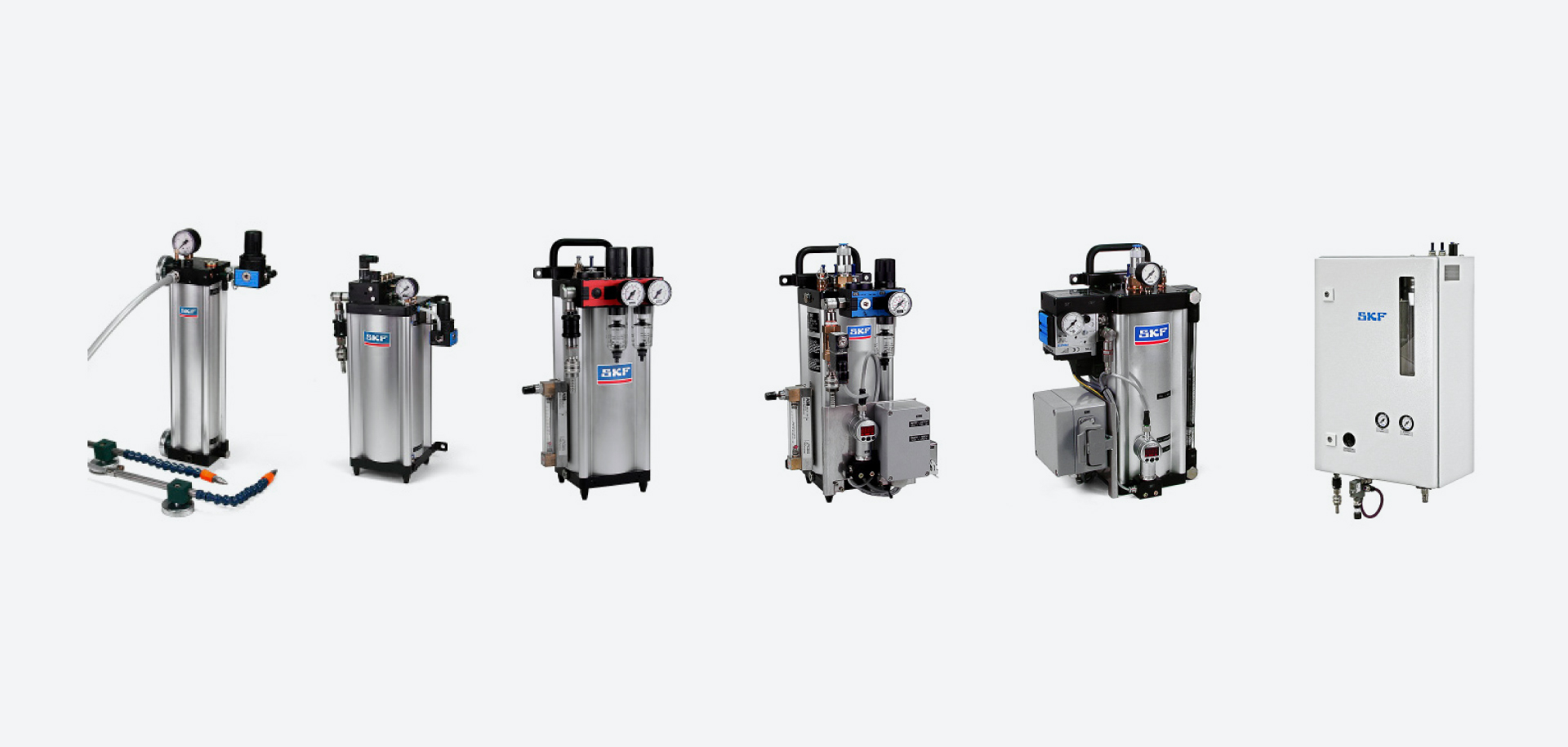
Tanto quanto basta
La lubrificazione minimale si sta sempre più diffondendo nei processi di lavorazione meccanica, essendo una soluzione compatibile con l’ambiente che migliora la produttività e riduce i costi nelle operazioni di taglio.
SKF ha adottato la lubrificazione minimale (Minimum Quantity Lubrication, MQL) per i propri processi di lavorazione, ma ha anche sviluppato un consistente assortimento di soluzioni MQL nell’ambito della gamma LubriLean. Mentre SKF ha ricavato notevoli benefici dall’introduzione di questo tipo di lubrificazione al proprio interno, in particolare una sensibile riduzione dei consumi di olio e una maggiore produttività delle lavorazioni, uno dei suoi distributori specializzati in lubrificazione, la spagnola HRE Hydraulic S.L., ha commissionato una ricerca per quantificare i risparmi ottenibili in termini di costi totali di possesso. Tecnalia, un’azienda leader nella ricerca e sviluppo con sede a Bilbao ha eseguito i relativi test.
