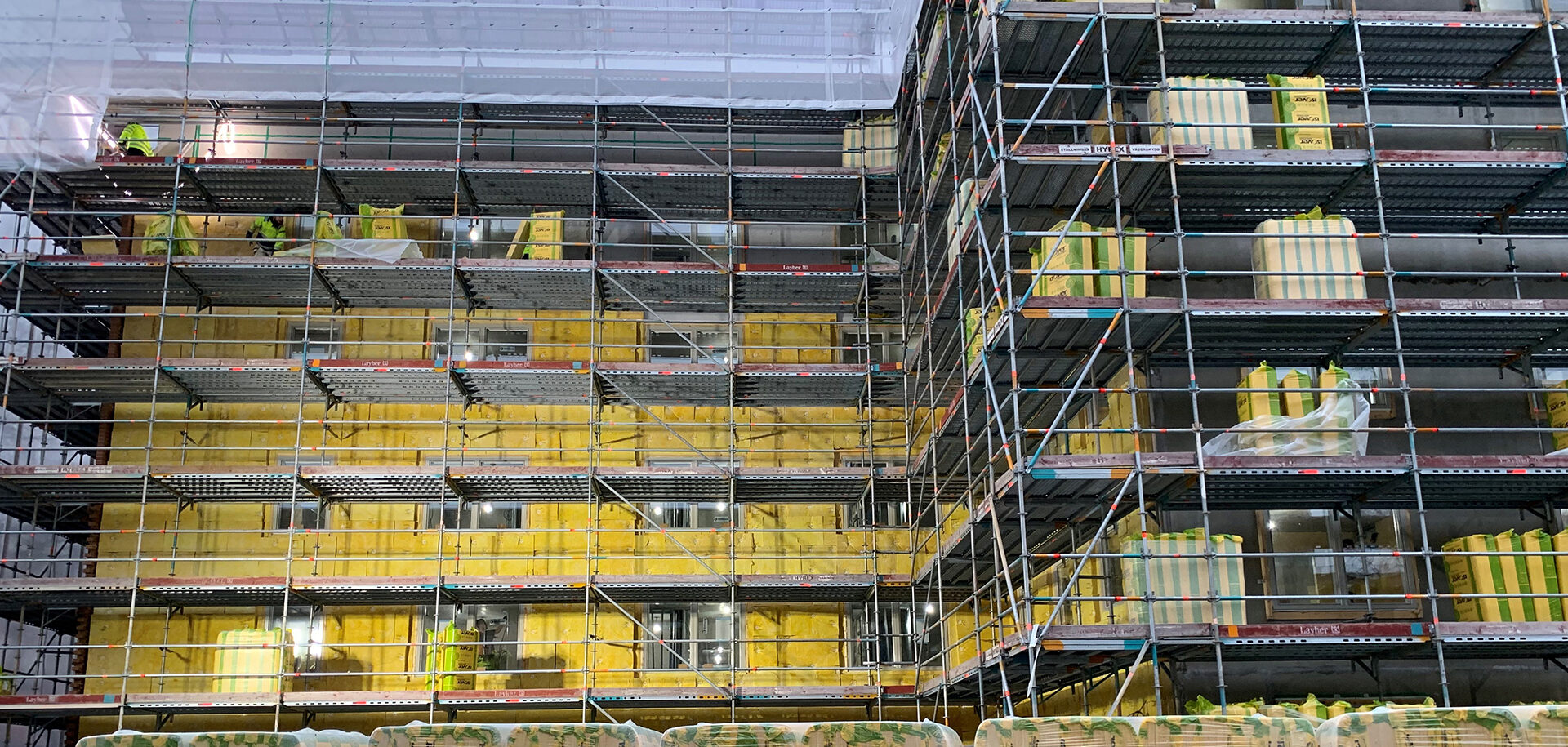
Insulating for success: protecting machines against failure
Maintenance teams at Saint-Gobain Isover are using the power of digital technology to boost the output of a product that could help save the planet.
