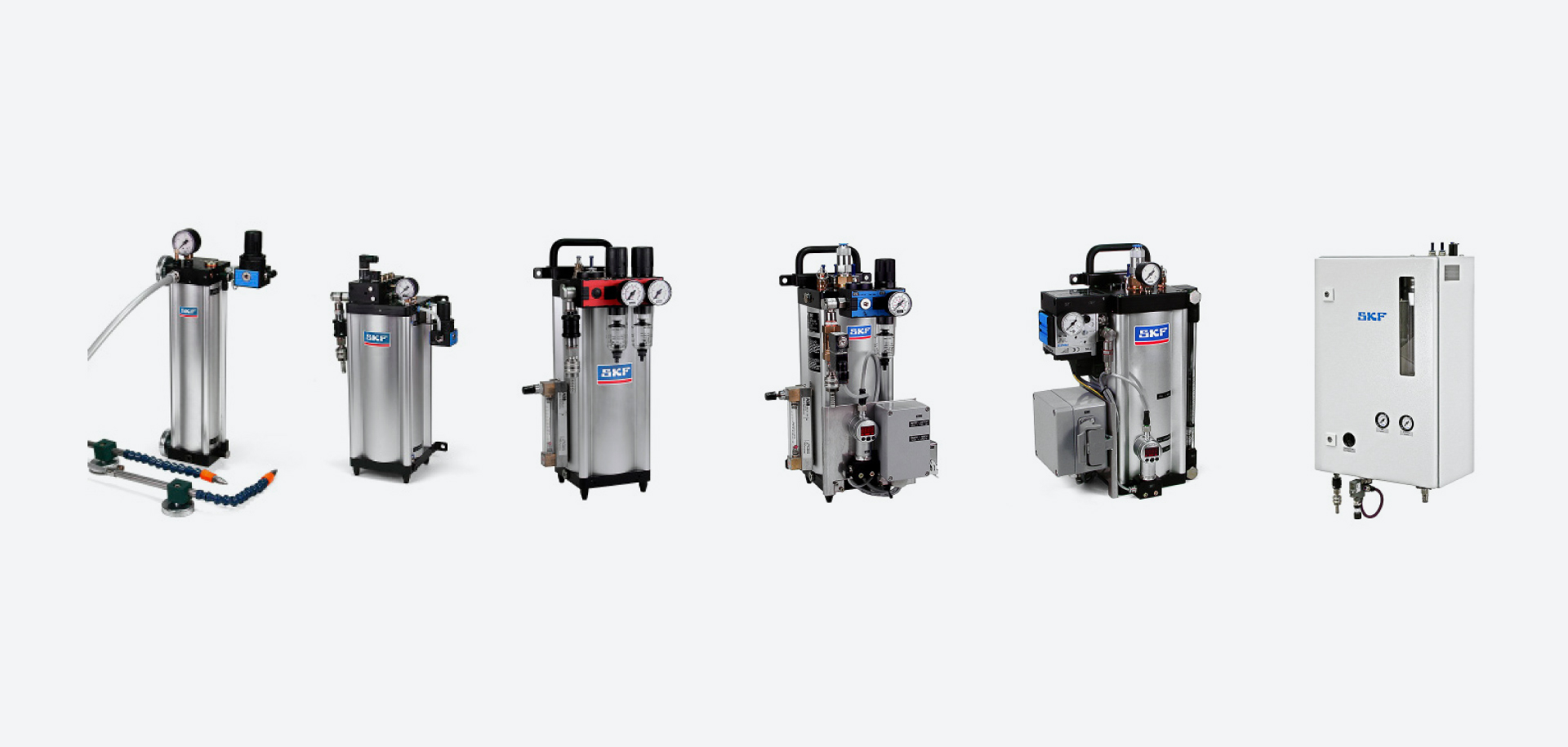
Un rien suffit
La microlubrification est de plus en plus présente au sein des procédés d’usinage car, outre ses atouts en matière de développement durable et d’écologie, elle améliore la productivité et réduit les coûts.
SKF, qui utilise la microlubrification (MQL) dans ses propres processus de fabrication, a par ailleurs mis au point un portefeuille complet de solutions MQL, baptisé LubriLean. Si SKF a déjà pu tirer des avantages significatifs de son introduction de la MQL, notamment une réduction considérable de la consommation d’huile et une plus grande productivité en matière d’usinage, l’un de ses distributeurs spécialisés dans la lubrification, l’espagnol HRE Hydraulic S.L., a quant à lui commandé une étude afin de quantifier les économies potentielles sur le coût total du cycle de vie. Les essais ont été confiés à Tecnalia, société leader en recherche et développement, également basée en Espagne, dans les environs de Bilbao.
