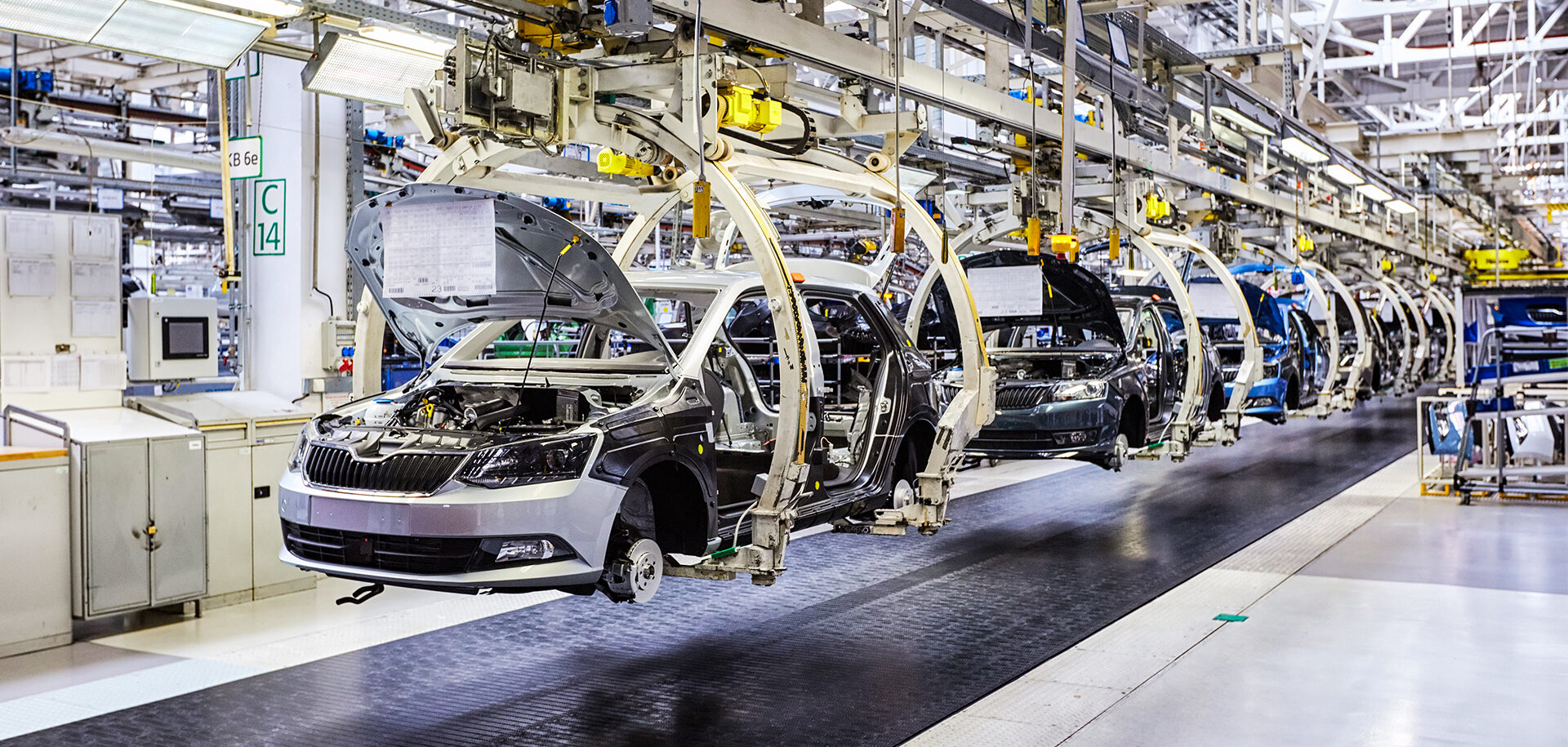
Keine Stillstände bei der Automobilfertigung mit dem richtigen Lager
Eine von SKF maßgeschneiderte Lösung mit Pendelrollenlagern verlängerte die Lagergebrauchsdauer des Montagebands bei einem deutschen Automobilhersteller von drei auf über 36 Monate.