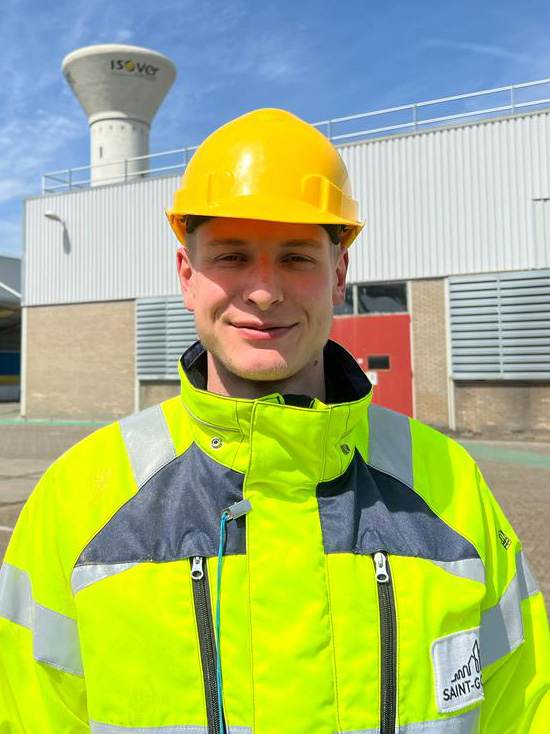
How can we stay comfortable at home and at work without heating up the atmosphere? Buildings are responsible for almost 40 percent of energy-related carbon emissions globally, and more than two-thirds of those emissions come from the energy used to keep the buildings warm in winter and cool in summer.
If the world is to meet its goals for greenhouse gas reduction, it needs to accelerate the transition to cleaner, more efficient buildings. That’s going to require investment in new technologies, such as rooftop solar panels and heat pumps powered by renewable electricity. But one of the most effective ways of reducing a building’s carbon footprint is thermal insulation, and it is also one of the simplest.
Good thermal insulation stops buildings from leaking valuable heat through their walls and roofs. It’s simple, proven and cost-effective too. In most buildings, owners will recoup the cost of additional insulation in just a few years through savings in their energy bills.
Saint-Gobain’s Isover plant at Etten-Leur in the Netherlands has been in the energy-efficiency business since 1962. The facility manufactures around 45,000 tonnes per year of glass wool insulation, producing mats for roof insulation as well as a loose-fibre product that can be injected into cavity walls or blown into loft spaces.
The Etten-Leur factory operates three glass wool production lines, and an additional production line that makes the glass-fibre material that is used as a facing on some of its products. Bas Beishuizen is a maintenance engineer at the site. His job is to ensure that the equipment on those lines always runs reliably and efficiently.
Glass wool production is a high-speed, high-volume, energy-intensive activity, so the maintenance team has a lot of equipment to look after. “We have 57 critical assets across the site,” Beishuizen says. “Those are mainly pumps and ventilators, but they can be quite large pieces of equipment. Our biggest ventilators are powered by 500-kilowatt motors, for example.”
How can we stay comfortable at home and at work without heating up the atmosphere? Buildings are responsible for almost 40 percent of energy-related carbon emissions globally, and more than two-thirds of those emissions come from the energy used to keep the buildings warm in winter and cool in summer.
If the world is to meet its goals for greenhouse gas reduction, it needs to accelerate the transition to cleaner, more efficient buildings. That’s going to require investment in new technologies, such as rooftop solar panels and heat pumps powered by renewable electricity. But one of the most effective ways of reducing a building’s carbon footprint is thermal insulation, and it is also one of the simplest.
Good thermal insulation stops buildings from leaking valuable heat through their walls and roofs. It’s simple, proven and cost-effective too. In most buildings, owners will recoup the cost of additional insulation in just a few years through savings in their energy bills.
Saint-Gobain’s Isover plant at Etten-Leur in the Netherlands has been in the energy-efficiency business since 1962. The facility manufactures around 45,000 tonnes per year of glass wool insulation, producing mats for roof insulation as well as a loose-fibre product that can be injected into cavity walls or blown into loft spaces.
The Etten-Leur factory operates three glass wool production lines, and an additional production line that makes the glass-fibre material that is used as a facing on some of its products. Bas Beishuizen is a maintenance engineer at the site. His job is to ensure that the equipment on those lines always runs reliably and efficiently.
Glass wool production is a high-speed, high-volume, energy-intensive activity, so the maintenance team has a lot of equipment to look after. “We have 57 critical assets across the site,” Beishuizen says. “Those are mainly pumps and ventilators, but they can be quite large pieces of equipment. Our biggest ventilators are powered by 500-kilowatt motors, for example.”
