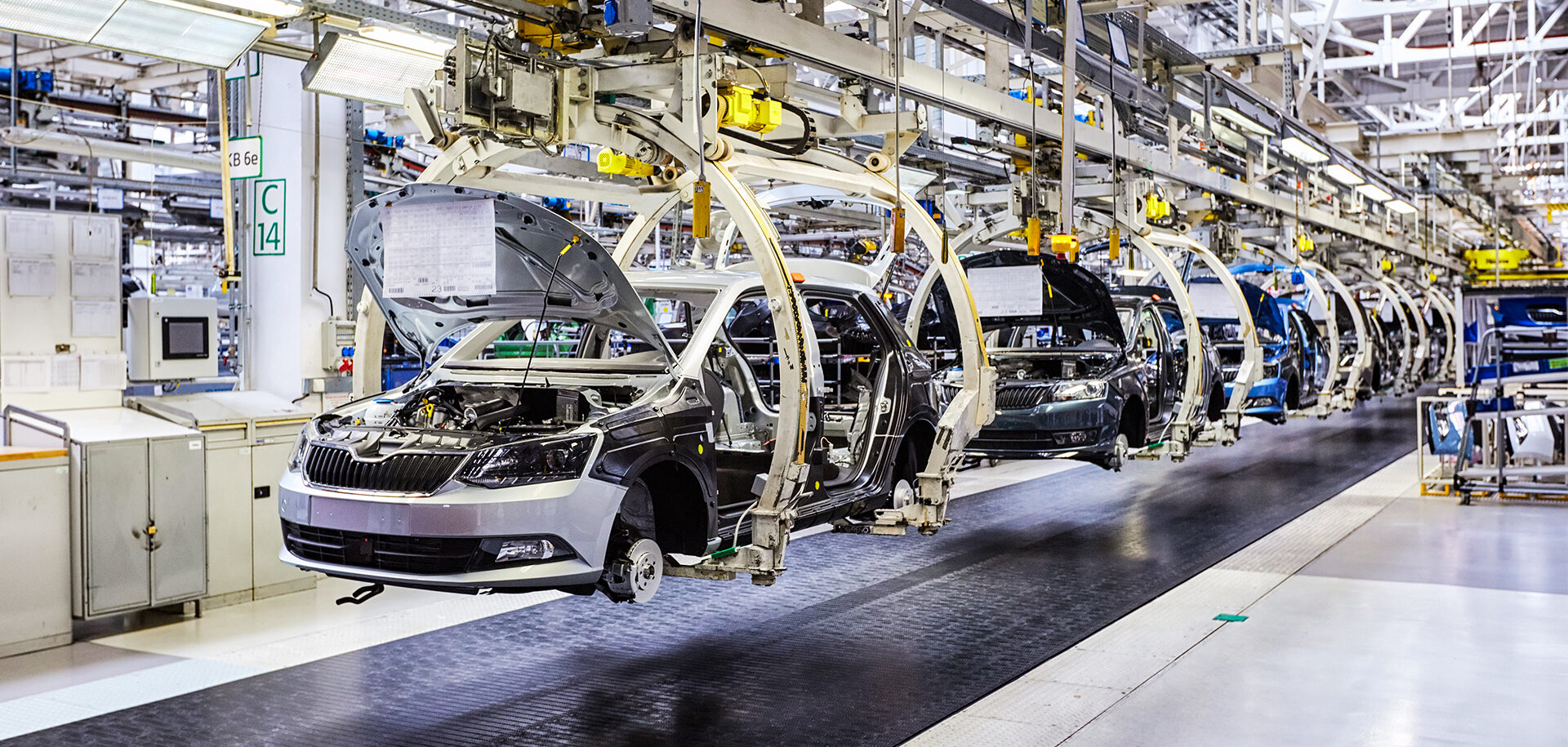
I cuscinetti giusti mettono fine ai fermi macchina nell’industria automobilistica
Grazie a una soluzione personalizzata di cuscinetti orientabili a rulli SKF, un costruttore di veicoli tedesco ha aumentato da tre a oltre trentasei mesi la durata di esercizio.
Il cambiamento tecnologico nel settore manifatturiero accelera e, con il progredire dei macchinari, aumenta la produzione. Nell’evoluzione delle fabbriche, tuttavia, spesso si trascurano particolari importanti, specie quando si tratta di cuscinetti.
Pensiamo, per esempio, al settore automobilistico. Negli anni ‘80, le automobili pesavano di norma intorno ai 1.000 kg, mentre oggi non è raro trovare vetture che pesano il doppio. Ottimizzare le tecniche di produzione comporta un consistente aumento del numero di vetture prodotte in tempi nettamente inferiori.
