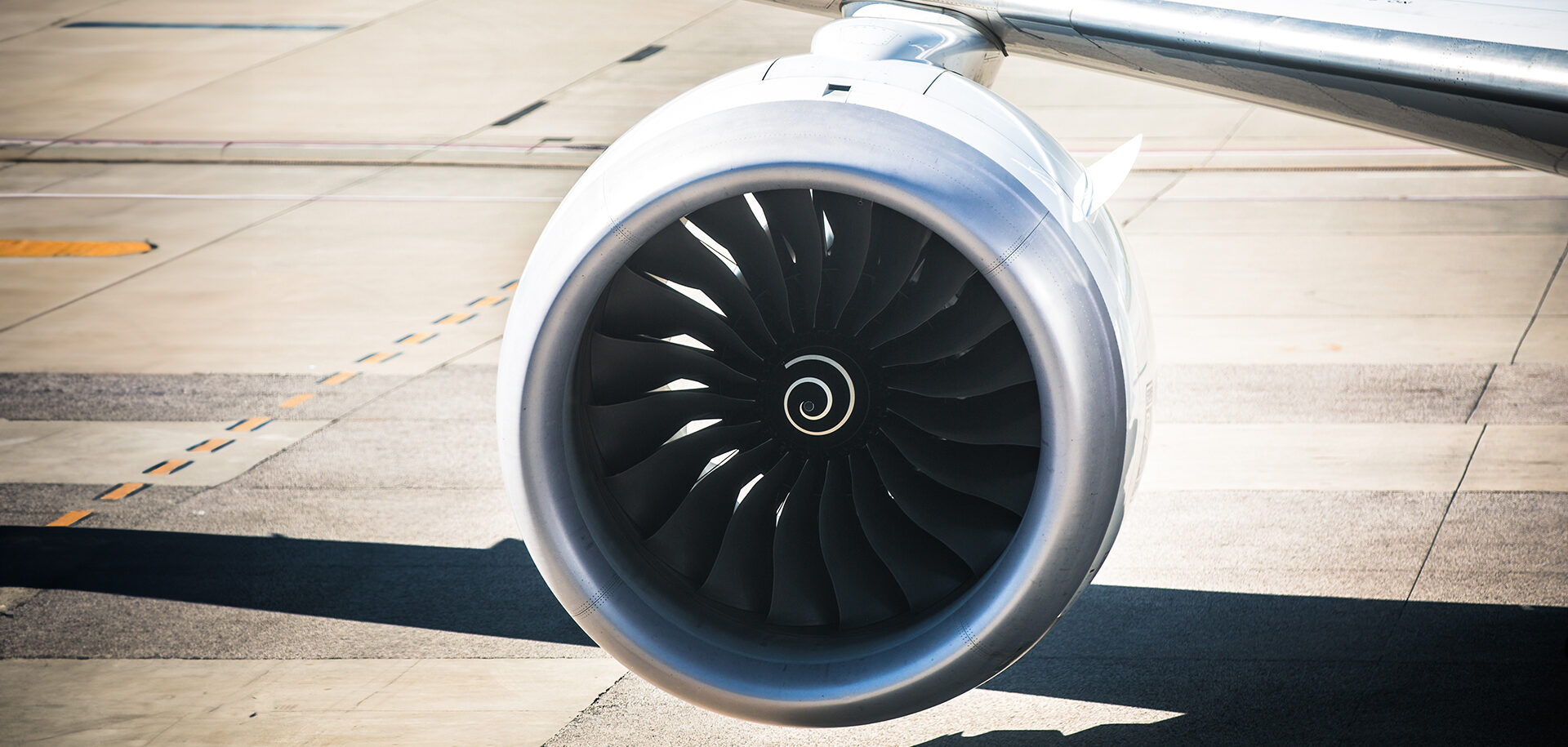
Innovazione collaborativa per gli aerei del futuro
L’SKF Aerospace Development Centre lavora a stretto contatto con i clienti per sviluppare le tecnologie per i velivoli di domani.
Per l’industria aeronautica mondiale gli ultimi anni sono stati turbolenti. Prima il crollo dei passeggeri dovuto all’emergenza sanitaria legata alla pandemia di Covid-19. Poi l’enorme effetto rimbalzo legato al ritorno alla normalità: solo nel 2022 il numero di passeggeri è aumentato del 47 percento.