Parametri di prova
I test di ricerca e sviluppo hanno messo a confronto l’efficacia delle lavorazioni e l’effetto della forza di taglio degli utensili, nonché l’usura e la temperatura di questi con i costi totali valutati nelle varie condizioni di lubrificazione: lavorazione a secco, lavorazione con lubrorefrigerazione e lavorazione con lubrificazione interna ed esterna MQL.
Sintesi
La lubrificazione minimale (Minimal Quantity Lubrication, MQL) sta assumendo un’importanza crescente nel rendere produttivi, economici e compatibili con l’ambiente i processi di lavorazione. Sotto la spinta alla riduzione dei costi di produzione, i test effettuati hanno dimostrato come la SKF MQL interna possa ridurre della metà il costo totale di possesso rispetto ai processi in cui è usata la lubrificazione con refrigerante. Dato che la MQL viene sviluppata in collaborazione con partner industriali, si prevede che i benefici si potranno estendere a livello globale.
Come banco prova è stato scelto il centro di lavoro IBARMIA ZV 25 (fig. 1), impostato per le diverse condizioni di lavorazione, totalmente a secco, con lubrificante e sistema refrigerante e con sistema MQL SKF LubriLean VarioSuper interno ed esterno.
Per le prove è stato scelto come materiale da lavorare l’acciaio inossidabile duplex 1.4462, in billette da 400 x 90 mm. Come utensili, sono state scelte frese Kendu 3203.57(Z4) a quattro scanalature per le prove con lubrificazione esterna o a secco, e le stesse frese, ma modificate per quanto riguarda i canali interni.
Sono stati scelti due tipi di lubrificante: per il processo con lubrorefrigerazione si è scelto l’Houghton HOCUT B-750, un olio solubile con una concentrazione del 7 %, fatto arrivare esternamente alla macchina utensile alla pressione di 2,3 MPa (23 bar). Per la MQL interna ed esterna si è impiegato il LubriOil di produzione SKF. I parametri di impostazione del processo sono i seguenti:
Parametri:
Velocità di rotazione 2.228 giri/min
Velocità di taglio 70 m/min
Avanz. per tagliente 0,05 mm/tagliente
Profondità di taglio 8 mm
Larghezza di taglio 4 mm
I test sono stati ripetuti con due utensili in ciascuno dei casi e si sono misurati valori di consumo di energia e di durata degli utensili.
Risultati
Il consumo di energia è stato misurato impiegando un analizzatore FlukeView 435, che registra la potenza in ingresso della macchina, la potenza utilizzata in ciascuna fase e la potenza totale (fig. 2).
E stata eseguita un’analisi comparativa della durata dell’utensile in funzione delle varie tecniche di lubrificazione. Come criterio per stabilire il termine di vita dell’utensile è stata considerata la comparsa di usura sul tagliente (valore di usura del fianco VB) sui 0,3 mm; le misurazioni di VB sono state fatte per mezzo di un microscopio stereoscopico, con rilievi a intervalli di dieci passaggi.
Nelle prove di lavorazione a secco gli utensili si sono rotti dopo breve tempo, La fig. 3 mostra lo stato degli utensili di taglio nei due test eseguiti con il refrigerante.
Nel caso della prova 1 (fig. 3a), la figura di destra mostra lo stato dell’utensile dopo 36 m di passaggi; in quella di sinistra si ipotizza che la rottura totale dell’utensile sia stata causata dalla rottura di una delle scanalature.
Nel caso della prova 2 (fig. 3b) le immagini mostrano come la rottura dei taglienti sia stata meno radicale. Ma la presenza di trucioli sulla punta dell’utensile indica che questo non era ben lubrificato durante il taglio, cosa che provoca tensioni localizzate e il distacco di materiale dal tagliente.
La fig. 4 mostra lo stato degli utensili nelle due prove eseguite con MQL esterna. In tali prove l’usura del tagliente risulta progredire maggiormente che nel caso di lavorazione con fluido refrigerante.
Nel caso della prova 1 (fig. 4a), le immagini mostrano l’usura sulla facciata di spoglia dell’utensile.
Nel caso della prova 2 (fig. 4b), le immagini mostrano che l’utensile si rompe in punta, producendo una frattura localizzata all’estremità del tagliente.
Infine, nel caso delle prove di fresatura con MQL interna si nota come l’usura del tagliente sia progredita maggiormente che nei casi della lavorazione con refrigerante e della lavorazione con MQL esterna, mentre non c’è stata rottura del tagliente in nessuna delle due prove di lavorazione con MQL interna.