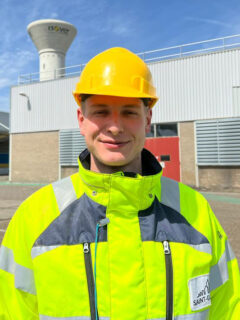
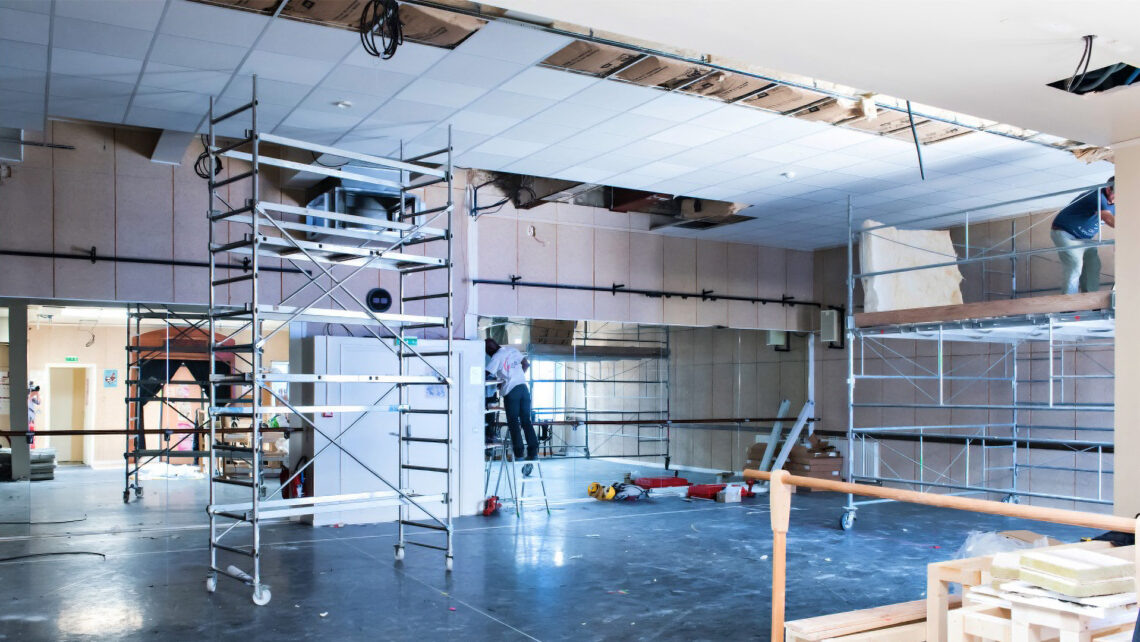
Preventing the unexpected
The failure of any critical asset could force a line shutdown, potentially scrapping an entire batch of material. The maintenance team at Etten-Leur tries to adopt preventive and condition-based approaches wherever it can. “For improving our maintenance of bearings, we start out by using SKF QuickCollect hand-held vibration sensors. We determine the frequency for the vibration measurements by how important and critical the component is. A technician will take the measurements and, through a joint effort with SKF, the bearings will get analysed. This is so we can use that data to see if there are indications of problems.”
With the help of condition monitoring experts from SKF, the hand-held equipment quickly began providing useful insights.
Bas Beishuizen, maintenance engineer at Saint-Gobain Isover
With the help of condition monitoring experts from SKF, the hand-held equipment quickly began providing useful insights. Analysis of the vibration spectrums showed, for example, that some bearings were suffering from poor lubrication. “When we looked into the issue further, we found that lubrication points on some machines were in the wrong position, so the grease wasn’t getting to the right place in the bearing,” Beishuizen says. “Once we knew the root cause, it was simple to fix.”
Vibration measurement doesn’t only reveal problems with bearings. It can also detect issues elsewhere in the equipment. “One common problem within Saint-Gobain Isover is an imbalance on the ventilators,” he continues. “Contamination can build up on the fan blades, which makes them less efficient and could lead to failure.
Vibration measurements allow the maintenance team to work with the operations team to clean and balance the fans that are polluted during a shutdown. This can reduce breakdowns caused by bearings or motor mountings failing due to high vibrations.”