L’Organizzazione internazionale dell’aviazione civile (ICAO) stima che nel 2023 il traffico aereo civile supererà i livelli pre-pandemia e i costruttori, dal canto loro, riportano un portafoglio ordini pieno e linee di produzione a pieno regime.
Certamente un’ottima notizia per il settore dell’aviazione, che tuttavia deve ancora affrontare grandi sfide nel lungo termine, non ultimo gli obiettivi di sostenibilità fissati dalle autorità di tutto il mondo. Ma a differenza di molti altri settori, le soluzioni tecniche necessarie ad azzerare le emissioni dei voli non sono ancora state individuate.
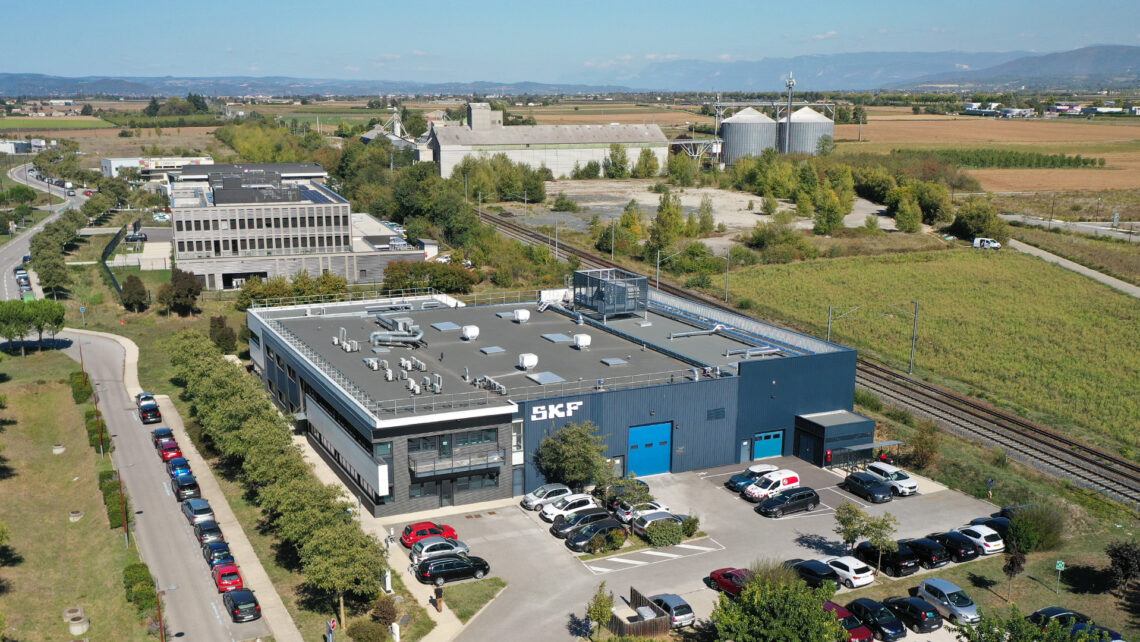
Il ruolo chiave della partnership con SKF
SKF contribuisce allo sviluppo delle tecnologie aerospaziali più avanzate attraverso il suo centro di prova Aerospace Development Centre di Valence, in Francia, che è stato recentemente potenziato.
Molti dei progetti ai quali stiamo lavorando sono destinati ad aerei che saranno costruiti a partire dal 2030
Yves Maheo, director, SKF Aerospace Development Centre
“Per la prima volta abbiamo un’unica struttura attrezzata dove collaudare tutti i componenti usati in un aereo, da quelli di tipo volvente a quelli radenti, da quelli con rotazioni a migliaia di giri al minuto a quelli stazionari”, afferma Paolo Andolfi, aerospace engineering manager di SKF.
Lo sviluppo di prodotti aerospaziali richiede tempi lunghi e intense collaborazioni. “Per sviluppare una tecnologia aerospaziale innovativa ci possono volere anche 10 anni”, dichiara Yves Maheo, director dell’Aerospace Development Centre. “Molti dei progetti ai quali stiamo lavorando ora sono destinati ad aerei che saranno costruiti a partire dal 2030”. A differenza di altri settori, i clienti finali partecipano ai progetti fin dalle prime fasi.
