKF in Sweden for calculation and analysis.
Both the Magic Roller and the measuring plate are important tools in engineers’ armory to discover real conditions within bearing applications so that better information can be gained about the design parameters for the bearing systems within equipment. This leads to improved design and longer operation of the equipment.