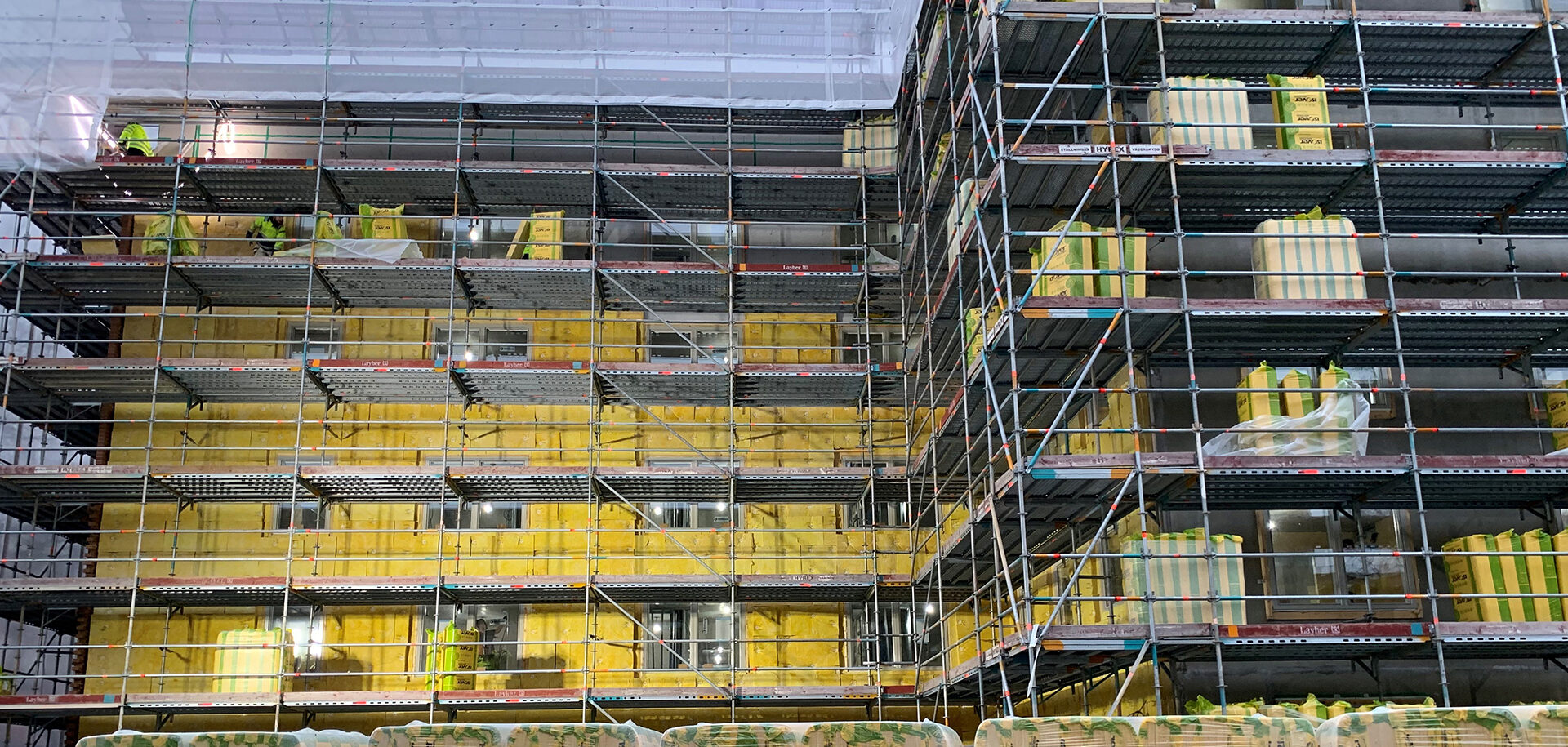
Aislar con éxito: proteger las máquinas de las fallas
Los técnicos de mantenimiento de Saint-Gobain Isover aprovechan la potencia de la tecnología digital para aumentar la fabricación de un producto que podría ayudar a salvar el planeta.