“Collaboriamo con i clienti a qualsiasi livello”, precisa Maheo. “Condividiamo reciprocamente le rispettive tabelle di marcia tecnologiche. I loro ingegneri vengono a Valence per collaborare con i nostri team su progetti di collaudo e sviluppo”.
Una collaborazione proficua, che assicura a SKF la conoscenza approfondita delle esigenze dei clienti e la capacità di integrarle nei diversi progetti. “Un esempio è il Textilub, un nuovo materiale tessile composito, autolubrificante, impiegato per gli attuatori aerospaziali”, commenta Maheo. “Le lunghe durate di esercizio degli aerei causano inevitabilmente l’usura dei componenti, che devono essere sostituiti. Abbiamo dedicato molto del nostro lavoro a prolungarne la durata. Ma parlando con i clienti abbiamo capito che, pur apprezzando componenti più duraturi, ciò che vogliono veramente è che questi si usurino in modo costante e prevedibile, così da facilitare le operazioni di revisione e sostituzione. Questa conoscenza è utile per sviluppare il nuovo materiale”.
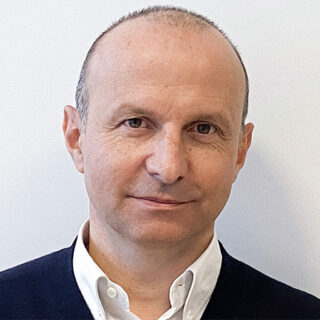
Aerospace engineering manager di SKF.
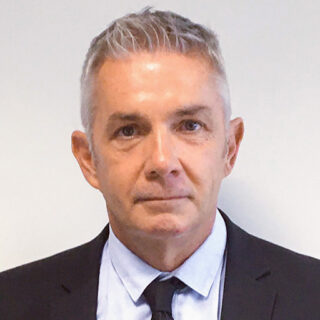
Director, SKF Aerospace Development Centre
Ibridi avanzati
Un’altra area di ricerca che suscita profondo interesse è lo sviluppo di cuscinetti per i motori a reazione di prossima generazione. Si tratta di componenti essenziali per i moderni velivoli commerciali, poiché supportano l’albero principale dei motori turbofan di grandi dimensioni, soggetto ad alte velocità di rotazione.
Questi motori sono equipaggiati con più di 10 cuscinetti lungo l’albero principale, ma i nuovi design, che prevedono l’inserimento di un ingranaggio epicicloidale tra la ventola frontale e i componenti del compressore posteriore, richiedono ulteriori cuscinetti fortemente caricati.
Le capacità dei cuscinetti incidono notevolmente sulle prestazioni del motore. Devono sopportare carichi e velocità di rotazione elevati, e devono funzionare a lungo e in modo affidabile in condizioni gravose e in presenza di temperature elevate. Nel progettare l’architettura di un nuovo motore, inoltre, gli ingegneri devono tenere conto dello spazio occupato dai cuscinetti.
L’esigenza di incrementare l’efficienza energetica nello spazio disponibile sottopone i cuscinetti a carichi sempre più elevati. Questa evoluzione sta spingendo le esecuzioni e i materiali degli attuali cuscinetti verso il loro limite fisico.
Un progetto ultimato di recente, che ha coinvolto in maniera trasversale le competenze SKF, ha portato allo sviluppo di un nuovo materiale che potrebbe segnare un deciso cambiamento nelle prestazioni dei futuri cuscinetti per motori. Finanziato da Clean Sky 2 Joint Undertaking, nell’ambito del programma di ricerca e innovazione dell’Unione Europea Horizon 2020, il progetto ARCTIC (Advanced Bearing Technologies to Increase Capabilities) ha visto Rolls-Royce come sponsor principale.
“I cuscinetti per motori aeronautici che oggi offrono le migliori prestazioni sono di tipo ibrido, ossia hanno corpi volventi in ceramica e anelli in acciaio”, sostiene Alexandre Mondelin, product development engineer di SKF, il quale aggiunge che il limite prestazionale del cuscinetto in questi progetti è dato dalla capacità dell’anello in acciaio di far fronte alle elevate sollecitazioni da contatto delle sfere in ceramica più rigide.