Paramètres des essais
Les essais de R&D ont été élaborés de manière à comparer les performances d’usinage, l’impact de la force d’usinage, l’usure et la température de l’outil, ainsi que les coûts totaux entre différents systèmes de lubrification : usinage à sec (aucune lubrification), usinage sous arrosage avec un fluide de coupe, et lubrification MQL interne et externe.
Résumé
La microlubrification s’impose de plus en plus comme la clé de procédés d’usinage productifs, économiques et respectueux de l’environnement. Face à des pressions croissantes sur les coûts de production, des essais ont montré que la technologie de MQL interne de SKF permet de réduire de moitié le coût total du cycle de vie par rapport à des procédés d’usinage par arrosage. Le développement de cette technologie en collaboration avec des partenaires industriels devrait contribuer à une diffusion des avantages offerts dans le monde entier.
Le centre d’usinage IBARMIA ZV 25 (Fig. 1) a été choisi en guise de banc d’essai. Cette machine a été équipée tour à tour pour un usinage sous arrosage (système de refroidissement), un usinage totalement à sec et avec le système SKF VarioSuper, de microlubrification externe et interne.
Le matériau sélectionné pour les essais était un acier inoxydable duplex 1.4462 sous forme de billettes de 400 mm x 90 mm. Les outils étaient des fraises Kendu 3203.57(Z4) à quatre goujures pour les essais dans des conditions de lubrification externe ou d’usinage à sec et le même type, mais modifié par ajout de canaux internes, pour les autres essais.
Deux types de lubrifiants ont été sélectionnés. Pour le procédé sous arrosage avec fluide de coupe, l’huile soluble Houghton HOCUT B-750 a été utilisée à une concentration de 7 %. Elle était acheminée de l’extérieur à la machine-outil à une pression de 2,3 MPa (23 bar). Pour la microlubrification interne et externe, c’est le produit SKF LubriOil qui a été utilisé. Les paramètres du procédé ont été configurés comme suit :
Paramètres :
Vitesse de rotation 2 228 tr/min
Vitesse de coupe 70 m/min
Avance par arête 0,05 mm/arête
Profondeur de coupe 8 mm
Largeur de coupe 4 mm
Les essais ont été réalisés avec deux outils dans chaque cas et ont fourni des valeurs de mesure pour la consommation d’énergie et la durée de vie de l’outil.
Résultats
La consommation d’énergie a été mesurée à l’aide d’un énergimètre FlukeView 435 connecté à la source d’alimentation. Cet appareil enregistre la puissance d’entrée de la machine, la consommation à chaque phase et la puissance totale (Fig. 2).
Une analyse comparative de la durée de vie de l’outil selon les différentes techniques de lubrification a pu être établie. Une anomalie visible au niveau de l’usure de la lèvre (valeur d’usure en dépouille VB) inférieure à 0,3 mm a été définie comme critère de fin de vie de l’outil ; les valeurs d’usure en dépouille (VB) sont mesurées au niveau du flanc de la lèvre de l’outil à l’aide d’un microscope stéréoscopique tous les dix passages.
Lors des essais d’usinage à sec, les outils se sont rapidement cassés.
La Fig. 3 montre l’état des outils de coupe à l’issue des deux essais réalisés avec un fluide de coupe.
Concernant l’essai 1 (Fig. 3a), l’image de droite montre l’outil cassé après une longueur totale de fraisage de 36 m. Il semblerait que la rupture de l’une des goujures, visible sur l’image de gauche, soit à l’origine de la casse catastrophique de l’outil.
Concernant l’essai 2 (Fig. 3b), les images montrent des arêtes moins endommagées. Toutefois, l’écaillage de la pointe de l’outil indique qu’une lubrification insuffisante de celui-ci lors de la coupe a entraîné des tensions locales et une exfoliation du matériau de l’arête de coupe de la fraise.
La Fig. 4 montre l’état des outils de coupe à l’issue des deux essais réalisés avec un système de microlubrification externe. Pour ces essais, l’usure de l’arête de l’outil est plus progressive que dans le cas d’un usinage à l’huile de coupe.
Concernant l’essai 1 (Fig. 4a), les images montrent une usure de la face de dépouille de l’outil.
Concernant l’essai 2 (Fig. 4b), les images montrent que la fraise s’est brisée à la pointe, produisant une fracture localisée à l’extrémité de l’arête de coupe.
Enfin, en ce qui concerne la microlubrification interne, les résultats font état d’une usure de l’arête de coupe plus progressive que dans le cas de l’usinage sous arrosage et avec une microlubrification externe. Aucune défaillance de coupe n’a été déplorée dans aucun des deux essais d’usinage avec microlubrification interne.
