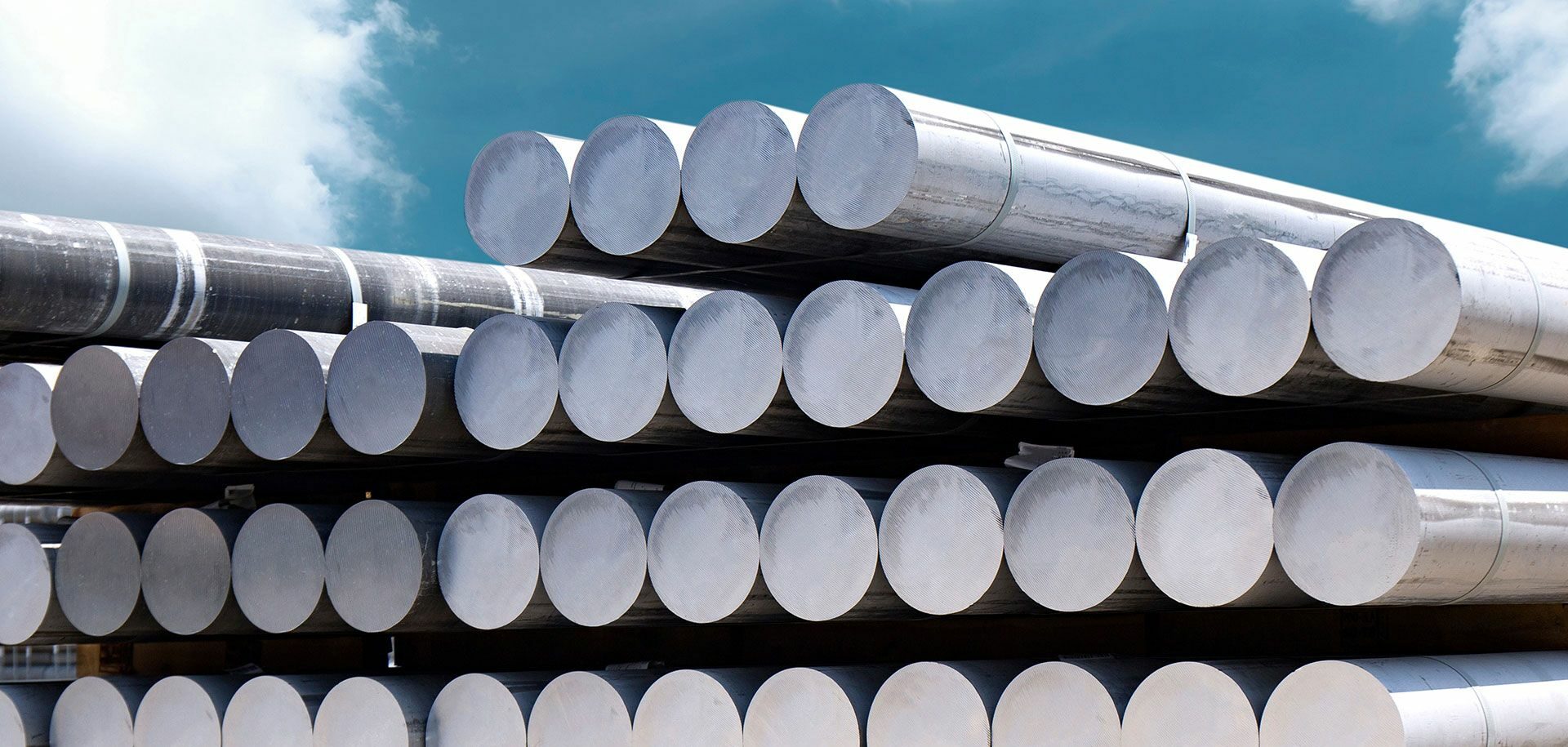
Rapsodia rumena
L’approccio all’ingegneria dell’affidabilità di SKF si è rivelato un buon investimento per uno dei maggiori produttori europei di alluminio.