L’obiettivo dei progetti ARCTIC era creare una nuova lega di acciaio unita a corpi volventi in ceramica in grado di gestire il 15 percento in più di sollecitazioni da contatto e il 25 percento in più di velocità di rotazione rispetto ai tradizionali acciai per cuscinetti aerospaziali. Sviluppare un materiale di questo tipo partendo da zero è stata un’impresa formidabile. Gli acciai per i cuscinetti dei motori attualmente in uso sono stati concepiti nella seconda metà del XX secolo. “È estremamente insolito sviluppare un nuovo acciaio pensando a una sola applicazione”, commenta Jean-Baptiste Coudert, technology development engineer di SKF.
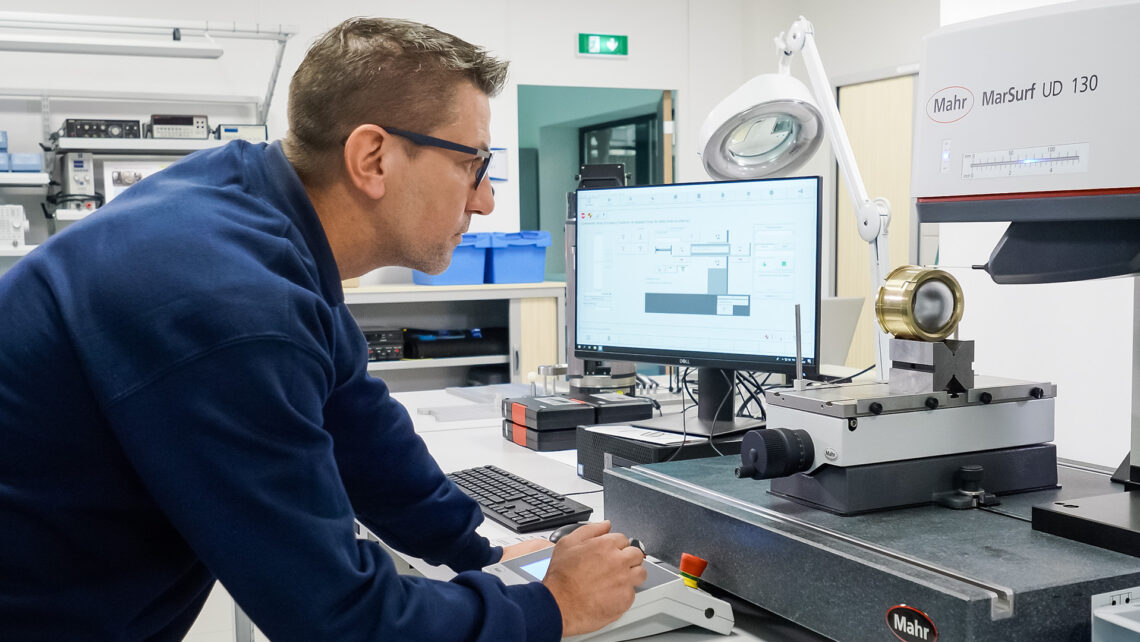
Lega innovativa
Per realizzare il nuovo acciaio, un team dell’SKF Research and Technology Development Centre nei Paesi Bassi si è avvalso di decenni di esperienza nella scienza dei materiali. Con l’ausilio del software di simulazione Thermo-Calc, di proprietà SKF, ha sottoposto a prove decine di formulazioni. Si è reso inoltre necessario ideare un nuovo ciclo di trattamento termico per garantire che sia il processo di produzione sia il trattamento stesso potessero essere attuati in modo economico su scala industriale. Yves Maheo e il suo team di Valence hanno quindi progettato e costruito un nuovo e potente banco prova ad alta velocità per i cuscinetti dell’albero principale, in scala reale, fabbricati con il nuovo acciaio.
La nuova lega ottenuta, brevettata con il nome di ARCTIC15, ha raggiunto tutti gli obiettivi del progetto. Incrementare del 15 percento la capacità di carico può sembrare un risultato modesto, ma in realtà aumenta notevolmente le prestazioni del motore. I cuscinetti ibridi realizzati con il nuovo acciaio reggono carichi superiori del 50 percento rispetto ai tipi tradizionali. Ciò consente di impiegare cuscinetti più piccoli e un albero principale di minore diametro.