Nel caso della prova 1 (fig. 5a), il tagliente si è usurato all’altezza della profondità di passata.
Per contro, nel caso della prova 2 (fig. 5b), si è verificata una micro-rottura della punta dell’utensile.
La fig. 6 mostra la lunghezza dei trucioli ottenuti sugli utensili testati a seconda della tecnica di lubrificazione adottata. Per ciascuna tecnica viene inoltre indicato il valore medio ottenuto dopo varie ripetizioni delle prove.
Conclusioni
È stato dimostrato che la durata degli utensili migliora sensibilmente se si impiega la tecnica MQL interna, con la quale la lunghezza dei trucioli è considerevolmente maggiore che nel caso delle altre due tecniche di lubrificazione.
Dopo l’esecuzione dei calcoli relativi ai quattro metodi presentiamo in tabella 1 i costi totali delle operazioni (calcolati per asportare 1.000 cm3 di metallo).
Si nota chiaramente che il costo totale delle operazioni si riduce con l’impiego della LubriLean MQL. Con la MQL interna il costo totale è meno del 54 % di quello della lavorazione con lubrirefrigerante.
MQL a più alti livelli
La foratura profonda con utensili di piccolo diametro pone grandi sfide alla MQL. Tuttavia si tratta di un processo di lavorazione importante. Il problema è che con l’aumentare della profondità di foratura, aumenta la pressione di ritorno nei condotti refrigeranti. Di conseguenza la generazione di aerosol diventa più difficile a causa della piccola differenza di pressione tra l’ingresso dell’aria e l’uscita dell’aerosol, il che fa aumentare il rischio di rotture e di scarto degli utensili. Ciò può comportare costi elevati non necessari, specialmente su pezzi da lavorare in lega di alta qualità.
Gli ingegneri SKF si sono posti l’obiettivo di migliorare l’alimentazione di aerosol nelle lavorazioni di foratura profonda con diametri (D) inferiori a 5 mm e profondità superiori a 25 x D. Con l’integrazione di un sistema di bypass nel DigitalSuper, la differenza di pressione tra l’ingresso dell’aria e l’uscita dell’aerosol viene costantemente monitorata. Quando la differenza di pressione è inferiore al valore richiesto, viene attivato il bypass per allentare la pressione nella linea in modo che il sistema MQL possa generare un aerosol sufficiente per lubrificare la punta degli utensili, che sono lunghi e di piccolo diametro.
SKF ha sottoposto i propri sistemi a lunghi periodi di prova per verificare i risultati ottenibili rispetto alle varianti tecnicamente più complicate a due condotti prodotte dai concorrenti. L’azienda specializzata in utensili di precisione Gühring ha fornito un’avanzata strumentazione per eseguire e valutare i test. Spray test e test quantitativi sono stati eseguiti su uno speciale banco Gühring MQL, fotografando le caratteristiche degli spray.
Sono stati anche eseguiti test sull’AlSi7Mg, un materiale molto difficile da lavorare, impiegando una punta a forare lunga 200 mm, con 4,5 mm di diametro e condotti di raffreddamento di 0,6 mm di diametro. Dopo le analisi, un blocco di AlSi7Mg è stato lavorato con una velocità di taglio di 130 m/min e un avanzamento di 0,2 mm/giro. Lo scopo era di esaminare le prestazioni della lavorazione di foratura e il grado di usura su un percorso totale di 100 m. La soluzione SKF ha richiesto 18 ml di lubrificante all’ora. Al termine del test di 100 m l’utensile era ancora in eccellenti condizioni.
Vantaggi confermati
L’impiego del Digital Super con bypass e una pressione d’ingresso di 1 MPa (10 bar) consente una distribuzione di aerosol più favorevole per la stabilità dei processi di foratura profonda, rispetto alle precedenti varianti e ai prodotti dei concorrenti. Riprese video hanno evidenziato l’esistenza di un rilascio di aerosol fine e uniforme sull’utensile, come richiesto per ottenere una qualità elevata di lavorazione (fig. 7). Ciò consente una buona umidificazione della zona di lavorazione e quindi un miglioramento della durata degli utensili e della qualità del pezzo finito.
Futuro dell’SKF LubriLean
LubriLean è stato incluso nei prodotti SKF BeyondZero sin dal 2014. Le macchine utensili equipaggiate con il sistema SKF LubriLean sono impiegate con successo nei più importanti stabilimenti automotive e aerospace. Finora la MQL è stata fornita essenzialmente tramite OEM europei e americani, ma, grazie al suo successo in un crescente numero di applicazioni in tutto il mondo, i prodotti LubriLean possono essere impiegati da altre industrie e in altri paesi. Dove ci sono problemi ambientali, la MQL può essere la soluzione ideale per risolverli, consentendo nel contempo la realizzazione di processi di lavorazione economici e di alta qualità.