Der Technologiewandel in der Fertigung macht Maschinen und Anlagen immer komplexer, die Produktionsleistung nimmt stetig zu. Allerdings werden Kleinigkeiten bei Weiterentwicklung und Ausbau von Fabriken oft übersehen, das gilt besonders für Lager.
Zum Beispiel in der Automobilindustrie: In den 1980er-Jahren wog ein Pkw im Schnitt knapp über 1.000 Kilogramm. Heute sind Fahrzeuge nicht selten doppelt so schwer. Dank fertigungstechnischer Fortschritte können Fabriken inzwischen mehr Fahrzeuge als je zuvor in wesentlich kürzerer Zeit produzieren.
Zu schwache Förderbänder sind oft ein Problem
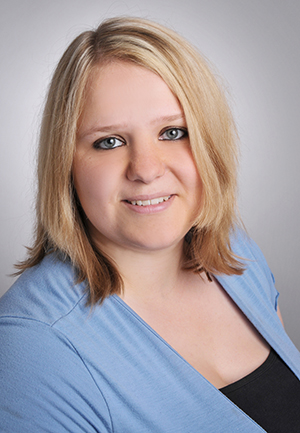
Durch diese Entwicklungen wird jedoch die vorhandene betriebliche Ausstattung stärker beansprucht, vor allem die Förderbänder und deren Lagerungen. Die Ingenieure von SKF besuchen immer häufiger Fabriken, die über Stillstände klagen, weil ihre Förderbänder die größeren Lasten oder die gestiegene Produktionsleistung nicht mehr bewältigen. Die Fehlerquelle sind meist ungeeignete Lager, die nicht an die produktionstechnischen Veränderungen angepasst oder von vornherein falsch ausgewählt sind, erklärt Corinna Ulherr, Anwendungsingenieurin im Industrievertrieb bei SKF.
„In der Regel lässt ein Hersteller, der an einer vorhandenen Produktionslinie die Leistung steigern oder schwerere Autos montieren will, die Lager in den Förderbändern außer Acht“, sagt Ulherr „Oft sind Spannlager das Problem, weil sie für die neue Produktionsleistung oder Belastungssituation nicht ausgelegt sind.“
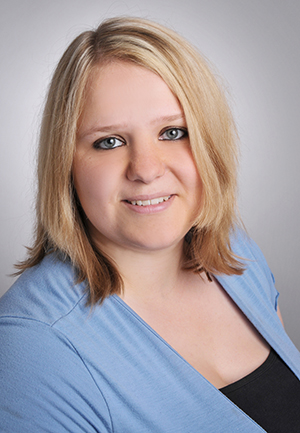
Zu schwache Förderbänder sind oft ein Problem
Durch diese Entwicklungen wird jedoch die vorhandene betriebliche Ausstattung stärker beansprucht, vor allem die Förderbänder und deren Lagerungen. Die Ingenieure von SKF besuchen immer häufiger Fabriken, die über Stillstände klagen, weil ihre Förderbänder die größeren Lasten oder die gestiegene Produktionsleistung nicht mehr bewältigen. Die Fehlerquelle sind meist ungeeignete Lager, die nicht an die produktionstechnischen Veränderungen angepasst oder von vornherein falsch ausgewählt sind, erklärt Corinna Ulherr, Anwendungsingenieurin im Industrievertrieb bei SKF.