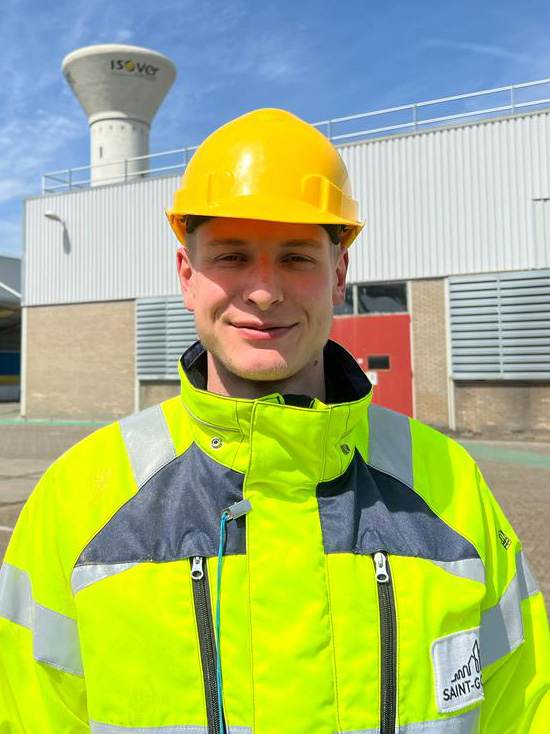
¿Cómo mantener el confort en casa y en el trabajo sin calentar la atmósfera? Los edificios son responsables de casi el 40 % de las emisiones mundiales de carbono derivadas de la energía; y de esas emisiones, más de dos tercios proceden de la energía utilizada para calentar los edificios en invierno y refrigerarlos en verano.
Si el mundo quiere cumplir sus objetivos de reducción de gases de efecto invernadero, debe acelerar la transición hacia edificios menos contaminantes y más eficientes, invirtiendo en tecnologías nuevas, como paneles solares en los tejados y bombas de calor conectadas a fuentes de electricidad renovables. Uno de los recursos más efectivos, y también uno de los más sencillos, para reducir la huella de carbono de un edificio es el aislamiento térmico.
Con un buen aislamiento térmico, los edificios ya no pierden un calor valioso a través de las paredes y el tejado. Es sencillo, está probado y, además, es rentable. En la mayoría de los edificios, los propietarios recuperarán el costo del aislamiento adicional en pocos años, gracias al ahorro en sus facturas de energía.
La planta de Saint-Gobain Isover en Etten-Leur, Países Bajos, se dedica al negocio de la eficiencia energética desde 1962. Cada año, la planta fabrica unas 45 000 toneladas de lana de vidrio aislante, ya sea como mantas para el aislamiento de techos o en forma de fibras sueltas que se inyectan en las cámaras de aire de las paredes o en el espacio bajo las cubiertas inclinadas.
La planta de Etten-Leur cuenta con tres líneas de producción de lana de vidrio y una línea de producción adicional que fabrica la fibra de vidrio que se utiliza como revestimiento en algunos de sus productos. Bas Beishuizen es uno de los ingenieros de mantenimiento de la planta. Concretamente, es responsable de asegurar el funcionamiento confiable y eficiente de las máquinas que conforman esas líneas.
La producción de lana de vidrio es una actividad caracterizada por velocidades altas, volúmenes grandes y un elevado consumo energético. “En toda la planta, existen 57 activos críticos”, explica Beishuizen. “Mayormente se trata de bombas y ventiladores, pero algunas de estas máquinas pueden tener unas dimensiones considerables. Por ejemplo, nuestros ventiladores más grandes funcionan con motores de 500 kW”.
Si el mundo quiere cumplir sus objetivos de reducción de gases de efecto invernadero, debe acelerar la transición hacia edificios menos contaminantes y más eficientes, invirtiendo en tecnologías nuevas, como paneles solares en los tejados y bombas de calor conectadas a fuentes de electricidad renovables. Uno de los recursos más efectivos, y también uno de los más sencillos, para reducir la huella de carbono de un edificio es el aislamiento térmico.