ALRO, acronimo di Aluminium Romania, è uno dei maggiori produttori di alluminio in Europa, nonché una delle più grandi aziende della Romania, con oltre 3.400 dipendenti in tre siti produttivi nel paese. Nei due stabilimenti di Slatina sono presenti una fonderia, un centro R&S e impianti di lavorazione (raddrizzatori, un impianto per trattamenti anodici, un piano di colata, laminatoi a caldo e a freddo e un’officina di estrusione). La raffineria di allumina, parte del gruppo ALRO, si trova anch’essa in Romania, a Tulcea, nei pressi del delta del Danubio e del Mar Nero.
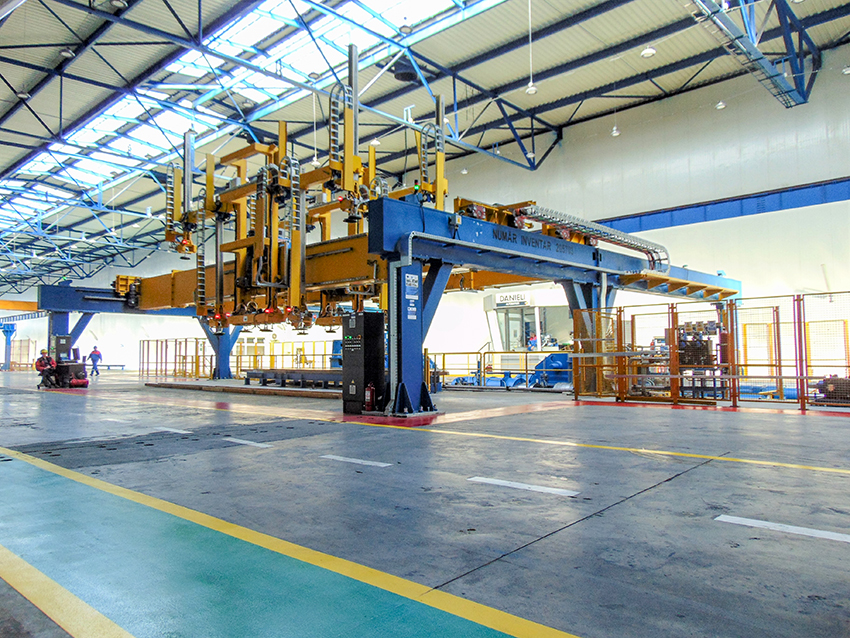
Lo stabilimento di Slatina si estende su una vasta superficie. Utilizza il 5 percento della produzione di energia elettrica della Romania per fabbricare prodotti in alluminio primario come vergelle, billette e bramme, nonché semilavorati come lamiere, fogli, bobine, nastri e profili. Attraverso varie innovazioni e sviluppi, ALRO ha creato un assortimento di prodotti che soddisfa le esigenze di oltre 300 clienti che operano nei settori dei cavi e conduttori, dell’edilizia, dell’automobile, dell’aeronautica e dell’ingegneria in tutto il mondo.
SKF ha rivoluzionato il nostro approccio alla manutenzione
Gheorghe Dobra, CEO, ALRO
“Grazie ai risultati ottenuti nel controllo dei costi per raggiungere l’efficienza operativa, e a programmi aggressivi per aumentare la capacità produttiva, nel 2018 abbiamo raggiunto una produzione di 210.000 tonnellate di alluminio primario, 283.000 tonnellate di alluminio pressofuso, 31.000 tonnellate di alluminio riciclato e 105.000 tonnellate di prodotti in alluminio lavorato (profili estrusi inclusi), prodotti ad alto valore aggiunto, con l’obiettivo di raggiungere le 120.000 tonnellate di alluminio lavorato entro il 2021”, afferma Dobra.
L’alluminio è un elemento chimico della tavola periodica con numero atomico 13 ed è tra i più diffusi, costituendo oltre l’8 percento della crosta terrestre. Ma non esiste in natura allo stato puro. Fu isolato per la prima volta dal fisico danese Christian Oersted nel XIX secolo, con il metodo della riduzione per via elettrolitica di vari minerali ricchi di alluminio. Oggi si ricava principalmente dall’allumina, che a sua volta si ottiene dalla bauxite, un minerale argilloso estratto prevalentemente ai tropici. Per produrre una tonnellata di alluminio sono necessarie da quattro a cinque tonnellate di bauxite.