Concernant l’essai 1 (Fig. 5a), l’arête s’use à hauteur de la profondeur de passe.
À l’inverse, dans le cas de l’essai 2 (Fig. 5b), une micro-rupture de la pointe de l’outil est apparue.
La Fig. 6 montre la durée de vie, en longueur totale usinée, de chacun des outils de coupe testés, en fonction de la technique de lubrification employée. La moyenne des valeurs obtenues sur l’ensemble des différentes répétitions est également indiquée pour chaque technique de lubrification.
Conclusions des essais
Il est démontré que la technique MQL interne améliore de façon significative la durée de vie des outils puisque la longueur de fraisage totale est nettement supérieure par rapport à celle atteinte avec les deux autres techniques de lubrification.
Un calcul du coût total (calculé pour usiner 1 000 cm3 de métal) a été effectué pour les quatre méthodes et les résultats sont fournis dans le Tableau 1.
Comme le montre clairement ce tableau, le recours à la solution LubriLean MQL réduit nettement le coût total d’exploitation qui représente moins de 54 % de celui de l’usinage sous arrosage.
Repousser encore plus loin les limites de la MQL
Le perçage d’alésages profonds avec des outils de petit diamètre est problématique avec la MQL. Il s’agit pourtant d’un procédé d’usinage important. La difficulté vient du fait que plus la profondeur d’alésage est grande, plus la contre-pression dans les canaux de refroidissement est élevée. Par conséquent, la génération de l’aérosol devient plus difficile du fait de la faible différence de pression entre l’entrée d’air et la sortie d’aérosol, avec pour conséquence un risque plus élevé de cassure de l’outil et de pertes. Cela peut entraîner des coûts inutilement élevés, notamment avec des pièces fabriquées dans des alliages de grande qualité.
Les ingénieurs SKF se sont fixé comme objectif d’améliorer la distribution d’aérosol pour le perçage d’alésages profonds de diamètre (D)inférieur à 5 mm, à des profondeurs supérieures à 25 x D. Grâce à un système de dérivation intégré au système DigitalSuper, la différence de pression entre l’entrée d’air et la sortie d’aérosol est surveillée en permanence. Lorsque cette différence est inférieure à la valeur requise, la dérivation est activée pour relâcher la pression dans la ligne afin que le système MQL puisse produire suffisamment d’aérosol pour une lubrification adéquate de la pointe de l’outil.
SKF a soumis son système à des essais intensifs afin de comparer ses performances à celles de produits concurrents de type bi-canaux techniquement plus complexes. Le spécialiste des outils de précision Gühring a fourni des instruments de mesure de pointe pour la réalisation de ces essais et l’évaluation des résultats. Des essais de pulvérisation et de dosage ont été effectués sur un banc d’essai spécial MQL conçu par Gühring et enregistrés à l’aide d’une caméra.
D’autres essais ont également été réalisés sur l’alliage AlSi7Mg, un matériau particulièrement difficile à usiner. Pour ce faire, un foret de 4,5 mm de diamètre et 200 mm de long a été utilisé pour des diamètres de canaux de refroidissement de 0,6 mm. Suivant les analyses effectuées au banc d’essai, un bloc de AlSi7Mg a été usiné à une vitesse de coupe de 130 m/min et une vitesse d’avance de 0,2 mm/tr. L’objectif était d’examiner les performances de forage et l’usure sur une distance totale de 100 m. La solution SKF a consommé 18 ml de lubrifiant par heure. L’outil était toujours en excellent état à l’issue de la distance totale de forage de 100 m.
Des avantages confirmés
L’utilisation du Digital Super avec une commande de dérivation et une pression d’entrée de 1 MPa (10 bar) permet un apport du lubrifiant sous forme d’aérosol qui contribue à la stabilité du procédé de perçage d’alésages profonds, par rapport aux variantes précédentes et aux produits de la concurrence. Comme en attestent les enregistrements vidéo, l’aérosol assure une lubrification uniforme en fine couche de l’outil, répondant ainsi aux exigences pour une qualité d’usinage élevée (Fig. 7). La zone d’usinage est parfaitement couverte, ce qui participe à augmenter la durée de vie de l’outil et à améliorer la qualité de la pièce.
Le futur de SKF LubriLean
LubriLean figure dans la gamme de produits SKF BeyondZero depuis 2014. Des machines-outils équipées d’un système SKF LubriLean sont utilisées avec succès dans des usines automobiles et aéronautiques de pointe. Jusqu’à présent, la MQL était principalement proposée par l’intermédiaire de fabricants OEM européens et américains. Compte tenu du succès de cette technologie au sein d’un nombre croissant d’applications partout dans le monde, les produits LubriLean vont désormais pouvoir être étendus à d’autres industries et pays. La MQL apporte une réponse aux préoccupations environnementales tout en offrant un procédé d’usinage économique et de qualité.