„In der Regel lässt ein Hersteller, der an einer vorhandenen Produktionslinie die Leistung steigern oder schwerere Autos montieren will, die Lager in den Förderbändern außer Acht“, sagt Ulherr „Oft sind Spannlager das Problem, weil sie für die neue Produktionsleistung oder Belastungssituation nicht ausgelegt sind.“
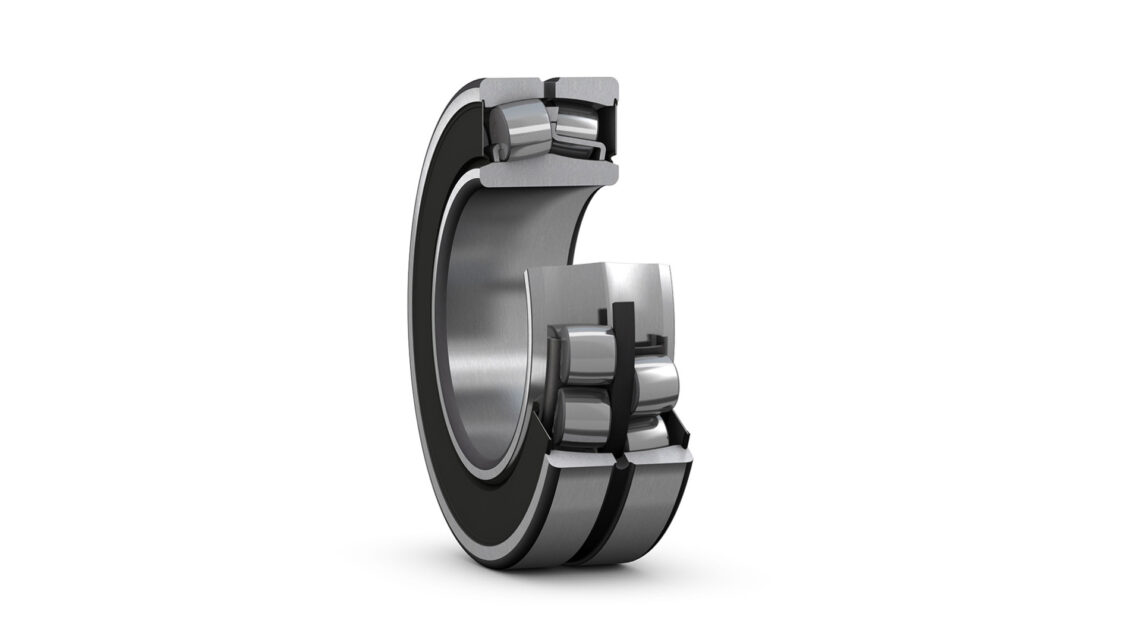
Falsche Anwendung von Spannlagern
Fehlanwendungen von Spannlagern findet man in zahlreichen Sektoren, besonders dort, wo mehrere Förderanlagen unter anspruchsvollen Bedingungen im Einsatz sind. Ulherr besuchte 2018 einen Automobilhersteller in Deutschland, bei dem alle drei bis sechs Monate Lagerausfälle auftraten.
Oft sind Spannlager das Problem, weil sie für die neue Produktionsleistung oder Belastungssituation nicht ausgelegt sind.
Corinna Ulherr, Anwendungsingenieurin Industrievertrieb bei SKF.
Die betroffene Anlage war Teil eines fünf Meter breiten Montagebandes, das die Monteure beförderte, die an den Fahrzeugen arbeiteten. Aufgrund der Breite des Förderbandes bewirkte ein Temperaturanstieg von wenigen Graden eine thermische Längenänderung der Wellen. Spannlager sind immer Festlager und können sich deshalb an Längenänderungen nicht anpassen.
Diese Längenänderung in Kombination mit einer leichten Schiefstellung des Bandes verursachte Axialkräfte, welche die Belastung der Lager noch weiter verstärkten. Zusätzlich waren die Lager auch nicht für die von der schweren Trommel und der Vorspannung des Förderbandes induzierten Radialkräfte ausgelegt. Hinzu kam, dass die Lager unzureichend geschmiert waren und dadurch ausfielen.