I trasportatori deboli spesso rappresentano un problema
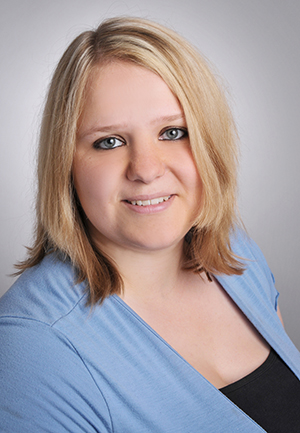
Questa evoluzione del mercato causa un aumento delle pressioni sulle strutture esistenti, in particolare sui nastri trasportatori e i loro cuscinetti, che costituiscono l’anello debole del sistema. Sempre più spesso, infatti, gli ingegneri SKF che si recano nelle fabbriche dove si sperimentano fermi macchina constatano che le cause sono perlopiù imputabili all’incapacità dei trasportatori di sopportare carichi maggiori o ritmi di produzione più elevati. Corinna Ulherr, Application Engineer, industrial sales di SKF, sostiene che il problema è spesso riconducibile ai cuscinetti che non sono stati aggiornati per essere in linea con i nuovi requisiti del processo produttivo o che sono stati scelti in modo errato sin dall’inizio.
“Nella maggior parte dei casi, i costruttori vogliono incrementare la capacità di una linea esistente o il peso delle vetture prodotte, ma l’ultima cosa a cui pensano sono i cuscinetti dei nastri trasportatori”, commenta. “Spesso sono proprio loro il problema, perché non sono in grado di reggere i nuovi ritmi o le condizioni di carico”.
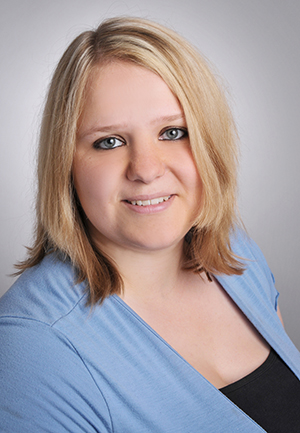
I trasportatori deboli spesso rappresentano un problema
Questa evoluzione del mercato causa un aumento delle pressioni sulle strutture esistenti, in particolare sui nastri trasportatori e i loro cuscinetti, che costituiscono l’anello debole del sistema. Sempre più spesso, infatti, gli ingegneri SKF che si recano nelle fabbriche dove si sperimentano fermi macchina constatano che le cause sono perlopiù imputabili all’incapacità dei trasportatori di sopportare carichi maggiori o ritmi di produzione più elevati. Corinna Ulherr, Application Engineer, industrial sales di SKF, sostiene che il problema è spesso riconducibile ai cuscinetti che non sono stati aggiornati per essere in linea con i nuovi requisiti del processo produttivo o che sono stati scelti in modo errato sin dall’inizio.
“Nella maggior parte dei casi, i costruttori vogliono incrementare la capacità di una linea esistente o il peso delle vetture prodotte, ma l’ultima cosa a cui pensano sono i cuscinetti dei nastri trasportatori”, commenta. “Spesso sono proprio loro il problema, perché non sono in grado di reggere i nuovi ritmi o le condizioni di carico”.
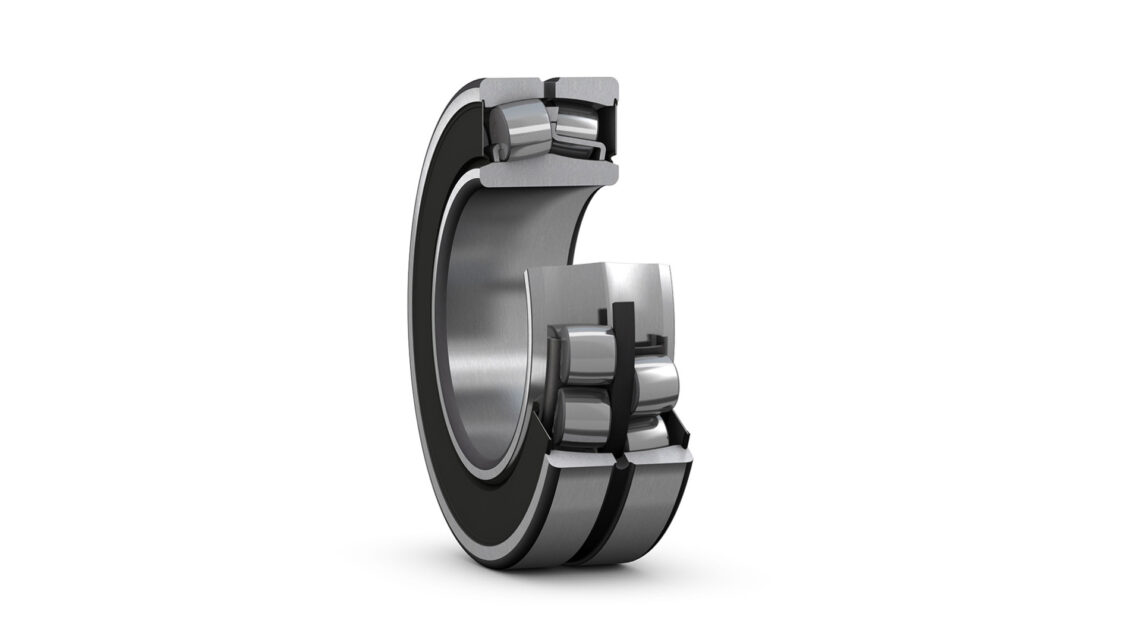
L’uso improprio dei unità cuscinetti a sfere è un errore comune
L’uso improprio delle unità cuscinetto a sfere è frequente in molti settori, in particolare in quelli dove si utilizzano nastri trasportatori multipli in condizioni operative gravose.