La technologie MQL et ses applications connaissent un développement rapide. Cependant, les performances d’usinage ne dépendent pas seulement du système MQL en lui-même, mais aussi de la machine-outil, de l’outil utilisé, du matériau à usiner, des paramètres d’usinage, etc. Tous ces facteurs doivent être optimisés et alignés les uns sur les autres. Le succès des applications repose par conséquent sur une assistance en ingénierie solide et une coopération avec d’autres partenaires techniques. Nous sommes à l’aube de la prochaine phase de développement et de croissance de la MQL.
Qu’est-ce que la microlubrification (MQL) ?
La microlubrification, en anglais Minimum Quantity Lubrication (MQL), a été mise au point dans la perspective d’une lubrification de l’arête de coupe de l’outil qui soit aussi précise que possible tout en consommant aussi peu de lubrifiant qu’il n’est nécessaire pour le procédé d’usinage. Un système MQL (Fig. 8) utilise de la biohuile pour générer un aérosol constitué de gouttelettes homogènes, de l’ordre du micron, puis le diffuse sur le point de coupe de l’outil afin de lubrifier ce dernier, la pièce et les copeaux. La pulvérisation s’effectue via une buse orientée vers le point de coupe de l’outil (MQL externe) ou via la broche de la machine-outil et les canaux de l’outil conduisant à sa pointe (MQL interne). Leur taille réduite évite à la plupart de ces gouttelettes de se séparer de l’air sous l’effet de la force centrifuge au moment où l’aérosol traverse la broche en rotation.
En général, la consommation de lubrifiant est inférieure à 50 ml/h, en fonction de la méthode de coupe, du matériau de la pièce et des réglages de la machine. Cette faible quantité de lubrifiant se traduit par des pièces et des copeaux secs. Il n’est plus nécessaire de nettoyer la pièce ou les copeaux, d’où une réduction considérable des coûts.
Cette technologie assure en outre une lubrification fiable de la lame de l’outil, y compris à des vitesses de rotation supérieures à 20 000 tr/min.
La MQL s’applique à des procédés primaires d’usinage : tournage, fraisage, alésage et façonnage. Grâce à la technologie MQL, une cellule de fabrication dotée d’un système de refroidissement complexe peut être équipée avec une solution de lubrification compacte.
Gamme de produits SKF
SKF a développé une gamme complète de produits et solutions MQL qui englobe la lubrification interne et externe pour des outils de faible ou gros diamètre, avec réglage manuel ou contrôle automatique, et avec ou sans surveillance automatique des paramètres relatifs à l’aérosol. L’ensemble de la gamme est représenté sur la Fig. 9.
Le produit MQL le plus évolué, baptisé DigitalSuper, est doté de son propre système de contrôle et prend en charge les bus de terrain ProfiBus et ProfiNet pour les applications au sein de centres d’usinage et de tournage à une ou deux broches.
La série Vario est conçue pour la lubrification interne et externe et peut être pilotée par l’unité de commande de la machine-outil. Le VarioSuper convient aux centres d’usinage, centres de tournage et machines spéciales. Le VarioPlus est réglable manuellement, convient au tournage, au fraisage et à l’alésage et peut être installé en seconde monte dans des centres de tournage et d’usinage. Le système Vario est équipé d’un dispositif de réglage manuel pour une mise en œuvre facile dans des applications générales comme spéciales (multi-broches par ex.) et en deuxième monte dans des tours.
LubriLean Basic et Smart sont des produits d’entrée de gamme de MQL externe. Le LubriLean Basic est particulièrement adapté aux machines sur lesquelles l’outil est arrosé des deux côtés (jusqu’à huit buses prises en charge), pour le fraisage par exemple. LubriLean Smart constitue une solution économique et facile à installer. Sa modularité contribue à une mise en œuvre flexible et économique des applications (chaînes de transfert et alimentation centralisée de plusieurs points d’usinage par exemple).
SKF LubriLean s’adresse aussi bien aux fabricants OEM qu’aux utilisateurs finaux pour équiper de nouvelles machines-outils ou être installé en seconde monte. Au lieu d’un fluide de coupe sous haute pression, les appareils SKF LubriLean diffusent un aérosol à base d’huile végétale en s’appuyant sur l’effet Venturi, sans nécessiter aucune pompe. Cette solution réduit la consommation d’énergie, permet d’atteindre des vitesses de coupe et une durée de vie de l’outil supérieures, évite les déversements à proximité de la machine et fournit des pièces sèches qui ne nécessitent plus aucune opération de nettoyage ou décontamination.
LubriLean et BeyondZero sont des marques déposées du Groupe SKF.