Con un buen aislamiento térmico, los edificios ya no pierden un calor valioso a través de las paredes y el tejado. Es sencillo, está probado y, además, es rentable. En la mayoría de los edificios, los propietarios recuperarán el costo del aislamiento adicional en pocos años, gracias al ahorro en sus facturas de energía.
La planta de Saint-Gobain Isover en Etten-Leur, Países Bajos, se dedica al negocio de la eficiencia energética desde 1962. Cada año, la planta fabrica unas 45 000 toneladas de lana de vidrio aislante, ya sea como mantas para el aislamiento de techos o en forma de fibras sueltas que se inyectan en las cámaras de aire de las paredes o en el espacio bajo las cubiertas inclinadas.
La planta de Etten-Leur cuenta con tres líneas de producción de lana de vidrio y una línea de producción adicional que fabrica la fibra de vidrio que se utiliza como revestimiento en algunos de sus productos. Bas Beishuizen es uno de los ingenieros de mantenimiento de la planta. Concretamente, es responsable de asegurar el funcionamiento confiable y eficiente de las máquinas que conforman esas líneas.
La producción de lana de vidrio es una actividad caracterizada por velocidades altas, volúmenes grandes y un elevado consumo energético. “En toda la planta, existen 57 activos críticos”, explica Beishuizen. “Mayormente se trata de bombas y ventiladores, pero algunas de estas máquinas pueden tener unas dimensiones considerables. Por ejemplo, nuestros ventiladores más grandes funcionan con motores de 500 kW”.
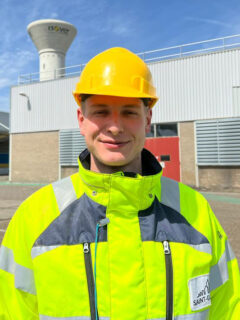
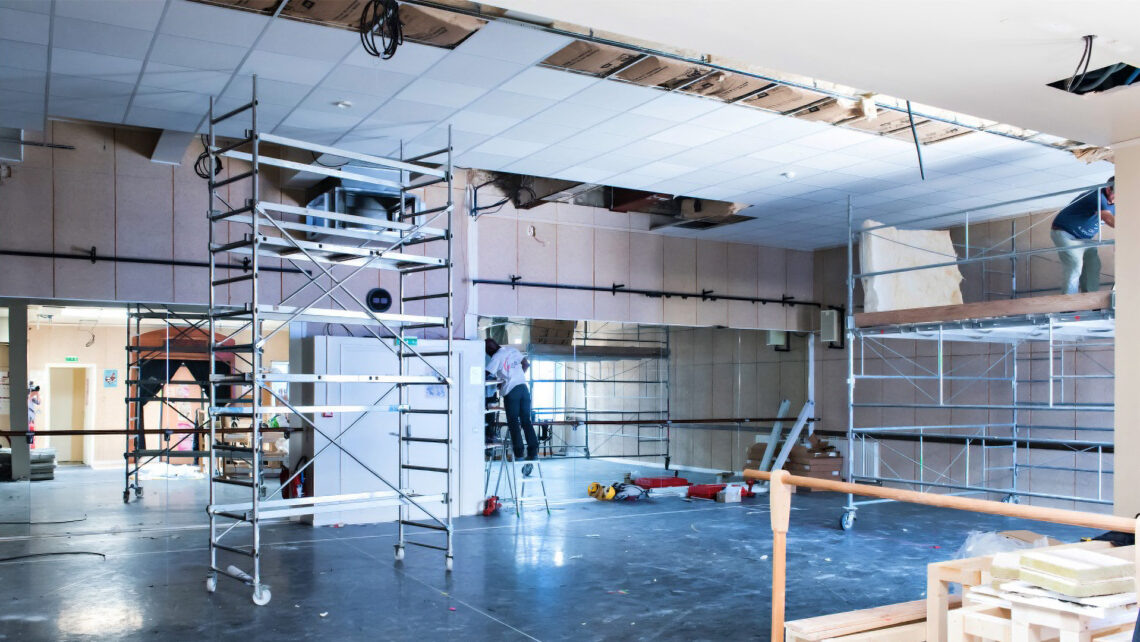
Prevenir lo inesperado
Si falla un activo crítico, podría obligar a parar toda la línea, con la posibilidad de tener que desechar el lote entero de material. Siempre que puede, el equipo de mantenimiento de Etten-Leur intenta aplicar enfoques preventivos basados en la condición. “Para mejorar nuestro mantenimiento de los rodamientos, utilizamos los sensores de vibración portátiles QuickCollect de SKF. Calculamos la frecuencia de las mediciones de vibración en función de la importancia y criticidad del componente. Una vez que el técnico realiza las mediciones, los rodamientos se someten a un análisis en colaboración con SKF. De este modo, podemos utilizar los datos para detectar indicios de potenciales problemas”.