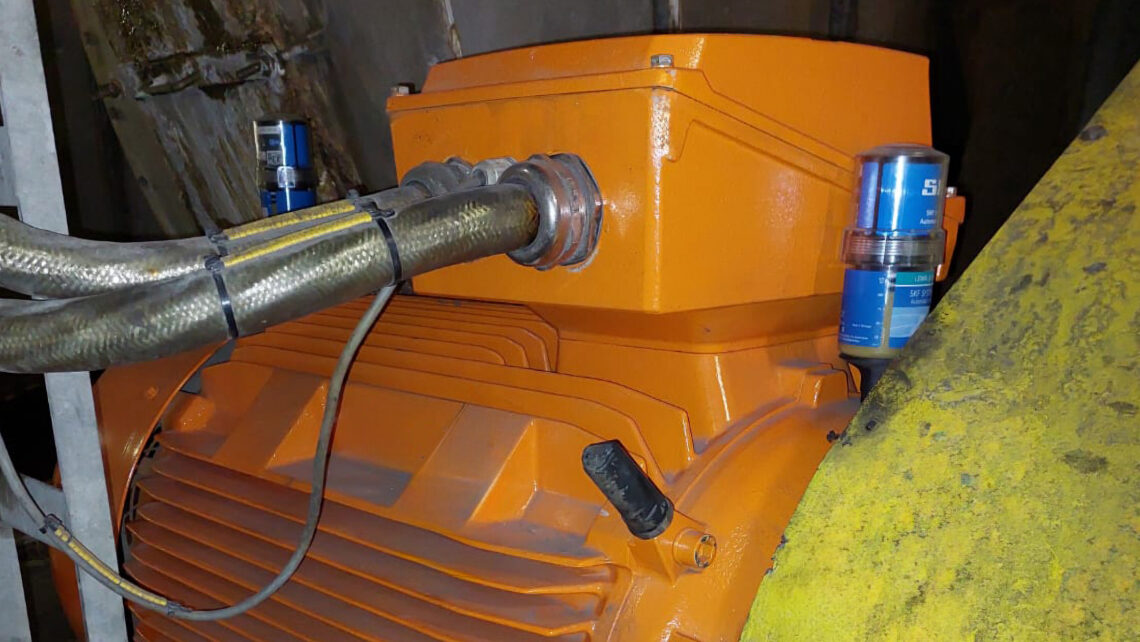
Getting on-line
Encouraged by the success of the vibration measurements, Beishuizen was keen to go further with the approach. “With hand-held measurements, you get really useful data, but this is only done a certain number of times per year,” he says. “The maintenance team wants more data, so more frequent measurements are needed to obtain and build up good data.”
To do that, the Etten-Leur team made the switch to online monitoring technology. It has installed SKF IMx-1 fixed sensors on critical machines across the facility. These compact, battery-operated devices continually record vibration and temperature data and transmit it via a wireless-mesh radio network to a gateway, which sends it on to the SKF cloud using a 4G mobile connection. “Within Saint-Gobain we already run our own maintenance management software platform, but thanks to the API connection from SKF to Saint-Gobain we can pull all the vibration data and combine it with all our other data,” Beishuizen says. “This allows us to get all the data organized at one location.”
Continuous vibration monitoring has multiple potential benefits for the plant. If vibration suddenly and unexpectedly increases, for example, the system can alert the maintenance or operations team to trigger an investigation. Recording data over time, meanwhile, will help the team to spot more gradual trends that may indicate that the performance of a machine is degrading.
“The maintenance team is developing a condition monitoring dashboard to create condition-based maintenance within the Isover plant,” says Beishuizen. “The dashboard gives us an overview of all our critical assets and prioritizes the machines that need attention.
“We stop each line several times a year for scheduled maintenance,” he says. “We’d like to get to the point where we know from the data exactly what actions we will take during each shutdown.” This would improve maintenance and shorten the stops; inspections before the stops are already done through the analyses.
But that’s just the next step, Beishuizen says. The maintenance team has plenty of other ambitions for the plant’s digitized maintenance approach. “Combining condition data with operations and maintenance data, we can start to build a more complete picture of how our assets perform and how and when they fail,” he says. “That will allow us to focus our efforts on projects that improve reliability and efficiency across our operations.”