Nel 2018 Ulherr si era recata presso un costruttore di automobili in Germania che si trovava ad affrontare cedimenti dei cuscinetti ogni tre, massimo sei mesi.
Spesso sono proprio loro il problema, perché non sono in grado di reggere i nuovi ritmi o le condizioni di carico
Corinna Ulherr, Application Engineer, industrial sales di SKF.
L’attrezzatura interessata faceva parte di un sistema largo cinque metri, adibito al trasporto del personale al lavoro sulle vetture. La larghezza del nastro faceva sì che un aumento di temperatura di pochi gradi portasse a un allungamento degli alberi. Essendo sempre cuscinetti di vincolo assiale, le unità a sfere non sono in grado di compensare la dilatazione dell’albero.
Questa condizione, unita a un lieve disallineamento del nastro, generava forze assiali che aumentavano ulteriormente il carico sui cuscinetti. Le forze radiali indotte dal pesante tamburo e dal pretensionamento del nastro, inoltre, erano superiori a quelle per le quali erano stati progettati i cuscinetti. Le cose erano rese peggiori dalla lubrificazione insufficiente, che ne provocava il cedimento.
“Essendo facili e veloci da montare, le unità cuscinetto a sfere trovano largo impiego, ma non bisogna dimenticare che si tratta di cuscinetti di vincolo assiale”, precisa Ulherr. “Trascurare questo particolare può rivelarsi costoso, perché in caso di cedimento non si possono sostituire senza fermare la produzione”.
Questo è quanto è successo al costruttore tedesco. Si è reso infatti necessario fermare la produzione per sostituire i cuscinetti; l’arresto temporaneo del nastro trasportatore ha obbligato gli addetti a camminare accanto alle vetture per continuare il loro lavoro. Il tutto ha causato un calo di produzione pari al 10 percento.
