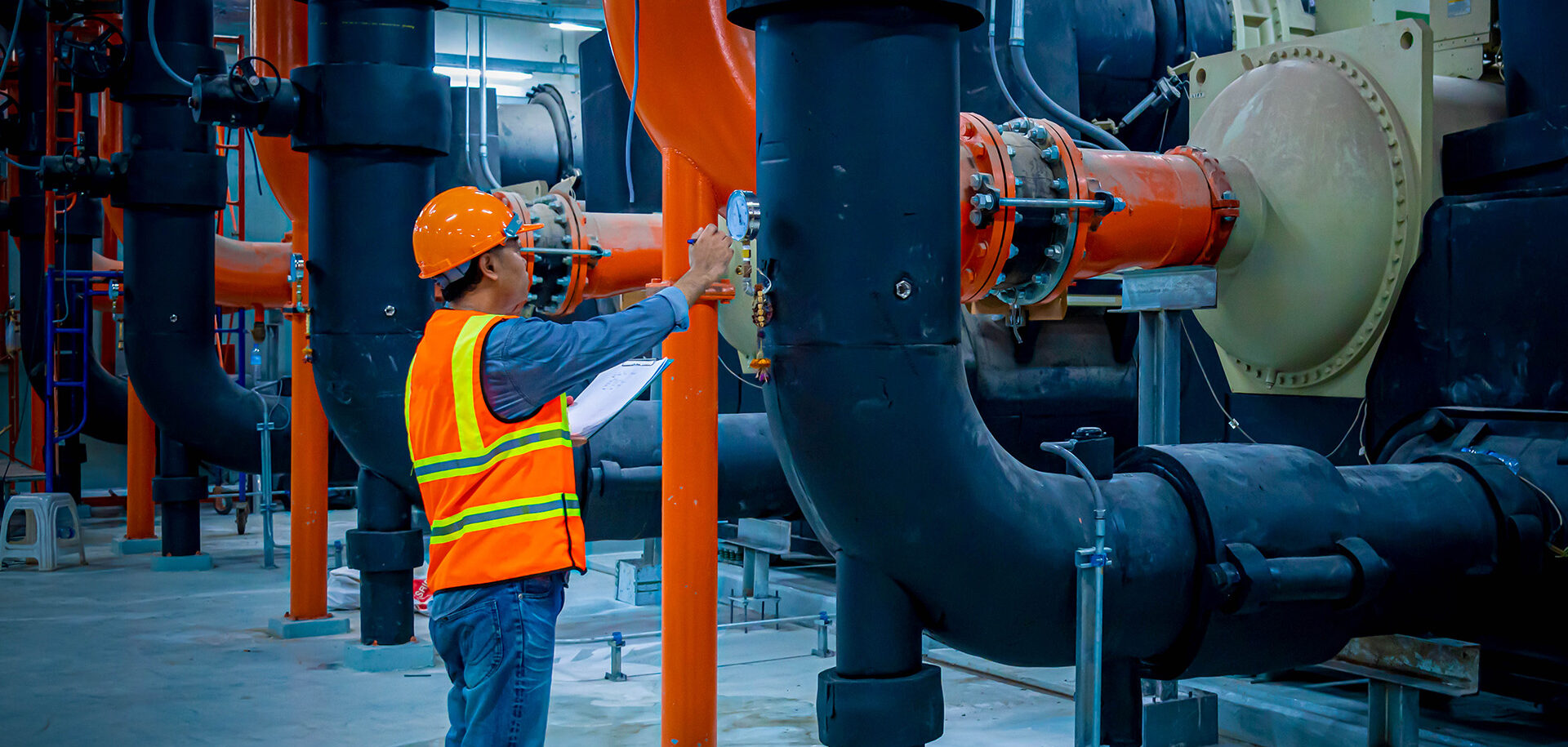
Heat pumps favour global drive for zero emissions
There is reason to believe that as the world seeks to drive down carbon emissions, heat pumps will become the dominant heating system. However, the growth of this solution will depend on finance, political will and technological innovation.
The advantage of heat pump technology is that heat can be collected from a variety of renewable sources, such as air, water, ground and waste heat, and it produces no direct local emissions. Industrial heat pumps and heat pumps for district heating often use waste heat derived from industrial processes in the food & beverage, pulp & paper, chemical and petrochemical industries as well as refineries, cement and brickmaking and even large computer/data centres that need significant cooling for their operations.
Eliminating fossil fuels while moving to electrical generation from sustainable sources has the added benefit of being a more efficient use of renewable heat energy and makes electricity consumption more flexible, which in turn helps to stabilize power grids.
Heat pumps are projected to be the predominant technology for both domestic and industrial heating applications. The International Energy Agency forecasts that as much as 90 percent of the world’s space and water heating needs could be fulfilled by heat pump systems. As of 2021, heat pumps supplied only 3 to 5 percent of the world’s needs, and less than 10 percent of global process heat comes from renewable sources.