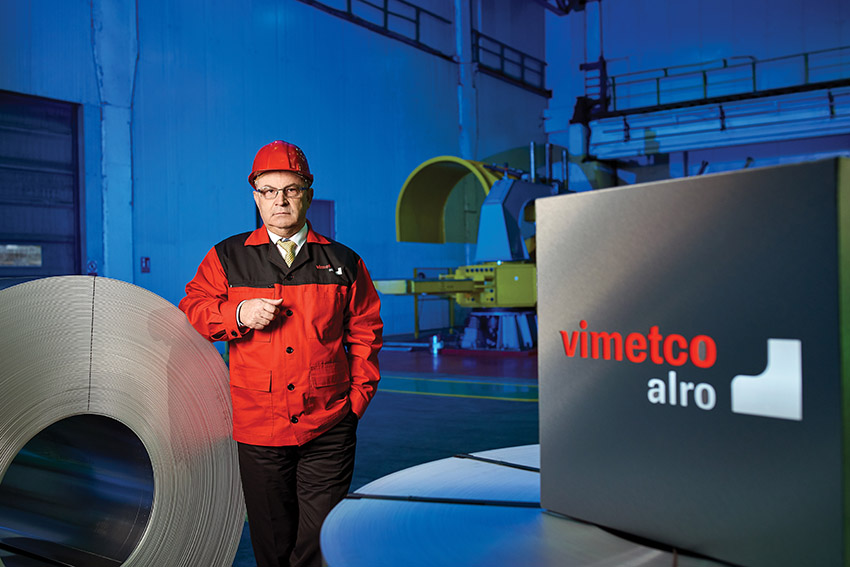
Ciascuno di questi rappresenta una materia prima fondamentale per la produzione di automobili, treni, aerei, telefoni, cavi, scambiatori di calore, computer, prodotti per uso domestico e numerosi altri.
Nella sua veste di produttore di alluminio di rilevanza mondiale, il Gruppo ALRO rappresenta un caso unico, poiché possiede e gestisce l’intera catena del valore, dalla bauxite ai prodotti automobilistici e aerospaziali (compresi un impianto per trattamenti anodici e impianti per il riciclo dell’alluminio). Nel linguaggio aziendale, questa si chiama integrazione verticale, in quanto l’azienda detiene e gestisce l’intero processo di produzione, dalla miniera di bauxite in Sierra Leone (occorrono due settimane per far arrivare i minerali al porto di Tulcea) agli impianti di Slatina.
Dobra prevede un futuro sostenibile per la sua azienda: “ALRO rimarrà un produttore di alluminio competitivo ancora per molto tempo a venire”.
Il successo duraturo di ALRO come azienda privata in Romania è dovuto in gran parte ai continui investimenti in nuove tecnologie e processi per aumentare l’efficienza complessiva (solo nel 2018 sono stati investiti 54,8 milioni di euro).
Alcuni di questi hanno coinvolto la SKF Romania, il cui compito è stato quello di offrire ad ALRO un approccio per l’intero ciclo di vita, aiutando l’azienda a ottimizzare l’impiego di cuscinetti e strumenti di condition monitoring SKF in centinaia di canali di misura, come forni, laminatoi a caldo e a freddo, spazzolatrici e macchinari correlati. L’idea è stata quella di adottare un approccio all’“ingegneria dell’affidabilità” per ottimizzare le risorse di ALRO lungo il loro intero ciclo di vita.
“Abbiamo iniziato a collaborare con SKF nel 2009, e riteniamo che siano i migliori del settore”, afferma Dobra. “SKF ha rivoluzionato il nostro approccio alla manutenzione, facendoci ridurre i costi del 15 percento. Abbiamo iniziato applicando la tecnologia SKF Machine Health per eliminare del 100 percento i guasti imprevisti, e non siamo lontani da questo obiettivo. Abbiamo investito in questa tecnologia e nel cambiamento di mentalità e processi. Ora ci concentriamo su altri obiettivi, come la digitalizzazione dei dati nell’ambito della manutenzione e del controllo dei processi. La partnership con SKF è estremamente importante per i nostri programmi attuali e futuri”.