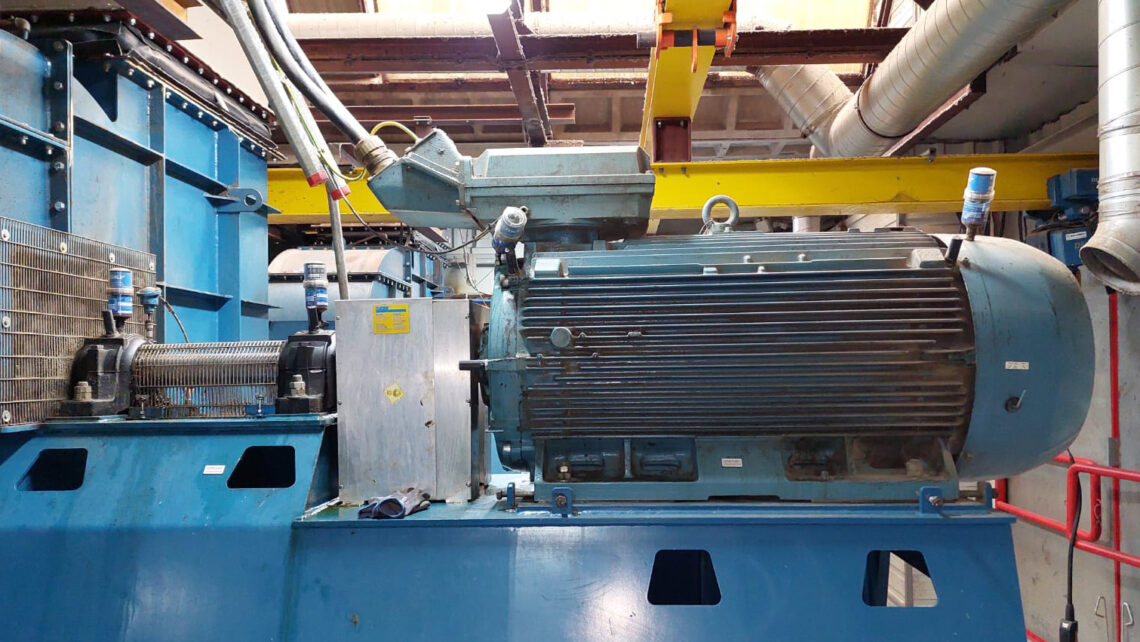
All in a spin
Glass wool production works a little like the fairground candyfloss machines that spin melted sugar into a fluffy treat, but its processes are significantly hotter, and they operate on a much bigger scale.
Batches of material are first mixed, then heated in a furnace to around 1400 ºC. Traditionally those materials were just the basic ingredients of glass: sand, soda ash and limestone. Today, however, around half the mixture used in Isover furnaces is recycled glass. That reduces consumption of virgin materials and saves energy in production, since glass melts at a lower temperature than sand.
The liquid glass is then pumped through a centrifugal spinner, which stretches it out into fine hair-like fibres. To produce glass wool mats, the fibres are sprayed with a binder and shaped into blankets. The blankets next pass through a curing oven, where they are compressed to their final thickness. The cured binder holds the fibres together where they cross, creating a durable material that can be squashed down to a tenth its volume for transport. It springs back to full size when unpacked. Depending on the end application, a glass-fibre facing may be glued onto the blankets to further improve durability and ease of handling.
The perfect dose of lubrication
After experiencing the impact of lubrication failures on critical assets, the Etten-Leur factory has adopted another SKF technology across many of its machines. “We know that a bearing might require 50 grams of grease for six months of operation,” says Bas Beishuizen, maintenance engineer at Saint-Gobain Isover. “But you won’t get the best performance if you add all that lubricant at once; it is also not always clear whether the bearing is actually lubricated.”
Instead, the factory has installed SKF TLDD connected single-point lubricators. These devices provide regular small doses of lubricant to each bearing from an on-board reservoir at a predetermined rate. They report their status to the SKF cloud via a wireless network and a gateway to the 4G mobile network, so the maintenance team knows that the bearings have been lubricated, when each unit requires refilling and if a problem has interrupted the lubricant flow.