„Spannlager werden oft verwendet, weil sie schnell und einfach einzubauen sind. Dabei vergisst man leicht, dass sie eben nur Festlager sind“, weiß Ulherr aus Erfahrung. „Diese Fehlentscheidung kann kostspielig werden; denn in der Regel muss die Produktion unterbrochen werden, wenn diese Lager ausfallen und ausgetauscht werden müssen.“
So war es bei dem deutschen Automobilhersteller. Die Monteure, die vorübergehend kein Förderband zur Verfügung hatten, waren gezwungen, zu Fuß an den Fahrzeugen entlang zu gehen, um ihre Arbeit fortzuführen. Die Produktion sank um zehn Prozent.
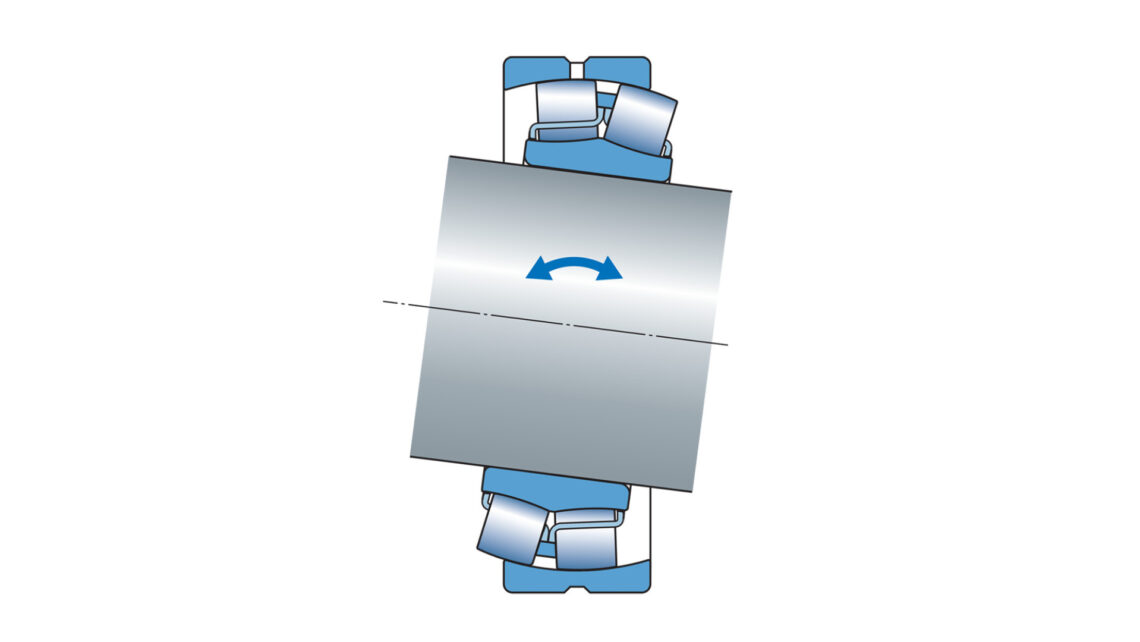
Eine Lösung mit höherer Tragfähigkeit
Ulherr schlug vor, abgedichtete SKF Pendelrollenlager in speziell konstruierte Gehäuse einzubauen. „Diese Lager haben eine wesentlich höhere Tragfähigkeit als die kleinen Spannlager“, erklärt sie. „Und sie haben einen weiteren Vorteil: Sie können sich einem Fluchtungsfehler der Welle anpassen, der in diesen Anwendungen häufig vorkommt. Ein Loslager ist im Lagersitz in axialer Richtung verschiebbar und kann deshalb die Längenveränderung der Welle problemlos aufnehmen. Das Festlager trägt die axialen Lasten.“
Die richtige Schmierung war ein weiterer entscheidender Teil von Ulherrs Lösung. Langsam laufende Förderanlagen brauchen ein Schmierfett mit hoher Ölviskosität. Die Lager mit LGEV2 von SKF zu schmieren, erwies sich als optimal für die niedrige Laufgeschwindigkeit des Bandes, bei der die Monteure ihre Montagearbeiten an den Fahrzeugen ausführten. LGEV2 ist ein hochviskoses Fett auf Mineralölbasis, das Molybdändisulfid und Graphit enthält. Schmierfett mit mineralischen Partikeln wie Graphit ist besonders wichtig für Anwendungen, bei denen die Produktion regelmäßig anhält und wieder anläuft oder sich in verschiedene Richtung bewegt.