Con la ayuda de los expertos de SKF en monitoreo de condición, el sensor portátil no tardó en producir información útil
Bas Beishuizen, ingeniero de mantenimiento de Saint-Gobain Isover
Con la ayuda de los expertos de SKF en monitoreo de condición, el sensor portátil no tardó en producir información útil. Por ejemplo, el análisis de los espectros de vibración mostró que la lubricación de algunos rodamientos era deficiente. “Cuando estudiamos el problema más a fondo, descubrimos que los puntos de lubricación de algunas máquinas no estaban en el lugar correcto y la grasa no llegaba correctamente al rodamiento”, explica Beishuizen. “Una vez identificada la causa raíz, fue fácil corregir el problema”.
La medición de la vibración no solo revela problemas en los rodamientos. También puede detectar problemas en otras partes del equipo. “Un problema que se da con bastante frecuencia en Saint-Gobain Isover es un desequilibrio en los ventiladores”, prosigue. “La contaminación puede acumularse en las aspas del ventilador, y eso, a su vez, reduce la eficiencia y puede provocar fallas.
Las mediciones de la vibración permiten a los técnicos de mantenimiento trabajar con el personal de operaciones para organizar una parada programada para limpiar y equilibrar los ventiladores contaminados. Así, podemos reducir las paradas no programadas de las máquinas provocadas por fallas de los rodamientos o de los soportes del motor derivadas de vibraciones intensas”.
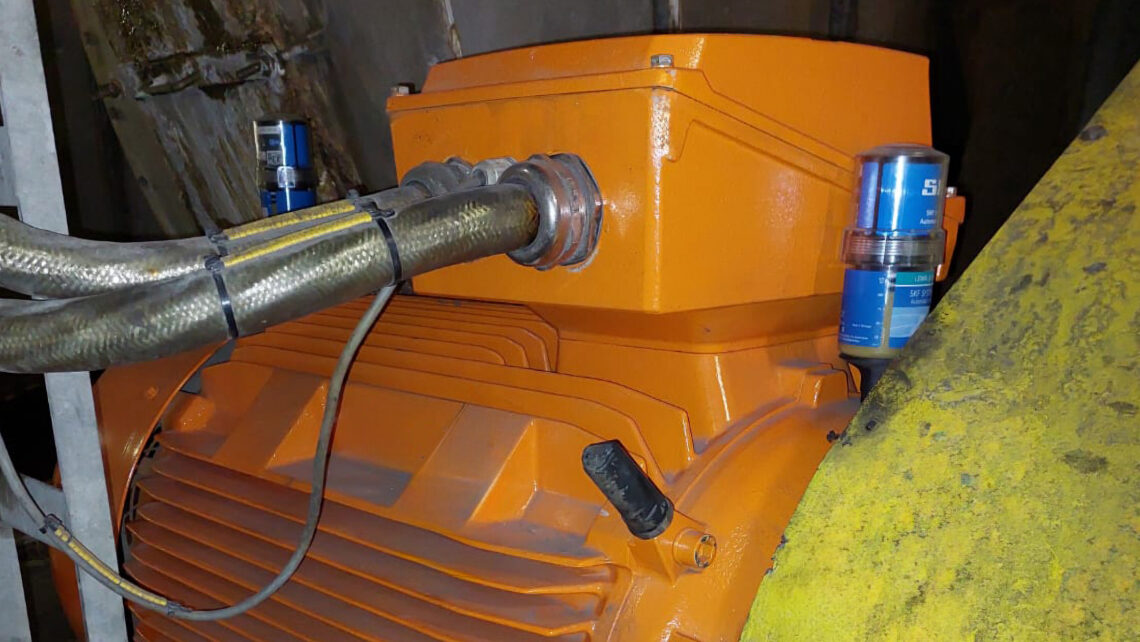
Trabajar en línea
Animado por el éxito de las mediciones de la vibración, Beishuizen quiso llevar el enfoque al próximo nivel. “Las mediciones manuales aportan datos realmente útiles, pero solo se hacen unas cuantas veces al año”, afirma. “El equipo de mantenimiento pide más datos y, para ello, las mediciones deben realizarse más a menudo para acumular datos confiables”.