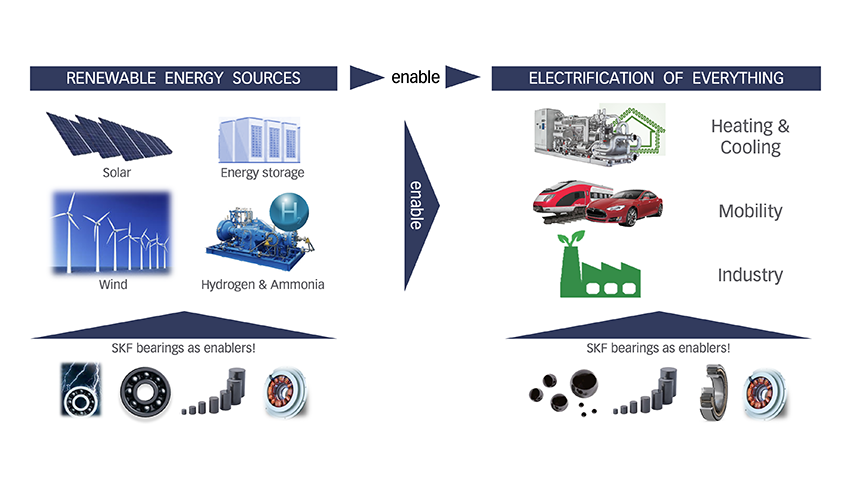
Ambitions for heat pumps
According to the EU strategy for Energy Systems Integration, the European Commission predicts that by 2030 40 percent of all residential and 65 percent of all commercial buildings will be heated by electricity, with a consequential need for 50 million heat pumps. The UK has its own ambitious plans for heat pumps, with a target of installing 600,000 heat pumps a year for home, schools and hospitals by 2028.
So, with the global push to move to green energy, heat pump technology is set to undergo dramatic growth. Between 2021 and 2027 the market for industrial heat pumps is forecast to grow by more than 10 percent, while heat pumps used in district heating are expected to grow from the 2020 level of USD 450 million (EUR 396 million) with a compound annual growth rate of 7 percent between 2021 and 2026.
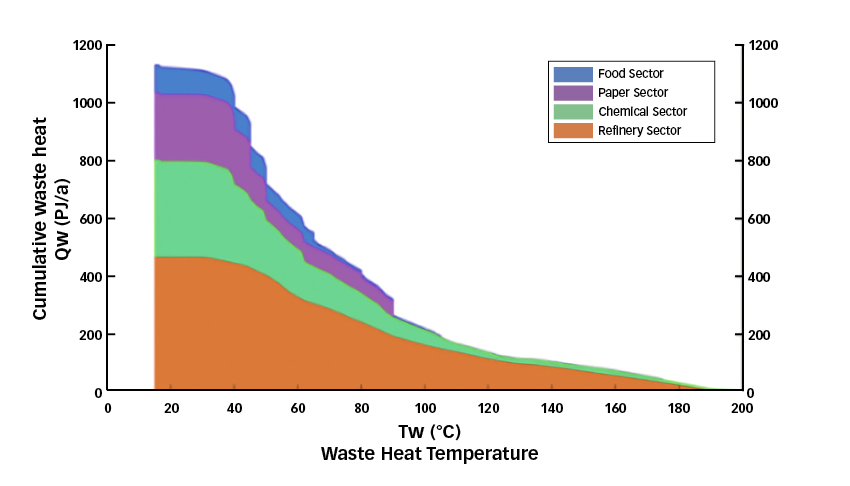
Investment a big challenge
The advantage of heat pump technology is that heat can be collected from a variety of renewable sources.
Investment is one of the key enablers for the heat pump industry. To meet the EU’s ambition to reach its goals for net-zero emissions, a monthly investment of at least 200 million euros (more than USD 227 million) over decades would be needed. Globally, the estimated cumulative investment needed by 2050 in renewable heat for industry (solar thermal, geothermal, biomass and electrification including heat pumps) alone adds up to EUR 3.7 trillion. Electrification represents 65 percent of this.
In addition, the higher cost of electricity, compared with that of oil and gas in markets such as the US and coal in markets such as China, is a barrier to growth, despite the environmental damage being done.
Technical hurdles
These considerations aside, there are also technical hurdles to overcome, particularly for the larger installations required for industrial and district heating systems. One example is the use of ammonia in large district heat pumps. Ammonia leads to very high thermodynamic efficiency but can affect bearing service life.
As temperature demands for industry are higher than domestic heating, achieving temperatures of higher than 100 °C (e.g., 150 to 300 °C) requires overcoming technical as well as commercial hurdles.
Higher temperatures can lead to lubrication and thermodynamic issues, and the coefficient of performance for such heat pumps is relatively low. In addition, heat pumps require special refrigerants that may be more chemically active and corrosive, and much higher working temperatures put increased demands on materials, seals and bearings.
A promising future
Companies including SKF are already working on developing the ideas, technologies and strategies that will bring heat pumps into the mainstream of industrial heating applications. The German Aerospace Centre (DLR) Institute of Low-Carbon Industrial Processes has already developed prototype models that can deliver heat at 500 °C.
One company, Envola GmbH, has launched the first heat pump with integrated storage tanks, making it both economical and environmentally friendly. Another important development is the incorporation of digital systems to control every aspect of the operation, so that demand can respond to load and the system can be optimized in its electricity use, load profiles and operating cost.
Heat pumps will be at the heart of a more sustainable future for our planet. The speed at which this transformation takes place will depend on politics and finance, backed by industrial support.