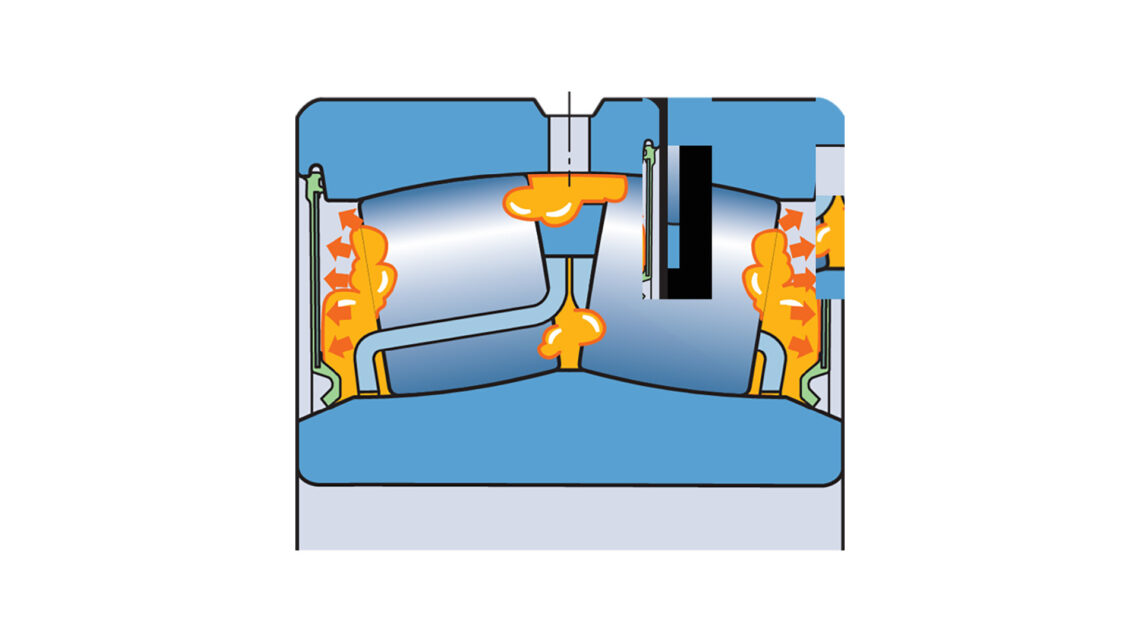
Erheblich längere Gebrauchsdauer
Ulherrs Veränderungen verlängerten die Gebrauchsdauer der Lager insgesamt von drei auf über 36 Monate und reduzierten das Ausfallrisiko deutlich.
„Das war zwar eine besondere Situation, aber ich habe viele ähnliche Fälle“, meint Ulherr. „Wir stoßen immer wieder auf Probleme mit Spannlagern, weil die Kunden nicht wissen, dass diese Lager keine hohe Last bewältigen können oder dass es sich nur um Festlager handelt.“
Ulherrs Rat ist eindeutig: Bei jeder Neukonzeptionierung der Produktionsanlagen oder Veränderungen von Belastung und Geschwindigkeit muss die Lagerwahl überprüft werden. Der deutsche Fahrzeughersteller entschied sich für eine maßgeschneiderte Lösung. Aber in den meisten Fällen versucht Ulherr, Standardkomponenten zu verwenden, damit der Kunde sie bei Bedarf einfacher austauschen kann. Das ist allerdings nicht immer möglich. Deshalb ist die richtige Wahl in der Konzeptions- oder Umgestaltungsphase wichtig, um auf längere Sicht viele Ausfälle zu vermeiden.