La tecnologia MQL e le applicazioni dei prodotti si evolvono rapidamente. Tuttavia le prestazioni nella lavorazione meccanica non dipendono esclusivamente dalla MQL in sé, ma anche dalla macchina utensile, dagli utensili di taglio, dal materiale da lavorare, dai parametri di processo, ecc. I vari fattori devono essere allineati e ottimizzati tutti insieme. Affinché abbiano successo, le applicazioni richiedono pertanto un forte supporto ingegneristico e la collaborazione con altri partner tecnici. Di qui parte la fase successiva dello sviluppo e della crescita della MQL.
Cos’è la MQL?
La Minimum Quantity Lubrication (lubrificazione minimale, MQL) è stata sviluppata nell’intento di lubrificare i taglienti degli utensili nel modo più accurato possibile, utilizzando nello stesso tempo la quantità più piccola di lubrificante che il processo di lavorazione richiede. Il sistema MQL (fig. 8) utilizza un bio-olio per generare un aerosol, costituito da un insieme omogeneo di goccioline microscopiche; esso viene inviato sull’utensile, sul pezzo in lavorazione e sul truciolo, tramite un ugello, indirizzato sul punto di taglio dell’utensile stesso (MQL esterna) oppure, tramite il mandrino della macchina utensile e speciali condotti, sulla punta dell’utensile (MQL interna). La maggior parte delle microgocce non viene separata dall’aria per forza centrifuga quando l’aerosol passa attraverso il mandrino.
Normalmente la quantità di lubrificante usata è inferiore a 50 ml/h, a seconda del metodo di taglio, del materiale da lavorare e dal settaggio della macchina. Dato che è in piccola quantità, il lubrificante mantiene asciutto il pezzo e i trucioli; si hanno quindi considerevoli risparmi grazie al fatto di non doverli pulire.
Questa tecnologia consente anche una lubrificazione affidabile del tagliente dell’utensile anche con velocità di rotazione superiori a 20.000 giri/min.
La MQL è stata applicata nei principali processi di lavorazione quali tornitura, fresatura, foratura e formatura. Con la tecnologia MQL una cella di produzione con un sistema di refrigerazione complesso può essere dotato di una soluzione di lubrificazione di ridotto ingombro.
Assortimento SKF
SKF ha realizzato un assortimento completo di prodotti e soluzioni MQL, che vanno dalla lubrificazione esterna o interna per diametri di utensile piccoli o grandi ai controlli automatici o regolabili manualmente, con o senza monitoraggio automatico delle condizioni dell’aerosol. La fig. 9 illustra l’intero assortimento.
Il prodotto MQL più avanzato, la serie DigitalSuper, ha il proprio sistema di controllo ed è disponibile con gli avanzati bus di campo ProfiBus o ProfiNet per centri di lavorazione e centri di tornitura con mandrini singoli o doppi.
La serie Vario è stata progettata per la lubrificazione esterna e interna e può essere controllata da un controller della stessa macchina utensile. La VarioSuper è idonea per centri di lavorazione, centri di tornitura e macchine speciali. La VarioPlus è regolabile a mano e adatta per tornitura, fresatura e foratura e può essere installata per ammodernare centri di lavorazione e di tornitura. Vario è un dispositivo manuale di facile utilizzo in applicazioni speciali (per esempio nei multimandrini) e su torni da ammodernare.
LubriLean Basic e Smart sono prodotti entry-level per la MQL esterna. LubriLean Basic è particolarmente idoneo per le macchine in cui l’utensile deve essere bagnato da due lati come le fresatrici (c’è l’opzione per otto ugelli). LubriLean Smart è una soluzione economica e di facile installazione. Grazie al suo sistema modulare, le applicazioni possono essere implementate in modo flessibile ed economico (ad es. linee transfer e alimentazione centralizzata di molti punti di lavorazione).
SKF LubriLean può servire i clienti OEM e gli utilizzatori finali sia per le macchine utensili di nuova costruzione sia per quelle da ammodernare. In luogo di un liquido refrigerante ad alta pressione, i dispositivi SKF LubriLean generano un aerosol con un olio vegetale sfruttando l’effetto Venturi senza l’uso di una pompa. In tal modo si riducono i consumi di energia, sono possibili velocità di taglio maggiori e più lunghe durate degli utensili, si evitano spargimenti di olio nella zona attorno alla macchina e si riesce a mantenere asciutti i pezzi da lavorare, che non devono quindi essere ripuliti.
LubriLean e BeyondZero sono marchi registrati del Gruppo SKF