El siguiente paso fue implementar la tecnología de monitoreo en línea, instalando sensores IMx-1 fijos de SKF en máquinas críticas de toda la planta. Estos dispositivos compactos, alimentados con batería, registran continuamente los datos de vibración y temperatura, y los transmiten a través de una red de malla inalámbrica de radio a una puerta de enlace, que los envía, a su vez, a la nube de SKF mediante una conexión móvil 4G. “En Saint-Gobain, ya contamos con una plataforma propia para el software de gestión del mantenimiento. Sin embargo, gracias a la conexión API entre SKF y Saint-Gobain, podemos extraer todos los datos de vibración y combinarlos con los demás datos que tenemos”, afirma Beishuizen. “De este modo, reunimos todos los datos en un solo punto”.
El monitoreo continuo de la vibración ofrece múltiples beneficios a la planta. Por ejemplo, si se produce un aumento repentino e inesperado de la vibración, el sistema puede alertar al personal de mantenimiento u operaciones para que inicie una investigación. Mientras tanto, el hecho de grabar los datos a lo largo del tiempo ayudará al equipo a identificar tendencias de evolución más lenta que pueden indicar un deterioro del rendimiento de una máquina.
“El equipo de mantenimiento está desarrollando un tablero de comando de monitoreo de condición cuyo objetivo es implementar el mantenimiento basado en la condición en la planta de Isover”, dice Beishuizen. “Este tablero nos da una visión de conjunto de todos nuestros activos críticos y prioriza las máquinas que necesitan atención.
“Paramos cada línea varias veces al año para realizar un mantenimiento programado”, continúa. “Nos gustaría poder determinar a partir de los datos exactamente qué acciones corresponde hacer durante cada parada”. Mejoraría el mantenimiento y acortaría las paradas, ya que los análisis permitirían tener las inspecciones hechas antes de iniciar las paradas.
Pero es solo el próximo paso, dice Beishuizen. El equipo de mantenimiento aspira a sacar mucho más provecho de la digitalización del mantenimiento de la planta. “Combinando los datos de condición con los de operaciones y mantenimiento, podremos empezar a hacernos una idea más completa del rendimiento de nuestros activos y de cómo y cuándo fallan”, explica. “Y eso nos permitirá centrar nuestros esfuerzos en proyectos que mejoren la confiabilidad y la eficiencia de todas nuestras operaciones”.