„Mir geht es eher darum, den Kunden bewusst zu machen, dass sie bei der Konzeption einer neuen Produktionslinie oder einer neuen Anlage an die bisher eingesetzten Lager denken sollten und nicht einfach die gleichen Lager wieder verwenden, nur weil die vorher funktioniert haben“, fügt Ulherr hinzu. „Wir können immer kundenspezifische Lösungen entwickeln, aber für die Kunden ist es auf jeden Fall besser, alle für die Anwendung vorgesehenen Lager von Anfang an überdenken.“
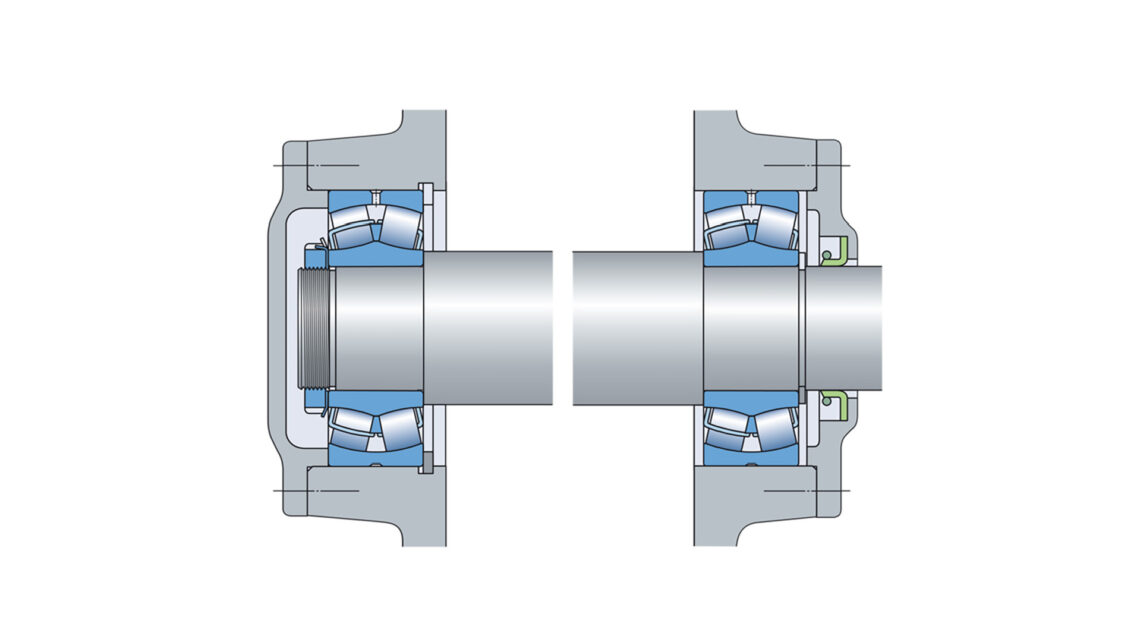
Nominelle Lagerlebensdauer
Wenn Sie den ermüdungsbedingten Ausfall eines Lagers vor Ablauf der geplanten Anwendungsgebrauchsdauer vermeiden wollen, können Sie einen statistischen Ansatz zur Bestimmung der geeigneten Lagergröße heranziehen. Die nominelle Lebensdauer L10 ist die Ermüdungslebensdauer, die 90 % einer ausreichend großen Gruppe identischer Lager bei gleichen Betriebsbedingungen voraussichtlich erreichen oder überschreiten.
Die nominelle Lebensdauer L10 ist ein bewährtes und effektives Instrument zur Bestimmung der Lagergröße, die erforderlich ist, um Ermüdungsausfälle zu vermeiden. Vergleichen Sie die berechnete nominelle Lebensdauer mit der Gebrauchsdauererwartung der Lageranwendung. Sie können Ihre Erfahrungen aus früheren Entscheidungen nutzen oder die Richtlinien auf der SKF Website verwenden.