L’utilizzo di questa tecnologia sul progetto attuale ha permesso di ridurre la riduzione della perdita di potenza fino al 25 percento, consentendo di ridurre le dimensioni dei sistemi di lubrificazione e raffreddamento e risparmiare direttamente peso. L’ulteriore ottimizzazione del progetto può aumentare la densità di potenza, aprendo la strada a una maggiore efficienza nel consumo di carburante e a una riduzione del 25-30 percento delle emissioni di anidride carbonica e monossido di azoto (obiettivi del cliente).
Durante i test, ARCTIC15 ha dimostrato ulteriori benefici. Rispetto agli acciai tradizionali, offre maggiori durate, soprattutto in condizioni di scarsa lubrificazione o in assenza di olio. I cuscinetti ceramici ibridi realizzati con questo materiale, inoltre, producono minori vibrazioni rispetto ai tipi tradizionali, il che aumenta complessivamente le prestazioni e l’affidabilità del motore.
Attualmente SKF collabora con Rolls-Royce per sviluppare la soluzione su scala industriale e poi collaudare i cuscinetti ibridi ARCTIC15 sui prototipi dell’UltraFan®H2, il turbofan a ingranaggi di nuova generazione per gli aerei di linea.
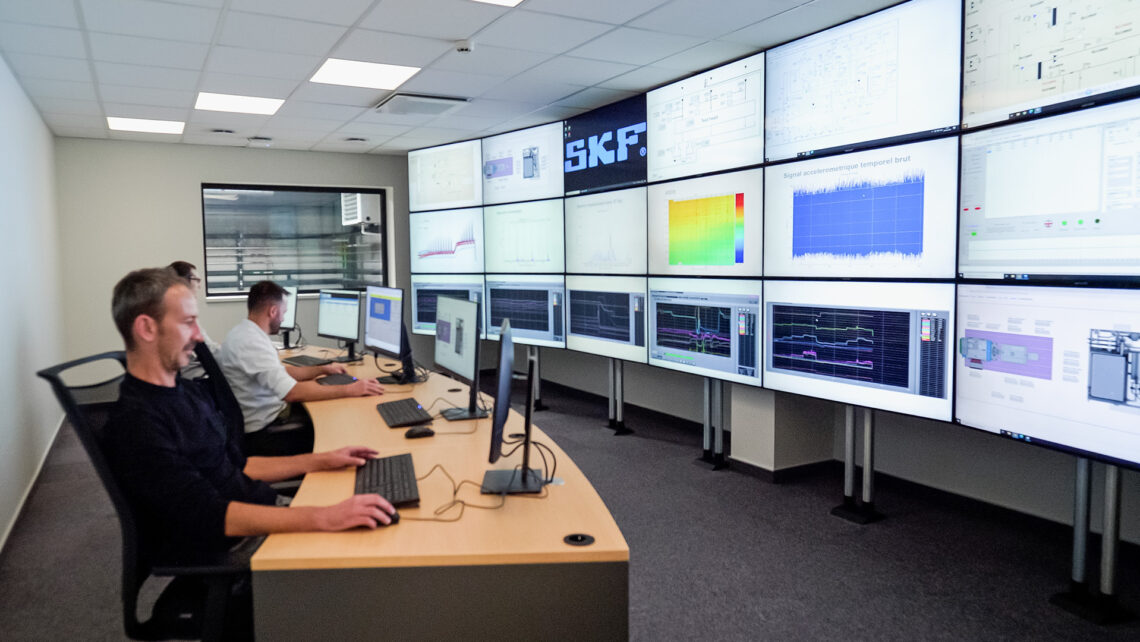
Numeri in crescita per il trasporto aereo passeggeri
Il settore del trasporto aereo è stato tra i più colpiti dalla pandemia di Covid-19, poiché le restrizioni ai viaggi a livello mondiale hanno determinato il crollo della domanda. A distanza di tre anni dalle prime misure restrittive, la maggior parte dei paesi ha riaperto completamente. Persino la Cina, che ha imposto alcune delle regole più severe, nel marzo 2023 ha annunciato il ripristino delle regole pre-pandemia relatativamente ai visti turistici e business.
E le persone sono tornate a volare. Nel 2022, il numero di passeggeri è salito del 47 percento rispetto all’anno precedente, con un numero totale di chilometri percorsi superiore del 70 percento grazie alla ripresa del lungo raggio.