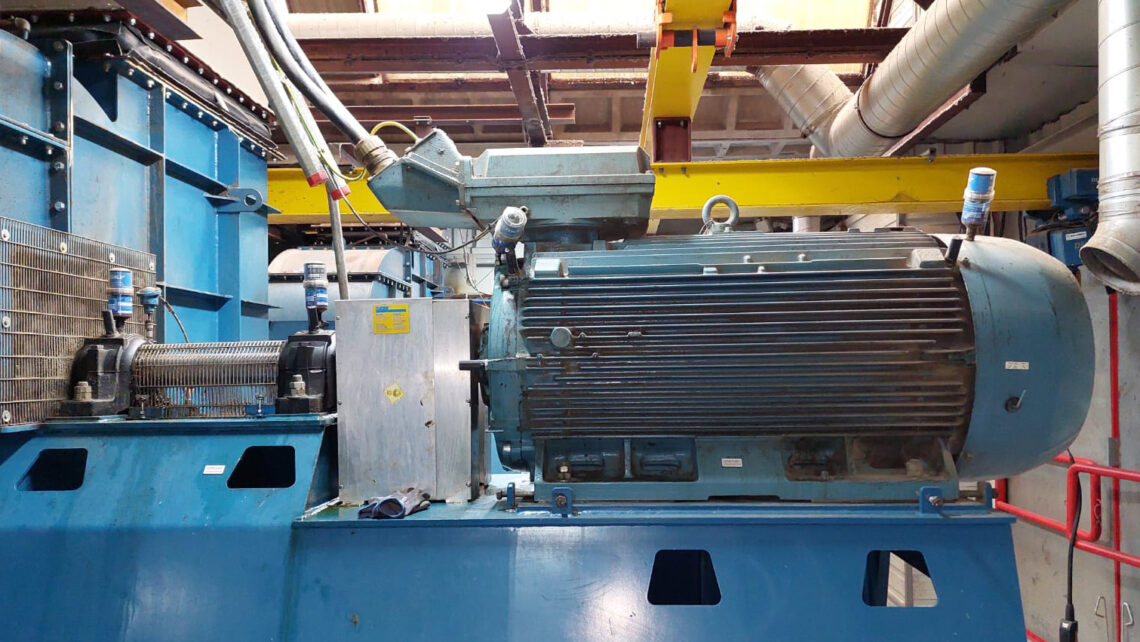
Cómo se hace
La producción de lana de vidrio funciona de forma parecida a las máquinas de feria que convierten el azúcar derretido en una golosina esponjosa, pero sus procesos generan mucho más calor y su escala es mucho mayor.
Primero se mezclan los lotes de material y, después, se calientan en un horno hasta unos 1400 ºC. Tradicionalmente, los únicos materiales utilizados eran los ingredientes básicos del vidrio: arena, carbonato sódico y piedra caliza. Hoy en día, sin embargo, alrededor de la mitad de la mezcla utilizada en los hornos de Isover es vidrio reciclado. De este modo, el consumo de material virgen es menor y se ahorra energía en la producción, ya que el vidrio se funde a menor temperatura que la arena.
A continuación, el vidrio líquido se bombea a través de una centrifugadora, que lo estira formando finas fibras parecidas al cabello. Para producir las mantas de lana de vidrio, las fibras se rocían con un aglutinante y se les da la forma de lámina. A continuación, pasan por un horno de curado, donde se comprimen hasta alcanzar su grosor final. El aglutinante curado mantiene unidas las fibras en los puntos de contacto y crea un material duradero que puede comprimirse hasta una décima parte de su volumen para el transporte. Recupera su tamaño original cuando se desembala. Según la aplicación final, se puede encolar a las mantas un revestimiento de fibra de vidrio para mejorar su durabilidad y facilidad de manejo.
Lubricación con la dosis justa
Tras ver el impacto de las fallas de lubricación en activos críticos, la planta de Etten-Leur ha implementado otra tecnología de SKF en muchas de sus máquinas. “Sabemos que un rodamiento puede necesitar 50 gramos de grasa para funcionar durante seis meses”, aclara Bas Beishuizen, ingeniero de mantenimiento de Saint-Gobain Isover. “Pero no se conseguirá un rendimiento óptimo si se suministra todo ese lubricante de golpe; tampoco se puede saber siempre con certeza si el rodamiento está realmente lubricado”.
Por ello, la planta ha instalado lubricadores TLDD conectados de un solo punto, de SKF. Estos dispositivos suministran dosis pequeñas y uniformes de lubricante a cada rodamiento desde un depósito interno a una velocidad predeterminada. Comunican su estado a la nube de SKF a través de una red inalámbrica y una puerta de enlace a la red móvil 4G. De este modo, el personal de mantenimiento sabe que los rodamientos han sido lubricados, cuándo es necesario recargar cada unidad y si el flujo de lubricante se ha interrumpido debido a algún problema.