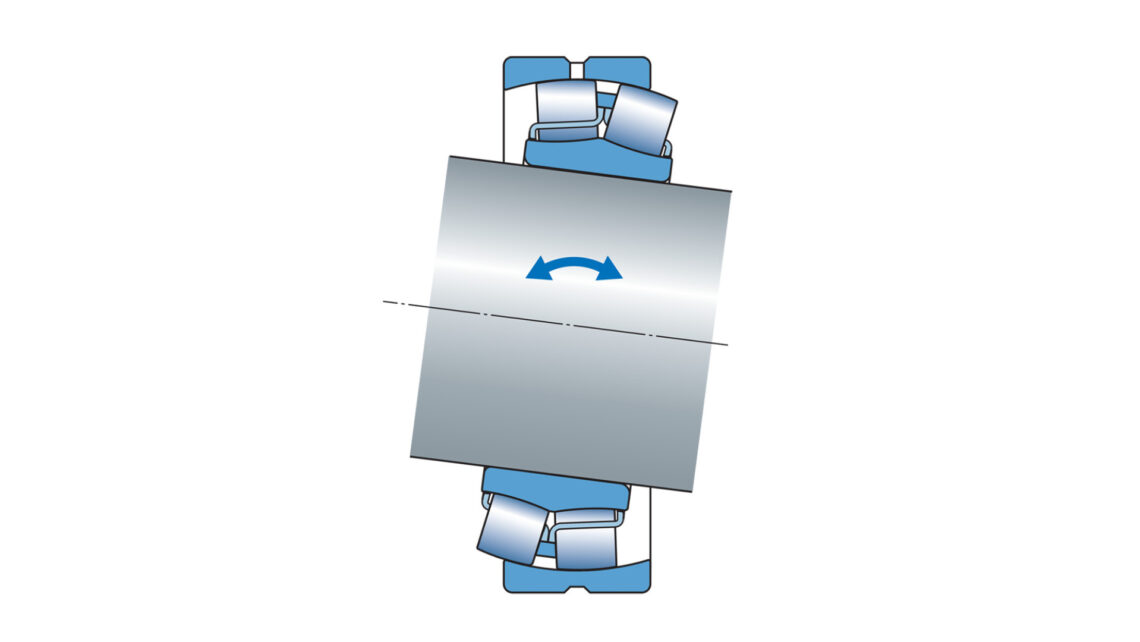
Soluzione con maggiore capacità di carico
La soluzione di Ulherr ha previsto l’installazione di cuscinetti orientabili a rulli SKF schermati all’interno di alloggiamenti progettati appositamente. “I cuscinetti a rulli hanno una capacità di carico molto più elevata rispetto alle unità a sfere. E hanno un vantaggio in più: possono sopportare anche il disallineamento dell’albero, che è frequente in queste applicazioni”. Il cuscinetto che costituisce il lato libero può muoversi in senso assiale nella sede dell’alloggiamento e quindi può facilmente sopportare la dilatazione dell’albero. Mentre il cuscinetto di vincolo assiale sopporta i carichi assiali”.
Anche la corretta lubrificazione ha svolto un ruolo essenziale. I nastri trasportatori, che operano a basse velocità, richiedono un grasso con olio ad alta viscosità. La scelta di impiegare l’SKF LGEV2, un grasso ad alta viscosità a base di olio minerale, contenente bisolfuro di molibdeno e grafite, si è rivelata ottimale per la lubrificazione dei cuscinetti soggetti a rotazioni lente, come nel caso dei trasportatori su cui lavorano gli addetti al montaggio delle auto. Il grasso con particelle minerali, quali la grafite, è particolarmente importante per le applicazioni che richiedono arresti e riavvii regolari della produzione o che sono soggette a rotazione in diverse direzioni.
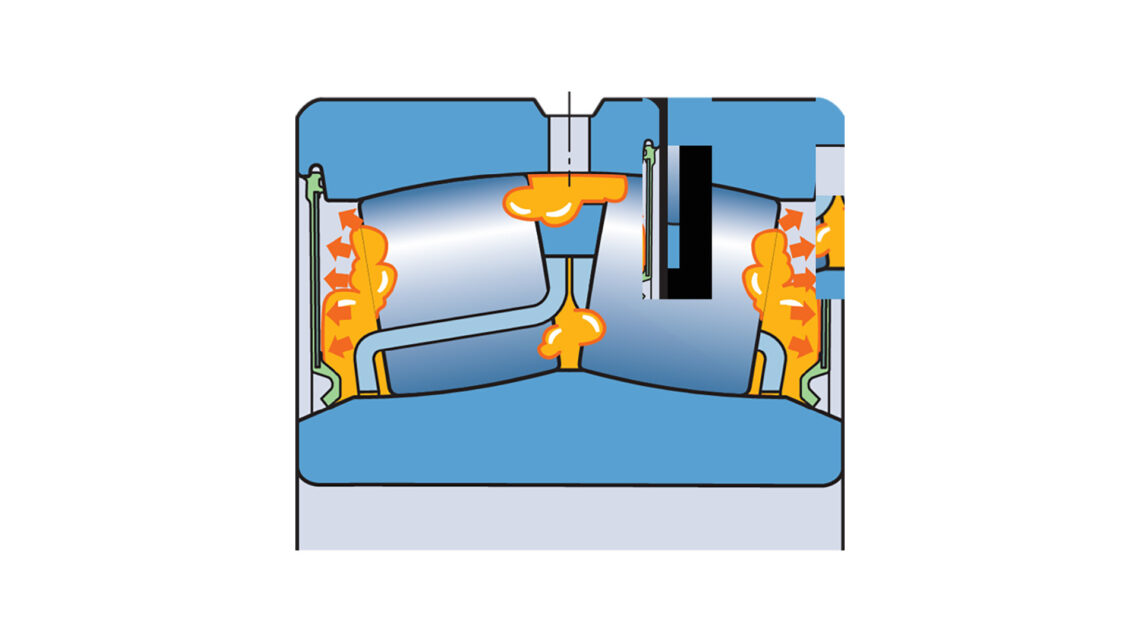
Notevole aumento della durata di esercizio
Le misure intraprese, complessivamente, hanno aumentato la durata di esercizio da tre a più di trentasei mesi, oltre ad aver ridotto notevolmente il rischio di cedimenti.
“Anche se questa era una situazione specifica, vedo molti casi come questo”, dichiara Ulherr. “Spesso riscontriamo problemi con unità cuscinetto a sfere semplicemente perché i clienti non sono consapevoli del fatto che questi non possono sopportare carichi pesanti o che sono esclusivamente di vincolo assiale”.
Il messaggio di Ulherr agli operatori è chiaro: nel riprogettare un macchinario o nell’adattarlo a nuovi carichi o velocità, è necessario ripensare alla scelta dei cuscinetti. Anche se il cliente tedesco ha optato per un sistema personalizzato, Ulherr ritiene che scegliere come prima opzione componenti standard renda più facile per il cliente sostituirli in caso di necessità. Quando questo non è possibile, operare scelte corrette durante le fasi di progettazione o riprogettazione permette di evitare fermi macchina nel lungo periodo.
“Il mio obiettivo consiste soprattutto nel far sì che il cliente sia consapevole che quando allestisce una nuova linea o una nuova macchina, deve pensare ai cuscinetti più idonei allo scopo, anziché a riutilizzare quelli che andavano bene prima”, dice Ulherr. “Tutte le soluzioni sono personalizzabili, ma è sempre meglio che i clienti tengano conto fin dall’inizio delle esigenze di tutti i cuscinetti impiegati”.
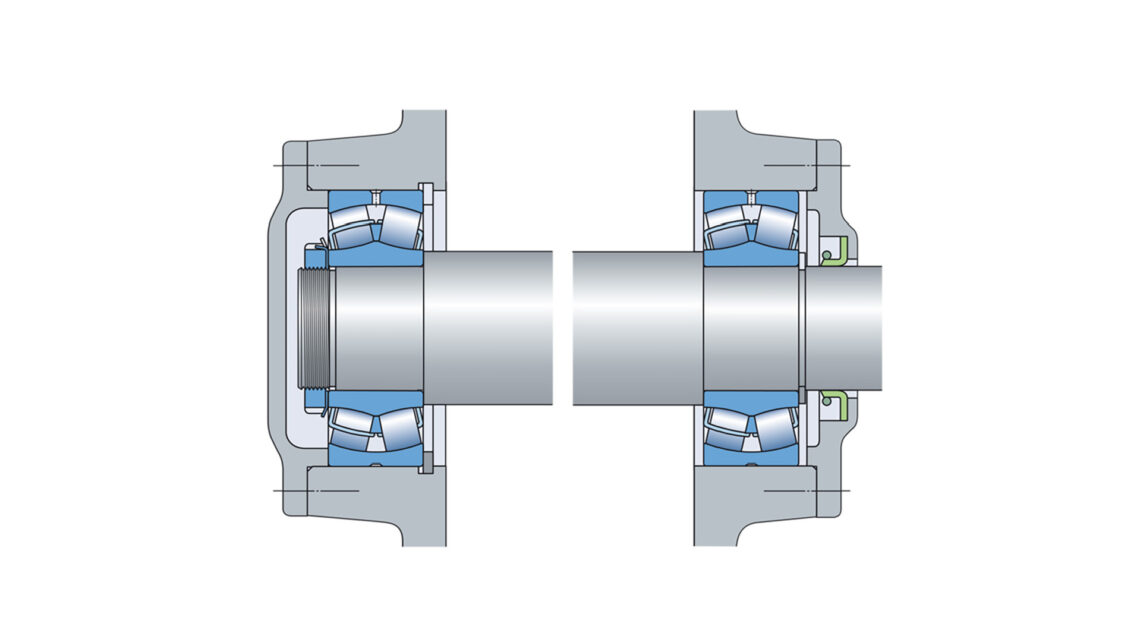
Durata di base dei cuscinetti SKF
Se si desidera evitare cedimenti prematuri dei cuscinetti per fatica, si può ricorrere a un approccio statistico per determinare le loro dimensioni. La durata teorica di base L10 è la durata a fatica che si prevede possa essere raggiunta o superata dal 90% di un gruppo sufficientemente grande di cuscinetti identici, che operano nelle stesse condizioni.
La durata teorica di base L10 è uno strumento di comprovata efficacia, che può essere usato per determinare una dimensione cuscinetto adeguata a evitare i cedimenti da fatica, confrontando la durata di base calcolata con le aspettative per la durata di esercizio del cuscinetto sull’applicazione. Ci si può basare sulle esperienze precedenti, se disponibili, o utilizzare le linee guida sul sito SKF.